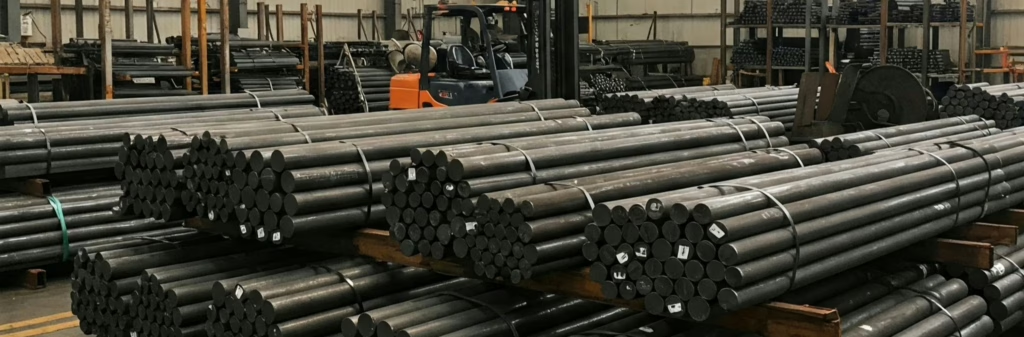
El acero para herramientas H13 es un acero para herramientas de trabajo en caliente que se endurece al aire y es uno de los más utilizados entre todos los aceros para herramientas de trabajo en caliente. Similar a Acero para herramientas D2 as a benchmark for cold work tool steels, H13 is the benchmark for hot work tool steels. Compared to H11 tool steel, this steel grade has higher thermal strength and hardness. It can be air-hardened, so it performs well in terms of temple deformation and residual stress, and has a lower likelihood of surface oxidation. Additionally, it can achieve secondary hardening, has excellent thermal stability, and can effectively resist corrosion from aluminum alloy molten metal.
Los fabricantes utilizan ampliamente este grado de acero para producir matrices y mandriles de extrusión en caliente, matrices de forja con martillo de caída y matrices de forja. También se utiliza comúnmente para insertos en máquinas de forja de precisión y matrices de fundición a presión para aluminio, cobre y sus aleaciones.
The designation in the U.S. ASTM A681 system is H13, and the name in the American AISI system is AISI H13 steel. Similarly, other national standards use comparable designations, such as ISO 40CrMoV5, Japan/JIS SKD61, USA/UNS T20813, Germany/DIN X40CrMoV5-1, Germany/W-Nr. 1.2344, and Czech Republic (CSN) 19554, BS (BH13), SS (2242), ANFOR (Z40CDV5), and UNI (X35CrMoV05KU / X40CrMoV511KU).
1. Aplicaciones
- Herramientas para trabajo en caliente:Es la opción principal para la mayoría de las operaciones de trabajo en caliente, especialmente cuando las matrices requieren enfriamiento con agua u otros medios de limpieza.
- Moldes de fundición a presiónEl material H13 es especialmente adecuado para la fundición a presión de aleaciones de zinc, aluminio y magnesio, como varillas de empuje, pasadores de expulsión, pasadores de núcleo, correderas, boquillas y bebederos. Los bloques de material H13 purificados mediante refusión por electroescoria (ESR) son adecuados para moldes de plástico que requieren un acabado superficial de alta calidad, como los moldes de lentes para automóviles, gracias a su mayor pureza y uniformidad.
- Matrices y punzones de forja en caliente
- Matrices de extrusión en caliente:Extrusión en caliente de metales ligeros como aluminio y magnesio, así como para mandriles, punzones y matrices.
- Moldes de inyección de plástico:Esta es la aplicación más común, especialmente para mecanizar cavidades.
- Cuchillas de corte:Aplicaciones de cizallamiento en caliente.
- Herramientas de soldadura por fricción y agitación (FSW)1: FSW tools, particularly for welding aluminum plates, are often coated with TiN for enhanced performance.
- Componentes estructuralesEl acero H13 tiene una alta resistencia y puede mantener su dureza a altas temperaturas, por lo que se utiliza en componentes estructurales que están sujetos a altos esfuerzos, como trenes de aterrizaje de aeronaves, ganchos de detención y carcasas de cohetes en la industria aeroespacial.
2. Composición del acero H132
Elemento | Carbono (C) | Cromo (Cr) | Molibdeno (Mo) | Vanadio (V) | Silicio (Si) | Manganeso (Mn) | Fósforo (P) | Azufre (S) |
Contenido (%) | 0,32 – 0,45 | 4.75 - 5.50 | 1.10 – 1.75 | 0.80 - 1.20 | 0.80 – 1.25 | 0.20 - 0.60 | ≤ 0.030 | ≤ 0.030 |
H13 tool steel equivalent grades’ composition
Grado | Estándar | C (%) | Si (%) | Manganeso (%) | P (%) | S (%) | Cr (%) | Mo (%) | V (%) |
1.2344 | DIN | 0.37-0.42 | 0.90-1.20 | 0.30-0.50 | ≤0.030 | ≤0.030 | 4.80-5.50 | 1.20-1.50 | 0.90-1.10 |
SKD61 | JIS | 0.35-0.42 | 0.80-1.20 | 0.25-0.50 | ≤0.030 | ≤0.030 | 4.80-5.50 | 1.00-1.50 | 0.80-1.15 |
4Cr5MoSiV1 | GB | 0.32-0.42 | 0.80-1.20 | 0.20-0.50 | ≤0.030 | ≤0.030 | 4.75-5.50 | 1.10-1.75 | 0.80-1.20 |
3. Propiedades del acero para herramientas H13
H13 mold steel is a hot-work tool steel widely used globally. It is characterized by high strength, high toughness, high hardenability, and resistance to thermal cracking. In particular, it can maintain its strength and hardness at high temperatures. Additionally, it has excellent comprehensive mechanical properties and high tempering stability.
3.1 Propiedades mecánicas
Las propiedades específicas dependen en gran medida de la temperatura de revenido. A continuación se presentan las propiedades mecánicas longitudinales típicas cuando air-cooled from 1025 °C (1875 °F) and tempered:
Propiedades mecánicas clave (valores típicos a temperatura ambiente, doble revenido 2 h + 2 h)
Propiedad | Temple a 527 °C (980 °F) | Temple a 555 °C (1030 °F) | Temple a 575 °C (1065 °F) |
Dureza | 52 HRC | 50 HRC | 48 HRC |
Resistencia a la tracción (Rm) | 1960 MPa (284 ksi) | 1835 MPa (266 ksi) | 1730 MPa (251 ksi) |
Límite elástico (Rp0,2) | 1570 MPa (228 ksi) | 1530 MPa (222 ksi) | 1470 MPa (213 ksi) |
Elongación (en 4D) | 13.0% | 13.1% | 13.5% |
Reducción de la superficie | 46.2% | 50.1% | 52.4% |
Impacto Charpy con muesca en V | 16 J (12 pies·lbf) | 24 J (18 ft·lbf) | 27 J (20 ft·lbf) |
3.2 Propiedades físicas
Propiedad | Valor |
---|---|
Densidad | 7,75 – 7,80 g/cm3 |
Resistencia a la tracción, última | 1200 – 2050 MPa (174000 – 231000 psi) |
Resistencia a la tracción, límite elástico | 1000 – 1380 MPa (145000 – 200000 psi) |
Dureza | 45-52 HRC (dureza Rockwell C) |
Resistencia al impacto | 20-40 J/cm2 |
Resistencia a la compresión | 2550 MPa |
3.3 Otras propiedades importantes:
- Resistencia al desgaste: Excelente resistencia al desgaste. Para mejorar aún más esta resistencia, se puede nitrurar, lo que aumenta su dureza superficial a más de 1000 HV (>70 HRC).
- Dureza y resistencia al impacto: Excelente resistencia al impacto y buena ductilidad.
- Resistencia a la comprobación de calor: Excelente resistencia al agrietamiento térmico, característica que está influenciada por su tenacidad al impacto sin entalla y dureza.
- Resistencia a la fatiga: Buena resistencia a la fatiga, y en este sentido este acero tiene una ventaja sobre acero de aleación 4340.
- Estabilidad dimensional: Cuando este acero se somete a un enfriamiento por aire, su volumen generalmente se expande aproximadamente 0,001 pulg./pulg. (0,001 mm/mm).
- Maquinabilidad: Si la clasificación de maquinabilidad del acero al carbono con un contenido de carbono de 1% se establece en 100, entonces el H13 tiene una clasificación de maquinabilidad de 70 cuando está recocido correctamente.
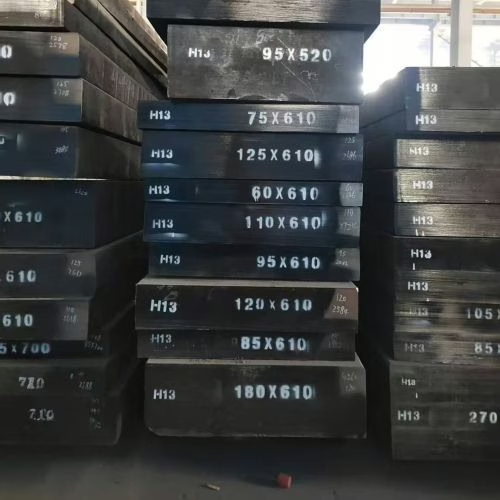
¿Está interesado en el acero para herramientas H13? Complete el siguiente formulario para contactarnos y le responderemos en 12 horas.
4. Tratamiento térmico
El Tratamiento térmico del acero H13 implica varios pasos críticos para lograr las propiedades deseadas:
4.1 Forjado y enfriamiento posterior al forjado
Es fácil de forjar y normalmente se forja a temperaturas entre 1120 y 1150 °C (2050 a 2100 °F)Antes de forjar, recomendamos precalentar el acero a 790 a 815 °C (1450 a 1500 °F), calentándolo luego uniformemente a la temperatura de forja requerida.
Durante el forjado, la temperatura del material no debe descender por debajo de 925 °C (1700 °F)Si está a punto de caer por debajo de esta temperatura, debe recalentarse hasta la temperatura de forja requerida.
Este material es un acero de temple al aire que debe enfriarse lentamente para evitar el agrietamiento por tensión. Después del forjado, el material debe colocarse en un horno a 790 °C (1450 °F) y se mantiene hasta que la temperatura sea uniforme; luego se enfría lentamente.
4.2 Recocido (recocido esferoidizado)
Después del paso anterior, el material H13 debe someterse a un recocido esferoidizante, cuyo objetivo es eliminar la tensión, mejorar la tenacidad y la ductilidad y formar la microestructura requerida.
Los detalles específicos del proceso de recocido son los siguientes: calentar el acero a 871 °C (1600 °F), mantener durante 1 hora por pulgada (25,4 mm) de espesor, luego enfriar a una velocidad de 14 °C (25 °F) por hora hasta 482 °C (900 °F), seguido de enfriamiento con aire a temperatura ambiente.
4.3 Normalización (generalmente no recomendada)
Because of the risk of cracking, we generally do not recommend normalizing treatment for H13, especially when a controlled atmosphere furnace does not prevent surface decarburization. However, this normalizing treatment can still improve the uniformity of the material. This step must be performed immediately after spheroidizing annealing.
Los pasos específicos son los siguientes: precalentar a aproximadamente 790 °C (1450 °F), calentar lenta y uniformemente a 1040 a 1065 °C (1900 a 1950 °F), mantener durante 1 hora por cada 25 mm (1 pulgada) de espesor y luego enfriar al aire.
4.4 Hardening (Austenitizing and Quenching)
La temperatura de endurecimiento es de alrededor de 1030 °C (1885 °F)Otras fuentes sugieren un rango de 1010-1040 °C (1850-1900 °F), o específicamente 1025 °C (1875 °F).
El H13 es un acero de temple al aire, por lo que recomendamos realizar un tratamiento de precalentamiento. El objetivo es estabilizar la estructura cristalina, reducir la dureza, aumentar la ductilidad, mejorar la maquinabilidad, promover una estructura de grano uniforme y minimizar la distorsión y el agrietamiento. La temperatura de precalentamiento es 815 °C (1500 °F)Para un cubo de 25 mm (1"), debe precalentarse a 650 °C (1200 °F) y mantenerse así de 10 a 15 minutos antes de preparar el horno para el remojo. Para piezas delicadas, podría ser necesario un precalentamiento adicional.
Después del precalentamiento, eleve la temperatura del horno a su temperatura de austenización de 1010 °C (1850 °F). The soaking process then begins, with the soaking time calculated from the moment the material’s temperature is the same as the furnace temperature. Specific details are as follows: For parts thicker than 1“ (25mm), the soak time is typically half an hour per inch of the smallest cross-section. For smaller parts, specific soak times are provided: 1/8” (3.175mm) for 10-15 minutes, 1/4” (6.350mm) for 15 minutes, 1/2“ (12.70mm) for 20 minutes, 3/4” (19.05mm) for 25-30 minutes, and 1” (25mm) for 30 minutes.
El temple al aire puede minimizar la tensión residual y reducir el choque térmico. Si bien el temple al aire es el método más común para el H13, el temple en aceite también se utiliza en la práctica, pero aumenta las tensiones internas. La dureza después del temple es de 52-54 HRC. Durante el ciclo de temple del material, el siguiente paso de revenido debe realizarse inmediatamente a una temperatura no inferior a 66 °C/150 °F para evitar el agrietamiento.
4.5 Templado
El objetivo es reducir la fragilidad, transformar la martensita en una microestructura más estable, mejorar la tenacidad, aliviar tensiones conservando la dureza.
We recommend tempering H13 twice or even three times to achieve optimal toughness and extend tool life. The first tempering temperature is 565 °C (1050 °F), la segunda temperatura de revenido es 550°C (1025°F), con cada ciclo con una duración de 2 horas por pulgada (25 mm) de espesor.
After tempering, the hardness varies with the tempering temperature. For example, as-quenched H13 has a hardness of 52-54 HRC. Tempering at 204°C (400°F) results in 51-53 HRC, while tempering at 538°C (1000°F) yields 47-48 HRC, and at 621°C (1150°F), it can be 36-38 HRC. Typical tempering temperatures range from 540-620°C (1000-1150°F), producing a stable microstructure that makes the material most suitable for high-temperature applications.
It is essential to Evite templar el H13 a alrededor de 500 °C (930 °F), as this temperature yields the lowest toughness.
5. Soldadura
El acero H13 es fácilmente soldable, especialmente para aplicaciones de reparación en moldes, herramientas y matrices. La soldadura por arco de tungsteno con gas (GTAW o TIG) es el proceso de soldadura más adecuado para moldes, herramientas y matrices H13, y también puede realizarse mediante un proceso con gas inerte o electrodos revestidos. Al soldar, se deben utilizar el voltaje y la corriente de arco mínimos recomendados, y el electrodo debe moverse lentamente en línea recta para minimizar la aportación de calor. Limpie la escoria con frecuencia y martille las soldaduras mientras aún estén calientes (por encima de 370 °C o 700 °F); nunca martille una soldadura en frío.
- Preheating. Preheating is essential before welding H13 steel, as cold welding can easily cause cracking. The preheating temperature should be between 110°C (230°F) and 375°C (707°F).
- Filler Wire. H13 filler wire is the preferred choice. If H13 filler wire is not available on site, a general-purpose medium-hardness tool steel filler wire designed specifically for thermal and cold working tools can be used.
- Shielding Gas. Argon is the standard welding gas for TIG welding H13, and it protects the weld seam from contamination. Hydrogen can be used as a backing shielding gas for the underside of the weld when an explosion risk is not present.
- Post-Welding Treatment for H13 Tool Steel. After welding, H13 welded parts (especially thick-walled welded parts) should be cooled slowly, either in a furnace at the preheating temperature or using an insulating medium (such as furnace slag, lime, mica, or diatomaceous earth). After slow cooling, the weld should undergo complete spheroidizing annealing.
6. Ventajas y desventajas del acero H13
6.1 Ventajas
- Excelente tenacidad y resistencia al impacto.
- Alta resistencia al desgaste. H13’s relatively high vanadium content makes it very resistant to abrasion. This is because vanadium promotes the formation of very hard, stable carbides (like V8C7, MC type), which significantly increase wear resistance. Nitriding treatment can further improve the wear resistance of H13.
- Excelente dureza en caliente, resistencia al revenido y estabilidad térmica.
- Alta templabilidad y estabilidad dimensional
- Buena resistencia a la corrosión por calor (fatiga térmica)
- Soldabilidad y maquinabilidad. El H13 es fácilmente soldable y, después de un tratamiento de recocido adecuado, tiene buena maquinabilidad.
6.2 Desventajas
- Alto costoEl acero para herramientas H13 generalmente se ve limitado por su alto costo. El alto contenido de elementos de aleación contribuye a este costo. Por supuesto, esto es solo una desventaja relativa. Nuestros clientes en China tienen una demanda muy alta de acero H13, que supera las 2000 toneladas mensuales, principalmente para perfiles de aluminio.
- Dificultades de fabricación y procesamiento. The heat treatment process for H13 during production may be relatively complex, which is mainly a challenge for manufacturers. Additionally, its machinability is more difficult compared to low-alloy materials. As mentioned earlier in the article, the good machinability of H13 is one of its advantages, so both advantages and disadvantages are relative.
- Problemas de tenacidad y fragilidad. Es bastante sensible a la fragilización por temple, donde la precipitación de carburos a lo largo de los límites de grano de austenita previa puede reducir significativamente la tenacidad al crear caminos para la propagación de grietas, especialmente para materiales de sección grande.
- Susceptibilidad al agrietamiento y distorsión. Los procesos de temple inadecuados, un tiempo de revenido insuficiente o temperaturas de revenido bajas pueden aumentar el riesgo de agrietamiento y deformación.
- Rendimiento limitado a altas temperaturas. Aunque el H13 es un acero para trabajo en caliente, su resistencia disminuye a temperaturas superiores a 650 °C.
7. Comparar con otros aceros
7.1 Comparado con el acero para herramientas D2
El acero H13 se utiliza en condiciones de alta temperatura, donde presenta una excelente resistencia al ablandamiento, la fatiga térmica y el impacto. Sin embargo, en comparación con el acero trabajado en frío, presenta una menor resistencia al desgaste. El acero D2, por otro lado, se desempeña excepcionalmente bien en aplicaciones de trabajo en frío, ofreciendo alta resistencia al desgaste y excelente estabilidad dimensional. Sin embargo, en comparación con el H13, el D2 presenta menor tenacidad y un rendimiento inferior en condiciones de alta temperatura.
A continuación se presenta una comparación lado a lado que resalta sus diferencias y similitudes clave:
Característica/Propiedad | Acero para herramientas H13 (serie AISI H) | Acero para herramientas D2 (serie AISI D) |
Aplicación principal | Hot Work: Ideal for applications involving high temperatures and thermal fatigue, such as die casting molds, hot forging, and hot extrusion. Also used in plastic injection molds. | Cold Work: Best suited for applications requiring high wear resistance at room temperature, like long-run dies, blanking, piercing, and trimming tools. |
Clasificación | Acero para matrices para trabajo en caliente, grupo cromo 5%. | Acero para herramientas de trabajo en frío con alto contenido de carbono y cromo. |
Resistencia al desgaste | Muy bien | Excelente |
Dureza | Alta resistencia al impacto, buena resistencia a la fractura frágil. | Menor resistencia al impacto y tenacidad en comparación con el H13 |
Dureza en caliente / Resistencia al revenido | Excelente, funciona bien hasta 700°C (1300°F) | Limitado, no diseñado para uso a alta temperatura; generalmente restringido por debajo de 205-260 °C (400-500 °F) debido al ablandamiento |
Templabilidad | Endurecimiento profundo, endurecimiento al aire, mínima distorsión. Se puede templar en secciones grandes. | Endurecimiento profundo, endurecimiento al aire, mínimo movimiento y distorsión durante el endurecimiento. Puede endurecerse completamente en secciones grandes. |
Estabilidad dimensional | Distorsión muy baja; se expande aproximadamente 0,001 pulg./pulg. cuando se enfría al aire. | Distorsión mínima; se expande/contrae aproximadamente 0,0005 pulg./pulg. cuando se enfría al aire. |
Maquinabilidad | Bien | Pobre |
Comprobación de calor | Muy buena resistencia, especialmente en forma fundida. | Not a primary characteristic, as it’s typically used in cold applications. |
Soldabilidad | Fácilmente soldable | Difícil de soldar (no soldable) |
7.2 Compared to M2 tool steel
Acero para herramientas M2 is primarily used for high-speed cutting, boasting excellent wear resistance and thermal hardness.
Característica | Acero H13 | Acero M2 |
Clasificación | Acero para matrices de trabajo en caliente (acero Cr 5%). | Acero rápido tipo molibdeno (HSS), uso general. |
Uso principal | Aplicaciones que implican altas temperaturas y cargas, como fundición a presión, forja en caliente, matrices de extrusión en caliente y moldes de plástico. | Operaciones de corte y mecanizado de metales. |
Resistencia al desgaste | Alto, | Muy alto |
Dureza | Buena, excelente resistencia al impacto, | Bien, |
Dureza en caliente / Resistencia al revenido | Excelente resistencia al revenido, manteniendo alta dureza y resistencia a temperaturas elevadas gracias al temple secundario. Puede operar hasta 700 °C. | Muy alta, superior al H13, especialmente a temperaturas más altas; desarrolla dureza secundaria. Las adiciones de cobalto mejoran aún más la dureza en caliente. |
Templabilidad | Templabilidad profunda, se puede endurecer en grandes secciones mediante enfriamiento por aire. | Gran templabilidad. El rango de endurecimiento más tolerante entre los aceros rápidos (HSS). |
Distorsión | Mínimo debido al endurecimiento por aire. | Medio. |
Maquinabilidad | Bastante bueno en estado recocido. | Medio. |
Soldabilidad | Fácilmente soldable | Difícil de soldar (no soldable) |
8. Suministro de formas y dimensiones
El acero para herramientas H13 que suministramos está disponible en tres formas: barra plana, bloque y barra redondaLas dimensiones de la barra plana varían entre: Ancho: 20–600 mm × Grosor: 20–400 mm × Longitud: 1000–5500 mm. Las dimensiones de la barra redonda varían entre un diámetro de 20–400 mm y una longitud de 1000–5500 mm. Las dimensiones del bloque se obtienen cortando la barra plana.
Para tamaños más pequeños, como barras redondas con un diámetro inferior a 70 mm, utilizamos el proceso de laminado en caliente. Para tamaños superiores a 70 mm, ofrecemos productos forjados.
También ofrecemos el proceso ESR (Refusión por Electroescoria), diseñado a medida para satisfacer las necesidades del cliente. La ventaja es una mejor microestructura interna, pero su coste es mayor. Contáctenos para conocer sus requisitos específicos.
Pruebas UT: septiembre de 1921-84 D/d, E/e.
Tratamiento de superficie: acabados superficiales originales negros, pelados, mecanizados/torneados, pulidos, rectificados o fresados.
Estado del inventario: No disponemos de acero para herramientas H13. Organizamos la producción según los pedidos de los clientes.
Plazo de entrega: Los materiales para hornos de arco eléctrico (EAF) tardan entre 30 y 45 días. Los materiales ESR tardan aproximadamente 60 días.
Muchos de nuestros clientes optan por procesos sin ESR por razones de rentabilidad. Por favor, converse directamente con nosotros sobre sus necesidades específicas.
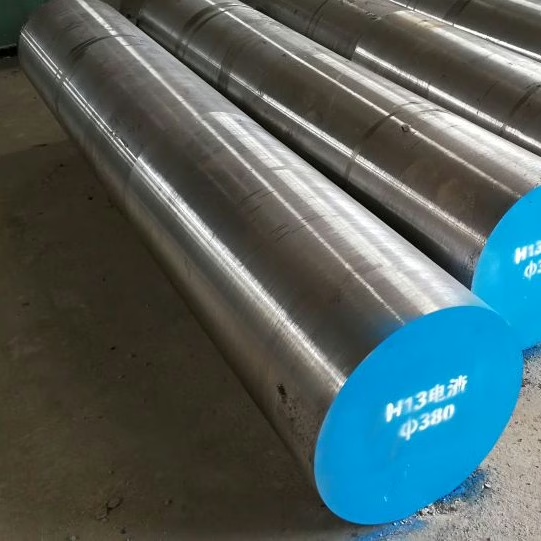
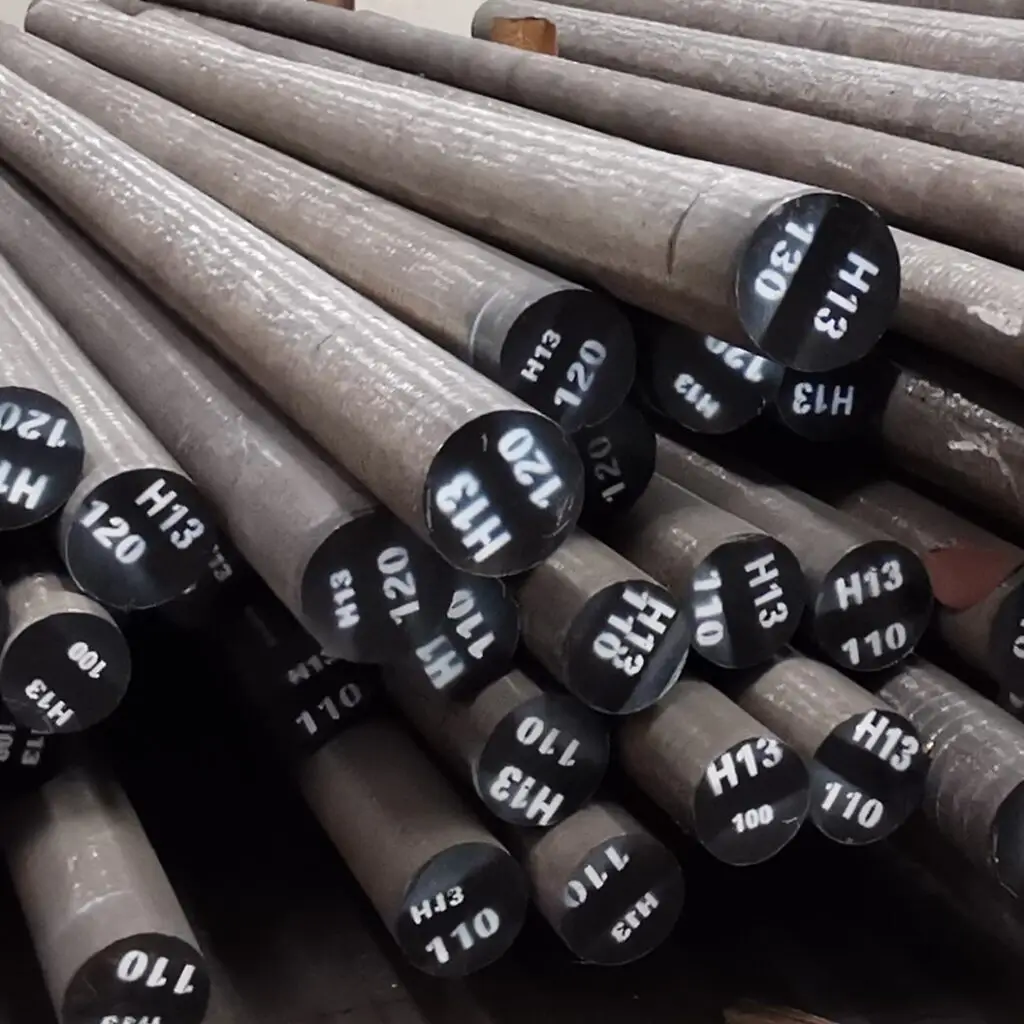
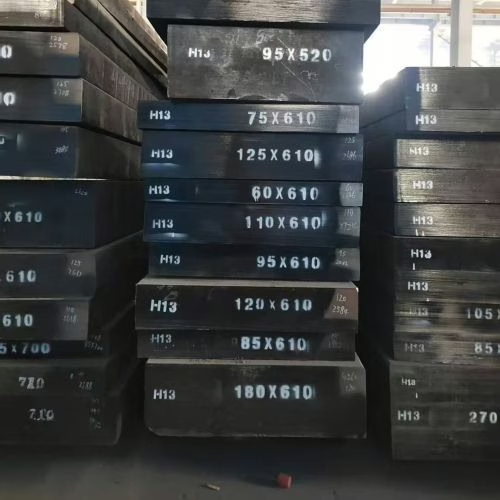
- Totten, G. E., & MacKenzie, D. S. (Eds.). (2003). Manual del aluminio: Volumen 2: Producción de aleaciones y fabricación de materiales (p. 581). ↩︎
- Bringas, J. E. (Ed.). (2002). Manual de normas comparativas mundiales del acero (2nd ed., p. 434). ASTM International. ↩︎
Preguntas frecuentes
Sí, el acero para herramientas H13 se puede soldar, pero su soldabilidad es limitada y requiere procedimientos específicos debido a su naturaleza de endurecimiento al aire y su susceptibilidad al agrietamiento durante y después de la soldadura. El precalentamiento antes de soldar, el mantenimiento de temperaturas adecuadas entre pasadas y el tratamiento térmico posterior a la soldadura (PWHT) son esenciales para minimizar el agrietamiento y preservar sus propiedades. La soldadura por arco de tungsteno con gas (GTAW) se recomienda con frecuencia para su control.
No, H13 steel is not classified as a high-speed steel. It is identified as a hot-work tool steel.
La resistencia última (también conocida como resistencia a la tracción) del acero H13 varía según la temperatura de revenido y el proceso de fabricación. Las propiedades mecánicas longitudinales típicas del acero H13 a temperatura ambiente, basadas en barras revenidas a diferentes niveles de dureza, son las siguientes:
When tempered at 527 °C (980 °F), the tensile strength is 1960 MPa (284 ksi).
When tempered at 555 °C (1030 °F), the tensile strength is 1835 MPa (266 ksi).
When tempered at 575 °C (1065 °F), the tensile strength is 1730 MPa (251 ksi).
When tempered at 593 °C (1100 °F), the tensile strength is 1580 MPa (229 ksi).
When tempered at 605 °C (1120 °F), the tensile strength is 1495 MPa (217 ksi).
Sí, el acero H13 puede ser difícil de mecanizar, especialmente una vez endurecido. Sin embargo, su maquinabilidad puede verse afectada por su estado y la operación de mecanizado específica.
The recommended hardness range for H13 tool steel is generally 40-55 HRC. Specific applications and tempering temperatures can result in values ranging from 36 HRC (at a tempering temperature of 621°C) to 56 HRC (at a tempering temperature of 500°C). Forging tools in service typically range from 38-52 HRC.
The primary difference between H11 and H13 steel lies in their vanadium content and the resulting impact on their properties. H13 may show slightly lower toughness than H11, especially during quench embrittlement.
Key characteristics include exceptional heat resistance, high toughness, high hot strength, high hot wear resistance, high retention of hardness, and strong resistance to thermal fatigue (heat checking)
Yes, H13 tool steel has excellent wear resistance. This property can be further improved by nitriding, which can increase surface hardness to over 1000 HV, equivalent to more than 70 HRC.
H13 tool steel has excellent resistance to thermal fatigue cracking.
Typical mechanical properties at room temperature (when double tempered) include an Ultimate Tensile Strength ranging from 1200 to 2050 MPa (174,000-231,000 psi) and Yield Strength from 1000 to 1570 MPa (145,000-228,000 psi). Specific values are highly dependent on the tempering temperature. It also possesses good impact strength and ductility, with a Charpy V-notch impact strength of 16-27 J depending on tempering.
No, el acero para herramientas H13 no es muy resistente a la corrosión en comparación con el acero inoxidable u otras aleaciones especializadas. Se elige principalmente por su resistencia y resistencia al calor, más que por sus propiedades anticorrosivas, y es propenso a oxidarse en entornos agresivos, como aquellos con humedad o plásticos químicamente agresivos.
Los mecanismos de fallo comunes incluyen desgaste, fatiga mecánica, agrietamiento grueso, deformación plástica y agrietamiento por fatiga térmica (fisuras térmicas). Estos pueden verse agravados por factores como una temperatura demasiado baja del tocho, un diseño inadecuado de la matriz (p. ej., radios agudos, paredes delgadas), un tratamiento térmico o superficial inadecuado, un soporte insuficiente de la matriz o niveles elevados de tensión en la cavidad.
El proceso de endurecimiento suele implicar un precalentamiento a unos 815 °C (1500 °F), seguido de un aumento de temperatura a un rango de austenización de 1010-1040 °C (1850-1900 °F), seguido de un temple al aire. El revenido es crucial y suele realizarse dos o tres veces, a temperaturas que suelen estar entre 540-620 °C (1000-1150 °F), con una duración aproximada de 2 horas por cada pulgada de espesor. Es fundamental evitar el revenido a temperaturas cercanas a 500 °C (930 °F), ya que produce la menor tenacidad.
Recomendamos realizar inspecciones periódicas para detectar signos de desgaste o fatiga, aplicar un repintado o retemplado cuando sea necesario y evitar el sobrecalentamiento durante la operación, ya que puede ablandar el material. Un precalentamiento adecuado de la matriz también reduce significativamente el riesgo de fallos catastróficos por agrietamiento.
Los tratamientos superficiales se aplican comúnmente al acero para herramientas H13 para mejorar la resistencia al desgaste. La nitruración, por ejemplo, es un tratamiento termoquímico que crea una capa superficial dura y puede inducir tensión residual de compresión, lo que ayuda a contrarrestar el agrietamiento por calor. Sin embargo, la capa nitrurada puede ser frágil, por lo que es necesario un control cuidadoso del espesor (p. ej., normalmente no más de 0,3 mm).
H13 tool steel has various international equivalents, including AISI H13 (USA), X40CrMoV5-1 (Europe/Germany DIN 1.2344), and SKD61 (Japan JIS), and 4Cr5MoSiV1(China GB)
Desbloquee un rendimiento superior con nuestro acero para herramientas H13
En Aobo Steel, aprovechamos más de 20 años de experiencia en forja Para ofrecer acero para herramientas H13 de primera calidad. Reconocido por su excepcional dureza en caliente, tenacidad y resistencia a la fatiga térmica, nuestro H13 es la opción ideal para sus aplicaciones más exigentes, como fundición a presión, matrices de extrusión y herramientas de forja.
Asociese con un proveedor confiable respaldado por más de 40 fuentes de material estableObtenga la calidad y confiabilidad constantes de las que dependen sus operaciones.
¿Está listo para mejorar su producción con H13 de máxima calidad?
Simplemente complete el formulario de contacto a continuación. Nuestros especialistas en H13 se pondrán en contacto con usted lo antes posible para hablar sobre sus necesidades y ofrecerle un presupuesto personalizado.
Explora nuestros otros productos
D2/1.2379/SKD11
D3/1.2080/SKD1
D6/1.2436/SKD2
A2/1.23663/SKD12
O1/1.2510/SKS3
O2/1.2842
S1/1.2550
S7/1.2355
DC53
H13/1.2344/SKD61
H11/1.2343/SKD6
H21/1.2581/SKD7
L6/1.2714/SKT4
M2/1.3343/SKH51
M35/1.3243/SKH55
M42/1.3247/SKH59
P20/1.2311
P20+Ni/1.2738
420/1.2083/2Cr13
acero inoxidable 422
Acero para cojinetes 52100
Acero inoxidable 440C
4140/42CrMo4/SCM440
4340/34CrNiMo6/1.6582
4130
5140/42Cr4/SCR440
SCM415