Seleccionar el grado de acero correcto es fundamental para el rendimiento y la longevidad de sus herramientas. Acero AoboGracias a nuestra amplia experiencia en la forja de acero para herramientas, a menudo orientamos a nuestros clientes sobre las diferencias entre los grados más comunes. Dos opciones comunes, especialmente para aplicaciones de moldes y matrices, son P20 acero para herramientas y Acero para herramientas H13Si bien ambos son caballos de batalla, tienen propiedades distintas que los hacen adecuados para diferentes trabajos. Veamos las diferencias técnicas clave.
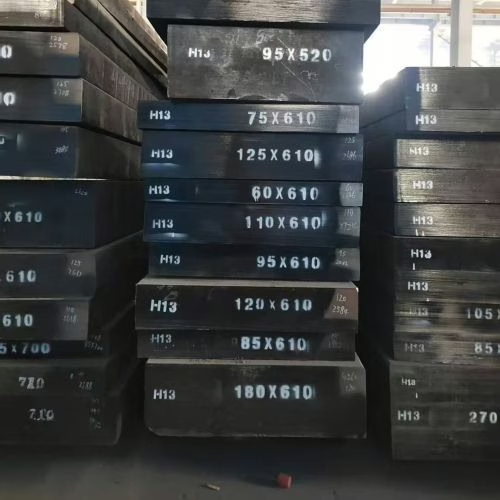
Clasificación y uso básico
- P20: Este acero se clasifica típicamente como un acero para herramientas de aleación de medio carbono, conocido principalmente como acero para moldes. Se considera un grado versátil para el moldeo de plástico y ciertas aplicaciones de fundición a presión, en particular para zinc.
- H13: Este grado entra dentro de la categoría de cromo 5%. aceros para herramientas de trabajo en calienteTambién es reconocido por sus capacidades de resistencia ultraalta.
Composición química: la base del rendimiento
Las principales diferencias entre P20 y H13 provienen de sus composiciones de aleación:
- P20: Generalmente contiene entre 0,18 y 0,401 TP3T de carbono (a menudo alrededor de 0,351 TP3T), junto con silicio, manganeso, cromo (entre 0,5 y 2,001 TP3T) y molibdeno (entre 0,30 y 0,551 TP3T).
- H13: Si bien los niveles de carbono pueden solaparse (0,30-0,451 TP3T), el H13 presenta un paquete de aleación significativamente diferente, según lo definen normas como ASTM A681 o JIS SKD61. Presenta un contenido mucho mayor de cromo (4,75-5,501 TP3T), un contenido mayor de molibdeno (1,10-1,751 TP3T) y una adición crucial de vanadio (0,80-1,201 TP3T). Este contenido de vanadio contribuye significativamente a sus características de rendimiento.
Aplicaciones
- P20: Ampliamente utilizado para moldes de inyección de plástico.1Matrices de fundición a presión de zinc y bloques de soporte. Es una opción ideal para tiradas de producción de longitud intermedia.
- H13: Como acero para trabajo en caliente, el H13 destaca en entornos de alta temperatura con ciclos térmicos. Esto incluye moldes de fundición a presión (especialmente para aluminio u otras aleaciones de alto punto de fusión), matrices de extrusión en caliente, matrices de forja en caliente y moldes de inyección de plástico exigentes que requieren mayor dureza o mejor gestión térmica que el P20.
Procesamiento y dureza
Cómo se suministran estos aceros y tratado térmicamente Hay una diferencia práctica importante:
- P20: Dureza del acero P20 Tiene una dureza de 28-32 HRC y se suministra generalmente pretemplada. Esto permite a los fabricantes de moldes mecanizar cavidades directamente y utilizar la herramienta sin necesidad de tratamientos térmicos adicionales a alta temperatura, minimizando así el riesgo de distorsión. Para una mayor dureza superficial y tener puesto Para mejorar la resistencia en moldes de plástico, el P20 puede cementarse después del mecanizado. Generalmente se templa en aceite.
- H13: Aunque a veces se utiliza preendurecido, el H13 suele ser tratado térmicamente por el usuario para alcanzar niveles de dureza más altos (p. ej., 45-54 HRC o incluso superiores para aplicaciones específicas) y resistencias superiores a 2070 MPa (300 ksi). El H13 es un acero de temple al aire, lo que significa que puede endurecerse en secciones grandes con mínima distorsión durante el proceso de enfriamiento. También es un acero de temple secundario, que mantiene una alta dureza y resistencia a temperaturas de operación elevadas, conocidas como "dureza roja.”A menudo se recomienda el doble revenido.
Características clave de rendimiento
Vamos a compararlos directamente en cuanto a propiedades críticas:
- Resistencia al desgaste: El H13 generalmente ofrece una resistencia superior al desgaste y a la abrasión debido a su mayor contenido de vanadio, que forma carburos duros. El P20 tiene una resistencia al desgaste aceptable, lo que lo hace adecuado para muchos moldes, pero el H13 es más adecuado para condiciones abrasivas o para tiradas más largas. La carburación mejora significativamente el desgaste superficial del P20.
- Tenacidad: Ambos aceros se consideran resistentes. El H13 generalmente exhibe una excelente resistencia al impacto y tenacidad, que son vitales para resistir el agrietamiento en aplicaciones exigentes. El P20 también ofrece buena tenacidad.
- Resistencia al temple (dureza roja): Este es un diferenciador importante. El H13 tiene una excelente resistencia al ablandamiento a altas temperaturas, lo que lo hace ideal para aplicaciones de trabajo en caliente. La resistencia del P20 al revenido es menor.
- Estabilidad dimensional: La naturaleza de endurecimiento al aire del H13 resulta en una distorsión mínima durante el tratamiento térmico. El P20 (endurecimiento al aceite) ofrece mayor estabilidad que los aceros de endurecimiento al agua, pero generalmente menor que el H13.
- Maquinabilidad: P20 es conocido por su excelente maquinabilidad En estado pretemplado. El H13 también presenta buena maquinabilidad cuando se recoce adecuadamente.
- Pulibilidad: Tanto el P20 como el H13 permiten obtener una superficie pulida de buena calidad, esencial para moldes de plástico de alta calidad. El H13 suele pulirse bien a durezas más altas (superiores a 50 HRC).
- Resistencia a la comprobación de calor: Fundamental para la fundición a presión, el H13 ofrece buena resistencia al agrietamiento por fatiga térmica, comúnmente conocido como agrietamiento por calor. El P20 es adecuado para la fundición a presión a baja temperatura, como el zinc, pero el H13 es preferible para trabajos en caliente más exigentes.
- Calidad interna: Para herramientas grandes o críticas, la limpieza interna del acero es vital. El H13 se produce a menudo mediante la Refusión por Electroescoria (ESR) o procesos similares, lo que proporciona mayor limpieza y uniformidad en comparación con los aceros fundidos convencionalmente. Esto mejora el rendimiento, especialmente la resistencia a la fatiga térmica.
Tomar la decisión
- Elija P20: Si Necesita un acero rentable y fácilmente mecanizable para moldes de plástico o fundición a baja temperatura, pretemplado para mayor comodidad y apto para series intermedias. La carburación es una opción para mejorar la resistencia al desgaste superficial.
- Elija H13: Si Si su aplicación implica altas temperaturas de operación, requiere una resistencia superior al desgaste, alta dureza en rojo, máxima estabilidad dimensional durante el tratamiento térmico, resistencia al agrietamiento por calor o altos niveles de dureza (superiores a 50 HRC) para moldes o herramientas de trabajo en caliente exigentes, considere el H13. Su mayor contenido de aleación (Cr, Mo, V) proporciona un rendimiento superior en estas condiciones, lo que a menudo justifica el uso de un producto más limpio. ESR/Calidades VAR para aplicaciones críticas.
Comprender estas diferencias le ayudará a seleccionar el acero para herramientas óptimo para sus necesidades específicas. Si tiene alguna pregunta o necesita grados específicos, como P20 o H13, no dude en contactarnos en sales@aobosteel.com. Contamos con la experiencia para ayudarle a elegir el acero adecuado.