Acero para herramientas H11 El objetivo del tratamiento térmico es transformar la microestructura blanda y recocida, compuesta principalmente de ferrita y carburos de aleación, en una estructura martensítica endurecida y revenida con carburos beneficiosos que proporcionan las propiedades de corte o trabajo deseadas. Este proceso multietapa suele incluir precalentamiento, temple, temple y revenido.
¿Qué es el acero para herramientas H11? El H11 es un popular acero para herramientas de trabajo en caliente con cromo 5%. Se utiliza ampliamente en aplicaciones de alta temperatura, como moldes de fundición a presión, laminado en caliente, extrusión en caliente, forjado en caliente e incluso en componentes estructurales de la tecnología aeroespacial, como ejes de rotores de helicópteros.
A continuación, presentamos los pasos para el tratamiento térmico del acero H11.
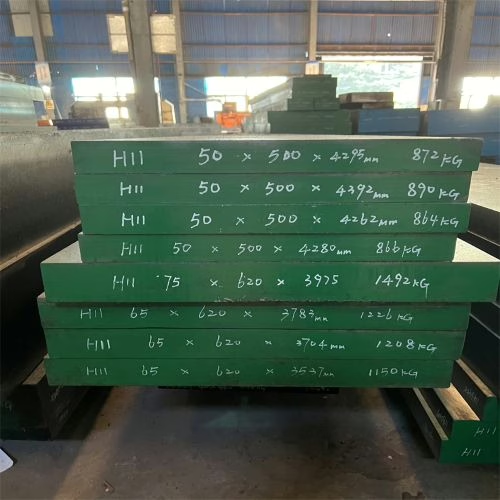
1. Precalentamiento y Alivio del estrés
El precalentamiento tiene tres funciones: reduce el choque térmico (que puede causar distorsión o agrietamiento), aumenta la productividad del equipo al reducir el tiempo del horno de alta temperatura y minimiza la carburación/descarburación si la atmósfera del horno de alta temperatura no es neutra.
La temperatura de precalentamiento para el H11 es de 650 °C (1200 °F) y se mantiene a esta temperatura durante 10 a 15 minutos. Para piezas con cambios significativos en la sección transversal, o para herramientas grandes o complejas, es más seguro calentar lentamente el horno hasta la temperatura de precalentamiento o colocar la pieza sobre el horno para eliminar el frío antes de colocarla en su interior. Para el tratamiento térmico en atmósfera o vacío, se suele utilizar un único precalentamiento entre 790 y 845 °C (1450 y 1550 °F).1.
Aunque el precalentamiento puede aliviar algunas tensiones, el revenido convencional es más efectivo. El revenido a alta temperatura del acero H11 puede aliviar significativamente las tensiones. El revenido busca reducir las tensiones internas que pueden causar distorsión o agrietamiento durante el tratamiento térmico o el servicio posterior. Se recomienda encarecidamente un revenido de revenido después de operaciones importantes de mecanizado, rectificado, soldadura o electroerosión (EDM). La temperatura de revenido suele ser de 14 a 28 °C (25 a 50 °F) inferior a la temperatura de revenido anterior. La temperatura de revenido se mencionará más adelante.
2. Austenitización (endurecimiento)
Este es el segundo paso crítico, donde el acero se calienta a alta temperatura para disolver diversos carburos de aleación complejos y transformar la estructura de ferrita-perlita en austenita. El rango de temperatura de austenización para el acero H11 es de 995 a 1025 °C (1825 a 1875 °F). Los tiempos de remojo varían de 20 minutos, más 5 minutos adicionales por cada 25 mm (1 pulgada) de espesor de sección. Para el acero H13, las temperaturas de austenización son generalmente más altas, de 1050 a 1180 °C (1920 a 2155 °F). Más información. Acero H11 vs H13.
3. Enfriamiento
Enfriamiento Es el proceso de enfriamiento rápido de un material desde la temperatura de austenización para transformar la austenita en una estructura martensítica dura. El acero H11 es un acero de temple al aire, lo que minimiza la tensión residual y los cambios dimensionales al enfriarse al aire. El acero H11 se enfría al aire a 52–65 °C (125–150 °F) antes de someterse a un tratamiento de revenido.
En términos generales, todos los aceros para herramientas trabajados en caliente no se pueden templar con agua, ya que el temple con agua conlleva un alto riesgo de agrietamiento.
4. Templado
Templado Se realiza después del temple. El objetivo es aumentar la tenacidad del acero y aliviar las elevadas tensiones internas que hacen que la estructura martensítica, una vez templada, sea muy susceptible al agrietamiento. El H11 es un acero de temple secundario. Su rendimiento óptimo se alcanza después de dos revenidos. La temperatura de revenido del acero H11 es de 510 °C (950 °F), y el tiempo de mantenimiento para ambos revenidos es de dos horas. Tras el temple, el acero H11 debe revenirse inmediatamente cuando alcance la temperatura recomendada para evitar el agrietamiento.
5. Recocido
Recocido Se realiza para ablandar el acero, haciéndolo apto para el mecanizado, y para lograr uniformidad microestructural para los tratamientos de temple posteriores. Las piezas forjadas H11 deben enfriarse lentamente a temperatura ambiente después del forjado y luego recocerse completamente. 870–900 °C (1600–1650 °F), remojo durante aproximadamente 1 hora por pulgada (2,4 min/mm) de espesor, y luego enfriamiento lento a una velocidad de 14 °C (25 °F) por hora hasta 482 °C (900 °F) antes de enfriarse al aire a temperatura ambiente. Este proceso da como resultado una dureza máxima de recocido de aproximadamente 220 HB.
Los pasos anteriores son los tratamientos térmicos comunes para el acero H11, basados en nuestra experiencia y literatura especializada. Esperamos que esta información sea útil para los usuarios de acero H11. Si necesita materiales de acero H11, no dude en contactarnos.
- ASM Internacional. (1989). Manual de ASM, Volumen 16: Mecanizado (pág. 120). ASM Internacional. ↩︎
Obtenga una cotización competitiva para acero para herramientas H11
Con más de 20 años de experiencia en forja, Aobo Steel es su socio de confianza para acero para herramientas H11 de alto rendimiento. Ofrecemos no solo materiales, sino también soluciones. Aproveche nuestro profundo conocimiento del sector y nuestra confiable cadena de suministro para el éxito de su proyecto.
✉Contáctanos rellenando el siguiente formulario.