Qual é a principal diferença entre H13 e Aço para ferramentas A2? Resumindo: o H13 é a escolha ideal para aplicações de trabalho a quente, onde as ferramentas operam em altas temperaturas. O A2, por outro lado, é projetado para aplicações de trabalho a frio, destacando-se em tarefas onde a estabilidade dimensional e a boa resistência ao desgaste em temperaturas ambientes são essenciais..
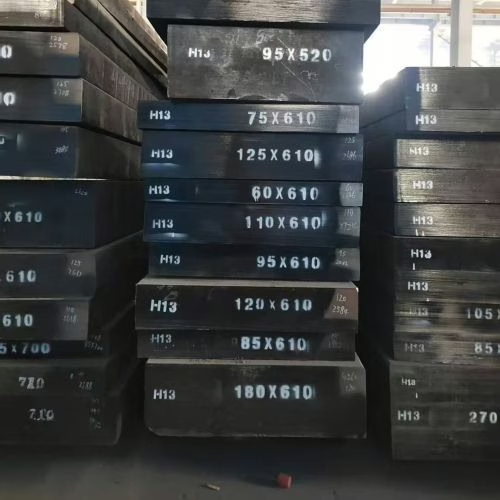
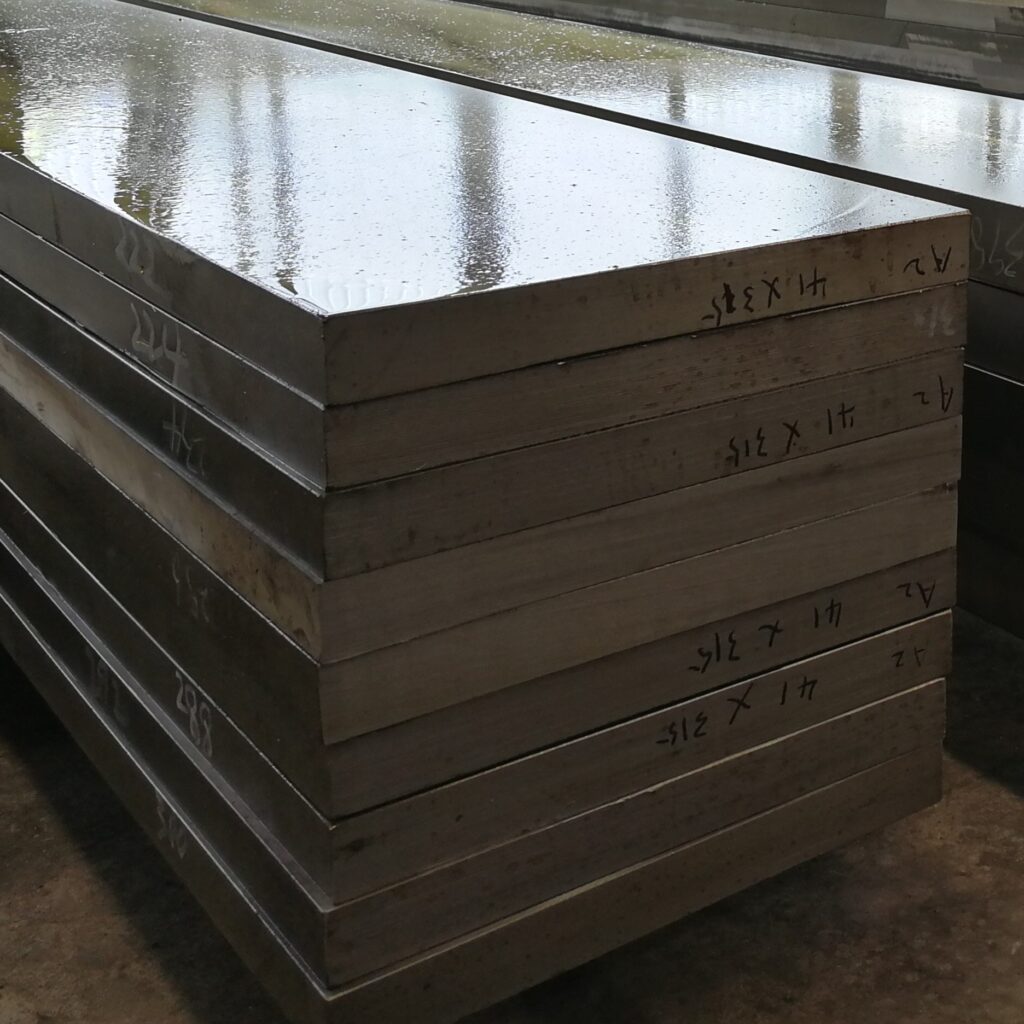
Compreendendo os princípios básicos: classificação e propósito
Os aços para ferramentas são categorizados com base em sua finalidade e propriedades. Tanto o H13 quanto o A2 são bastante respeitados, mas pertencem a grupos diferentes:
H13: O Especialista em Trabalho a Quente
H13 é classificado como um Aço para ferramentas de trabalho a quente, parte da série "H" do sistema AISI (American Iron and Steel Institute). Especificamente, trata-se de um aço para trabalho a quente à base de cromo. Toda a sua filosofia de design gira em torno da manutenção da resistência e da resistência ao desgaste e à fadiga térmica quando os materiais esquentam – como forjamento, fundição sob pressão ou extrusão.
A2: O executor do trabalho a frio
A2 se enquadra na série 'A', designando-o como um Endurecimento ao ar, liga média Aço para ferramentas de trabalho a frio. Como o nome sugere, ele foi projetado para trabalhos realizados em temperatura ambiente ou próxima dela. Para o A2, as prioridades são manter seu formato preciso durante tratamento térmico e proporcionando uma boa combinação de vestir resistência e tenacidade para tarefas como estampagem, conformação e corte.
O que há dentro? Uma análise da composição química
As propriedades distintas do H13 e do A2 se devem à sua composição química. Os elementos de liga são cuidadosamente selecionados para proporcionar características de desempenho específicas.
Destaques da composição H13
- Carbono (C): Em volta 0.35-0.45%. Esse nível moderado de carbono contribui para sua tenacidade, o que é essencial para aplicações de trabalho a quente que geralmente envolvem impacto.
- Cromo (Cr): Sobre 5%. O cromo é essencial para temperabilidade, resistência à corrosão e resistência a altas temperaturas.
- Molibdênio (Mo): Aproximadamente 1.35-1.4%. Mo aumenta a resistência ao calor, a tenacidade e a temperabilidade.
- Vanádio (V): Em volta 1%. O vanádio é crucial para a formação de carbonetos duros, o que aumenta a resistência ao desgaste, especialmente em temperaturas elevadas, e ajuda a refinar a estrutura dos grãos.
- Silício (Si): Aproximadamente 1%. O silício melhora a resistência a altas temperaturas e a resistência à oxidação.
Essa composição, particularmente o equilíbrio de Cr, Mo e V, confere ao H13 sua capacidade de suportar os rigores do trabalho a quente.
Destaques da Composição A2
- Carbono (C): Em volta 1.0%. Esse maior teor de carbono é um dos principais fatores que contribuem para a maior dureza e resistência ao desgaste do A2 em cenários de trabalho a frio.
- Cromo (Cr): Também por perto 5%. Assim como no H13, o cromo auxilia na temperabilidade e na resistência ao desgaste.
- Molibdênio (Mo): Tipicamente 1.0-1.1%. Mo contribui para a temperabilidade e tenacidade.
- Vanádio (V): Uma quantidade menor, geralmente 0.2-0.25%. Embora menor que no H13, ele ainda desempenha um papel na resistência ao desgaste.
A2 geralmente tem um equilíbrio diferente, adequado para aplicações de trabalho a frio.
O alto teor de carbono no A2 é um diferencial significativo, preparando-o para dureza e desgaste em aplicações a frio.
Tratamento Térmico: Desbloqueando o Desempenho
O tratamento térmico transforma esses aços de seu estado mais macio e usinável em ferramentas duras e duráveis. Tanto o H13 quanto o A2 possuem características de tratamento térmico fáceis de usar.
Endurecimento e temperabilidade
Tanto H13 quanto A2 são aços endurecíveis ao ar. Esta é uma grande vantagem. Isso significa que eles podem ser endurecidos por resfriamento ao ar parado após serem aquecidos até sua austenitização (temperatura de têmpera). A têmpera ao ar minimiza as tensões internas que podem levar à distorção ou trincas, o que é especialmente benéfico para formatos de ferramentas complexos. Ambos os aços também apresentam boa temperabilidade, o que significa que podem endurecer até uma profundidade significativa, tornando-os adequados para ferramentas maiores.
Têmpera e Estabilidade Dimensional
Após o endurecimento, os aços para ferramentas são revenidos para aliviar tensões e atingir o equilíbrio desejado entre dureza e tenacidade.
- H13 exposições endurecimento secundárioIsso significa que, quando revenido em temperaturas mais altas (tipicamente em torno de 510 °C ou 950 °F), ele ganha dureza devido à precipitação de carbonetos de liga fina. Essa característica é vital para seu desempenho em trabalho a quente, pois ajuda o H13 a manter a dureza mesmo quando exposto a altas temperaturas de operação. Geralmente, ele é revenido duas vezes para garantir estabilidade e tenacidade.
- A2 também apresenta um pico de endurecimento secundário, embora tipicamente menos pronunciado que o H13. Sua principal vantagem durante o tratamento térmico é sua excelente estabilidade dimensional. O A2 é conhecido pela alteração mínima de tamanho e baixa distorção após têmpera e revenimento, o que é essencial para ferramentas de precisão.
Tratamentos de superfície
Para propriedades de superfície melhoradas, tratamentos como nitretação Pode ser aplicado tanto ao H13 quanto ao A2. A nitretação cria uma camada superficial muito dura, melhorando significativamente a resistência ao desgaste e, em alguns casos, a resistência à fadiga. O H13, em particular, se beneficia muito da nitretação em aplicações como matrizes de fundição sob pressão, onde enfrenta altas temperaturas e desgaste abrasivo.
Propriedades mecânicas principais: o essencial
Vamos comparar algumas das propriedades mecânicas mais importantes para um usuário de ferramenta:
Dureza
- A2 é geralmente usado em níveis de dureza de trabalho mais elevados, normalmente 56-61 HRC (Dureza Rockwell C). Essa dureza mais alta é resultado direto de seu maior teor de carbono e é ideal para resistir ao desgaste em trabalho a frio.
- H13 é normalmente usado em níveis de dureza de trabalho que variam de 42-54 HRC, dependendo da aplicação específica. Por exemplo, ferramentas de fundição sob pressão podem estar na faixa de 44-48 HRC, enquanto aplicações que exigem maior resistência ao choque podem ser ligeiramente mais macias. Sua dureza após têmpera é inferior à do aço A2.
Dureza a Quente (Resistência ao Amolecimento à Temperatura)
É aqui que o H13 realmente se destaca e é a principal razão pela qual é um aço para trabalho a quente. Ele retém uma parcela significativa de sua dureza mesmo em temperaturas elevadas (até cerca de 550 °C ou 1020 °F, e pode suportar exposições curtas ainda mais altas). Essa "dureza vermelha" impede que a ferramenta amoleça e se deforme em contato com os materiais quentes da peça.
O A2, por ser um aço para trabalho a frio, não apresenta boa dureza a quente. Sua resistência diminui rapidamente em temperaturas muito acima de 200-260 °C (400-500 °F), tornando-o inadequado para trabalho a quente.
Robustez
Tenacidade é a capacidade do aço de absorver energia e resistir à fratura, especialmente sob impacto.
- H13 ofertas excelente tenacidade e resistência ao impacto, especialmente para aços para trabalho a quente. Isso é crucial para aplicações como matrizes de forjamento que sofrem cargas de impacto repetidas. Seu menor teor de carbono (em comparação com o A2) contribui significativamente para isso.
- A2 fornece boa tenacidade para um aço trabalhado a frio, oferecendo um melhor equilíbrio entre tenacidade e resistência ao desgaste do que algumas outras classes trabalhadas a frio, como a série D. É mais resistente do que os aços endurecíveis em óleo, mas geralmente não é tão resistente quanto os aços dedicados à resistência a choques (série S).
Resistência ao desgaste
Resistência ao desgaste é a capacidade de resistir à abrasão e à perda de material por atrito.
- A2 ofertas boa a alta resistência à abrasão para aplicações de trabalho a frio. Seu maior teor de carbono e os carbonetos resultantes conferem essa propriedade. Geralmente, situa-se entre os aços para ferramentas da série S (menor resistência ao desgaste) e da série D (maior resistência ao desgaste).
- H13 também fornece boa resistência ao desgaste, especialmente em temperaturas elevadas. Os carbonetos de vanádio em sua estrutura contribuem para isso. Quando nitretado, a resistência ao desgaste do H13 é significativamente aumentada. No entanto, para desgaste a frio puramente abrasivo, sem altas temperaturas, o A2 normalmente teria uma vantagem.
Usinabilidade
Em seu estado recozido (amolecido), H13 geralmente oferece melhor usinabilidade do que A2. Isso pode ser uma consideração prática na fabricação de ferramentas complexas.
Aplicações típicas
Entender suas propriedades ajuda a explicar seus usos comuns:
Aplicações H13
Dada a sua resistência em altas temperaturas, o H13 é a melhor opção para:
- Matrizes de fundição sob pressão para alumínio, zinco e magnésio
- Matrizes e punções para forjamento a quente
- Ferramentas de extrusão (matrizes, mandris, revestimentos) para alumínio e latão
- Moldes de injeção de plástico, especialmente para plásticos de engenharia abrasivos ou de alta temperatura
- Lâminas de corte a quente
- Mandris e núcleos
Aplicações A2
Com sua excelente estabilidade dimensional e bom equilíbrio entre resistência ao desgaste e tenacidade, o A2 é amplamente utilizado para:
- Matrizes de estampagem e conformação
- Matrizes de cunhagem
- Matrizes de corte
- Facas de corte e facas de corte
- Punções e mandris para longas tiragens
- Medidores e ferramentas de medição
- Moldes que exigem alta precisão
Fazendo a escolha certa para sua fábrica
Então, ao decidir entre H13 e A2, a primeira pergunta a fazer é: A ferramenta sofrerá muito calor durante a operação?
- Se a resposta for sim (normalmente acima de 200-250°C ou 400-480°F), H13 é quase sempre a melhor escolha. Sua capacidade de manter dureza e resistência em temperaturas elevadas e sua boa tenacidade e resistência à fadiga térmica (verificação de calor) o tornam ideal para trabalho a quente.
- Se a aplicação for trabalho a frio, A2 é um forte candidato. Sua excelente estabilidade dimensional durante o tratamento térmico garante que suas ferramentas mantenham seu formato preciso. Oferece uma boa combinação de resistência ao desgaste e tenacidade para diversas operações de estampagem, conformação e corte.
Tanto o H13 quanto o A2 são excelentes aços para ferramentas quando utilizados no contexto adequado. Entender suas diferenças fundamentais em termos de resistência à temperatura, dureza, tenacidade e resistência ao desgaste ajudará você a selecionar o material mais eficaz e econômico para as necessidades da sua fábrica.
Se você tem aplicações específicas em mente ou precisa de mais orientações, não hesite em nos contatar. Temos vasta experiência em aço para ferramentas e podemos ajudar você a encontrar a solução perfeita.
Dê o próximo passo para soluções de aço superiores!
Nossos experientes especialistas da Aobo Steel estão prontos para ajudá-lo a selecionar o aço para ferramentas ideal para suas necessidades específicas. Aproveite preços competitivos, serviço incomparável e nosso amplo conhecimento do setor.
👇 Preencha o formulário abaixo para entrar em contato com nossa equipe de vendas hoje mesmo! 👇
(Você encontrará o formulário de contato logo abaixo desta seção)