Aço para ferramentas D2 O aço carbono 1095 e o aço carbono 1095 são materiais distintos, com composições, propriedades e aplicações distintas, tornando-os adequados para finalidades muito distintas. A principal distinção reside no fato de o D2 ser um aço para ferramentas de alta liga, projetado para resistência ao desgaste e estabilidade dimensional. Ao mesmo tempo, o 1095 é um aço comum de alto carbono, frequentemente utilizado por sua dureza após tratamento térmico. Apresentaremos os dois tipos de aço separadamente e, em seguida, os compararemos.
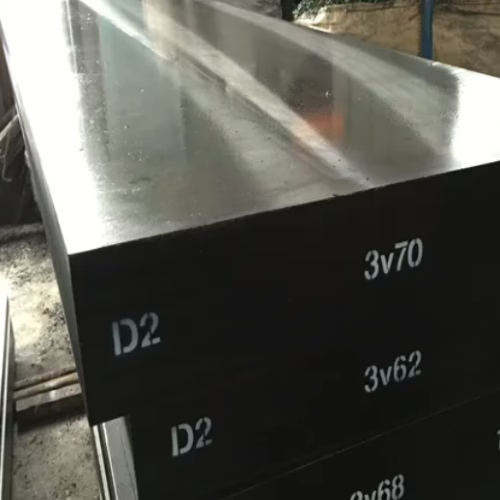
Introdução do aço D2
Classificação e Composição
O aço D2 é um aço com alto teor de carbono e alto teor de cromo aço para ferramentas de trabalho a frio. Também é conhecido como aço endurecível ao ar. As faixas de composição típicas para D2 incluem aproximadamente 1,40-1,60% de carbono, 11,00-13,00% de cromo, 0,70-1,20% de molibdênio e 0,50-1,10% de vanádio.
Propriedades
- Resistência ao desgaste: O aço D2 contém uma grande quantidade de carbonetos duros do tipo M7C3, ricos em cromo, que lhe conferem excelente vestir resistência. Aços da série D com alto teor de carbono, como Aço ferramenta D3 ou D6 (semelhante ao D3), têm um teor de carboneto ainda maior, proporcionando melhor resistência ao desgaste do que o D2.
- Dureza. Dureza do aço D2 pode ser alcançado em 58-64 HRC após tratamento térmico.
- Resistência. Comparado com outros aços para ferramentas, como Aço para ferramentas A2 ou aço resistente a impacto da série S, o aço D2 apresenta menor resistência ao desgaste. No entanto, no uso real, a resistência ao desgaste do aço D2 também pode ser considerada boa. O alto volume de carbonetos que contribui para a resistência ao desgaste também pode reduzir a tenacidade.
- Estabilidade dimensionalO aço D2 apresenta excelente estabilidade dimensional durante o tratamento térmico. A expansão ou contração pode ser de até aproximadamente 0,0005 polegadas por polegada (0,0005 mm/mm) quando resfriado ao ar a temperaturas de têmpera adequadas.
- Usinabilidade e retificaçãoO D2 é difícil de usinar e retificar, principalmente devido ao seu alto teor de cromo e à faixa de carbono. Sua classificação de usinabilidade é 45, em comparação com um aço carbono 1% com classificação 100.
- SoldabilidadeO aço ferramenta D2 é difícil de soldar ou não pode ser soldado por métodos convencionais devido ao seu alto teor de carbono e quantidade significativa de carbonetos.
- Comportamento de fratura: Sob carga de tração, o aço D2 normalmente apresenta quase nenhuma estriação antes da fratura (redução de cerca de 1,3% na área) e exibe uma superfície de fratura plana. A morfologia da superfície de fratura tende a ser mais rugosa, com microvazios maiores, em comparação com o aço O1.
Aço para ferramentas D2 Tratamento térmico
O D2 é um aço endurecível ao ar. A temperatura típica de têmpera varia de 1010 a 1095 °C (1850-2000 °F), seguida de têmpera ao ar. O revenimento é frequentemente realizado em dois ou até três ciclos, tipicamente na faixa de 205 a 540 °C (400 a 1000 °F), com recomendações específicas em torno de 480 a 515 °C (900 a 960 °F) para refinar a estrutura dos grãos e melhorar a resistência ao desgaste e o alívio de tensões. O superaquecimento durante a têmpera pode levar ao aumento da austenita retida, o que pode reduzir a dureza desejada. Para mais informações sobre este tópico, leia Como tratar termicamente o aço D2 adequadamente.
Aplicativos
O aço D2 é amplamente utilizado em aplicações de estampagem de longo prazo, punções e matrizes de estampagem e conformação a frio, punções e matrizes de perfuração, operações de forjamento e ferramentas de corte. Também é usado como inserto em carcaças de aço mais resistentes para matrizes. Saiba mais sobre Aplicações do aço D2 na fabricação de ferramentas.
Introdução de Aço 1095
Classificação e Composição
O aço 1095 é um aço simples de alto carbono. Sua composição é tipicamente de 0,90-1,03% de carbono e 0,30-0,50% de manganês.
Propriedades
- Dureza. O aço 1095 é capaz de atingir alta dureza após têmpera, por exemplo, uma dureza Rockwell C de 42 após têmpera e trefilação.
- Resistência ao escoamentoO limite de escoamento do aço 1095 varia dependendo de fatores como a espessura da barra e a severidade do resfriamento. Barras menores e aquelas resfriadas mais rapidamente pela temperatura de austenitização tendem a apresentar maior limite de escoamento.
- Ductilidade e Tenacidade. A ductilidade é influenciada pela dureza, geralmente diminuindo à medida que a dureza aumenta. O aço 1095 pode atingir melhor ductilidade em uma determinada dureza em comparação ao aço carbono comum, como o 1060, quando ligado.
- Resistência ao desgaste. Sua resistência ao desgaste é muito baixa (<1) quando comparada aos ferros fundidos com diversas estruturas de grafite (1,11 a >1,45).
- Resistência à corrosão: Aços carbono simples, como o 1095, são geralmente mais suscetíveis à corrosão em comparação aos aços resistentes às intempéries, como o Cor-Ten.
Tratamento térmico
O aço 1095 pode ser temperado em óleo, temperado a gás (ar forçado) ou resfriado ao ar parado (normalizado) a partir de temperaturas de austenitização (por exemplo, 900 °C/1650 °F) para atingir diferentes níveis de dureza. Por exemplo, o aço 1095 pode ser temperado em água a partir de 1000 °C (1830 °F) para formar uma estrutura em forma de agulha. A taxa de resfriamento do aço 1095 pode ser aumentada por uma incrustação muito leve (0,08 mm/0,003 pol.), mas uma incrustação pesada (0,13 mm/0,005 pol.) a retarda.
Aplicativos
O aço 1095 é um aço simples de alto carbono. É um material candidato para engrenagens.
Comparação direta: aço D2 vs. aço 1095
Recurso | Aço para ferramentas D2 | Aço carbono 1095 |
Tipo/Classe | Aço para ferramentas de trabalho a frio com alto teor de carbono e cromo; endurecimento ao ar. | Aço simples de alto carbono. |
Composição | Alto teor de liga (1,5% C, 12% Cr, 0,8% Mo, 0,9% V) para formação e endurecimento de carboneto. | Alto carbono (0,90-1,03% C) com adições de liga baixas ou nenhumas significativas, tipicamente 0,30-0,50% Mn. |
Mecanismo de Força Primário | Depende de alto volume de carbonetos de liga dura (M7C3) e têmpera secundária por revenimento. | O teor de carbono permite alta dureza por meio de transformação martensítica após têmpera, mas sem endurecimento secundário significativo. |
Resistência ao desgaste | Padrão excelente a altíssimo de resistência à abrasão. Superior a 1095 devido aos carbonetos de liga estáveis. | Bom para aplicações básicas após a têmpera, mas significativamente inferior ao D2. A resistência ao desgaste tende a aumentar com a quantidade/tamanho das partículas de carboneto, resultando em baixíssima resistência ao desgaste por abrasão. |
Dureza | Alto (58-64 HRC). | Alto após têmpera (por exemplo, 42 HRC), mas pode variar. Inferior a D2 em aplicações de alto desgaste. |
Robustez | De moderado a razoável. | Pode atingir tenacidade razoável para sua classe, mas geralmente inferior à de aços ligados com níveis de dureza comparáveis. Menor resistência à fratura frágil em comparação com aços de liga média para trabalho a quente. |
Estabilidade dimensional | Excelente, distorção mínima | Como a têmpera em água é frequentemente usada para têmpera completa, sua estabilidade interna é relativamente baixa. |
Usinabilidade | Difícil de usinar e retificar. | Difícil ou não soldável por métodos convencionais. |
Soldabilidade | Difícil ou não soldável por métodos convencionais. | Pode ser soldado, mas requer manuseio cuidadoso para evitar possíveis rachaduras causadas pelo hidrogênio. |
Comportamento de fratura | Têmpera em água, óleo ou gás a partir de temperaturas de austenitização (p. ex., 900 °C/1650 °F). Revenimento para atingir o equilíbrio desejado entre dureza e tenacidade. | Aços com alto teor de carbono geralmente apresentam menos fratura dúctil do que aços com baixo teor de carbono. |
Tratamento térmico | Endurecimento ao ar de 1010-1095 °C (1850-2000 °F), normalmente temperado dupla ou triplamente entre 205-540 °C (400-1000 °F). | Têmpera em água, óleo ou gás a partir de temperaturas de austenitização (p. ex., 900 °C/1650 °F). Revenimento para atingir o equilíbrio desejado entre dureza e tenacidade. |
Custo | Custo mais alto | Matrizes de longo curso, punções de estampagem e conformação a frio, ferramentas de corte e punções de perfuração. |
Aplicações típicas | Pode atingir tenacidade razoável para sua classe, mas geralmente inferior à de aços ligados com níveis de dureza comparáveis. Menor resistência à fratura frágil em comparação com aços de liga média para trabalho a quente. | Engrenagens, componentes gerais de alta dureza ou quando é preferível um tratamento térmico simples. |
Resumo
O aço D2 é projetado para extrema resistência ao desgaste e estabilidade dimensional em aplicações de ferramentas de alto desempenho, tornando-o adequado para longas séries de produção, nas quais o material da ferramenta contribui significativamente para os custos gerais em matrizes grandes. O aço 1095, por outro lado, é um aço de alto carbono mais econômico e simples, escolhido para aplicações que exigem alta dureza e resistência geral, sem a necessidade das propriedades superiores de desgaste do D2 ou adições complexas de liga.
Obtenha um orçamento competitivo para aço para ferramentas D2
Com mais de 20 anos de experiência em forjamento, a Aobo Steel é sua parceira de confiança para aço para ferramentas D2 de alto desempenho. Fornecemos não apenas materiais, mas também soluções. Aproveite nosso profundo conhecimento do setor e nossa cadeia de suprimentos confiável para o sucesso do seu projeto.
✉ Entre em contato conosco preenchendo o formulário abaixo.