Aço Aobo
Fornecimento de aço para ferramentas com boa relação custo-benefício para fábricas de pequeno e médio porte
Sobre a Aobo Steel
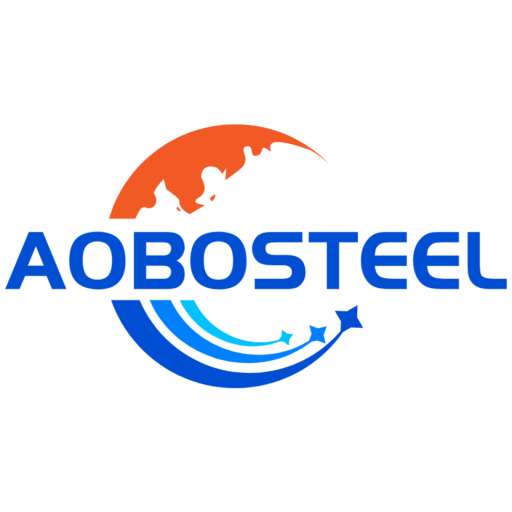
A Aobo Steel, originalmente estabelecida em 2003 como Fuding Equipment Engineering Co., Ltd., tem um rico histórico de experiência no processamento e forjamento de aços para ferramentas de alta qualidade. Desde a expansão para os mercados internacionais em 2017, construímos parcerias sólidas com mais de 30 clientes em cinco países. Nossa ampla experiência na fabricação de aços para ferramentas nos permite oferecer uma grande variedade de materiais de qualidade superior, incluindo D2, D3, H13, H11, O1, O2, A2 e muito mais. Esses produtos são projetados para atender aos requisitos exigentes dos setores que dependem de precisão, resistência e durabilidade. Na Aobo Steel, temos o compromisso de combinar nosso conhecimento técnico com um serviço excepcional para fornecer soluções personalizadas para cada cliente. Nossa dedicação à qualidade e à confiabilidade garante a entrega consistente de materiais que superam as expectativas e contribuem para o sucesso de nossos clientes.
Seu parceiro de confiança em soluções de aço para ferramentas de alta qualidade
Fornecendo aço para ferramentas durável, confiável e de alto desempenho, feito sob medida para atender às suas demandas industriais mais desafiadoras.
Do processamento à entrega, fornecemos aço para ferramentas de qualidade superior que supera suas expectativas.
D2, D3, H13, H11, O1, O2, A2 e muito mais. Ideal para forjamento, corte e aplicações industriais pesadas.
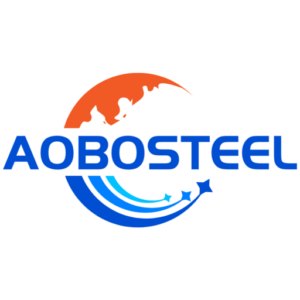
Encontre a solução perfeita para suas necessidades de aço para ferramentas
Principais produtos
Nossos principais produtos são o aço para ferramentas de trabalho a quente e o aço para ferramentas de trabalho a frio. Nossas principais vantagens competitivas incluem preço direto da fábrica, qualidade consistente e entrega rápida. Para obter mais produtos, visite nossa página de produtos.
Por que você deve escolher a Aobo Steel como seu fornecedor de aço para ferramentas?
Na Aobo Steel, temos orgulho de nossa excepcional capacidade de fornecimento e dedicação em atender às demandas dos clientes. Nossos embarques mensais ultrapassam 1.500 toneladas no mercado chinês, o que reflete nossa robusta capacidade de produção e entrega. Com uma forte rede de mais de 40 fornecedores confiáveis, garantimos um fornecimento constante de aços para ferramentas de alta qualidade para atender a várias necessidades do setor.
Para oferecer ainda mais flexibilidade, mantemos estoque de produtos selecionados, o que nos permite atender rapidamente a pedidos urgentes. Além disso, somos especializados em soluções totalmente personalizáveis, adaptando nossos produtos às suas especificações exatas para obter o desempenho ideal da aplicação.
Nossa localização estratégica, próxima ao rio Yangtze, nos dá uma vantagem significativa na logística de exportação, permitindo o envio rápido e econômico para clientes em todo o mundo. Se você precisa de produtos padrão ou pedidos personalizados, a Aobo Steel tem o compromisso de oferecer confiabilidade, qualidade e excelência em serviços.
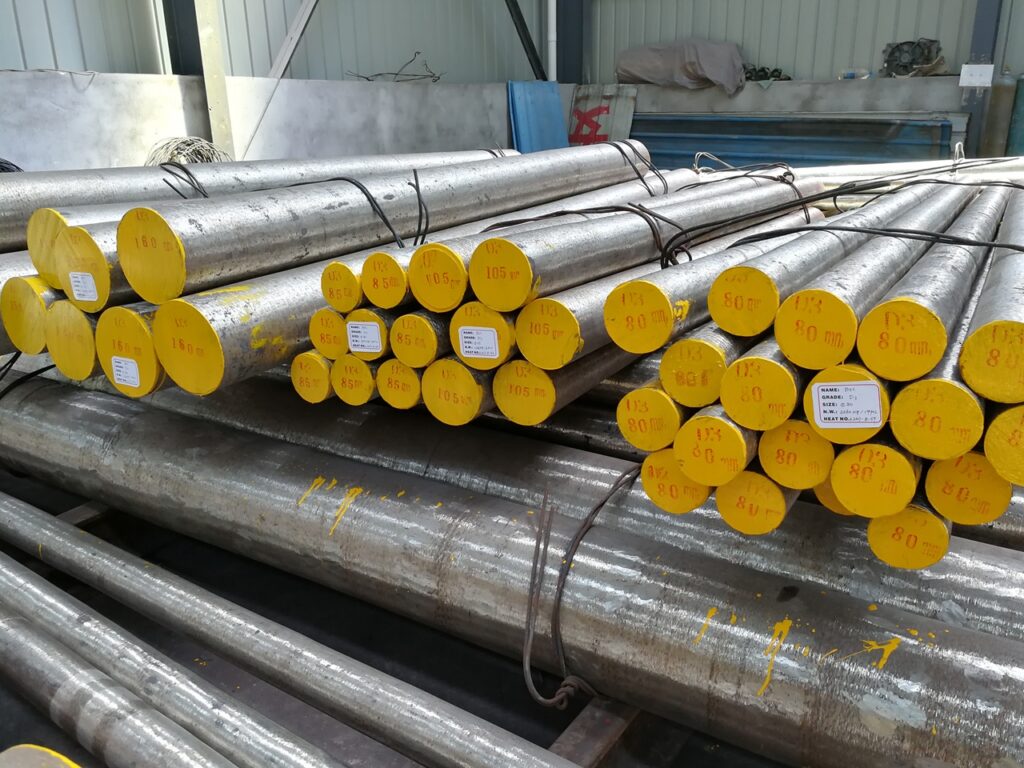
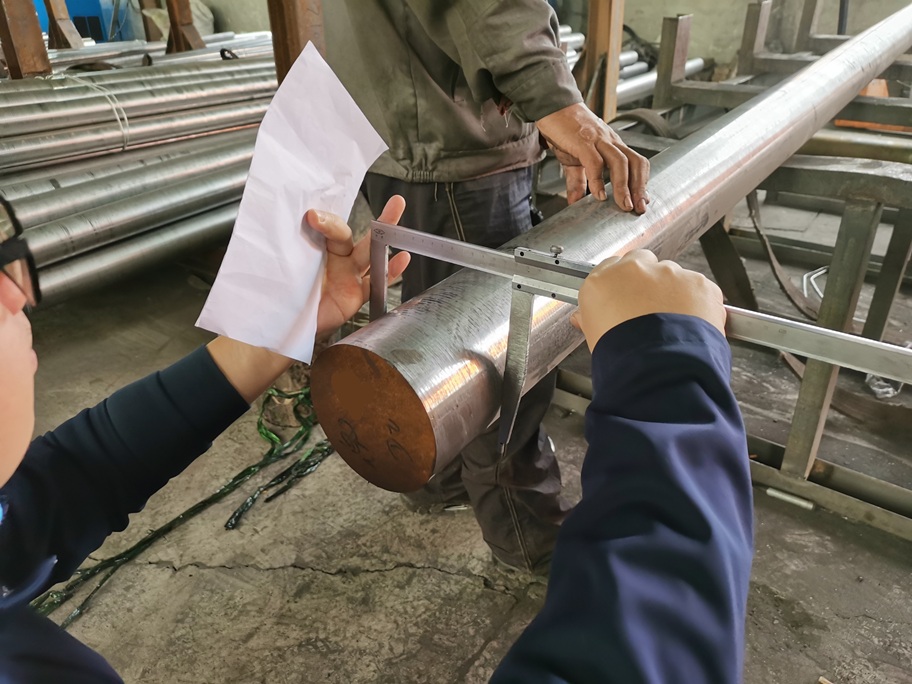
Na Aobo Steel, o controle de qualidade está no centro de nossas operações. Nossa dedicada equipe de testes, com mais de 20 anos de experiência, garante que cada produto atenda aos mais altos padrões antes de sair de nossas instalações. Nosso abrangente processo de garantia de qualidade inclui análise de composição química, exame metalográfico, teste de dureza, avaliação de desempenho físico e teste ultrassônico (UT) para detectar defeitos internos.
Para garantir a confiabilidade, realizamos a inspeção de qualidade 100% em todos os produtos antes do envio, garantindo que eles atendam às especificações exigidas e aos padrões do setor. Além disso, oferecemos suporte a inspeções de terceiros, mediante solicitação, para que nossos clientes tenham mais confiança na qualidade de nossos materiais. Com essa abordagem rigorosa, a Aobo Steel fornece consistentemente aços para ferramentas que oferecem desempenho superior e confiabilidade em várias aplicações.
Na Aobo Steel, nossa capacidade de serviço é projetada para atender às diversas necessidades dos clientes com eficiência e precisão. Fornecemos produtos totalmente personalizáveis, oferecendo tratamentos de superfície, descalcificação e opções de corte de comprimento personalizado para atender a requisitos específicos. Nossa experiente equipe de comércio exterior é bem versada em lidar com pedidos internacionais, garantindo uma comunicação tranquila e transações perfeitas.
Para oferecer o melhor serviço, garantimos uma resposta rápida de 24 horas a todas as consultas, o que nos permite atender às suas necessidades de forma imediata e eficaz. Na Aobo Steel, temos o compromisso de fornecer aços para ferramentas de alta qualidade e um atendimento excepcional ao cliente para apoiar o seu sucesso.
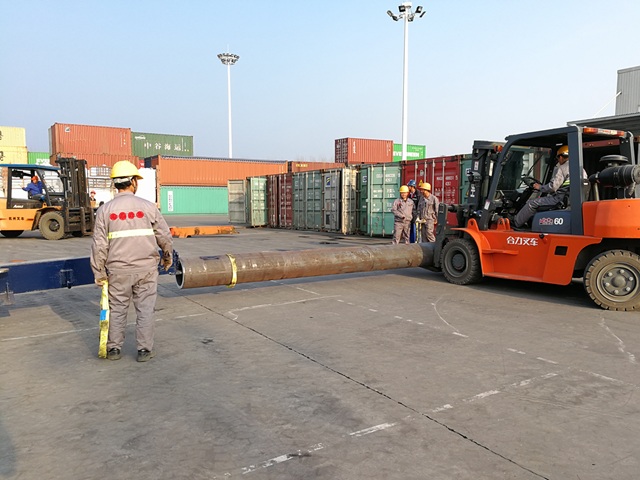
Como produzimos aço para ferramentas
O diagrama abaixo ilustra o processo de produção de aço forjado para ferramentas. Nossa produção se concentra principalmente no fornecimento de barras e chapas redondas forjadas de alta qualidade. O processo começa com a fusão e o refino das matérias-primas, a fundição e a refusão opcional para melhorar a pureza. O aço forjado é então moldado, recozido para melhor usinabilidade e processado para remover a escala de óxido. Por fim, o acabamento da superfície é aplicado para garantir a qualidade e a aparência desejadas.

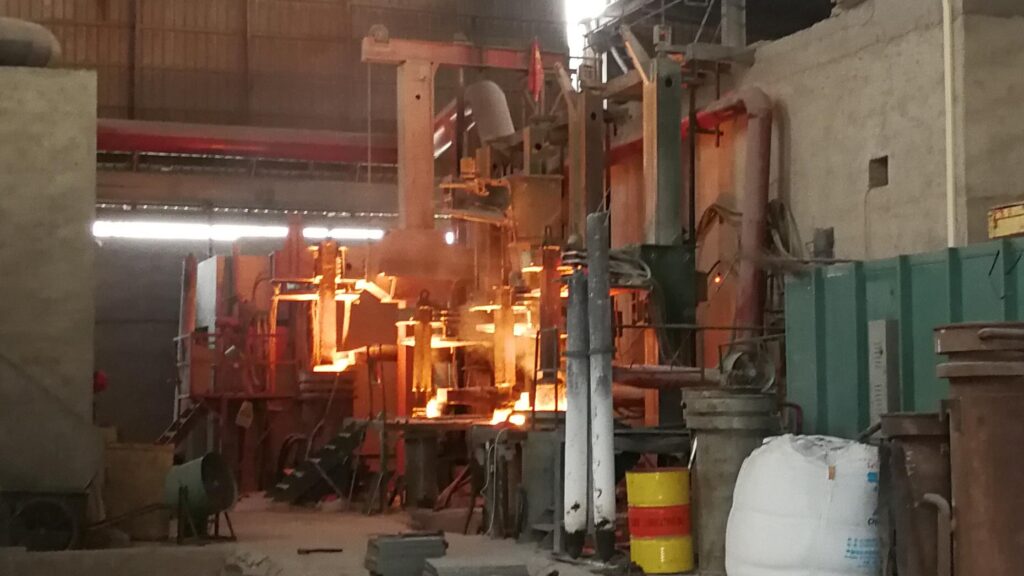
Esta imagem mostra uma máquina de Electroslag Remelting (ESR) em operação. O ESR é um processo especializado usado para melhorar a pureza e a qualidade do aço. Durante esse processo, um lingote pré-moldado é refundido sob uma camada de escória derretida, que atua como um purificador, removendo impurezas e inclusões. O aço refinado se solidifica à medida que esfria, resultando em um material com uma estrutura uniforme, propriedades mecânicas aprimoradas e qualidade de superfície superior. Esse processo é essencial para a produção de aços para ferramentas de alto desempenho e outros materiais críticos.
Neste vídeo, você pode ver o processo de forjamento de um lingote de aço para ferramentas aquecido. Após ser aquecido até a temperatura necessária, o lingote de aço para ferramentas é colocado em uma prensa mecânica. A prensa de forjamento aplica uma pressão imensa para moldar o aço na forma desejada, aprimorando sua estrutura interna e propriedades mecânicas. Esse processo elimina defeitos internos, refina a estrutura do grão e melhora a resistência e a durabilidade do material, tornando-o ideal para aplicações de alto desempenho.
Este vídeo mostra uma máquina de retificação sem centro processando uma barra redonda de aço para ferramentas. Nessa operação, a barra redonda é retificada com precisão para atingir o diâmetro e o acabamento de superfície necessários sem a necessidade de um centro para segurar o material. Esse processo de alta eficiência garante excelente precisão dimensional, qualidade de superfície lisa e arredondamento consistente, tornando o produto acabado adequado para aplicações industriais exigentes.
Obtenha acesso instantâneo aos preços de aço para ferramentas + recomendação de especialistas
👇[Solicite seu orçamento gratuito + Guia de Aço em PDF] 👇Sem compromisso. Rápido, profissional e 100% confidencial.