O1 tool steel is a low-alloy cold-worked tool steel. It has a certain degree of hardenability and wear resistance, with minimal quenching deformation. The carbide distribution is uniform, and the particles are fine. Manufacturers typically use tool steel O1 for manufacturing cold punching dies with small cross-sections, complex shapes, and various gauges and measuring tools. The equivalent grades of O1 are DIN 1.2510 (Germany), JIS SKS3 (Japan), and GB 9CrWMn (China).
1. Applications
- Dies & Punches: Blanking dies, Coining dies, Drawing dies, Forming dies, General Stamping (punches & dies for short/moderate runs), Thread-rolling dies, Cold-trimming dies
- Cutting & Machining Tools: General shop tool bits (economical choice), Shear blades (especially smaller ones), Taps, Reamers, Hobs, Slitting saws, Circular cutters, Drills
- Molds & Precision Parts: Plastic mold components (inserted cavities, master hubs), Gauges, Master tools
- General Tooling & Wear Parts: Cams, Bushings, Guides, Plain sliding bearings, Cam followers, Burnishing tools, Knurling tools, Feed rolls, Roll forming tooling (moderate runs)
2. O1 Steel Composition
C | Mn | Si | Cr | W | V | Ni | Mo | P | S |
0.85 – 1.00% | 1.00 – 1.40% | Max 0.50% | 0.40 – 0.60% | 0.40 – 0.60% | Max 0.30% | Max 0.30% | Max 0.30% | Max 0.03% | Max 0.03% |
[Reference: Davis, J. R. (Ed.). (1998). Metals handbook desk edition (2nd ed., p. 815). ASM International.]
3. Properties
- Hardness: It can achieve a hardness of 57-64 Rockwell C (HRC) through oil quenching. As the tempering temperature increases, the hardness decreases. For example, after tempering at 900°F (482°C), the hardness can be reduced to 47 HRC.
- Strength (Tensile and Yield): Tool steel O1 exhibits a tensile strength of 846 MPa and a 0.2% Offset Yield Strength of 829 MPa, with a general yield strength of 758 MPa. For a specific O1 composition, tensile strength can be as high as 1725 MPa (250 ksi) when tempered at 800°F (425°C), decreasing with higher tempering temperatures.
- Ductility and Toughness: O1 steel exhibits noticeable necking before fracture, with a substantial area reduction at fracture of nearly 20%. Its fracture surface typically displays a cup–cone mode. While generally having medium toughness, it shows superior impact strength compared to other O-type steels within the common working hardness range of 57 to 64 HRC. The ductility usually improves with increasing tempering temperature.
- Modulus of Elasticity: 211 GPa.
- Dimensional Stability: Good dimensional stability during heat treatment. When oil quenched from the correct hardening temperature, it typically expands by about 0.0015 inches per inch (0.0015 mm/mm). However, factors like part geometry and distortion (bending, bowing, or twisting) can influence the final dimensional changes.
- Machinability: Very good machinability. If the machinability of steel with 1% carbon content is set at 100, the machinability of O1 steel is 90.
4. O1 Heat treatment
The heat treating O1 steel generally involves four primary steps: preheating, austenitizing (hardening), quenching, and tempering.
4.1 Preheating
Preheating is an essential step for virtually all tool steels, including O1. Metallurgically, it doesn’t directly contribute to the hardening reaction but serves several crucial functions:
- Reduces Thermal Shock: Placing a cold tool into a hot furnace can cause thermal shock, leading to excessive distortion or cracking. Preheating minimizes this risk.
- Relieves Stress: It helps relieve some stress developed during machining or forming processes.
- Increases Equipment Productivity: By bringing the tool to a uniform temperature before the high-heat furnace, it decreases the time required in the austenitizing furnace.
- Reduces Surface Degradation: If the high-heat furnace isn’t neutral, preheating reduces carburization and decarburization.
The preheat temperature is 1200°F (650°C). The steel should be held at this temperature for 10 to 15 minutes, or until it is uniformly heated throughout its cross-section. DO NOT soak the tool steel for too long at this temperature, as it can upset the molecular structure. Based on our experience, if placing the part in a preheated furnace (up to 1200°F/650°C), first place it at the top of the furnace to remove any chill, which helps reduce thermal shock and lower the risk of cracking.
4.2 Austenitizing (Hardening)
After preheating, set the furnace temperature to the austenitizing temperature, which is 1500°F (815°C). We must heat the material until it fully reaches this temperature, which can be confirmed by observing its color matching the furnace. Once the temperature is consistent, begin calculating the soaking time. Soaking for an additional 5 minutes per inch of the smallest cross-section. While O1 steel may be damaged by over-soaking, its tolerance is generally higher compared to high-alloy steels.
4.3 Quenching
O1 steel is classified as an O-type steel because it is steel that uses oil as a quenching medium. Oil as a quenching medium is slower than water but safer, reducing internal stress and the tendency for cracking and deformation. After quenching, it should be cooled to 125 to 150°F (52 to 65°C). Once this temperature range is reached, tempering should be performed immediately.
[Reference: Bryson, W. E. (2007). Heat Treatment, Selection, and Application of Tool Steels (p. 91). Hanser Publications.]
4.4 Tempering
After quenching, the steel is in a highly stressed state and susceptible to cracking. Tempering serves to:
- Relieve Internal Stresses: It reduces the internal stresses set up during hardening, which can cause brittleness.
- Increase Toughness: Tempering significantly increases the steel’s toughness.
- Transform Retained Austenite: It transforms retained austenite from the quenching step into fresh martensite.
This steel typically requires only one tempering process, but in some cases, two tempering processes may be necessary. Two tempering processes can refine the grain structure to enhance toughness, making it suitable for parts with complex details or those requiring high strength.
The single tempering temperature is 350°F (175°C), with a soaking time of 2 hours per inch (25mm) of cross-section.
If a second tempering is performed, the temperature should be slightly lower, typically 325°F (160°C), and the part should be allowed to cool to room temperature between the two tempering processes.
The as-quenched O1 tool steel hardness is 64-65 HRC. After tempering at 350°F (177°C), the hardness is 62-63 HRC, and at 400°F (204°C), it is 62 HRC.
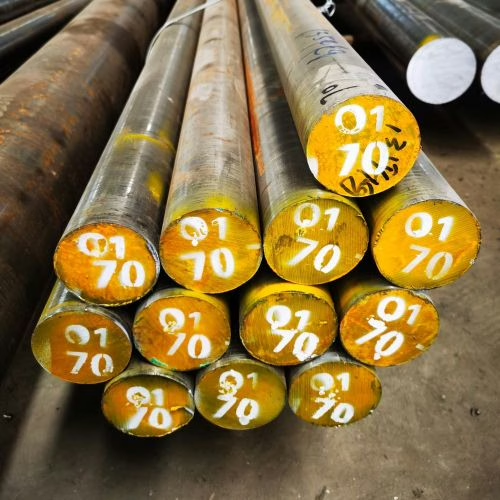
Interested in O1 Tool Steel?
Please fill out the form below to contact us today! We will respond within 12 hours!
5. Compare O1 steel with other steels
5.1 O1 Vs. A2 steel
We provide a direct comparison of the key properties and characteristics of O1 and A2 cold-work tool steels.
Feature | O1 Tool Steel | A2 Tool Steel |
Classification | Oil-hardening, manganese type. | Air-hardening, medium-alloy type. |
General Characteristics | Good edge-holding, high hardness, widely available, inexpensive. | Excellent dimensional stability (low distortion), high abrasion resistance. |
Primary Advantage | Good all-around performance and ease of heat treat for a lower cost. | Superior dimensional stability during heat treatment and better wear resistance. |
Hardness (Typical) | 57–62 HRC | 57–62 HRC |
Wear Resistance | Good | Very Good to Excellent; a standard for abrasion resistance. Better than O1. |
Toughness | High; Modulus of Toughness is 68 MPa. | Higher than O1; provides better toughness. Modulus of Toughness is 81 MPa. |
Dimensional Stability | Very low distortion, but less stable than A2. Expands ~0.0015 in./in. | Minimum movement during hardening; considered a standard for stability. |
Machinability | Excellent (rated 90 vs. 1% carbon steel at 100). | High. |
Austenitizing Temp. | Lower: 802–816 °C (1475–1500 °F) | Higher: 925–980 °C (1700–1800 °F) |
Quenching Medium | Oil | Air |
Tempering | Single temper is often sufficient. | Double tempering is recommended. Higher resistance to softening. |
Typical Applications | Short-run blanking/forming dies, punches, woodworking knives, master hubs. | Long-run blanking/forming dies, punches, mold inserts, thread-rolling dies. |
5.2 O1 Vs. O2 steel
Feature | O1 Tool Steel | O2 Tool Steel |
Hardness (Typical) | 57-62 HRC | 57-62 HRC |
Wear Resistance | Good | High |
Toughness | Good; slightly higher than other oil-hardening steels. | Medium |
Dimensional Stability | Very Low Distortion | Very Low Distortion |
Machinability | Excellent | Good |
Hardenability | Medium | Medium |
Hardening Temperature | 802–816°C (1475–1500°F) | 760–790°C (1400–1450°F) |
Heat Treat Concerns | Prone to decarburization and thermal shock cracking. | Not specified as a primary concern. |
5.3 O1 tool steel Vs. D2
Feature | O1 Tool Steel | D2 Tool Steel |
AISI Group | Oil-hardening cold-work tool steel | High-carbon, high-chromium cold-work die steel |
Quenching Medium | Oil-quenching | Air-hardening |
Hardness (typical) | 57-62 HRC (can be 62-63 HRC) | 54-61 HRC (can be 60-62 HRC) |
Wear Resistance | Good, relies on hardened martensite | Very high, superior to O1, due to high Cr-carbides |
Toughness | Sufficient/Good, generally better than D2 | Moderate/Fair, generally lower than O1 |
Dimensional Stability | Small changes, good | Minimum movement/distortion, good |
Machinability | Excellent (Rating 90/100) | Poor/Difficult (Rating 45/100) |
Hardenability | Medium | Deep |
Necking (Tensile) | Clear necking (19.7% area reduction) | Almost no necking (1.3% area reduction) |
Fracture Mode | Cup-cone | Flat surface |
Yield Strength (0.2%) | 829 MPa | 411 MPa |
Ultimate Tensile Strength (UTS) | 846 MPa | 758 MPa |
Cost | Low | Good balance of properties vs. cost |
Typical Applications | General purpose, small tools, punches, woodworking knives | Long-run dies, blanking, forming, piercing, forging, trimming |
O1 is a more machinable and tougher steel with generally higher tensile properties, but D2 offers significantly better wear resistance and dimensional stability after heat treatment due to its air-hardening nature and higher alloy content, especially chromium carbides.
5.4 O1 tool steel Vs. 1095
Feature | O1 Tool Steel | 1095 Steel (as W1 Tool Steel) |
Classification | Oil-hardening, cold-work tool steel (AISI O-series) | Water-hardening, plain high-carbon steel |
Primary Use | Versatile cold-work tooling | General-purpose cutting tools and parts |
Hardenability | High, deep hardening. Can through-harden in sections up to 2.5 inches (63.5 mm). | Low, shallow hardening. Hardens only to about 1/16 inch deep. |
Quenching Medium | Oil. Offers better stability and lower risk of distortion. | Water or Brine. Severe quench leads to high risk of cracking and warping. |
Dimensional Stability | Good. Exhibits minimal size changes after quenching. | Poor. Highly prone to distortion and cracking during heat treatment. |
Hardness (Typical) | 57-64 HRC. | Can achieve 62 HRC or higher, but only at the surface. |
Wear Resistance | Medium. Better than simple carbon steels due to alloying elements. | Lower. Develops a keen edge but has poor hot hardness. |
Toughness | Medium. Slightly higher toughness than other oil-hardening steels. | Good. The unhardened, ductile core provides good toughness. |
Machinability | Excellent. Rated at 90 (compared to W1 at 100). | Excellent. Rated at 100, serving as a baseline. |
Typical Applications | Blanking/forming dies, gauges, shear blades, machine ways, plastic molds. | Small dies, vise jaws, centering pins, and tools where a sharp edge is needed but high wear resistance is not critical. |
While both O1 tool steel and 1095 steel are high-carbon steels capable of achieving high hardness, O1 is a more alloyed tool steel designed for oil quenching, offering deeper hardening, better dimensional stability, and slightly better wear resistance. 1095, being a plain carbon steel, relies on water quenching for maximum hardness, which leads to shallow hardening and a higher risk of distortion and cracking; however, it offers excellent machinability.
6. Supply forms and dimensions
The O1 tool steel we supply is available in various forms, including round bars, sheet plates, slabs, flat bars, square bars, and blocks. The dimensions of the flat bar range from: width 20–600 mm × thickness 20–400 mm × length 1,000–5,500 mm. The dimensions of the round bar range from a diameter of 20–400 mm × a length of 1,000–5,500 mm. The block dimensions are obtained by cutting the flat bar.
For smaller sizes, such as round bars with a diameter less than 70 mm, we use the hot-rolled process. For sizes greater than 70 mm, we offer forged products.
UT testing: Sep 1921-84 D/d, E/e.
Surface Treatment: original black, peeled, machined/turned, polished, grounded, or milled surface finishes.
Inventory Status: We do not maintain a stock of O1 tool steel. We arrange production based on customer orders.
Delivery time: Electric Arc Furnace (EAF) materials are 30-45 days. ESR materials are approximately 60 days.
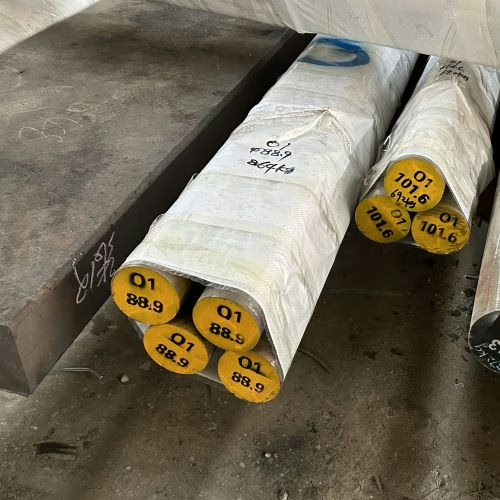
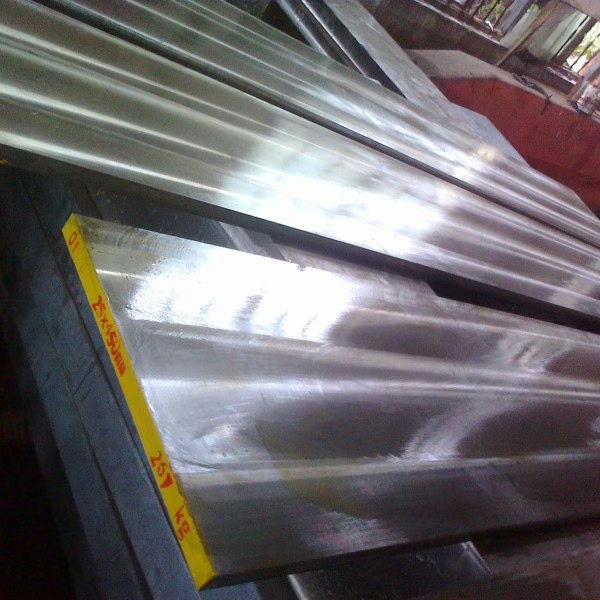
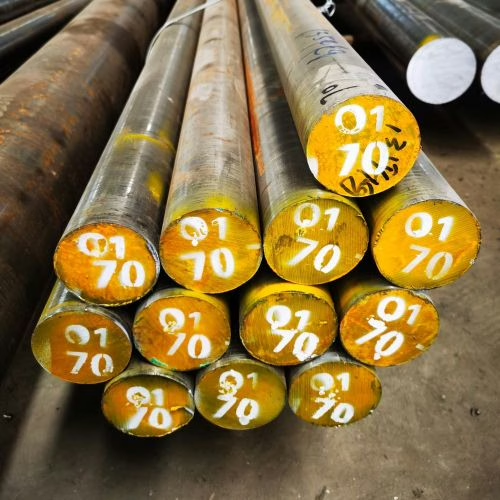
FAQs
1. What is O1 tool steel?
O1 tool steel is an oil-hardening, “non-shrinking” cold-work tool steel known for its high hardenability and dimensional stability during heat treatment. It is a general-purpose steel suitable for applications where alloy steels may not provide sufficient hardness, strength, and wear resistance.
2. What is O1 steel equivalent to?
German DIN grade: 1.2510
Japan JIS standard grade: SKS3 or SKS31
China GB standard grade: 9CrWMn
British BS standard grade: BO1
France NF standard grade: 90MnWCrV5
International Organization for Standardization (ISO) standard grade: 95MnWCr1
Sweden SS standard grade: 2140
Japan Daido (DAIDO) standard grade GOA
Korea KS standard grade STS3
Russian ГОСТ standard: 9ХВГ
3. What is the difference between 01 and A2 steel?
O1 steel is an oil-hardened tool steel with low heat treatment distortion and is suitable for precision tools; A2 steel is an air-cooled tool steel with higher wear resistance and good toughness.
4. Is O1 better than 1095?
If you are looking for the ultimate in hardness and wear resistance and can accept the risk of distortion, choose 1095 steel; if the balance of hardness and toughness is more important and the risk of distortion is lower, O1 steel is usually a better choice.
5. How to quench O1 steel?
O1 steel is quenched by quenching in oil.
6. Is O1 steel easy to machine?
O1 steel is easy to machine in the annealed condition.
7. What are the pros and cons of O1 steel?
O1 steel is a versatile and economical choice for cold-work applications requiring high hardness, good wear resistance, and reliable heat treatment with minimal distortion. However, its performance is limited at higher temperatures, and it requires careful atmospheric control during heat treatment to prevent decarburization.
8. Is O1 tool steel suitable for knife making, and does it rust easily?
Yes, O1 tool steel is a great material for knives. It is very easy to work with, reliable to heat-treat, and can be hardened to a Rockwell C 65 range. It holds a very fine edge for a long time, is easy to sharpen, and forms very fine carbides. While not “stainless” or “semi-stainless,” it has a decent amount of chromium, making it more corrosion resistant than plain carbon steels like 1095 or 52100. It will likely develop a patina, but with care, it won’t rust severely.
9. How machinable is O1 tool steel, and what are the considerations for drilling?
O1 tool steel has excellent machinability, rated at 85-90% compared to a 1% carbon steel. When drilling, it’s crucial to use a drill press, industrial-grade bits (like tungsten carbide drill bits for hardened O1), and adequate pressure to prevent work hardening. If the steel has accidentally air-hardened or work-hardened due to improper heating (e.g., heating raw stock to soften it) or light pressure during drilling, it will need to be re-annealed to become machinable again.
10. What are the key properties of O1 tool steel?
O1 tool steel can achieve a high hardness range of 58-65 HRC (Rockwell Hardness) after heat treatment. It offers good wear resistance due to its tungsten and higher chromium content, excellent machinability (85-90% of a 1% carbon steel), and good cutting edge retention. It is also considered “non-shrinking” due to its dimensional stability during heat treatment.
11. What are common applications for O1 tool steel?
O1 tool steel is commonly used for blanking and stamping dies (for cutting sheets up to 6mm thickness), threading tools, drills, broaches, gauges, measuring tools, plastic moulds, shear blades, and guide rails. It is also used for medium-run dies, intricate press tools, drawing punches, bushings, lathe centers, chuck jaws, master cavity sinking hobs, paper cutting machine knives, and various types of cutters and machine parts.
12. What are the physical properties of O1 tool steel?
Key physical properties of O1 tool steel include a density of approximately 7.83-7.85 g/cm³ (0.282-0.283 lb/in³), a melting point of around 1410-1421°C (2570-2590°F), and a Modulus of Elasticity of 210-214 GPa (31 x 10⁶ psi). Its thermal conductivity at 20°C is 33.4 W/(m*K).
13. How is O1 tool steel typically hardened?
The hardening process for O1 tool steel generally involves preheating slowly to 1200-1300°F (649-704°C), then raising the temperature to the austenitizing (high heat) range of 1475-1500°F (802-816°C). After soaking, it is oil-quenched to a temperature of no lower than 125-150°F (51-66°C) and then tempered immediately.
14. What is the recommended austenitizing (hardening) temperature for O1 tool steel?
The recommended austenitizing (hardening) temperature for O1 tool steel is between 1475-1500°F (802-816°C). For light sections, oil quenching from the lower end of this range (780-820°C) is suggested.
15. What is the recommended soak time during O1 tool steel hardening?
After reaching the hardening temperature, O1 tool steel should be soaked for 30 minutes for the first inch (25.4 mm) of thickness, plus 15 minutes for each additional inch. For knives or thin blades, a soak time of 5-10 minutes (or up to 20 minutes for optimal results) is often recommended after the blades become non-magnetic.
16. What type of quenching medium is used for O1 tool steel, and at what temperature?
O1 tool steel is an oil-hardening steel and should be quenched in warm oil, ideally at a temperature of 125-200°F (51-93°C), with some sources recommending 130°F or 149-204°C (300-400°F). It’s crucial to remove the part from the oil before it cools to ambient temperature.
17. How is O1 tool steel tempered, and what are the recommended temperatures and durations?
Tempering O1 tool steel should occur immediately after quenching. The typical tempering range is 350-400°F (177-204°C), though ranges from 100°C to 450°F are mentioned depending on desired hardness. The steel should be held at temperature for 1 hour per inch of thickness, with a minimum of 2 hours. Double tempering is sometimes preferred.
18. What is annealing, and when is it necessary for O1 tool steel?
Annealing is a heat treatment process that makes the steel soft and machinable. It is necessary after hot working (such as forging) and before rehardening. New O1 tool steel stock is typically supplied in the annealed condition.
19. How is O1 tool steel annealed?
To anneal O1 tool steel, heat slowly at a rate not exceeding 400°F (222°C) per hour to 1425-1450°F (774-816°C). Hold at this temperature for 1 hour per inch of maximum thickness (minimum 2 hours). Then, cool slowly in the furnace at a rate not exceeding 50°F (28°C) per hour to 900-1000°F (482-538°C), and continue cooling to ambient temperature in the furnace or air. The resulting hardness should be a maximum of 212-229 Brinell.
20. Is O1 tool steel prone to warping or cracking during heat treatment?
Yes, O1 tool steel is somewhat prone to quench cracking, especially if there are significant changes in section thickness or sharp internal corners. Warping issues, particularly with thin blades, are also common. Overheating or heating too quickly can cause cracks and large grain size.
Looking for Premium O1 Tool Steel?
At Aobo Steel, we leverage over 20 years of specialized forging experience to deliver top-tier O1 tool steel, precisely tailored to your application needs. Our expert team is dedicated to helping you find the optimal material solution.
Ready to enhance your project? Fill out the form below to connect with us for a personalized quote or expert consultation.
Explore Our Other Products
D2/1.2379/SKD11
D3/1.2080/SKD1
D6/1.2436/SKD2
A2/1.23663/SKD12
O1/1.2510/SKS3
O2/1.2842
S1/1.2550
S7/1.2355
DC53
H13/1.2344/SKD61
H11/1.2343/SKD6
H21/1.2581/SKD7
L6/1.2714/SKT4
M2/1.3343/SKH51
M35/1.3243/SKH55
M42/1.3247/SKH59
P20/1.2311
P20+Ni/1.2738
420/1.2083/2Cr13
422 stainless steel
52100 bearing steel
440C stainless steel
4140/42CrMo4/SCM440
4340/34CrNiMo6/1.6582
4130
5140/42Cr4/SCR440
SCM415