A2 tool steel is a deep-hardened, air-hardened tool steel. The deformation caused by air hardening is approximately one-quarter that of tungsten-based oil-hardened tool steel. Its wear resistance falls between that of chromium-type and high-carbon, high-chromium-type tool steels, but its toughness is superior. This makes it especially suitable for applications requiring good wear resistance, toughness, and dimensional stability. A2 steel is widely used in blanking dies, forming dies, rolling dies, punch dies, calendering dies, thread rolling dies, and specific cutting blades.
1. Applications
A2 tool steel is widely used for tooling operations performed at temperatures below 200°C (typically room temperature). It is an economical choice for general shop purposes. Its applications span situations demanding extreme hardness, friction resistance, durability, and strength, and it’s suitable where improved toughness and reasonable abrasion resistance are needed.
- Bending dies
- Blanking dies and punches (for long runs or thin/medium-thickness stock)
- Coining dies
- Cold forming tools
- Drawing dies
- Extrusion dies and punches for aluminum
- Forming dies
- Gages and precision measuring tools (due to dimensional stability)
- Knurls
- Mandrels
- Master hubs
- Molds
- Planer tools
- Shear knives and blades (cold shears for light and medium duty, trimming dies)
- Slitter knives
- Spindles
- Punches (even over wear-resisting D2)
[References: Totten, G. E., Xie, L., & Funatani, K. (Eds.). (2004). Handbook of Mechanical Alloy Design (p. 169). CRC Press.]
2. A2 Steel Composition
Element | Carbon (C) | Chromium (Cr) | Molybdenum (Mo) | Vanadium (V) | Manganese (Mn) | Silicon (Si) | Phosphorus (P) | Sulfur (S) |
Percentage (%) | 0.95 – 1.05 | 4.75 – 5.50 | 0.90 – 1.40 | 0.15 – 0.50 | 0.40 – 1.00 | 0.30 – 0.90 | ≤ 0.03 | ≤ 0.03 |
3. A2 steel equivalent
- DIN/ISO: 1.2363 (X100CrMoV5),
- JIS (Japan): SKD12
- China(GB/T 1299 standard): Cr5Mo1V
4. A2 Steel Properties
Basic Physical Properties and Mechanical Properties
Property |
Value |
---|---|
Density |
7.86 g/cm³ |
Melting Point |
1424°C |
Bulk modulus |
140 GPa |
Shear modulus |
78.0 GPa |
Poisson’s ratio |
0.27-0.30 |
Elastic modulus |
190-210 GPa |
Thermal expansion |
10.7 x 10⁻⁶/°C |
4.1 Hardness
The hardness after annealing is 235 HB to 269 BHN.
In the as-quenched condition, A2 can achieve a surface hardness of 60 HRC. As-quenched hardness is influenced by austenitizing temperature.
The hardness after tempering is 58–64 HRC. Tempering at 200°C (390°F) can achieve a hardness of 60 HRC.
4.2 Wear Resistance
The high carbon and chromium content give A2 excellent wear resistance. Compared to O1 steel, A2 steel has slightly better wear resistance. Compared to A6 steel, its wear resistance is improved by 20-25%. However, its wear resistance is lower than that of D2 steel or high-speed steel.
4.3 Toughness
A2 steel has moderate toughness, higher than oil-hardening die steels and D-series tool steel. Toughness and wear resistance are inversely proportional. The large amount of carbides in D-series tool steel increases wear resistance, but reduces toughness.
4.4 Dimensional Stability
A2 steel undergoes minimal deformation during hardening. The expansion is approximately 0.001 inches/inch (0.001 mm/mm).
4.5 Machinability
A2 steel is an easy-to-machine tool steel after appropriate annealing treatment. If the machinability of tool steel with a carbon content of 1% is set to 100, the machinability rating of A2 is 65.
4.6 Weldability
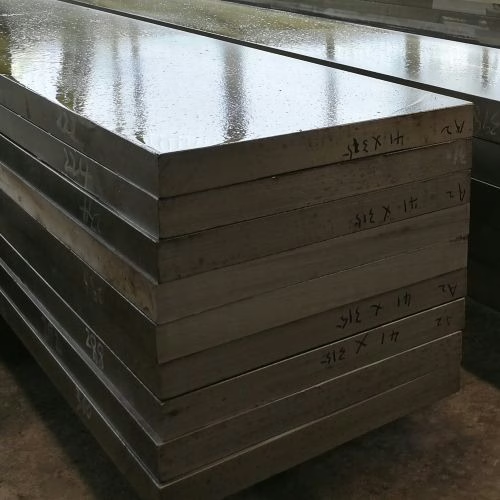
Interested in A2 tool steel?
Fill out the form below to get more technical support and the latest quotes for A2 tool steel!
5. Heat Treatment
Below, we outline the critical steps and considerations for a successful A2 tool steel heat treatment, based on industry best practices.
5.1 Initial Preparation
- Assessing Initial Condition: Before performing any heat treatment on A2 material, it is essential to ensure that the material surface is thoroughly degreased.
- Pre-Hardening Stress Relief (If Applicable): For A2 materials that have undergone extensive machining, we strongly recommend stress relief treatment, which minimizes deformation during heat treatment. Procedure for unhardened material: Heat the steel slowly and uniformly to 1200–1250°F (649–677°C). Hold at this temperature for approximately 2 hours per inch of the thickest section. Follow this with a slow cool, preferably within the furnace.
5.2 Protecting A2 Tool Steel During Heat Treatment
A2 tool steel is prone to decarburization when heated to high temperatures. To prevent decarburization and ensure the integrity of the heat treatment of A2 tool steel, we recommend securely wrapping the steel A2 with stainless steel foil and then placing it in a controlled neutral atmosphere furnace or a vacuum furnace. Sealing the material in stainless steel foil is a widely adopted and effective method.
5.3 Key Stages of A2 Tool Steel Heat Treatment
5.3.1 Preheating
The purpose of preheating A2 tool steel is to:
- Adjust the molecular structure of the material.
- Ensure that the temperature of the entire component is uniform, reducing thermal shock.
- Eliminate internal stress before reaching a higher austenitizing temperature.
The preheating temperature for A2 steel is 1200°F (650°C). Hold for 10-15 minutes to ensure that the temperature of the material is consistent with the temperature inside the furnace before proceeding to the next step. This can be determined by observing whether the color of the material and the furnace wall remains consistent.
5.3.2 Austenitizing (Hardening):
During this process, the alloy carbides within the material dissolve into the matrix, which determines the final quenching properties of A2 steel.
The standard quenching temperature is approximately 1775°F (968°C), with some processes ranging from 1775°F to 1825°F (970-995°C). The soaking time is 1 hour per inch (25mm) of the component’s thickest cross-section.
The soaking time should NOT be too long, as excessive soaking time can have a negative impact on the material’s microstructure.
5.3.3 Quenching:
Air quenching significantly reduces thermal shock and internal stress and is the mildest common quenching method. Use foil to seal the parts until all visible red-hot phenomena have completely dissipated.
However, air quenching of A2 has limitations. If the cross-sectional dimensions exceed approximately 5 inches (127 mm), air quenching may NOT achieve complete hardening.
5.4 Tempering
When A2 tool steel material is air cooled to 125-150°F (52-65°C), tempering should begin immediately. Delayed tempering may increase the risk of cracking or shorten the life of the tool. If straightening is required, it can be performed when the material temperature is above 400°F (205°C), at which point the martensitic transformation has not yet been completed.
The purpose of tempering is:
- To eliminate internal stresses in the material.
- To increase toughness and reduce brittleness.
- To minimize residual austenite and transform residual austenite into a more stable microstructure.
5.4.1 Single Temper
Heat the material to 400°F (205°C), then soak at that temperature for 2 hours per inch (25 mm) of cross-section, and finally allow to cool naturally.
The first tempering helps to stabilize the newly formed martensite and transform the residual austenite.
5.4.2 Multi-Tempering (Double/Triple Tempering)
We strongly recommend a double-tempering process, or even a triple-tempering process.
The first tempering temperature for the double-tempering process is 400°F (205°C). The second tempering temperature is 375°F (190°C). Ensure that the material is cooled to room temperature between each tempering cycle.
Multiple tempering cycles can significantly refine the grain structure, enhance wear resistance, and provide excellent stress relief. This is particularly beneficial for components with complex geometries or sharp angles.
The tempering temperature directly affects the final hardness of A2 tool steel.
5.5 Post-Hardening Stress Relief
After completing the above heat treatment steps, additional stress relief treatment may be required for A2 material, especially when the material has undergone grinding, welding, or electrical discharge machining (EDM).
This method involves tempering the material at a temperature 25-50°F (14-28°C) lower than the final tempering temperature used in the main heat treatment.
5.6 Forging A2 steel
Slowly preheat to 870°C (1600°F), then heat to the forging temperature of 1010°C to 1095°C (1850°F to 2000°F). Do NOT forge below 900°C (1650°F).
After forging, cool slowly in insulating material to at least 205°C (400°F). We do NOT suggest normalizing after forging. Instead, A2 tool steel should be annealed before subsequent machining or quenching operations.
6. Compare A2 Steel With Other Steels
6.1 A2 steel vs. 1095 steel
6.1.1 Hardenability and Heat Treatment
A2 tool steel’s primary advantage is its air-hardening capability and minimal distortion during heat treatment, making it highly reliable for intricate tooling. The hardenability of 1095 carbon steel is more dependent on section size and cooling severity, making it challenging to achieve consistent through-hardness in larger sections. Both are sensitive to heat treatment, but A2 is engineered for greater predictability in hardening.
6.1.2 Mechanical Properties
Compared to other tool steels and carbon steels, including 1095 carbon steel, A2 has better toughness.
In terms of wear resistance, A2 steel is also superior to 1095 steel, especially under long-term working conditions. 1095 steel generally has average wear resistance when untreated or in its simple hardened state.
6.1.3 Cost
A2 steel contains expensive alloys, making it more costly than 1095 steel, which does not contain these expensive alloys.
6.1.4 Applications
A2 is preferred for demanding cold-work tooling applications requiring high wear resistance, good toughness, and minimal distortion, such as long-run dies and molds. 1095 is used when high hardness is the primary requirement, such as for springs, gears, and simpler cutting tools, and is often chosen for its cost-effectiveness in certain wear applications. Based on our export experience, A2 steel is commonly used in markets outside China, especially in the United States.
In general, A2 steel is a more advanced and specialized tool steel containing expensive alloys. It exhibits excellent dimensional stability, comprehensive wear resistance, and toughness, making it suitable for high-precision and high-volume mold manufacturing. While 1095 steel is a high-hardness carbon steel with a simple composition, its performance is more dependent on the base carbon content and quenching conditions.
[References: Bringas, J. E. (Ed.). (2004). Handbook of Comparative World Steel Standards (3rd ed). ASTM International.]
6.2 A2 Steel vs. D2 Steel
Here’s a summary comparing the two steels:
Feature | A2 Steel | D2 Steel |
AISI Classification | Air-hardening, medium-alloy, cold-work tool steel | High-carbon, high-chromium, cold-work tool steel |
Hardening Method | Air-hardening (principal air-hardening tool steel) | Air-hardening (most D-type steels) |
Wear Resistance | Very good; more abrasion resistance than S-series, but less than D-series | Excellent; superior to A2 (30-40% better) |
Toughness | Higher than oil-hardening steels and D2 | lower than A2; low impact strength |
Machinability | Relatively easy machining | Difficult to work and grind |
Dimensional Stability | Minimal movement/low distortion | Minimal movement/low distortion |
Typical Hardness | 58-60 HRC | 60-62 HRC |
Carbide Content | Very small formation of carbides | Large amount of carbides (~16% by volume), primarily Cr-rich M7C3 |
Retained Austenite | Can have high amounts; high-temperature tempering helps | Prone to retaining significant amounts (up to 20%); often requires cold treatment/double tempering |
Overall, if you need higher toughness and easier machining for moderately demanding applications, A2 steel is the choice. However, if your priority is maximum wear resistance and dimensional stability for very long production runs, and you can manage the increased difficulty in machining and grinding, then D2 steel is the option.
6.3 O1 Vs. A2 steel
A direct comparison of O1 and A2 tool steels:
Feature | O1 Tool Steel | A2 Tool Steel |
Classification & Hardening | An oil-hardening tool steel, specifically a manganese oil-hardening type. | An air-hardening die steel. |
Heat Treatment | Hardened by heating to an austenization temperature of 802-816°C (1475-1500°F) and then quenching in oil. | Hardened by air cooling from temperatures around 955°C (1750°F). It can be heated in a preheated furnace, which is faster than O1 tool steel. |
Hardness (HRC) | Can easily harden to 62-63 HRC. The typical working range is 57-62 HRC. | The normal working hardness is 58–60 HRC, and it can be tempered to 59-61 HRC. |
Toughness | Has slightly higher toughness than other oil-hardening steels and can offer a great combination of high hardness and toughness. | Possesses higher toughness than oil-hardening die steels and offers good toughness in general. |
Wear Resistance | Good wear resistance | Very good wear resistance compared to O1. |
Machinability | Excellent machinability | Particularly poor. |
Dimensional Stability | Is subject to cracking and distortion during oil quenching. | Minimum movement in hardening and low distortion. Offers safety and dimensional stability. |
Applications | Blanking, coining, and forming dies, as well as punches, shear blades, and woodworking knives. | Bending dies, blanking dies, and punches. It is an excellent choice for tools where O1 might have hardenability issues and for designs prone to cracking. |
In summary, O1 steel offers good machinability and an excellent balance of hardness and toughness at a low cost, but it is more prone to distortion and cracking during oil quenching. A2 steel, while less machinable, provides superior dimensional stability and wear resistance due to its air-hardening characteristics, making it suitable for applications requiring higher precision and longer tool life, even at a slightly higher cost.
7. Supply forms and dimensions
The A2 tool steel we supply is available in three shapes: flat bar, block, and round bar.
The dimensions of the flat bar range from: width 20–600 mm × thickness 20–400 mm × length 1,000–5,500 mm. The dimensions of the round bar range from a diameter of 20–400 mm × a length of 1,000–5,500 mm. The block dimensions are obtained by cutting the flat bar.
For smaller sizes, such as round bars with a diameter less than 70 mm, we use the hot-rolled process. For sizes greater than 70 mm, we offer forged products.
UT testing: Sep 1921-84 D/d, E/e.
Surface Treatment: turning, milling, black, peeling.
Inventory Status: We do not maintain a stock of A2 steel. We arrange production based on customer orders.
Delivery time: Electric Arc Furnace (EAF) materials are 30-45 days.
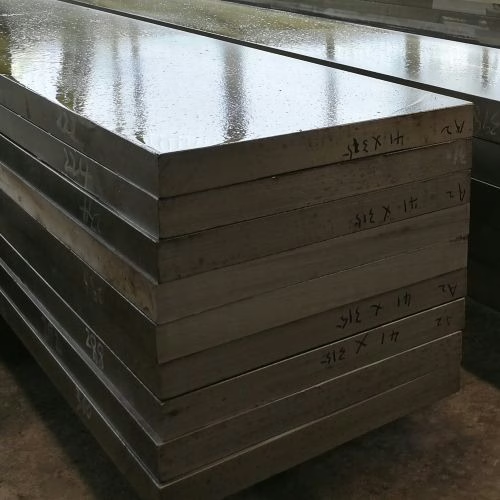
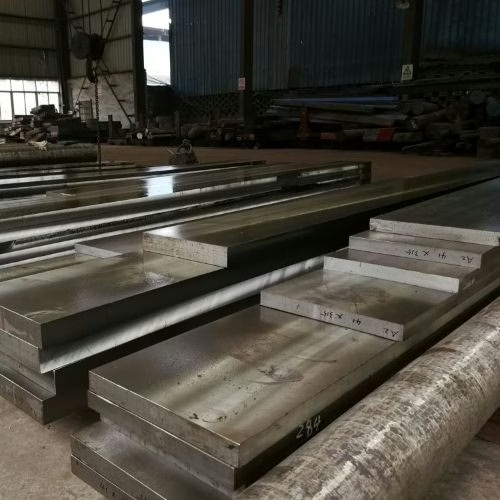
FAQs
1. What is A2 steel?
A2 steel is an air-cooled, medium-alloyed cold-worked tool steel known for its high wear resistance, good toughness, and small heat treatment deformation. It is commonly used in the manufacture of a variety of cold-worked molds.
2. Is A2 a good knife steel?
Yes, A2 tool steel has been used in knives for many years and continues to be used today. It is favored by knifemakers for its good toughness, wear resistance, and edge retention. It also offers great ease in grinding and polishing for the knifemaker and ease in sharpening for the end user. It can be heat-treated to various hardness levels (e.g., 64 Rc for excellent wear resistance, or 60 Rc for good toughness).
3. Is A2 steel better than A4?
A4 steel generally exhibits slightly better wear resistance than A2 steel and can be hardened at lower austenitizing temperatures. However, both exhibit good toughness and low heat-treat distortion.
4. Is A2 better than D2 steel?
A2 is intermediate in wear resistance between O1 and D2. D2 has a higher carbon and chromium content, providing higher wear resistance but generally lower toughness due to large chromium carbides. A2 is typically used in applications where D2 has insufficient toughness. A2 is also more easily machined and grindable than D2, and like D2, it is very resistant to distortion during heat treating.
5. Does A2 steel rust easily??
A2 tool steel has slightly better stain resistance compared to simple carbon steels, but it is not as stain-resistant as stainless steel. While its high chromium content (4.75%-5.50%) contributes some corrosion protection in areas with moisture or mild corrosive chemicals, it is not considered a true stainless steel because a significant portion of its chromium is tied up in carbides, reducing the amount available for corrosion resistance.
6. Is A2 steel the same as 304?
In the ISO 3506 standard, “A2” refers to 304 stainless steel. This “A2” is not the A2 tool steel under the AISI standard on this page.
7. Can A2 steel be hardened?
Yes, it can indeed be hardened, and it is known explicitly as an air-hardening tool steel.
8. Can A2 be oil quenched?
Yes, A2 steel can be oil quenched. Specifically, for sections of A2 steel greater than 125 mm (5 inches) square, it is recommended to oil quench them from the austenitizing temperature down to 540 °C (1000 °F). After this oil quench, the material should then be air quenched to 65 °C (150 °F) before tempering.
9. What are the key characteristics of A2 tool steel?
Key characteristics of A2 tool steel include good machinability, high compressive strength, high dimensional stability after hardening and tempering, good hardenability, very good non-deforming properties, deep hardening, and good wear resistance. It is also moderately tough and grindable.
10. Is A2 tool steel air-hardening? Why is this important?
Yes, A2 tool steel is an air-hardening steel. This characteristic allows it to achieve full hardness by simply cooling in air after being heated to hardening temperatures, which helps to minimize distortion and cracking that can occur with water or oil quenching. This makes it easier to maintain the required shape of tools and components after heat treatment.
11. What is the typical hardness range for A2 tool steel?
A2 tool steel is heat treatable and typically offers a hardness in the range of 57-62 HRC. As air-hardened, it averages 63-65 HRC, but tempering can adjust this, for example, to 60-62 HRC at 205°C (400°F) or 56-58 HRC at 540°C (1000°F).
12. Does A2 tool steel have good wear resistance?
Yes, A2 tool steel has good wear resistance. Its wear resistance is attributed to its alloying elements, such as chromium and molybdenum, which contribute to the formation of stable carbides, enhancing its resistance to abrasive wear.
13. What is the toughness of A2 tool steel?
A2 tool steel has good toughness. It compares favorably with higher-wear-resistance steels like D2 tool steel. It is often used in applications where D2 might have insufficient toughness. This property allows it to withstand stress and impact without cracking, making it suitable for tools operated under heavy loads.
14. What is the machinability of A2 tool steel?
A2 tool steel has medium machinability. Its machinability is rated at about 65% that of carbon tool steel, which is considered a baseline at 100%. It can be machined using conventional methods, especially before hardening, and machining rates can increase when the alloy is in a soft state.
15. How do you heat treat A2 tool steel?
A2 tool steel is heat-treated by heating it slowly to 788°C (1450°F), then increasing the temperature to 954°C (1750°F). It is held at this austenitizing temperature for 30 to 45 minutes to achieve a complete carbide solution in the matrix. After soaking, it is removed from the furnace and air-cooled to room temperature to harden. A tempering process typically follows this.
16. How do you temper A2 tool steel?
A2 tool steels are tempered at temperatures ranging from 177°C (350°F) for Rockwell C 62 hardness to 538°C (1000°F) for Rockwell C 56 hardness. Tempering involves heating uniformly and thoroughly to the desired temperature and holding for approximately 25 minutes per cm of thickness, or a minimum of 2 hours per inch of the most excellent cross-section. Double tempering is recommended after intermediate cooling to room temperature to enhance toughness and relieve residual stresses.
17. Can A2 tool steel be annealed?
Yes, A2 tool steels can be annealed. They are annealed at 857°C (1575°F) and then cooled slowly in the furnace at a rate of 4°C (40°F) per hour or less. A2 tool steels are typically cold worked in the annealed condition. It should always be annealed after forging.
18. Can A2 tool steel be nitrided?
Yes, A2 tool steels can be nitrided. Nitriding in ammonia gas at 525°C (975°F) for 20-60 hours can give the surface a hardness of approximately 1000 HV1 and a case depth of 0.2-0.4mm. Nitriding provides a hard, diffused surface layer resistant to wear, erosion, and corrosion. Nitrocarburizing is also an option.
Looking for Premium A2 Tool Steel?
Get a Fast, Competitive Quote from the Experts at Aobo Steel.
With over 20 years of industry experience, we deliver top-grade A2 tool steel tailored to your exact specifications. Ensure optimal performance and longevity for your critical applications.
Ready for Your A2 Steel Solution?
Simply fill out the form below to connect with our specialists. We'll respond promptly to discuss your requirements!
Explore Our Other Products
D2/1.2379/SKD11
D3/1.2080/SKD1
D6/1.2436/SKD2
A2/1.23663/SKD12
O1/1.2510/SKS3
O2/1.2842
S1/1.2550
S7/1.2355
DC53
H13/1.2344/SKD61
H11/1.2343/SKD6
H21/1.2581/SKD7
L6/1.2714/SKT4
M2/1.3343/SKH51
M35/1.3243/SKH55
M42/1.3247/SKH59
P20/1.2311
P20+Ni/1.2738
420/1.2083/2Cr13
422 stainless steel
52100 bearing steel
440C stainless steel
4140/42CrMo4/SCM440
4340/34CrNiMo6/1.6582
4130
5140/42Cr4/SCR440
SCM415