S7 tool steel is a type of Shock-Resisting Tool Steel, classified within the “S” series by the American Iron and Steel Institute (AISI). These steels are specifically designed for applications where repetitive impact stresses are encountered.
1. S7 Tool Steel Applications
- Punches
- Blanking Dies
- Cold Forming Dies
- Coining Dies
- Mandrels
- Structural Component Parts
- Trimming Dies
2. S7 Steel Composition
Carbon | Manganese | Silicon | Chromium | Molybdenum | Vanadium |
0.45 – 0.55 | 0.20 – 0.90 | 0.20 – 1.00 | 3.00 – 3.50 | 1.30 – 1.80 | 0.20 – 0.35 |
[Reference: Sinha, A. K. (2003). Physical Metallurgy Handbook (p. 62). McGraw-Hill.]
3. Properties
3.1 Physical Properties
Density | 7.80−7.83 g/cm3 |
Specific Gravity | 7.83 |
Modulus of Elasticity | 205−207 GPa |
Thermal Conductivity | 28.5 W/(m⋅K) (at 95∘C) |
Thermal Expansion (Linear) | |
20−100∘C | 12.5 μm/(m⋅K) |
20−250∘C | 13.3 μm/(m⋅K) |
20−500∘C | 14.27 μm/(m⋅K) |
Specific Heat Capacity | ∼0.46 J/(g⋅K) |
Electrical Resistivity | ∼0.75 μΩ⋅m |
Critical Temperature (Ac1) | 793∘C |
Critical Temperature (Ac3) | 838∘C |
Transformation Temperature | 785−800∘C |
3.2 Mechanical Properties
Tensile Strength | ∼1517−2151 MPa |
Yield Strength | ∼1310−1999 MPa |
Hardness (Annealed) | Max 223−250 HBW |
Hardness (Heat Treated) | Up to 60−61 HRC |
Hardness (Tempering Range) | 45−57 HRC (depending on temp) |
Elongation at Break | ∼7−15% |
Poisson’s Ratio | 0.27−0.30 |
Modulus of Elasticity | 207 GPa |
3.3 Other Properties
- Shock Resistance: Very high, a primary and defining characteristic of S7.
- Wear Resistance: Good, though generally lower than high-carbon, high-chromium cold-worked steels like O6 or D2 tool steel.
- Dimensional Stability: Good stability throughout the correct heat-treating process. Dimensional growth of +0.001 inches per inch (0.001 mm per mm) when S7 is air quenched from the correct hardening temperature.
- Air Hardening Benefit: The air-hardening capability of S7 provides a significant margin of safety during the hardening process, reducing the risk of distortion and cracking compared to liquid-quenching steels.
- Elevated Temperature Performance: S7 exhibits good resistance to softening at moderately elevated temperatures, making it suitable for medium-temperature hot work applications.
- Surface Hardening: Through surface treatment processes such as carbonitriding or nitriding, the surface hardness of S7 tool steel can be further improved to around 64 HRC. However, such surface treatments can affect the S7 steel’s inherent shock resistance and should be considered carefully based on application requirements.
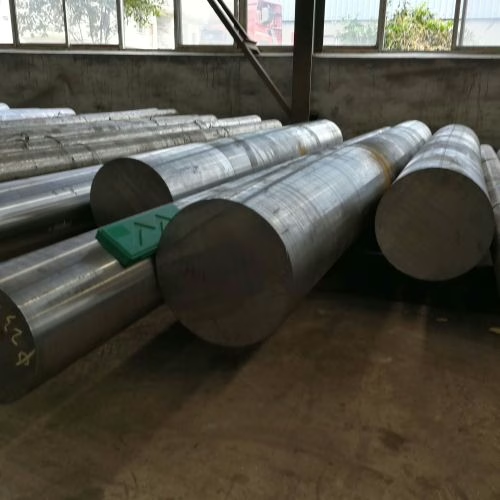
Are you looking for S7 tool steel?
Please fill out the following form to contact us today!
4. Heat treatment
4.1 Preheating
The preheating temperature for S7 steel is 1200°F (650°C), with a soaking time of 10 to 15 minutes.
Don’t soak for too long, as prolonged soaking will destroy the molecular structure and have an adverse effect on subsequent heat treatment.
4.2 Austenitizing (Hardening)
After preheating, set the furnace temperature to the austenitizing temperature, which is 1725°F (940°C). Begin soaking once the workpiece temperature has fully reached the austenitizing temperature.
The soak time depends on the part’s cross-section. For parts thicker than 1″ (25mm), the soak time should be 1 hour per inch (25mm) of the smallest cross-section. For smaller parts, a rule of thumb applies:
- 1/8″ (3.175mm) thick: 30 minutes
- 1/4″ (6.350mm) thick: 40 minutes
- 1/2″ (12.70mm) thick: 45-50 minutes
- 3/4″ (19.05mm) thick: 50-55 minutes
4.3 Quenching
S7 is an air-hardening tool steel. Air cooling is the slowest quenching method, but it offers the best security by reducing thermal shock and internal stress in hardened metals.
However, air-hardening steels have limitations on their ability to attain full hardness beyond certain cross-section sizes. For S7, if the cross-section size exceeds 2 1/2″ (63mm), full hardness may not be achieved when air cooled. Larger sections may require oil quenching to achieve the desired hardness, although this can compromise the stability of the heat treatment.
4.4 Tempering
Tempering enhances the toughness of steel and relieves its high stress state, thereby preventing cracking. S7 tool steel must be tempered immediately when the part temperature drops to 125 to 150°F (52 to 65°C).
The first tempering is typically performed at 450°F (230°C). If a second tempering is required, the temperature should be set to 425°F (220°C), which is 25℃ lower than the first tempering temperature. The hardness after a single tempering is 58 HRC. Each tempering cycle should last 2 hours per inch (25 mm) of cross-section.
4.5 Post-Treatment Considerations
If hardened S7 components undergo subsequent finishing operations such as grinding, welding, or Electrical Discharge Machining (EDM), a stress-relief temper is strongly advised. This should be performed at a temperature 25-50°F (14-28°C) below the temperature of the last effective tempering cycle used, to mitigate risks of cracking or dimensional instability induced by these processes.
4.6 Forging S7 Tool Steel
Slowly preheat S7 to 815°C (1500°F). The forging temperature is 1040-1150°C (1900-2100°F). For larger sections or when performing heavy and rapid reductions, the higher end of this temperature range is preferred, while smaller sections and lighter reductions can use the lower end. Never forge S7 below 870°C (1600°F).
S7 is an air-hardening steel and must be cooled slowly from the forging temperature to prevent cracking and ensure the steel remains in a semi-soft state. Cooling methods include furnace cooling or burying the material in an insulating medium such as lime, mica, or diatomaceous earth.
S7 must be annealed after forging. The annealing temperature involves heating to 843°C (1550°F) and holding for 1.5 hours per inch (3.5 minutes per mm) of thickness. When properly annealed, S7 has a machinability rating of 70% compared to a 1% carbon steel rated at 100%.
5. S7 tool steel equivalent grades
- UNS (Unified Numbering System): T41907
- DIN (German Standard): 1.2355 or 50CrMoV13-15
- JIS (Japanese Industrial Standards): SKS93
- Chinese Equivalent: 5Cr3Mn1SiMo1V
6. Compare S7 steel with 4140 steel
S7 tool steel excels in applications requiring high toughness and shock resistance, particularly in tooling for cold or medium-hot work, and benefits from air-hardening for dimensional stability. 4140 steel, a versatile alloy steel, is a strong choice for structural components and machine parts that require good strength, hardenability, and toughness. It often benefits from heat treatments such as oil quenching or nitriding for specific property enhancements.
7. Supply forms and dimensions
The S7 tool steel we supply is available in various shapes, including round bars, sheet plates, slabs, flat bars, square bars, and blocks. The dimensions of the flat bar range from: width 20–600 mm × thickness 20–400 mm × length 1,000–5,500 mm. The dimensions of the round bar range from a diameter of 20–400 mm × a length of 1,000–5,500 mm. The block dimensions are obtained by cutting the flat bar.
For smaller sizes, such as round bars with a diameter less than 70 mm, we use the hot-rolled process. For sizes greater than 70 mm, we offer forged products.
UT testing: Sep 1921-84 D/d, E/e.
Surface Treatment: original black, peeled, machined/turned, polished, grounded, or milled surface finishes.
Inventory Status: We do not maintain a stock of S7 steel. We arrange production based on customer orders.
Delivery time: Electric Arc Furnace (EAF) materials are 30-45 days. ESR materials are approximately 60 days.
FAQ
1. What is S7 tool steel?
S7 tool steel is a shock-resisting tool steel, classified as a group S steel under the ASTM A681 standard. It is primarily an air-hardening steel but can also be oil-hardened. S7 is known for its exceptional impact properties and the highest hardenability among shock-resisting tool steels. It combines high impact strength, good dimensional stability, and machinability with excellent resistance to shock.
2. What are the defining characteristics and key properties of S7 tool steel?
- High shock resistance and toughness: It exhibits excellent resistance to high impact and shock loads.
- Good softening resistance at high temperatures: This allows for hot work capabilities, typically up to 1000°F (538°C).
- High hardenability: It has the highest hardenability among shock-resisting grades.
- Good dimensional stability: It maintains its shape and size even under high stress and pressure, which is crucial for precision applications.
- Ease of machining and heat-treatment: It is considered safe and stable in heat treatment due to its air-hardening properties.
3. What are the common applications for S7 tool steel?
- Cold work tooling: Blanking dies, forming dies, cutting tools, and shear blades.
- Hot work tooling: Forging dies, extrusion dies, hot header dies, and die-casting dies.
- Shock applications: Bull riveters, concrete breakers (moll points), riveting dies, chisels, punches, and swaging dies.
- Molding: Plastic mold dies, machined cavities for plastic molding dies, and master hobs.
- Other uses include dowels, drills, drill plates, hubs, and engraving dies. It is also employed for critical components in the aerospace industry.
4. Are there international equivalents for AISI S7 tool steel?
German: W-nr 1.2357, or 1.2355 / 50CrMoV13-15 (DIN EN ISO 4957).
5. What is the typical hardness range for S7 tool steel?
The hardness of S7 tool steel can vary depending on the heat treatment and tempering temperature. Typically, its hardness ranges between 54-62 HRC. For specific tempering temperatures, Rockwell C hardness can be:
- As air quenched: 59-61 HRC
- Tempered at 149°C (300°F): 57-59 HRC
- Tempered at 204°C (400°F): 55-57 HRC
- Tempered at 449°C (840°F): 53 HRC
- Tempered at 649°C (1200°F): 41 HRC, 37-40 HRC When annealed, S7 tool steel typically has a hardness of Brinell 197 max or 187-220 BHN, with a maximum of 223 HBW.
6. What is the impact strength of S7 tool steel?
S7 tool steel is characterized by its very high impact toughness and exceptional impact properties, making it a “shock-resisting” grade. Measured Charpy impact (V-notch; air cooled from 941°C) values include:
- 16.9 J when tempered at 200°C.
- 13.6 J when tempered at 425°C.
- 16.3 J when tempered at 649°C.
7. Is S7 tool steel corrosion resistant?
S7 tool steel is susceptible to corrosion and can easily rust and corrode. It should be kept away from moisture and humidity, and rust inhibitors or corrosion-resistant materials like plastic or wax paper are recommended for storage.
8. What is the density and modulus of elasticity of S7 tool steel?
The density of S7 tool steel is 7.83 g/cm³ (or 0.283 lb/in³). The modulus of elasticity is 207 GPa (or 30 x 10^6 psi).
9. Why is slow heating important when working with S7 tool steel?
Slow heating, at a rate not exceeding 400°F (222°C) per hour, is crucial for S7 tool steel, especially for complex or large tools, to ensure uniform temperature distribution throughout the material and prevent cracking. Rapid heating can cause significant stress in the metal due to uneven expansion, leading to cracks, particularly if the core of the metal is not at the same temperature as the outside.
10. Can S7 tool steel be welded?
S7 tool steel demonstrates moderate weldability. However, we don’t recommend welding because the process can leave a weak heat-affected zone, introduce defects, and make the weld more ductile (less hard) than the tool steel. If welding is necessary, it should be carried out by an experienced die repair welder. Preheating and post-welding treatments (like re-tempering) can avoid cracking and maintain material integrity. Specialized welding consumables are also very expensive.
11. Is S7 tool steel easy to machine?
S7 tool steel is considered machinable, but it is comparatively more difficult to machine than lower alloy steels. It is rated at 95 for machinability (compared to 100 for a 1.00% carbon tool steel) when annealed to Brinell 197 max.
12. How does S7 tool steel compare to other materials for critical components like firing pins or bolts?
For applications like AR9 firing pins, while many are made from S7 tool steel, some experts suggest that heat-treated tool steels like S7 should be avoided because of embrittlement.
- Vs. 17-4 Stainless Steel: 17-4 stainless steel is considered better for firing pins due to its high ductility, especially when heat-treated to H900 condition, which provides comparable or superior Charpy impact strength to Grade 5 Titanium.
- Vs. Titanium: Titanium (e.g., Grade 5 Ti-6Al-4V) has a high strength-to-weight ratio but is not as hard as S7 and may not deliver the same energy as a heavier pin due to its low mass. It may also be prone to galling or friction wear in cam applications.
- Vs. 9310 Steel (for bolts): S7 tool steel, if hardened properly, can have superior tensile, thermal shock, and bending strength compared to 9310 steel. However, their shear strength is roughly equal. 9310 is often used for transmission gears in F1 and aerospace, suggesting a different set of optimal properties for those applications.
- The primary cause of firing pin breakage in AR9s is often a mis-dimensioned or mis-made bolt that allows the pin to bottom out, causing side stress, rather than the steel type itself.
13. What are the general limitations of S7 tool steel?
- Subject to decarburization: Like other high-carbon steels, S7 tool steel can lose carbon from its surface during thermal processing, requiring precautions.
- Unsuitable for nitriding: Due to its low tempering temperatures, S7 tool steel is typically not suitable for nitriding or similar surface treatments.
- More difficult to machine: Its high alloy content makes it comparatively harder to machine than lower alloy steels.
- Less wear and tear resistant (comparatively): While it has good wear resistance, it is considered less resistant to general wear and tear compared to some other tool steels.
Unlock Peak Performance with S7 Tool Steel
Aobo Steel is your premier source for high-quality S7 tool steel. With over 20 years of forging expertise, we deliver unmatched durability and precision for your most critical applications. Our specialists are ready to provide tailored advice and competitive quotes.
Ready to enhance your project? Complete the form below to connect with our experts & receive your custom quote!
Explore Our Other Products
D2/1.2379/SKD11
D3/1.2080/SKD1
D6/1.2436/SKD2
A2/1.23663/SKD12
O1/1.2510/SKS3
O2/1.2842
S1/1.2550
S7/1.2355
DC53
H13/1.2344/SKD61
H11/1.2343/SKD6
H21/1.2581/SKD7
L6/1.2714/SKT4
M2/1.3343/SKH51
M35/1.3243/SKH55
M42/1.3247/SKH59
P20/1.2311
P20+Ni/1.2738
420/1.2083/2Cr13
422 stainless steel
52100 bearing steel
440C stainless steel
4140/42CrMo4/SCM440
4340/34CrNiMo6/1.6582
4130
5140/42Cr4/SCR440
SCM415