M2 tool steel is a highly versatile, general-purpose high-speed tool steel that provides a good balance of toughness, wear resistance, hot hardness, and heat treatability, making it suitable for a broad spectrum of cutting, forming, and structural applications.
1. Applications
- General-Purpose Cutting Tools
- Single-Point Cutting Tools: They can machine a wide range of materials, including wrought steel, cast steel, cast iron, brass, bronze, copper, and aluminum.
- Drills: M2 material is the universal choice for general-purpose drills.
- Milling Cutters: More than 70% of free-machining milling cutters are made of M2 material.
- Saws: M2 high-speed tool steel is the general-purpose saw material.
- Reamers
- Taps and Dies:
- Broaches:
- Cold Work Applications
- 10. Other Applications: M2 hss is used as a core and ejector pin material in plastic injection molding tools. Also used for structural applications, such as machine elements, cams, shafts, spindles, gears, and sprockets.
[Reference: Roberts, G., Krauss, G., & Kennedy, R. (1998). Tool Steels: 5th Edition. ASM International.]
2. M2 steel composition
Element | Carbon (C) | Chromium (Cr) | Molybdenum (Mo) | Tungsten (W) | Vanadium (V) | Silicon (Si) | Manganese (Mn) | Phosphorus (P) | Sulfur (S) |
Composition (%) | 0.78–0.88 | 3.75–4.50 | 4.50–5.50 | 5.50–6.75 | 1.75–2.20 | 0.20–0.45 | 0.15–0.40 | ≤0.03 | ≤0.03 |
[Reference: Bringas, J. E. (Ed.). (2004). Handbook of Comparative World Steel Standards (3rd ed). ASTM International.]
3. M2 Tool Steel Properties
M2 tool steel stands as a cornerstone in the high-speed steel (HSS) family, and for many good reasons, it’s a popular choice for a wide array of demanding applications. This molybdenum-based HSS, part of the “M” series, delivers a reliable combination of hardness, wear resistance, and toughness, making it a versatile workhorse.
3.1 Hardness
The M2 tool steel hardness is very high, and through hardening and tempering, its working hardness ranges from 60 to 65 HRC.
3.2 Wear Resistance
Extremely high wear resistance.
3.3 Hot Hardness (Tempering Resistance)
Good thermal hardness, meaning that it can maintain its hardness and strength even under high-temperature working conditions. While some specialized HSS grades might offer higher hot hardness, M2 material performs reliably in typical high-temperature tooling scenarios.
3.4 Toughness
M2 steel has such high hardness and wear resistance while maintaining good toughness. Tool steel M2 produced by powder metallurgy (P/M) processes has higher toughness.
3.5 Physical Properties
Property | Value |
Density | 0.294 lb/in³ (8138 kg/m³) |
Specific Gravity | 8.14 |
Modulus of Elasticity | 30 x 10⁶ psi (207 GPa) |
Machinability | 50–60% of a 1% carbon steel |
3.6 Mechanical properties
Property | Value |
Hardness (Rockwell C) | 60–65 |
Ultimate Tensile Strength | 760–2,150 MPa (110,000–310,000 psi) |
Yield Strength | 3,250 MPa (471,000 psi) |
Compressive Yield Strength (tempered at 300°F) | 3,250 MPa (471,000 psi) |
Modulus of Elasticity (Young’s Modulus) | 200–207 GPa (29–30 x 10⁶ psi) |
Shear Modulus | 77 GPa (11 x 10⁶ psi) |
Poisson’s Ratio | 0.29 |
Impact Toughness | 67 J/cm² |
Abrasion Loss (as-hardened; ASTM G65) | 25.8 mm³ |
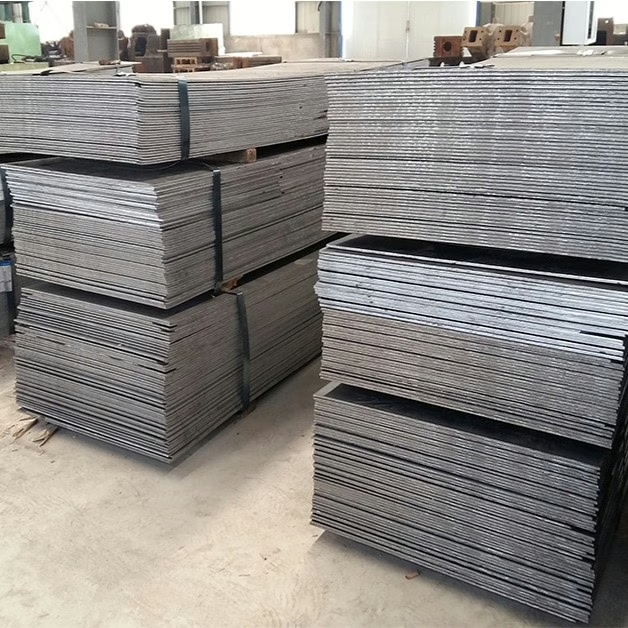
Interested in M2 tool steel?
Please fill out the form below to contact us immediately!
4. Heat Treatment
M2 steel can only achieve the required performance through proper heat treatment. The primary objective of M2 tool steel heat treatment is to transform M2 steel from a softened, annealed state (mainly composed of ferrite and alloy carbides) into a hardened and tempered martensitic structure, in which carbides are distributed in an optimal position to meet the necessary cutting performance requirements.
The typical heat treatment sequence for M2 tool steel involves the following stages:
4.1 Pre-heating
Preheating of materials should be carried out in stages to minimize the risk of thermal shock, especially when there are significant differences in the cross-section of parts. If the furnace is first heated to 650°C (1200°F), we can place M2 parts on the top of the furnace to remove any chill and then place it in the furnace. This helps to reduce thermal shock and lower the risk of cracking. It is then placed in the furnace and kept there for about 10-12 minutes.
4.2 Hardening(Austenitizing)
The hardening temperature for M2 tool steel typically ranges from 1190°C to 1220°C (2175°F to 2225°F). Some references cite up to 1230°C (2250°F). The soaking time at the final hardening temperature for M2 high-speed steel is relatively short, only a few minutes, depending on the part’s size and furnace efficiency.
4.3 Quenching
The quenching medium can be air, oil, or salt. Oil quenching works well for M2 steel parts with a cross-section of up to about 1 to 1.5 inches (25-38 mm). The martensitic transformation begins at about 316°C (600°F) and is completed at about 93°C (200°F). We recommend cooling M2 parts to approximately 65°C (150°F) after quenching, then proceeding to the next step of tempering.
4.4 Tempering
Tempering is performed after quenching M2 high-speed steel to relieve internal stresses, improve toughness, and promote secondary hardness. This involves reheating the steel to an intermediate temperature below its critical transformation temperature.
M2 high-speed tool steel requires 2 to 4 tempering cycles at a temperature of no less than 540°C (1000°F), typically 3 cycles.
For example, after austenitizing at 1230°C (2250°F), the first tempering cycle is performed at 565°C (1050°F), followed by the second at 550°C (1025°F), and the third at 540°C (1000°F).
For each tempering cycle, the soaking time is 2 hours per inch (25 mm) of the thickest cross-section. After the first tempering, the M2 steel component must be completely cooled to room temperature before the next tempering can be performed.
Tempering M2 material serves to transform retained austenite into fresh martensite, causing the precipitation of complex carbides and significantly contributing to the steel’s secondary hardness. Multiple tempering cycles refine the microstructure, enhance wear resistance, and further relieve stresses.
It is important to note that M2 steel must not be undertempered.
Additionally, we recommend performing stress-relief tempering after subsequent processes such as grinding, welding, or electrical discharge machining (EDM), with the tempering temperature set 14–28°C (25–50°F) below the final tempering temperature.
[Reference: ASM International. (1989). ASM Handbook, Volume 16: Machining. ASM International.]
5. Equivalent grades
- USA (AISI/ASTM): M2 (This is the primary designation)
- Germany (DIN/W-Nr): 1.3343, HS6-5-2
- Japan (JIS): SKH51
- Britain (BS): BM2
- China (GB): W6Mo5Cr4V2
- ISO: HS 6-5-2
- France (AFNOR): Z85WDCV06-05-04-02
- Sweden (SS): 2722
- Russia (GOST): R6M5
6. D2 Vs. M2 steel
In industrial production, we often compare D2 tool steel and M2. The comparison data for these two steels is provided in the table below for reference.
Property | D2 Steel | M2 Steel |
Type | Cold-worked tool steel | High-speed steel |
Composition | C: 1.40-1.60%, Cr: 10.00-13.00%, Mo: 0.70-1.20%, V: 0.90%, Mn: 0.60%, Si: 0.60%, Fe: Balance | C: 0.80-1.00%, W: 5.50-6.50%, Mo: 4.50-5.50%, Cr: 3.75-4.50%, V: 1.75-2.25%, Mn: 0.15-0.40%, Si: 0.20-0.45%, Fe: Balance |
Hardness (HRC) | 55-62 | 62-65 |
Wear Resistance | Excellent (room temperature) | Excellent (high temperatures) |
Toughness | Good, better for cold work | Good, adequate for high-speed cutting |
Corrosion Resistance | Fair, semi-stainless | Poor |
Heat Resistance | Poor | Excellent |
Machinability | Fair | Poor |
Cost | Moderate | Higher |
Typical Uses | Dies, punches, shear blades | Drill bits, end mills, taps |
For more information, please read What is the difference between D2 and M2 tool steel?
7. Supply forms and dimensions
The M2 tool steel we supply is available in various shapes, including round bars, sheet plates, slabs, flat bars, square bars, and blocks. The dimensions of the flat bar range from: width 20–600 mm × thickness 20–400 mm × length 1,000–5,500 mm. The dimensions of the round bar range from a diameter of 20–400 mm × a length of 1,000–5,500 mm. The block dimensions are obtained by cutting the flat bar.
For smaller sizes, such as round bars with a diameter less than 70 mm, we use the hot-rolled process. For sizes greater than 70 mm, we offer forged products.
UT testing: Sep 1921-84 D/d, E/e.
Surface Treatment: original black, peeled, machined/turned, polished, grounded, or milled surface finishes.
Inventory Status: We do not maintain a stock of M2 steel. We arrange production based on customer orders.
Delivery time: Electric Arc Furnace (EAF) materials are 30-45 days.
FAQ
1. What is M2 tool steel?
M2 tool steel is a tungsten-molybdenum high-speed steel (HSS) with a well-balanced composition, widely considered the standard and most popular industrial HSS globally. It is a high-carbon, high-molybdenum steel alloy.
2. What are the key properties of M2 tool steel?
M2 tool steel is highly valued for its excellent abrasion resistance, high hardness, and good toughness. It also possesses well-balanced wear resistance and red hardness properties. Its density is 0.294 lb/in³ (8138 kg/m³) and its modulus of elasticity is 30 x 10⁶ psi (207 GPa).
3. What does “red hardness” mean for M2 tool steel?
“Red hardness” refers to the ability of M2 tool steel to maintain high hardness and sharp cutting edges even under high stress and high temperature conditions.
4. Is M2 tool steel a high-alloy steel?
Yes, M2 tool steel is classified as a high-alloy steel because its significant alloying elements, such as molybdenum (4.5%), tungsten (5.5%), and vanadium (2.2%), collectively make up at least 5% of its weight.
5. What are the common applications or uses of M2 tool steel?
M2 tool steel is primarily used for metal-cutting tools, including twist drills, taps, milling cutters, reamers, broaches, and saws. It is also highly suitable for cold work applications like punches, dies, and tools used for forming and pressing. Additionally, its excellent abrasion resistance makes it a good choice for injection molding tooling.
6. Is M2 tool steel good for making knives?
Yes, M2 tool steel is a good material for fabricating knives due to its excellent hardness and abrasion resistance, which enable it to maintain a sharp edge. However, it is not as corrosion-resistant as stainless steels and is not recommended for environments where corrosion resistance is critical.
7. Can M2 tool steel be used for punches?
Yes, M2 tool steel is commonly used in cold-worked punches.
8. How is M2 tool steel typically manufactured?
M2 high-speed tool steel is usually produced by melting metals in an electric arc furnace along with the necessary alloying elements. After impurities are removed, the molten metal is cast into ingots, which are then forged into the desired shapes for further processing. The material is then annealed and hot-rolled into standard stock forms.
9. Can M2 tool steel be forged?
Yes, M2 tool steel can be forged, but it is difficult. It has a low forgeability rating and a high tendency to crack during plastic deformation, even after full annealing.
10. Is M2 tool steel difficult to machine?
Yes, it isn’t easy. M2 steel has high hardness and low machinability, typically 50-60% of 1% carbon steel or 39% of SAE 1112 steel. It is recommended to use specialized tooling, such as that with CBN (Cubic Boron Nitride) cutting tips, due to M2’s high hardness.
11. Can M2 tool steel be welded?
Yes, M2 tool steel can be welded using standard welding methods. It requires preheating to between 204°C and 538°C (depending on original draw temperatures) and a post-weld heat treatment.
12. How does M2 tool steel compare to D2 tool steel?
M2 and D2 tool steels share comparable hardness. However, D2 tool steel has a higher chromium content, providing slightly better corrosion resistance. In contrast, M2 tool steel offers superior toughness and wear resistance compared to D2.
13. What is the difference between M2 and T1 high-speed steel?
The main difference lies in their primary alloying elements: M2 tool steel contains substantial molybdenum and a modest amount of tungsten, whereas T1 tool steel has no molybdenum but a high level of tungsten. M2 has largely replaced T1 in many applications due to its superior properties, including 50% higher bending strength, toughness, and thermo-plasticity, coupled with its relative economy.
14. Does M2 tool steel rust?
Yes, M2 tool steel will rust over time. Despite containing chromium and nickel, it is not primarily formulated for corrosion resistance and has comparatively poor corrosion resistance when compared to stainless steels.
15. What are the disadvantages of using M2 tool steel?
Key disadvantages of M2 tool steel include its low machinability rating, which necessitates specialized tooling and methods. It also has relatively poor corrosion resistance compared to stainless steels. Furthermore, achieving its optimal properties requires extensive and precise heat treatments (annealing, hardening, tempering), adding complexity and cost to its processing. It also exhibits a tendency to crack during plastic deformation if not handled correctly.
16. Is M2 tool steel brittle?
M2 tool steel is known to be brittle in its hardened state or if improperly processed. For instance, it can shatter if pounded with a sledgehammer without proper heat treatment or if dropped. However, when properly processed and tempered, M2 exhibits good toughness, meaning it is less prone to chipping or cracking when exposed to shock loads and tends to bend rather than crack under typical loads.
17. Which is better, M1 or M2 steel?
While both M1 and M2 are all-purpose high-speed tool steels with excellent strength and toughness, M2 emerges as the more widely utilized.
Your Expert Partner for M2 Tool Steel
Aobo Steel brings over 20 years of forging expertise to deliver premium M2 tool steel. Renowned for its excellent wear resistance, high hardness, and toughness, our M2 steel is engineered to enhance your operational efficiency and product quality.
Ready to discuss your specific M2 steel requirements?
Fill out the form below, and our specialists will promptly provide a tailored solution and competitive quotation.
Explore Our Other Products
D2/1.2379/SKD11
D3/1.2080/SKD1
D6/1.2436/SKD2
A2/1.23663/SKD12
O1/1.2510/SKS3
O2/1.2842
S1/1.2550
S7/1.2355
DC53
H13/1.2344/SKD61
H11/1.2343/SKD6
H21/1.2581/SKD7
L6/1.2714/SKT4
M2/1.3343/SKH51
M35/1.3243/SKH55
M42/1.3247/SKH59
P20/1.2311
P20+Ni/1.2738
420/1.2083/2Cr13
422 stainless steel
52100 bearing steel
440C stainless steel
4140/42CrMo4/SCM440
4340/34CrNiMo6/1.6582
4130
5140/42Cr4/SCR440
SCM415