H13 tool steel is an air-hardening hot work tool steel and is one of the most widely used steels among all hot work tool steels. Similar to D2 tool steel as a benchmark for cold work tool steels, H13 is the benchmark for hot work tool steels. Compared to H11 tool steel, this steel grade has higher thermal strength and hardness. It can be air-hardened, so it performs well in terms of quenching deformation and residual stress, and has a lower likelihood of surface oxidation. Additionally, it can achieve secondary hardening, has excellent thermal stability, and can effectively resist corrosion from aluminum alloy molten metal.
Manufacturers widely use this steel grade to produce hot extrusion dies and mandrels, drop hammer forging dies, and forging dies. It is also commonly used for inserts in precision forging machines and die-casting dies for aluminum, copper, and their alloys.
The designation in the U.S. ASTM A681 system is H13, and the name in the American AISI system is AISI H13 steel. Similarly, other national standards use comparable designations, such as ISO 40CrMoV5, Japan/JIS SKD61, USA/UNS T20813, Germany/DIN X40CrMoV5-1, Germany/W-Nr. 1.2344, and Czech Republic (CSN) 19554, BS (BH13), SS (2242), ANFOR (Z40CDV5), and UNI (X35CrMoV05KU / X40CrMoV511KU).
1. Applications
- Hot Work Tooling: It is a primary choice for most hot-working operations, especially when dies require cooling with water or other flushing media.
- Die Casting Molds: H13 material is particularly suitable for die casting zinc, aluminum, and magnesium alloys, such as push rods, ejector pins, core pins, slides, nozzles, and sprues. H13 material blocks purified by electroslag remelting (ESR) are suitable for plastic molds that require a high surface finish, such as automotive lens molds, due to their higher purity and uniformity.
- Hot Forging Dies and Punches
- Hot Extrusion Dies: Hot extrusion of light metals such as aluminum and magnesium, as well as for mandrels, punches, and dies.
- Plastic Injection Molds: This is the most common application, especially for machining cavities.
- Shearing Blades: Hot shearing applications.
- Friction Stir Welding (FSW) Tools: FSW tools, particularly for welding aluminum plates, are often coated with TiN for enhanced performance. [References: Totten, G. E., & MacKenzie, D. S. (Eds.). (2003). Handbook of Aluminum: Volume 2: Alloy Production and Materials Manufacturing (p. 581).]
- Structural Components: H13 steel has high strength and can maintain its hardness at high temperatures, so it is used in structural components that are subject to high stress, such as aircraft landing gear, arrester hooks, and rocket shells in the aerospace industry.
2. H13 Steel Composition
Element | Carbon (C) | Chromium (Cr) | Molybdenum (Mo) | Vanadium (V) | Silicon (Si) | Manganese (Mn) | Phosphorus (P) | Sulfur (S) |
Content (%) | 0.32 – 0.45 | 4.75 – 5.50 | 1.10 – 1.75 | 0.80 – 1.20 | 0.80 – 1.25 | 0.20 – 0.60 | ≤ 0.030 | ≤ 0.030 |
[References: Bringas, J. E. (Ed.). (2002). Handbook of Comparative World Steel Standards (2nd ed., p. 434). ASTM International.]
3. H13 tool steel properties
H13 mold steel is a hot-work tool steel widely used globally. It is characterized by high strength, high toughness, high hardenability, and resistance to thermal cracking. In particular, it can maintain its strength and hardness at high temperatures. Additionally, it has excellent comprehensive mechanical properties and high tempering stability.
3.1 Mechanical Properties
The specific properties depend heavily on the tempering temperature. Here are typical longitudinal mechanical properties when air cooled from 1025 °C (1875 °F) and tempered:
Key Mechanical Properties (Typical Values at Room Temperature, Double Tempered 2h + 2h)
Property | 527 °C (980 °F) Temper | 555 °C (1030 °F) Temper | 575 °C (1065 °F) Temper |
Hardness | 52 HRC | 50 HRC | 48 HRC |
Tensile Strength (Rm) | 1960 MPa (284 ksi) | 1835 MPa (266 ksi) | 1730 MPa (251 ksi) |
Yield Strength (Rp0.2) | 1570 MPa (228 ksi) | 1530 MPa (222 ksi) | 1470 MPa (213 ksi) |
Elongation (in 4D) | 13.0% | 13.1% | 13.5% |
Reduction in Area | 46.2% | 50.1% | 52.4% |
Charpy V-notch Impact | 16 J (12 ft·lbf) | 24 J (18 ft·lbf) | 27 J (20 ft·lbf) |
3.2 Physical properties
Property | Value |
---|---|
Density | 7.75 – 7.80 g/cm3 |
Tensile Strength, Ultimate | 1200 – 2050 MPa (174000 – 231000 psi) |
Tensile Strength, Yield | 1000 – 1380 MPa (145000 – 200000 psi) |
Hardness | 45-52 HRC (Rockwell C Hardness) |
Impact Toughness | 20-40 J/cm2 |
Compressive Strength | 2550 MPa |
3.3 Other Important Properties:
- Wear Resistance: Excellent wear resistance. To further improve wear resistance, it can be nitrided, which can increase its surface hardness to over 1000 HV (>70 HRC).
- Toughness & Impact Strength: Excellent impact strength and good ductility.
- Heat Checking Resistance: Excellent resistance to thermal cracking, and this characteristic is influenced by its unnotched impact toughness and hardness.
- Fatigue Resistance: Good fatigue resistance, and in this respect, this steel has an advantage over 4340 alloy steel.
- Dimensional Stability: When this steel undergoes air quenching, its volume typically expands by approximately 0.001 in./in. (0.001 mm/mm).
- Machinability: If the machinability rating of carbon steel with a carbon content of 1% is set to 100, then H13 has a machinability rating of 70 when properly annealed.
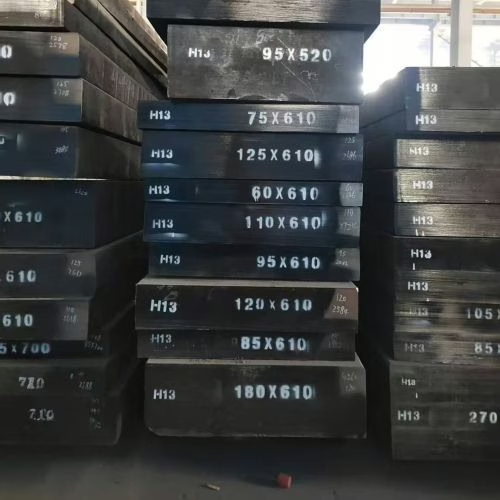
Interested in H13 tool steel?
Fill out the form below to contact us, and we will respond within 12 hours!
4. Heat Treatment
The H13 steel heat treatment involves several critical steps to achieve the desired properties:
4.1 Forging and Post-Forging Cooling
It is easy to forge and is typically forged at temperatures between 1120 and 1150°C (2050 to 2100°F). Before forging, we recommend preheating the steel to 790 to 815°C (1450 to 1500°F), then uniformly heating it to the required forging temperature.
During forging, the material temperature must not drop below 925°C (1700°F). If it is about to fall below this temperature, it must be reheated to the required forging temperature.
This material is an air-hardening steel that must be cooled slowly to prevent stress cracking. After forging, the material must be placed in a furnace at 790°C (1450°F) and held until the temperature is uniform; then cooled slowly.
4.2 Annealing (Spheroidize Anneal)
Following the previous step, the H13 material should undergo spheroidizing annealing, which aims to eliminate stress, enhance the toughness and ductility, and form the required microstructure.
The specific details of the annealing process are as follows: heat the steel to 871°C (1600°F), hold for 1 hour per inch (25.4 mm) of thickness, then cool at a rate of 14°C (25°F) per hour down to 482°C (900°F), followed by air cooling to room temperature.
4.3 Normalizing (Generally Not Recommended)
Because of the risk of cracking, we generally do not recommend normalizing treatment for H13, especially when surface decarburization is not prevented by a controlled atmosphere furnace. However, this normalizing treatment can still improve the uniformity of the material. This step must be performed immediately after spheroidizing annealing.
The specific steps are as follows: preheat to approximately 790 °C (1450 °F), slowly and uniformly heat to 1040 to 1065 °C (1900 to 1950 °F), hold for 1 hour per 25 mm (1 inch) of thickness, and then air cool.
4.4 Hardening (Austenitizing and Quenching)
The hardening temperature is around 1030 °C (1885 °F). Other sources suggest a range of 1010-1040 °C (1850-1900 °F), or specifically 1025 °C (1875 °F).
H13 is an air-hardening steel, and we recommend performing a preheating treatment. The purpose is to stabilize the crystalline structure, reduce hardness, increase ductility, improve machinability, promote uniform grain structure, and minimize distortion/cracking. The preheating temperature is 815 °C (1500 °F). For a 1” (25mm) cube, it should be preheated to 650 °C (1200 °F) and held for 10 to 15 minutes before setting the furnace for the soaking step. For delicate parts, an additional preheat may be necessary.
After preheating, raise the furnace temperature to its austenitizing temperature of 1010 °C (1850 °F). The soaking process then begins, with the soaking time calculated from the moment the material’s temperature is the same as the furnace temperature. Specific details are as follows: For parts thicker than 1“ (25mm), the soak time is typically half an hour per inch of the smallest cross-section. For smaller parts, specific soak times are provided: 1/8” (3.175mm) for 10-15 minutes, 1/4” (6.350mm) for 15 minutes, 1/2“ (12.70mm) for 20 minutes, 3/4” (19.05mm) for 25-30 minutes, and 1” (25mm) for 30 minutes.
Air quenching can minimize residual stress and reduce thermal shock. While air quenching is the most common method for H13, oil quenching is also used in practice, but it increases internal stresses. The hardness after quenching is 52-54 HRC. During the quenching cycle of the material, the next step of tempering should be performed immediately at a temperature no lower than 66°C/150°F to prevent cracking.
4.5 Tempering
The purpose is to reduce brittleness, transform martensite into a more stable microstructure, improve toughness, relieve stresses while retaining hardness.
We recommend tempering H13 twice or even three times to achieve optimal toughness and extend tool life. The first tempering temperature is 565°C (1050°F), the second tempering temperature is 550°C (1025°F), with each cycle lasting 2 hours per inch (25mm) of thickness.
After tempering, the hardness varies with the tempering temperature. For example, as-quenched H13 has a hardness of 52-54 HRC. Tempering at 204°C (400°F) results in 51-53 HRC, while tempering at 538°C (1000°F) yields 47-48 HRC, and at 621°C (1150°F) it can be 36-38 HRC. Common tempering temperatures range from 540-620°C (1000-1150°F), producing a stable microstructure that makes the material most suitable for high-temperature applications.
It is essential to avoid tempering H13 at around 500°C (930°F), as this temperature yields the lowest toughness.
5. Welding
H13 steel is readily weldable, especially for repair applications in molds, tools, and dies. Gas Tungsten Arc Welding (GTAW or TIG) is the most suitable welding process for H13 molds, tools, and dies, and can also be performed using an inert gas process or coated electrodes. When welding, the minimum recommended arc voltage and current must be used, and the electrode must be moved slowly in a straight line to minimize heat input. Clean slag frequently and peen the welds while they are still hot (above 370°C or 700°F); never peen a cold weld.
Preheating. Preheating is essential before welding H13 steel, as cold welding can easily cause cracking. The preheating temperature should be between 110°C (230°F) and 375°C (707°F).
Filler Wire. H13 filler wire is the preferred choice. If H13 filler wire is not available on site, a general-purpose medium-hardness tool steel filler wire designed specifically for thermal and cold working tools can be used.
Shielding Gas. Argon is the standard welding gas for TIG welding H13, and it protects the weld seam from contamination. Hydrogen can be used as a backing shielding gas for the underside of the weld when an explosion risk is not present.
Post-Welding Treatment for H13 Tool Steel. After welding, H13 welded parts (especially thick-walled welded parts) should be cooled slowly, either in a furnace at the preheating temperature or using an insulating medium (such as furnace slag, lime, mica, or diatomaceous earth). After slow cooling, the weld should undergo complete spheroidizing annealing.
6. H13 Steel Advantages and Disadvantages
6.1 Advantages
- Excellent Toughness and Impact Strength
- High Wear Resistance. H13’s relatively high vanadium content makes it very resistant to abrasion. This is because vanadium promotes the formation of very hard, stable carbides (like V8C7, MC type), which significantly increase wear resistance. Nitriding treatment can further improve the wear resistance of H13.
- Excellent Hot Hardness, Temper Resistance, and Thermal Stability
- High Hardenability and Dimensional Stability
- Good Resistance to Heat Checking (Thermal Fatigue)
- Weldability and Machinability. H13 is readily weldable, and after appropriate annealing treatment, it has good machinability
6.2 Disadvantages
- High-cost. H13 tool steel is generally limited by its high cost. The high content of alloying elements contributes to this cost. Of course, this is only a relative disadvantage. Our customers in China have a very high demand for H13 steel, exceeding 2,000 tons per month, mainly for aluminum profiles.
- Fabrication and Processing Difficulties. The heat treatment process for H13 during production may be relatively complex, which is mainly a challenge for manufacturers. Additionally, its machinability is more difficult compared to low-alloy materials. As mentioned earlier in the article, the good machinability of H13 is one of its advantages, so both advantages and disadvantages are relative.
- Toughness and Brittleness Issues. It is quite sensitive to quench embrittlement, where precipitation of carbides along prior-austenite grain boundaries can significantly reduce toughness by creating paths for crack propagation, especially for large-section materials.
- Susceptibility to Cracking and Distortion. Improper quenching processes, insufficient tempering time, or low tempering temperatures can all increase the risk of cracking and deformation.
- Limited High-Temperature Performance. Although H13 is a hot-work steel, its strength decreases at temperatures above 650°C.
7. Compare with other steels
7.1 Compared to D2 tool steel
H13 steel is used in high-temperature conditions, where it exhibits excellent resistance to softening, thermal fatigue, and impact. Compared to cold-worked steel, however, it has lower wear resistance. D2 steel, on the other hand, performs exceptionally well in cold-working applications, offering high wear resistance and excellent dimensional stability. Compared to H13, however, D2 has lower toughness and poorer performance in high-temperature conditions.
Here is a side-by-side comparison highlighting their key differences and similarities:
Feature/Property | H13 Tool Steel (AISI H-Series) | D2 Tool Steel (AISI D-Series) |
Primary Application | Hot Work: Ideal for applications involving high temperatures and thermal fatigue, such as die casting molds, hot forging, and hot extrusion. Also used in plastic injection molds. | Cold Work: Best suited for applications requiring high wear resistance at room temperature, like long-run dies, blanking, piercing, and trimming tools. |
Classification | Hot-work die steel, 5% Chromium group. | High-carbon, high-chromium cold-work tool steel. |
Wear Resistance | Very Good | Excellent |
Toughness | High impact strength, good resistance to brittle fracture | Lower impact strength and toughness compared to H13 |
Hot Hardness / Tempering Resistance | Excellent, performs well up to 700°C (1300°F) | Limited, not designed for high-temperature use; typically restricted below 205-260°C (400-500°F) due to softening |
Hardenability | Deep hardening, air-hardening, minimal distortion. Can be hardened in large sections. | Deep hardening, air-hardening, minimal movement, and distortion during hardening. Can be fully hardened in large sections. |
Dimensional Stability | Very low distortion; expands approximately 0.001 in./in. when air quenched. | Minimum distortion; expands/contracts approximately 0.0005 in./in. when air quenched. |
Machinability | Good | Poor |
Heat Checking | Very good resistance, especially in cast form. | Not a primary characteristic, as it’s typically used in cold applications. |
Weldability | Readily weldable | Difficult to weld (nonweldable) |
7.2 Compared to M2 tool steel
M2 is primarily used for high-speed cutting, boasting excellent wear resistance and thermal hardness.
Feature | H13 Steel | M2 Steel |
Classification | Hot-work die steel (5% Cr steel). | Molybdenum-type high-speed steel (HSS), general purpose. |
Primary Use | Applications involving high temperatures and loads, such as die casting, hot forging, hot extrusion dies, and plastic molds. | Metal cutting and machining operations. |
Wear Resistance | High, | Very High |
Toughness | Good, excellent impact strength, | Good, |
Hot Hardness / Temper Resistance | Excellent resistance to tempering, maintains high hardness and strength at elevated temperatures due to secondary hardening. Can operate up to 700°C. | Very high, superior to H13, especially at higher temperatures; develops secondary hardness. Cobalt additions further enhance hot hardness. |
Hardenability | Deep hardenability; can be hardened through in large sections by air cooling. | Deep hardenability. Most forgiving hardening range among HSS. |
Distortion | Minimal due to air hardening. | Medium. |
Machinability | Fairly good in annealed condition | Medium. |
Weldability | Readily weldable | Difficult to weld (nonweldable) |
8. Supply forms and dimensions
The H13 tool steel we supply is available in three shapes: flat bar, block, and round bar. The dimensions of the flat bar range from: width 20–600 mm × thickness 20–400 mm × length 1,000–5,500 mm. The dimensions of the round bar range from a diameter of 20–400 mm × a length of 1,000–5,500 mm. The block dimensions are obtained by cutting the flat bar.
For smaller sizes, such as round bars with a diameter less than 70 mm, we use the hot-rolled process. For sizes greater than 70 mm, we offer forged products.
We also offer the ESR (Electroslag Remelting) process, which is tailored to meet customer requirements. The advantage is better internal microstructure, but it comes at a higher cost. Please contact us for specific requirements.
UT testing: Sep 1921-84 D/d, E/e.
Surface Treatment: original black, peeled, machined/turned, polished, grounded, or milled surface finishes.
Inventory Status: We do not maintain a stock of H13 tool steel. We arrange production based on customer orders.
Delivery time: Electric Arc Furnace (EAF) materials are 30-45 days. ESR materials are approximately 60 days.
Many of our customers choose non-ESR processes when considering cost-effectiveness. Please discuss your specific requirements with us directly.
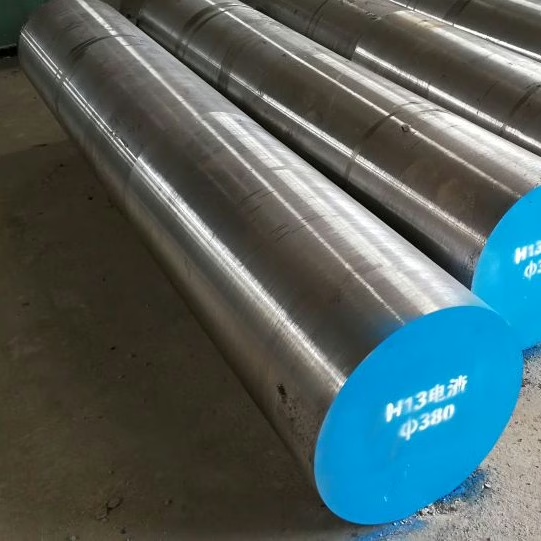
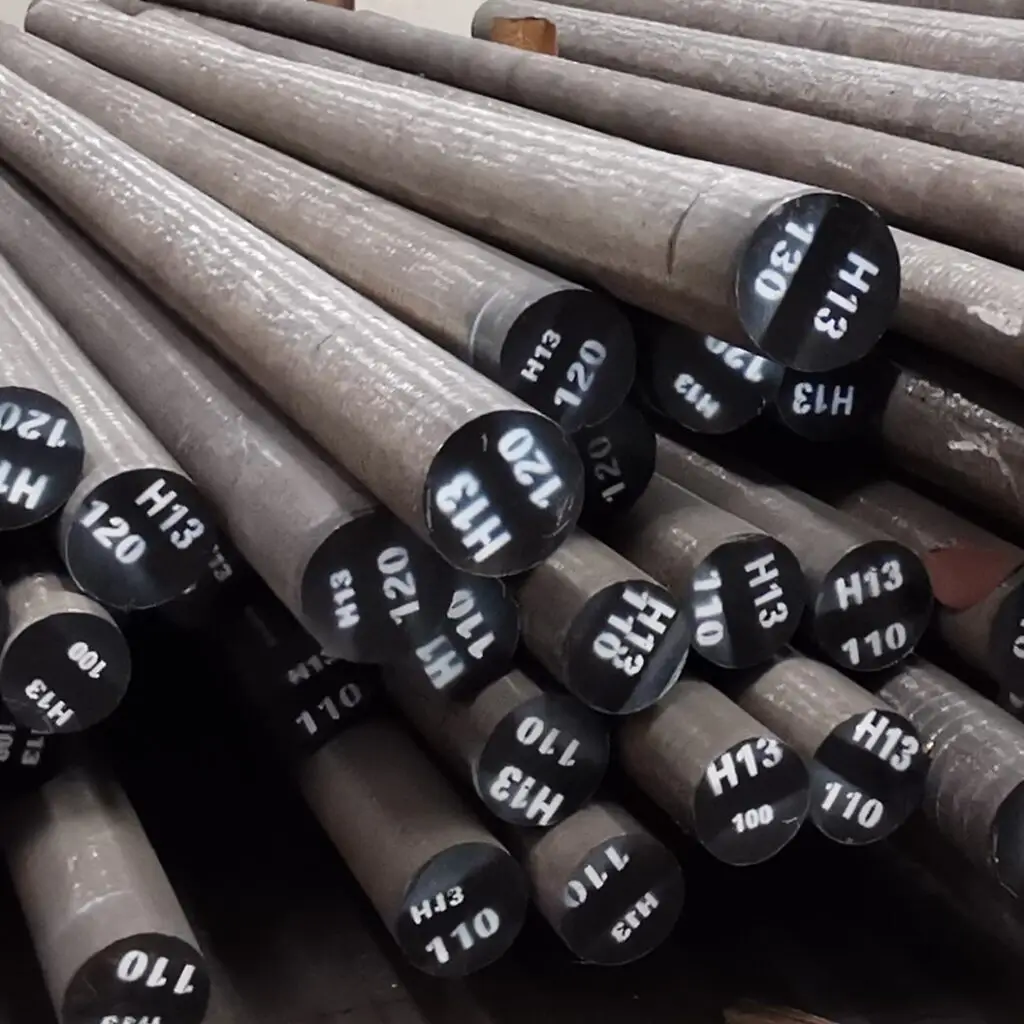
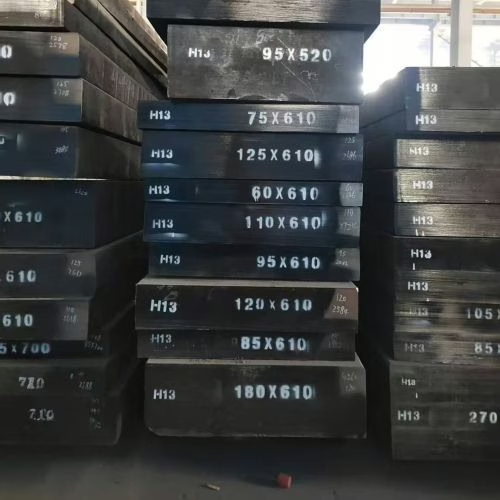
FAQ
1. Can H13 steel be welded?
Yes, H13 tool steel can be welded, but it has limited weldability and requires specific procedures due to its air-hardening nature and susceptibility to cracking during and after welding. Preheating before welding, maintaining suitable interpass temperatures, and performing post-weld heat treatment (PWHT) are essential to minimize cracking and preserve its properties. Gas Tungsten Arc Welding (GTAW) is often recommended for its control.
2. Is H13 high-speed steel?
H13 steel is not classified as a high-speed steel. It is identified as a hot-work tool steel.
3. What is the ultimate strength of H13?
The ultimate strength (also known as tensile strength) of H13 steel varies depending on the tempering temperature and manufacturing process. Typical room-temperature longitudinal mechanical properties of H13 steel, based on bars tempered to different hardness levels, are as follows:
- When tempered at 527 °C (980 °F), the tensile strength is typically 1960 MPa (284 ksi).
- When tempered at 555 °C (1030 °F), the tensile strength is typically 1835 MPa (266 ksi).
- When tempered at 575 °C (1065 °F), the tensile strength is typically 1730 MPa (251 ksi).
- When tempered at 593 °C (1100 °F), the tensile strength is typically 1580 MPa (229 ksi).
- When tempered at 605 °C (1120 °F), the tensile strength is typically 1495 MPa (217 ksi).
4. Is H13 hard to machine?
Yes, H13 steel can be difficult to machine, especially when hardened. However, its machinability can be influenced by its condition and the specific machining operation.
5. What is the Rockwell hardness of H13 steel?
The recommended hardness range for H13 tool steel is generally 40-55 HRC. Specific applications and tempering temperatures can result in values ranging from 36 HRC (at a tempering temperature of 621°C) to 56 HRC (at a tempering temperature of 500°C). Forging tools in service typically range from 38-52 HRC.
6. What is the difference between H11 and H13 steel?
The primary difference between H11 and H13 steel lies in their vanadium content and the resulting impact on their properties. H13 may show slightly lower toughness than H11, especially during quench embrittlement.
7. What are the main characteristics of H13 tool steel?
Key characteristics include exceptional heat resistance, high toughness, high hot strength, high hot wear resistance, high retention of hardness, and strong resistance to thermal fatigue (heat checking)
8. Does H13 tool steel have good wear resistance?
Yes, H13 tool steel has excellent wear resistance. This property can be further improved by nitriding, which can increase surface hardness to over 1000 HV, equivalent to more than 70 HRC.
9. Is H13 tool steel resistant to thermal fatigue (heat checking)?
H13 tool steel has excellent resistance to thermal fatigue cracking.
10. What are the mechanical properties of H13 tool steel?
Typical mechanical properties at room temperature (when double tempered) include an Ultimate Tensile Strength ranging from 1200 to 2050 MPa (174,000-231,000 psi) and Yield Strength from 1000 to 1570 MPa (145,000-228,000 psi). Specific values are highly dependent on the tempering temperature. It also possesses good impact strength and ductility, with a Charpy V-notch impact strength of 16-27 J depending on tempering.
11. Does H13 tool steel rust or have corrosion resistance?
No, H13 tool steel is not highly corrosion-resistant compared to stainless steel or other specialized alloys. It is primarily chosen for its strength and heat resistance rather than its corrosion properties, and is prone to rust in aggressive environments, including those with moisture, humidity, or chemically aggressive plastics.
11. What factors can cause H13 tool steel dies to fail prematurely?
Common failure mechanisms include wear, mechanical fatigue, gross cracking, plastic deformation, and thermal fatigue cracking (heat checking). These can be exacerbated by factors such as too low billet temperature, inadequate die design (e.g., sharp radii, thin walls), improper heat or surface treatment, insufficient die support, or high cavity stress levels.
12. How is H13 tool steel heat-treated for optimal hardness and toughness?
The hardening process typically involves preheating to around 815°C (1500°F), then raising the temperature to an austenitizing range of 1010-1040°C (1850-1900°F), followed by air quenching. Tempering is crucial and usually performed twice or three times, at temperatures typically between 540-620°C (1000-1150°F), with each cycle lasting approximately 2 hours per inch of thickness. Avoiding tempering around 500°C (930°F) is critical as it yields the lowest toughness.
13. What maintenance practices are recommended to optimize H13 tool hardness and lifespan?
We recommend performing regular inspections for signs of wear or fatigue, applying recoating or retempering when necessary, and avoiding overheating during operation, which can soften the material. Proper die preheating also significantly reduces the risk of catastrophic failure via cracking.
14. How does surface treatment benefit H13 tool steel?
Surface treatments are commonly applied to H13 tool steel to enhance wear resistance. Nitriding, for example, is a thermochemical treatment that creates a hard surface layer and can induce compressive residual stress, which helps counteract heat checking. However, the nitrided layer can be brittle, so careful control of thickness (e.g., typically no more than 0.3 mm) is necessary.
15. What are the international equivalent standards for H13 tool steel?
H13 tool steel has various international equivalents, including AISI H13 (USA), X40CrMoV5-1 (Europe/Germany DIN 1.2344), and SKD61 (Japan JIS).
Unlock Superior Performance with Our H13 Tool Steel
At Aobo Steel, we leverage over 20 years of forging expertise to deliver premium H13 tool steel. Renowned for its exceptional hot hardness, toughness, and resistance to thermal fatigue, our H13 is the ideal choice for your most demanding applications, including die casting, extrusion dies, and forging tools.
Partner with a trusted supplier backed by over 40 stable material sources. Get the consistent quality and reliability your operations depend on.
Ready to Enhance Your Production with Top-Quality H13?
Simply fill out the contact form below. Our H13 specialists will promptly get in touch to discuss your requirements and provide a personalized quote.
Explore Our Other Products
D2/1.2379/SKD11
D3/1.2080/SKD1
D6/1.2436/SKD2
A2/1.23663/SKD12
O1/1.2510/SKS3
O2/1.2842
S1/1.2550
S7/1.2355
DC53
H13/1.2344/SKD61
H11/1.2343/SKD6
H21/1.2581/SKD7
L6/1.2714/SKT4
M2/1.3343/SKH51
M35/1.3243/SKH55
M42/1.3247/SKH59
P20/1.2311
P20+Ni/1.2738
420/1.2083/2Cr13
422 stainless steel
52100 bearing steel
440C stainless steel
4140/42CrMo4/SCM440
4340/34CrNiMo6/1.6582
4130
5140/42Cr4/SCR440
SCM415