فولاذ الأدوات H11 عبارة عن فولاذ تصلب عن طريق تبريد الهواء فولاذ أداة العمل الساخن. It has excellent toughness, thermal strength, fatigue performance, and wear resistance at medium temperatures. Additionally, it retains some toughness in the quenched state and demonstrates strong resistance to thermal fatigue. When air-quenched at lower austenitizing temperatures, it exhibits minimal heat treatment deformation and a low tendency to form oxide skin. H11 tool steel can effectively resist the corrosion of molten aluminum, making it a popular choice for manufacturing aluminum die casting molds, hot extrusion tools, stamping and forging molds, and plastic molds.
تسمية هذا الفولاذ هي H11 في نظام ASTM A681 الأمريكي. وبالمثل، تستخدم معايير وطنية أخرى تسميات مماثلة، مثل ISO X37CrMoV5-1، واليابان/JIS SKD6، والولايات المتحدة/UNS T20811، وألمانيا/DIN X38CrMoV5-1، وألمانيا/W-Nr. 1.2343، وجمهورية التشيك (CSN) 19552، والصين/GB. 4Cr5MoSiV.
1. التطبيقات
- قوالب الصب
- قوالب التشكيل
- أدوات البثق
- شفرات القص الساخنة:
- مكونات الفضاء الجوي
2. التركيب الكيميائي1
ج | من | سي | كر | شهر | الخامس |
0.33 – 0.43% | 0.20 – 0.60% | 0.80 – 1.25% | 4.75 – 5.50% | 1.10 – 1.60% | 0.30 – 0.60% |
3. الخصائص2
يتمتع الفولاذ H11 بمزيج استثنائي من الصلابة التي يمكن تحقيقها، والصلابة الحمراء (الصلابة الساخنة)، والمتانة، ومقاومة التآكل.
- قوة:يمكن معالجتها حرارياً إلى قوى إنتاجية تبلغ 0.2% أعلى بكثير من 1380 ميجا باسكال (200 كيلو باسكال) وقوة الشد النهائية تتجاوز 2070 ميجا باسكال (300 كيلو باسكال).
- صلابةتتراوح صلادة العمل العادية عادةً بين 40 و55 HRC. في تطبيقات مثل صب الألومنيوم بالقالب، يُفضل استخدام صلابة 47 HRC. في صب القالب، يمكن تقوية قوالب H11 إلى 42-52 HRC، والحشوات والأنوية إلى 46-52 HRC، والمكابس إلى 46-50 HRC، والشرائح إلى 46-52 HRC، وأكمام القذف إلى 44-48 HRC، والفوهات إلى 32-42 HRC. بالنسبة لقوالب وثقوب التشكيل بالطرق الساخن، تتراوح صلادتها عادةً بين 44 و48 HRC. تستخدم أسطوانات الدرفلة الساخنة (للتشغيلات القصيرة ودرجات الحرارة المنخفضة) H11 بصلابة 40-48 HRC. عادةً ما تكون قوالب التشكيل بالطرق الساخن بصلابة 48-52 HRC.
- صلابة ساخنة/صلابة حمراء: يتميز بمقاومة جيدة للطقس، مع الحفاظ على صلابته ومتانته العالية في درجات الحرارة المرتفعة. كما يقاوم التليين أثناء التعرض المستمر لدرجات حرارة تصل إلى 540 درجة مئوية (1000 درجة فهرنهايت). ورغم أن صلابته الساخنة أقل من بعض أنواع الفولاذ الأخرى المُستخدمة في الشغل الساخن، مثل H19 أو H21، إلا أنه يحتفظ بصلابته بشكل أفضل من أنواع الفولاذ متوسطة السبائك الأخرى في درجات الحرارة المرتفعة. تُعد الصلابة الساخنة/الصلابة الحمراء خاصية مهمة جدًا في فولاذ الأدوات المُستخدم في الشغل الساخن.
- الصلابة والليونة: يتمتع بصلابة ومتانة جيدتين. كما يتميز بمقاومة أفضل للكسر الهش مقارنةً بالفولاذ ذي المحتوى العالي من السبائك مثل H14 وH19 وH21. يمكن لعمليات إعادة الصهر بالكهرباء الخبثية (ESR) أو إعادة الصهر بالقوس الفراغي (VAR) تحسين اللدونة والمتانة بشكل ملحوظ.
- مقاومة التعبتتميز هذه المادة بمقاومة عالية للتعب وثبات حراري في نطاق درجات حرارة يتراوح بين 75 و540 درجة مئوية (167 و1000 درجة فهرنهايت). وبالمقارنة مع الفولاذ 4340 الذي خضع لنفس المعالجة الحرارية عالية الكثافة، يتميز الفولاذ H11 بمقاومة أفضل للتعب.
- مقاومة التآكل:مقاومته للتآكل أقل من مقاومة H13.
- قابلية اللحام: It is readily weldable, even in heavy sections.
- قابلية التصنيع: Good machinability, rated around 70% of a standard 1% carbon steel.
- الخصائص الحرارية:يتمتع بمعامل تمدد حراري منخفض نسبيًا وموصلية حرارية تبلغ 26 واط/م·ك.
- مقاومة التآكل:مقاومة أعلى من المتوسط للأكسدة والتآكل.
- مقاومة فحص الحرارة:مقاومة جيدة للتعب الحراري أو اختبار الحرارة.
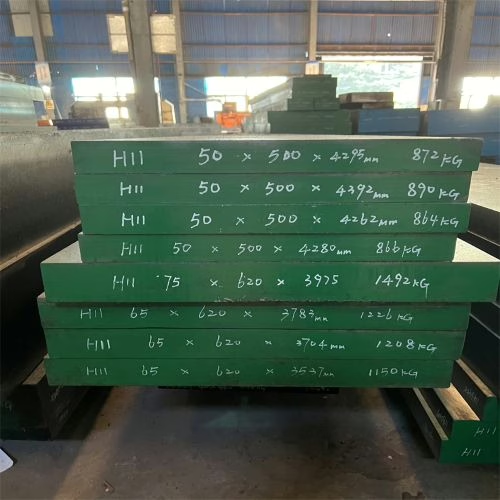
Interested in H11 tool steel? إملأ النموذج أدناه للتواصل معنا الآن!
4. المعالجة الحرارية لفولاذ الأدوات H11
دقيق المعالجة الحرارية لفولاذ الأدوات H11 يُعدّ هذا الأمر بالغ الأهمية لتحقيق الأداء الأمثل لفولاذ 5% المُشكّل على الساخن والمُغلّف بالكروم، بالإضافة إلى الفولاذ فائق القوة، على غرار H11 Modified وH13. تُحسّن هذه العملية البنية الدقيقة لتلائم متطلبات أدوات المصانع المُتطلبة.
4.1 التشكيل
يتم تشكيل هذا الفولاذ بسهولة، مع نطاق درجة حرارة تشكيل مناسبة يبلغ 1120 إلى 1150 درجة مئوية (2050 إلى 2100 درجة فهرنهايت).نوصي تسخين السبيكة مسبقًا إلى 790 إلى 815 درجة مئوية (1450 إلى 1500 درجة فهرنهايت)، ثم تسخينه بالتساوي إلى درجة حرارة التشكيل. يجب أن تكون درجة حرارة التشكيل لا يكون أقل من 925 درجة مئوية (1700 درجة فهرنهايت)إذا انخفضت درجة الحرارة إلى ما يقرب من هذا المستوى، فيجب إعادة تسخينها قبل مواصلة عملية التشكيل.
4.2 الأوستنيت (التصلب)
تتضمن عملية الأوستنيت، وهي الخطوة الأساسية للتصلب، التسخين لتحويل بنيتها إلى الأوستينيت. وهذا يسمح بالتحويل والتحلل الموحد لعناصر السبائك والكربيدات.
- التسخين المسبق: يوصى بتسخين H11 إلى 760-815 درجة مئوية (1400-1500 درجة فهرنهايت) قبل الأوستنيت لتقليل الصدمات الحرارية والتشقق، وخاصة لهذه المادة ذات السبائك العالية.
- درجات حرارة الأوستنيت وأوقات النقع: تتراوح درجة حرارة الأوستنيت بين ٩٩٥ و١٠٢٥ درجة مئوية (١٨٢٥ و١٨٧٥ درجة فهرنهايت). مدة النقع ٢٠ دقيقة + ٥ دقائق لكل ٢٥ مم (بوصة واحدة) من السُمك.
يضمن الاحتفاظ بدرجة حرارة الأوستنيت التحول والتحلل الموحد.
4.3 التبريد
بعد الأوستنيت، يُبرَّد فولاذ H11 بسرعة لتشكيل مارتنسيت صلب. H11 هو فولاذ مُقَوّى بالهواء، مما يُوفِّر تصلبًا موحدًا للمقاطع الكبيرة مع أدنى حد من الإجهاد المتبقي والتغير في الأبعاد. يُعد التبريد الهوائي الطريقة القياسية والمفضلة لفولاذ الأدوات H11. في حين أن التبريد الهوائي هو المعيار، يُعد التبريد بالزيت من 995 درجة مئوية (1825 درجة فهرنهايت) بديلًا ممكنًا. يجب استخدام H11 وغيره من فولاذ أدوات العمل الساخن. لا تطفأ أبدًا بالماء، حيث أن هذا يمكن أن يؤدي إلى التشقق.
4.4 التلطيف
After hardening, tempering H11 tool steel by reheating to a lower temperature is crucial for improving toughness, relieving stress, and stabilizing properties. Steel H11 is a secondary hardening steel. It achieves its best performance when tempered at temperatures above 510°C (950°F). We recommend performing multiple tempering treatments on it to achieve optimal toughness and extend tool life. Allow parts to cool to room temperature between each tempering cycle to minimize residual austenite.
4.5 التلدين
The annealing temperature is 845-900 درجة مئوية (1550-1650 درجة فهرنهايت). معدل التبريد هو 22-40 درجة مئوية/ساعة (40-75 درجة فهرنهايت/ساعة). الصلابة بعد التلدين هي 192-229 HB.
4.6 اعتبارات أخرى مهمة للمعالجة الحرارية لمادة H11
- التطبيع: هذه العملية عادة ما تكون غير موصى به بالنسبة لفولاذ الأدوات H11 أو H13 بسبب ارتفاع خطر التشقق، وخاصة مع إزالة الكربون من السطح.
- تخفيف التوتر: بعد خضوع H11 لعمليات المعالجة، مثل الطحن أو اللحام أو التفريغ الكهربائي (EDM)، نوصي بشدة بمعالجته لتخفيف الإجهاد عند درجة حرارة 650 درجة مئوية. يجب إجراء هذه المعالجة عند درجة حرارة أقل من درجة حرارة المعالجة السابقة بمقدار 14-28 درجة مئوية (25-50 درجة فهرنهايت). بعد تخفيف الإجهاد، يُبرّد ببطء بمعدل أقصى 300 درجة مئوية/ساعة لمنع تكوّن إجهادات جديدة.
- العلاج بالتبريد: Sub-zero treatment (e.g., -73°C / -100°F) can reduce retained austenite, but H11’s high tempering temperatures usually make it unnecessary for achieving maximum secondary hardening response.
- حماية السطح: حماية أسطحها من الأكسدة وإزالة الكربون أثناء المعالجات عالية الحرارة، مثل الأوستنيت والتلدين، أمرٌ بالغ الأهمية. ويتم ذلك غالبًا باستخدام أجواء مُتحكم بها، أو أفران تفريغ، أو حمامات ملحية.
5. أشكال وأبعاد التوريد
يتوفر فولاذ الأدوات H11 الذي نوفره بأشكال متنوعة، بما في ذلك القضبان المستديرة، والصفائح، والألواح، والقضبان المسطحة، والقضبان المربعة، والكتل. تتراوح أبعاد القضبان المسطحة بين: العرض 20-600 مم × السُمك 20-400 مم × الطول 1000-5500 مم. تتراوح أبعاد القضبان المستديرة بين القطر 20-400 مم × الطول 1000-5500 مم. يتم الحصول على أبعاد الكتل بقطع القضبان المسطحة.
للأحجام الصغيرة، مثل القضبان المستديرة التي يقل قطرها عن 70 مم، نستخدم عملية الدرفلة الساخنة. أما الأحجام التي تزيد عن 70 مم، فنقدم منتجات مزورة.
اختبار UT: سبتمبر 1921-84 D/d، E/e.
معالجة السطح: سطح أسود أصلي، مقشر، ميكانيكي/مخروطي، مصقول، مؤرض، أو مطحون.
حالة المخزون: لا نحتفظ بمخزون من فولاذ الأدوات H11. نرتب الإنتاج بناءً على طلبات العملاء.
مدة التسليم: مواد فرن القوس الكهربائي (EAF) تتراوح بين 30 و45 يومًا. ومواد فرن القوس الكهربائي (ESR) حوالي 60 يومًا.
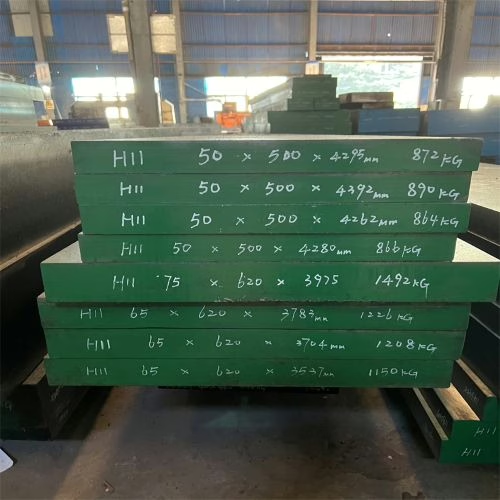
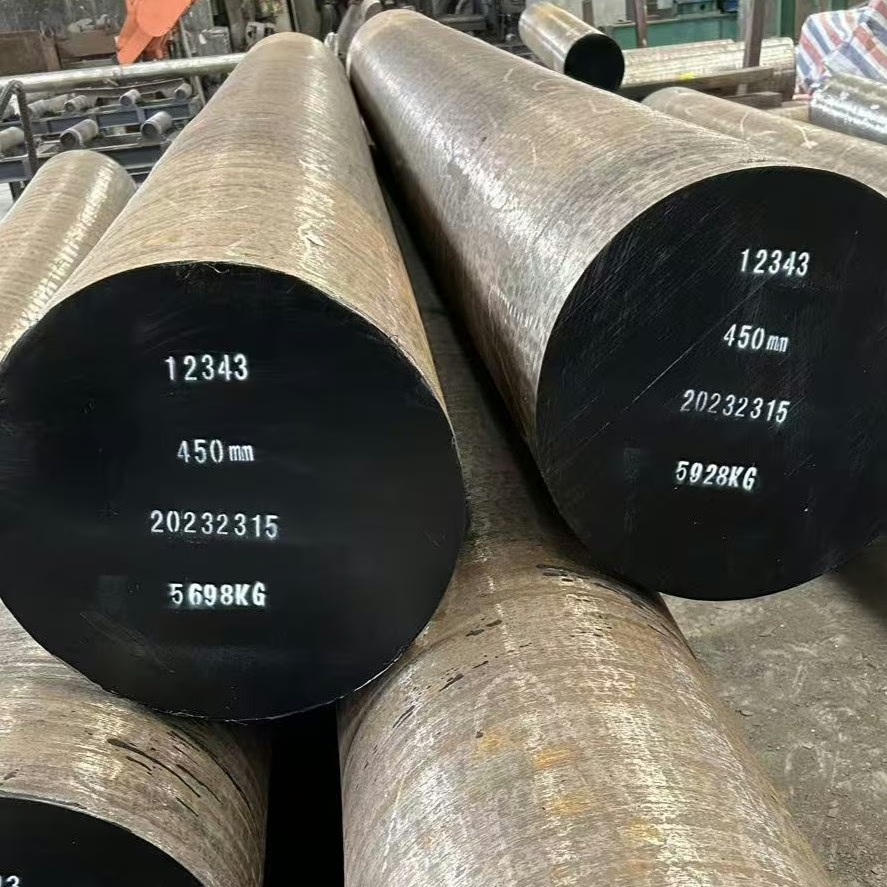
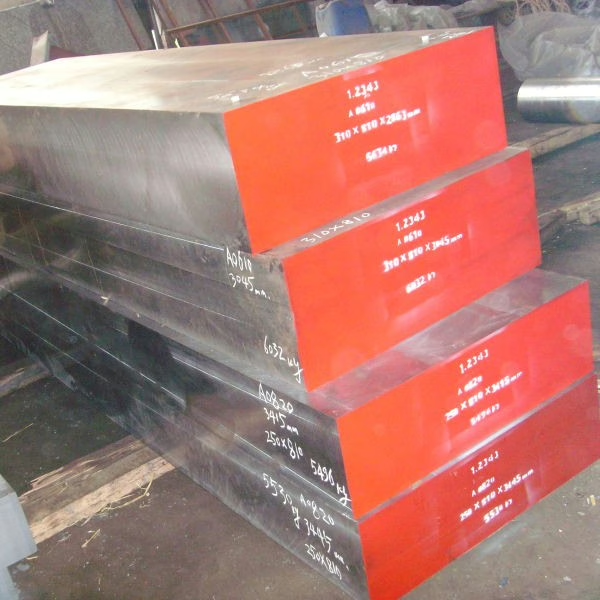
- برينغاس، جي إي (المحرر). (2004). دليل معايير الصلب العالمية المقارنة (الطبعة الثالثة، ص 434). ASTM الدولية. ↩︎
- Murray, G. T. (Ed.). (1997). دليل اختيار المواد للتطبيقات الهندسية. دار نشر سي آر سي. ↩︎
التعليمات
H11 steel is primarily an air-cooling type hot work mold steel, often referred to as DIN 1.2343 or JIS SKD6. It is a chromium-based hot work tool steel highly valued for its exceptional toughness and ability to retain its properties even at elevated temperatures. It is used extensively in the manufacturing of molds.
H11 tool steel is noted for its excellent impact toughness, strong resistance to thermal fatigue (also known as heat checking), and high strength, maintaining these qualities at temperatures approaching 600°C. It also offers good wear resistance, hardenability, plasticity, corrosion resistance, high temperature stability, oxidation resistance, and weldability, making it relatively easy to process.
H11 steel is recognized globally under various designations, including DIN 1.2343 (Germany), JIS SKD6 (Japan), and BH11 (British Standard). In the USA, it aligns with standards like ASTM A681, FED QQ-T-570, SAE J437, SAE J438, SAE J467, and its Unified Numbering System (UNS) designation is T20811.
H11 steel contains less vanadium than H13 steel. This results in H11 having higher toughness and superior resistance to thermal fatigue cracking (better handling of repeated heating and cooling cycles) compared to H13, though it might have slightly less wear and temper resistance.
H11 steel is often chosen when the application demands maximum resistance to cracking and thermal shock, particularly when water cooling is involved in service or under frequent heating and cooling cycles. Its superior toughness and generally easier machinability (due to lower hardness) also make it a favorable choice over H13 for certain projects.
H11 tool steel is frequently used in hot tooling applications that require high resistance to cracking. Key applications include die casting dies (especially for aluminum and magnesium alloys), forging dies, hot punches, hot shear blades, and extrusion tooling. It is also utilized in the aerospace industry for critical structural components, such as aircraft landing gear.
Yes, H11 steel is widely used in the manufacturing of plastic molds, particularly for the insert parts of the mold.
H11 tool steel is commonly available as round bars, sheets, plates, and flat bars. It can also be supplied as slabs, billets, wire, shapes, steel coils, and pipes. Surface conditions vary, including original black, peeled, polished, machined, hot rolled, ground, turned, drawn, or cold rolled.
For hardening, H11 tool steels are generally preheated to 816°C (1500°F) and then directly heated to 1010°C (1850°F), where they are held at that temperature for 15 to 40 minutes. The hardening process is completed by air-quenching, which is effective due to H11’s very high hardenability. Some methods involve oil cooling after quenching from 1000 °C to 1030°C, followed by air cooling.
Tempering of H11 steel is performed at temperatures ranging from 538 to 649°C (1000 to 1200°F) to achieve a Rockwell C hardness between 54 and 38. Double tempering is highly recommended, with each tempering step lasting one hour at the chosen temperature, followed by air cooling.
Yes, H11 tool steels can be welded using conventional methods. However, special procedures are often necessary, including pre-heating and using filler materials that match the base material’s composition. It’s important to note that H11 is susceptible to hydrogen-induced cracking (HIC) due to its high alloy content and hardenability, so precise temperature control (e.g., 310-370°C for hardfacing) during welding is crucial.
Yes, H11 steel exhibits good machinability. Its machinability rate is approximately 75% to 80% compared to 1% carbon steel and about 75% of “W” group tool steels. It is often considered easier to machine than H13 steel because of its lower hardness.
H11 tool steels are typically forged at around 1121°C (2050°F). Forging below 899°C (1650°F) is not recommended. The precise temperature can vary, generally falling within a range of 1000 to 1200°C (1832 to 2192°F), depending on desired deformation properties.
Yes, H11 steel serves as an excellent substrate for PVD coating. For nitriding, a small diffusion zone is preferred, and the formation of compound and oxidized layers should be avoided. H11 is suitable for bath, gas, and plasma nitriding processes and can be nitrided at temperatures of 500-600°C to achieve a hard surface. Studies have also explored TiN coatings on H11 steel.
The hardness of H11 steel post-heat treatment varies with tempering. For general applications, a hardness of 50-54 HRC is common. When air-cooled from 1038°C (1900°F) for 45 minutes, it can reach up to 57 HRC. Tempering within the range of 538-649°C (1000-1200°F) can result in a Rockwell C hardness from 54 down to 38.
Yes, H11 tool steel (specifically DIN 1.2343 / AISI H11) can be produced through additive manufacturing processes, such as Laser Powder Bed Fusion (LPBF). Research indicates that subsequent heat treatments after LPBF can be used to precisely tailor the microstructure and hardness of these additively manufactured steels.
يتم تصنيف H11 عادة عند 60-70% عند مقارنته بفولاذ الأدوات المتصلب بالماء W1 (والذي يعمل كمعيار لقابلية التصنيع 100% لفولاذ الأدوات).
هل تحتاج إلى الفولاذ عالي الأداء H11؟
Get Your Custom Quote from Aobo Steel’s Experts Today!
مع أكثر من 20 عامًا من الخبرة المتخصصة في التشكيل, Aobo Steel is your trusted source for premium H11 tool steel. We deliver durable, high-performance materials precisely tailored to your application’s demands. Our dedicated specialists are here to provide expert advice and ensure you get the perfect H11 solution.
هل أنت مستعد لتعزيز مشروعك باستخدام أداة الفولاذ H11 المتفوقة؟ فقط قم بملء النموذج أدناه to connect with our team. We’ll provide a personalized quote and answer all your questions.
استكشف منتجاتنا الأخرى
D2/1.2379/1.2379/SKD11
D3/1.2080/1.2080/SKD1
D6/1.2436/SKD2
A2/1.23663/1/SKD12
O1/1.2510/1.2510/SKS3
O2/1.2842
S1/1.2550
S7/1.2355
DC53
H13/1.2344/1.2344/SKD61
H11/1.2343/1.2343/SKD6
H21/1.2581/SKD7
L6/1.2714/SKT4
م2/1.3343/1.3343/سخ 51
M35/1.3243/1.3243/SK55
M42/1.3247/1.3247/SK59
P20/1.2311
P20+Ni/1.2738
420/1.2083/2Cr13
422 الفولاذ المقاوم للصدأ
محمل فولاذي 52100
الفولاذ المقاوم للصدأ 440C
4140/42CrMo4/SCM440
4340/34CrNiMo6/1.6582
4130
5140/42Cr4/SCR440
SCM415