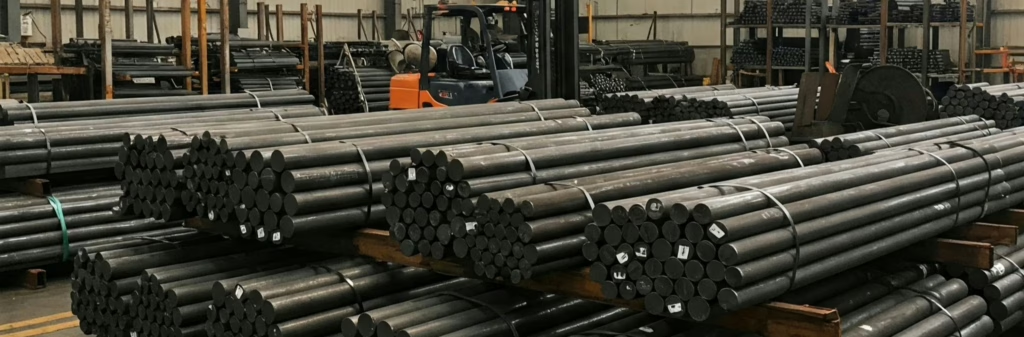
52100 Bearing Steel | 1.3505 | 100Cr6
AOBO STEEL – Trusted Global Tool Steel Supplier
52100 bearing steel is a low-alloy steel grade primarily recognized as the classic standard for rolling bearing applications. Due to its high carbon content and chromium addition, its performance characteristics, particularly hardness, wear resistance, and fatigue strength, serve as a benchmark for evaluating other bearing steels. This demonstrates its proven reliability in demanding industrial components.
1. 52100 Composition
The following weight percentages generally characterize the typical chemical composition for AISI/SAE 52100 steel:
- Carbon (C): 0.95% ~ 1.10%
- Chromium (Cr): 1.40% ~ 1.65%
- Manganese (Mn): 0.30% ~ 0.50%
- Silicon (Si): 0.22% ~ 0.35%
- Phosphorus (P): ≤0.030%
- Sulfur (S): ≤0.030%,
It’s worth noting that while AISI/SAE 52100 is the common designation in the US, it’s considered equivalent to the European grade 100Cr6. A steel similar to SAE 52100, designated 100 Cr Mn 6, has increased levels of manganese (1.10-1.20%) and silicon (0.55-0.70%).
2. Properties of 52100 Bearing Steel
This section details the critical characteristics of AISI/SAE 52100 steel that make it a preferred material in numerous industries.
Hardness Potential and Heat Treatment Response
One of the standout 52100 bearing steel properties is its exceptional hardness capability.
- Achievable Hardness: With appropriate heat treatment, 52100 steel consistently achieves a hardness of 60 to 64 HRC throughout its section. For example, a 1-inch-thick piece can reach approximately 60 HRC when tempered around 204°C (400°F).
- Bearing Applications: For critical ball bearing components, a minimum hardness of 62 HRC is typically specified and achieved after hardening and tempering.
- Hot Hardness: It’s important to consider that the hot hardness of 52100 steel decreases notably as operating temperatures rise.
2.1 Microstructure Characteristics
The microstructure of 52100 steel after correct heat treatment is fundamental to its performance:
- Typical Structure: It primarily consists of high-carbon martensite with finely dispersed primary (undissolved) spherical carbides. A retained austenite content of 5 to 10% is also typical.
- Wear Resistance Contribution: For bearing applications, 52100 steel is intentionally austenitized below its Acm temperature. This process encourages the formation of cementite carbide arrays within the final martensitic structure, significantly enhancing wear resistance.
- Cleanliness: A clean microstructure, free from excessive inclusions, is vital, especially for applications requiring highly polished surfaces, such as dies.
2.2 Core Mechanical Strengths of 52100 Steel
52100 alloy steel is engineered for high load-bearing capacity and resilience.
Mechanical Property | Typical Value / Characteristic for 52100 Steel | Notes |
Classification | High-carbon, chromium, low-alloy, through-hardening | Standard for bearing applications |
Achievable Hardness | 60-64 HRC | Min. 62 HRC for hardened ball bearings |
Tensile Strength (Hot Rolled) | 930 MPa (135 ksi) | As-supplied condition |
Yield Strength (Hot Rolled) | 570 MPa (83 ksi) | As-supplied condition |
Tensile Strength (Oil Quenched, Not Drawn) | 1515 MPa (220 ksi) | Illustrates hardening potential |
Yield Strength (Oil Quenched, Not Drawn) | 965 MPa (140 ksi) | Illustrates hardening potential |
Bending Strength | Approx. 2400 MPa (240 kgf/mm²) | Recommended for ball bearing applications |
Elastic Modulus (Young’s) | Approx. 210 GPa | Stiffness of the material |
2.3 Fatigue Performance
High fatigue life is a critical property of 52100 bearing steel, especially for components like journal bearings subjected to cyclic loading. The fatigue resistance can be influenced by factors such as inclusion content and the precision of heat treatment. Quality control, including fatigue testing, is paramount.
2.4 Wear Resistance
52100 steel demonstrates good wear resistance. This is significantly enhanced by the presence of very small, hard cementite particles that are uniformly distributed within the microstructure after optimal heat treatment. Specialized treatments, like duplex processes, can further improve wear characteristics compared to standard chromizing or other alloy steels like 8620 in certain conditions.
2.5 Hardenability
Thanks to its chromium content, 52100 steel possesses good hardenability. This allows it to achieve consistent hardness through its cross-section in parts up to approximately 1 inch thick. Its hardenability is comparable to that of 5280 steel.
2.6 Machinability
For the best machining outcomes and to ensure a uniform response during subsequent hardening processes, a spheroidized microstructure is highly recommended for 52100 steel. This condition improves tool life and surface finish.
2.7 Material Cleanliness and Quality
High-quality 52100 bearing steel is produced with a strong emphasis on internal soundness, cleanliness, and uniform chemical composition.
- Inclusion Control: For critical applications like ball bearings, very low levels of non-metallic inclusions (e.g., Type A, B, C, D) and minimal oxygen content are essential.
- Melting Processes: Advanced melting techniques such as consumable-electrode vacuum melting (CEVM) or electroslag remelting (ESR) can provide the exceptionally clean microstructure required for demanding applications like polished dies.
- Casting Considerations: When producing 52100 steel via modern continuous casting, insufficient homogenizing cycles can lead to segregation and undesirable carbide distributions, negatively impacting its properties and heat treatment response.
- Standards: ASTM A 535 covers special quality alloy steel billets, bars, tube rounds, rods, and tubes intended for manufacturing antifriction bearings.
2.8 Dimensional Stability
Achieving very high dimensional stability in 52100 steel components requires precise control over heat treatment. It can be sensitive to distortion, and tempering to a lower hardness might be necessary compared to some advanced steels if ultimate stability is the primary goal. Incorrect austenitizing temperatures or tempering practices can lead to cracking.
2.9Weldability
It is important to note that 52100 bearing steel is generally considered nonweldable due to its high carbon content, which makes it prone to cracking during and after welding.
2.10 Toughness
When correctly oil quenched from around 850°C (1560°F) to achieve a microstructure of dispersed spherical carbides in tempered martensite, 52100 steel exhibits good toughness. This can be assessed using standard tests like Charpy V-notch impact energy and plane-strain fracture toughness (KIc). Studies have shown that 52100 bainite can offer higher impact toughness compared to some powder-forged steels.
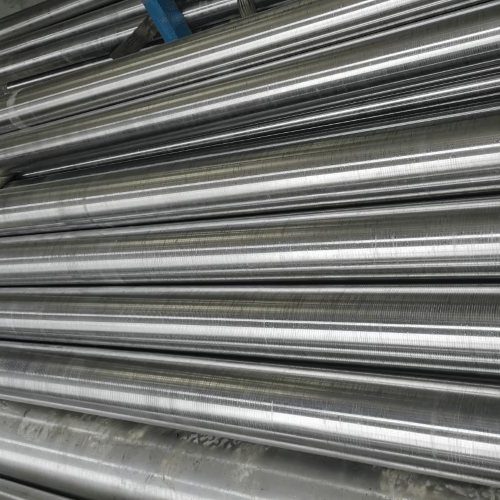
Are you looking for 52100 bearing steel? Please fill out the following form to contact us now!
3. Heat Treatment
52100 steel is a prominent bearing steel, valued for achieving high hardness. This hardness is primarily developed through the formation of martensite in its microstructure, a result of precise 52100 steel heat treatment. Understanding these thermal processes is key to optimizing your 52100 steel components.
3.1 Hardening 52100 Steel: Austenitizing and Quenching
To achieve the required high hardness and desired microstructure in 52100 steel, a critical two-step hardening process is employed: austenitizing followed by quenching.
3.1.1 Austenitizing
The austenitizing stage involves heating the 52100 steel to transform its structure. For optimal results, the austenitizing temperature for 52100 steel should be meticulously controlled, ideally around 855 +/- 5°C. Using temperatures such as 840°C or 850°C before quenching is also noted. It is important to avoid heating 52100 steel above this specific range (overheating), as this can lead to excessive retained austenite and an increased risk of cracking upon quenching.
3.1.2 Quenching
Following austenitizing, 52100 steel is rapidly cooled (quenched). Common quenching media for 52100 steel include:
- Oil
- Salt Bath
Martempering is another technique used for 52100 steel. This typically involves quenching in a hot salt bath, followed by cooling in still air, a method chosen to minimize distortion.
3.2 Tempering 52100 Steel
After the hardening process, tempering is a crucial step in the 52100 steel heat treatment cycle. Tempering is performed at temperatures below the steel’s Ac1 (lower critical) point. Its main purposes are to enhance toughness and relieve internal stresses within the 52100 steel.
Tempering Temperatures and Resulting Hardness
The choice of tempering temperature directly influences the final properties of 52100 steel.
Tempering Temperature for 52100 Steel | Typical Resulting Hardness (HRC) | Notes for 52100 Steel Applications |
220°C or 240°C | Approx. 60-60.5 HRC | For good dimensional stability in 52100 steel, especially for bearing applications (SO or S1 conditions). |
180°C or 190°C | Varies | Also a common tempering range for 52100 steel. |
150°C – 200°C | Varies | The toughness of 52100 steel is generally low when tempered in this range. |
A double temper is often employed for 52100 steel, sometimes with an intermediate subzero (cryogenic) treatment. This helps ensure that any retained austenite is transformed and that stresses are effectively relieved.
3.3. Annealing 52100 Steel (Softening)
When 52100 steel needs to be softened, for instance, before machining, annealing is the appropriate 52100 steel heat treatment.
Annealing Processes and Outcomes for 52100 Steel
Annealing Process for 52100 Steel | Target Hardness (HB) | Resulting Microstructure in 52100 Steel | Primary Benefit for 52100 Steel |
Standard Annealing | Approx. 198 HB | Mainly lamellar pearlite | General softening. |
Optimized / Spheroidize Annealing | 180-190 HB | Spheroidized structure (globular carbides in ferrite) | Improved machinability of 52100 steel. |
Spheroidizing, achieved through controlled cooling rates during annealing, produces globular carbides in a ferrite matrix, which significantly enhances the machinability of 52100 steel.
5. Surface Treatment of 52100 Steel
To further enhance surface hardness and wear resistance, various surface treatments can be applied to 52100 steel components.
- Chromizing: A surface treatment for 52100 steel.
- Duplex Treatment (Chromizing + Plasma Nitriding): This combination can offer better wear resistance for 52100 steel compared to chromizing alone.
- Induction Hardening: This method is used to achieve high surface hardness on 52100 steel. For example, it has been demonstrated to reach 61-63 HRC on 52100 steel shafts.
Careful control of all 52100 steel heat treatment stages, especially austenitizing and tempering, is essential for achieving the desired balance of hardness, toughness, and dimensional stability in your final 52100 steel components.
4. Applications
Primarily, 52100 steel is used for manufacturing ball bearings and is a classic grade for rolling bearing steel. Its critical role in high-performance bearing components is further highlighted by its specification in ASTM A295 (for hot-rolled alloy steel bars for anti-friction bearings) and ASTM A535 (for special quality ball and roller bearing steel).
After heat treatment, 52100 steel is well-suited for applications demanding:
- High load-bearing capacity
- Excellent wear resistance
- Long fatigue life
Consequently, it is successfully applied in electric motors, gearboxes, gas turbine aeroengine main shafts, helicopter transmissions, and steel rolling mill support bearings. These varied 52100 steel applications demonstrate its versatility.
Beyond bearings, its uses extend to specialized manufacturing processes. For instance, it is employed as a cladding material in plasma transferred arc (PTA) powder deposition welding. A 52100 steel layer cladding a substrate like AISI 1022M provides significant resistance to wear and fatigue, with the critical area for fatigue life designed within this cladding.
Furthermore, its properties make 52100 steel valuable for certain tool steel applications. Categorized as a semi-high-speed steel, it can achieve hardness in the 62–64 HRC range. While its tempering and wear resistance may be lower than some true high-speed steels, it is used for some cold work tools or mechanical components. For dies up to 50 mm (2 inches) in diameter, consumable-electrode vacuum-melted or electroslag remelted 52100 steel is utilized. Heat-treated to 59-61 HRC, this material provides optimum die life and is suitable for photochemical etching to create polished, low-relief die surfaces.
5. AISI 52100 Equivalent Standards
- AISI/SAE: 52100
- China(GB): GCr15
- UNS: G52986
- DIN (W-Nr): 3505 (also known as 100Cr6)
- JIS: SUJ2
- AMS: AMS 6490, AMS 6491 (Premium Aircraft Quality Bearing Steel)
- ASTM: A295 (Standard Specification for High-Carbon Anti-Friction Bearing Steel)
6. Supply forms and dimensions
The 52100 bearing steel we supply is available in various forms, including round bars, sheet plates, slabs, flat bars, square bars, and blocks. The dimensions of the flat bar range from: width 20–600 mm × thickness 20–400 mm × length 1,000–5,500 mm. The dimensions of the round bar range from a diameter of 20–400 mm × a length of 1,000–5,500 mm. The block dimensions are obtained by cutting the flat bar.
UT testing: Sep 1921-84 D/d, E/e.
Surface Treatment: original black, peeled, machined/turned, polished, grounded, or milled surface finishes.
Delivery time: 30-45 days.
FAQ
1. What is 52100 steel?
52100 alloy steel is a bearing steel characterized as a high-carbon, chromium alloy steel.
2. What are the key properties of 52100 steel?
Key properties of 52100 steel include high hardness (up to 66 Rockwell C when properly heat-treated) and excellent wear resistance. It also possesses robust strength and durability, and maintains good dimensional stability. While it has good corrosion resistance due to its chromium content, it is also noted for being quite brittle compared to other steel grades, sacrificing some malleability and resistance to impact forces.
3. Does 52100 steel resist corrosion, or does it rust?
52100 steel has excellent corrosion resistance because of its high chromium content. However, it is not stainless steel and is less corrosion-resistant than other types, such as 440C stainless steel.
4. What is the maximum hardness that 52100 steel can achieve?
When properly heat-treated, 52100 steel can achieve remarkably high hardness values, up to 66 Rockwell C (HRC).
5. Is 52100 steel magnetic?
Yes, 52100 steel is magnetic at room temperature.
6. What are the pros and cons of 52100 steel?
- Pros: It becomes very hard with heat treatment, is super resistant to wear and fatigue, maintains its shape well under tough conditions, and can be great for machining after proper heat treatment.
- Cons: It’s less corrosion-resistant than true stainless steels, welding can be tricky, it’s more brittle than some other steels, can be slightly more expensive, and is difficult to machine in its fully hardened state.
7. What are the common applications for 52100 steel?
52100 alloy steel is primarily used for components that experience punishing conditions and require minimal deformation during operation. Common applications include severe-duty bearings (ball and roller bearings), bushings, cams, shafts, and other high-load, high-wear components. It is also found in demanding industrial settings such as aircraft engines, machine tooling, and offshore equipment, as well as in automotive and aircraft components.
8. Is 52100 steel good for knives?
Yes, 52100 steel is considered a very good steel for knives, especially when in the hands of a skilled blacksmith and properly heat-treated. It is capable of taking a very sharp edge, offers high hardness, and provides excellent edge stability and ease of sharpening when treated well. However, poor heat treatment can lead to issues such as gumminess during sharpening and only ordinary edge retention.
9. Can 52100 steel be used for tooling?
Yes, 52100 steel is an excellent choice for various tooling applications due to its high hardness and wear resistance. Specific examples include punches, taps, dies, mill rolls, as well as general tooling, knives, chisels, hotcuts, and wood turning chisels.
10. How do you heat treat 52100 steel for optimal performance?
Optimal heat treatment for 52100 steel involves specific steps to maximize hardness and toughness. This typically includes annealing (often a Divorced Eutectoid Transformation or DET anneal with multiple heating and air cooling cycles), followed by hardening (austenitizing) at temperatures between 1475°F and 1525°F for 10-30 minutes. An immediate quench after austenitizing is crucial, followed by tempering at 300-500°F, often with multiple cycles, to balance hardness, toughness, and ductility. Higher austenitizing temperatures can increase hardness but also retain austenite.
11. What is the recommended annealing process for 52100 steel?
A common method is Divorced Eutectoid Transformation (DET) annealing to refine grain size. This involves heating to 1700°F (927°C) for 20 minutes, then air cooling until black and magnetic. This is followed by reheating to 1460°F (793°C) for 30 minutes, then air cooling (and optionally repeating this step). Finally, the steel is allowed to cool in the furnace to 1250°F slowly (677°C), then cooled in ambient air. This process helps reduce internal stresses and refines the steel’s microstructure.
12. What type of quenching medium is recommended for 52100 steel?
For 52100 steel, a medium- or fast-quenching oil is recommended. Oils in the 11 to 14-second range are generally very effective. Using a faster oil like Parks #50 (7 to 10-second) is often cautioned against for alloy steels with chromium, as it can increase the risk of cracking. Water cooling is generally not recommended due to the steel’s corrosion resistance.
13. Is 52100 steel difficult to forge or machine?
52100 steel can be very difficult to forge, requiring slow movement and high temperatures to avoid stress fractures. However, its medium-low hardenability and lack of carbides at forging temperatures make it more manageable for forging compared to air-hardening steels. In its fully hardened state, 52100 is difficult to machine, often necessitating specialized tools like carbide or cubic boron nitride (CBN) tooling. Its machinability can be improved by spheroidizing annealing before machining.
14. How does forging affect 52100 steel performance for knives?
Forging can lead to greater performance potential in 52100 steel. Forging at specific low temperatures, around 1625°F (885°C), can avoid carbon loss and grain growth while still improving the steel. This process, along with thermal cycling (normalizing), helps to dissolve carbides and refine the grain size, leading to improved wear resistance and overall performance.
15. Can 52100 steel be cold worked?
Yes, AISI 52100 alloy steel can be cold worked using conventional techniques when it is in the annealed or normalized conditions.
16. How does 52100 steel compare to O1 steel for knives?
52100 steel contains approximately three times the chromium content of O1 tool steel. While O1 has tungsten carbides, 52100 is noted for achieving a homogeneous and very fine-grained structure due to its manufacturing care, often involving vacuum melting. O1 is generally considered easier to heat treat than 52100, and 52100 is more difficult to forge and heat treat properly. However, many experts assert that when everything is done right (especially extensive forging and specific heat treatment), 52100 yields superior knife performance.
17. How does 52100 steel compare to 440C stainless steel for corrosion resistance?
440C stainless steel resists corrosion twice as well as conventional 52100 steel. 440C performs better in terms of fatigue life and under lubrication-free operating conditions.
18. What is the edge retention of 52100 steel compared to other steels like AEB-L or Japanese steels?
52100 steel’s edge retention is generally not particularly high compared to some advanced steels, being similar to other carbon and low alloy steels because of the volume and hardness of its cementite carbides. In tests, 52100 demonstrated superior edge retention to 1086 and Wootz damascus, but was not as good as AEB-L. Compared to Japanese steels, some users suggest that modern steels like Apex Ultra can offer significantly higher edge retention due to additional alloying elements.
19. Can 52100 steel be used in Damascus or San Mai knife constructions?
Yes, 52100 steel can be effectively used as a core steel in San Mai blades, particularly if a heat treatment oven is available, as it is a deep hardening steel. It has also been incorporated into Damascus steel alongside materials like 1095, though achieving a strong visual contrast can be difficult due to their similar compositions.
20. What is 52100 steel good for?
- Rolling bearings. It is considered a classic and standard material for high-carbon bearing applications, specifically ball and roller bearings.
- Die sections. It can be used for dies up to 50 mm in diameter that require critically polished surfaces.
- Cladding material in Powder Transfer Arc (PTA) welding.
- Applications requiring good wear resistance without carburizing.
21. What is the strength of 52100 steel?
The strength of 52100 steel is highly dependent on the specific heat treatment applied.
- Tensile Strength: 585-620 MPa (85-90 ksi). After oil quenching from 850 °C (1560 °F), tensile strength varies with tempering temperature. For die applications, tensile strength is listed as 80,000 psi (552 MPa) in the annealed condition and 120,000 psi (827 MPa) when oil-quenched and tempered at 400°F (204°C).
- Yield Strength: 450 MPa (65 ksi). After oil quenching from 850 °C (1560 °F), the yield strength varies with tempering temperature. For die applications, yield strength is listed as 35,000 psi (241 MPa) in the annealed condition and 93,000 psi (641 MPa) when oil-quenched and tempered at 400°F (204°C).
- Compressive Strength: 2760 MPa (400 ksi) or 2930 MPa (425 ksi).
22. What is the difference between 52100 and 1095 steel?
Main Differences Summarized:
- Chromium Content: 52100 contains chromium, while 1095 is a plain high-carbon steel with no significant chromium.
- Primary Applications: 52100 is mainly a bearing steel, whereas 1095 is a more general-purpose high-carbon steel often used for springs and blades.
- Corrosion Resistance: 52100 offers slightly better corrosion resistance than plain carbon 1095, although neither is considered a corrosion-resistant steel.
Get a Competitive Quote for 52100 Bearing Steel
With over 20 years of forging expertise, Aobo Steel is your trusted partner for high-performance 52100 bearing steel. We provide not just materials, but solutions. Leverage our deep industry knowledge and reliable supply chain for your project’s success.
✉ Contact us by filling out the form below.
Explore Our Other Products
D2/1.2379/SKD11
D3/1.2080/SKD1
D6/1.2436/SKD2
A2/1.23663/SKD12
O1/1.2510/SKS3
O2/1.2842
S1/1.2550
S7/1.2355
DC53
H13/1.2344/SKD61
H11/1.2343/SKD6
H21/1.2581/SKD7
L6/1.2714/SKT4
M2/1.3343/SKH51
M35/1.3243/SKH55
M42/1.3247/SKH59
P20/1.2311
P20+Ni/1.2738
420/1.2083/2Cr13
422 stainless steel
52100 bearing steel
440C stainless steel
4140/42CrMo4/SCM440
4340/34CrNiMo6/1.6582
4130
5140/42Cr4/SCR440
SCM415