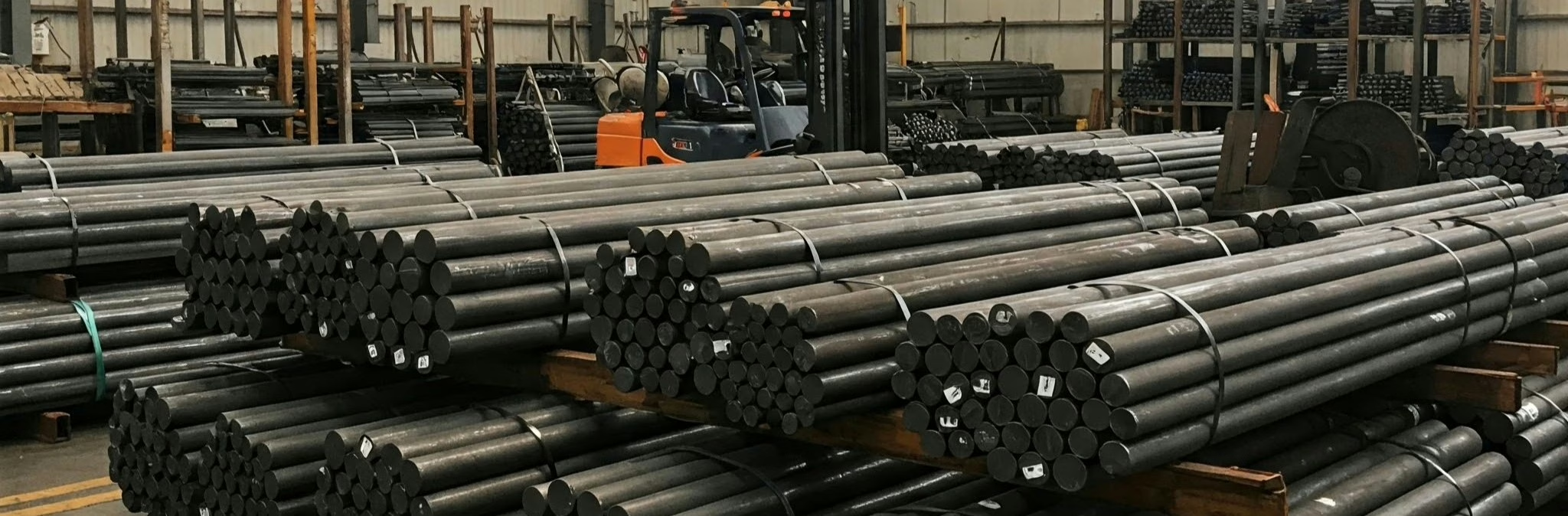
440C STAINLESS STEEL | 1.4125 | SUS440C
AOBO STEEL – Trusted Global Tool Steel Supplier
440C stainless steel is a high-carbon, high-chromium martensitic stainless steel. It belongs to the 400 series of stainless steels, which are generally magnetic. In the medical field, 440C steel is widely used for manufacturing surgical knives and other medical instruments. It is also used in the industrial field to manufacture corrosion-resistant plastic and rubber molds.
1. Applications
- Cutting Tools
- Bearings
- Plastic Mold Materials
- Valve Parts
- Gears, Shafts, Cams
- Surgical and Dental Instruments
- Springs
- Medical Applications
- Wear-Resistant Applications
- Automotive Industry
- Hardware
2. 440C Stainless Steel Composition1
Carbon (C) | Chromium (Cr) | Manganese (Mn) | Silicon (Si) | Molybdenum (Mo) | Phosphorus (P) | Sulfur (S) |
0.95 – 1.20 | 16.0 – 18.0 | 1.00 max | 1.00 max | 0.75 max | 0.040 max | 0.030 max |
3. 440C Stainless Steel Properties
3.1 Hardness
440C stainless steel can achieve the highest hardness among the 440 series stainless steels. 440C hardness is 59 HRC. It can be hardened to 60 HRC when tempered at 300°F (150°C). Stainless steel 440C has different hardness after different annealing processes. For example, an annealed bar can have a Rockwell hardness of B-95. Wrought bar, hot finished and annealed, has a hardness of 269 HB. Wrought bar, cold finished and annealed, has a hardness of 285 HB. Wire in the annealed condition has a hardness of B97 HRB.
3.2 Tensile Properties
- Annealed: 110 ksi (758 MPa), with a minimum of 110 ksi (758 MPa) for bar.
- Heat Treated/Hardened: 285 ksi (1965 MPa).
- Cold Finished Bar: Minimum 125 ksi (862 MPa).
- Annealed Wire: Minimum 140 ksi (965 MPa).
- Cold Heading Wire: Typical 110 ksi (760 MPa).
- Lightly Drafted Wire: Typical 120 ksi (830 MPa).
- MIM(Metal Injection Molded) 440C after heat treatment: 876 MPa2.
3.3 Yield Strength (0.2% Offset)
- Annealed: 65 ksi (448 MPa), with a minimum of 65 ksi (448 MPa) for bar.
- Heat Treated/Hardened: 275 ksi (1896 MPa).
- Cold Finished Bar: Minimum 100 ksi (689 MPa).
3.4 Elongation in 2 inches (50 mm)
- Annealed: 14%, with a minimum of 14% for bar.
- Heat Treated/Hardened: 2%.
- Cold Finished Bar: Minimum 7%.
- Annealed Wire: Minimum 13%.
3.5 Toughness(Heat Treated): 5ft-lb.
3.6 Modulus of Elasticity: 29 x 10^6 psi (approximately 200 GPa).
3.7 Specific Heat (32-212°F): 0.11 Btu/lb °F.
3.8 Density: Approximately 0.29 lb/in.^3 (8.02 g/cm^3) for stainless steels generally.
3.9 Thermal Conductivity (20°C): 29.3 W/(m·K).
3.10 Coefficient of Linear Thermal Expansion: Approximately 10.5 x 10^-6 K^-1 (over ranges like 20-100°C, 20-200°C, 20-300°C, 20-500°C)3.
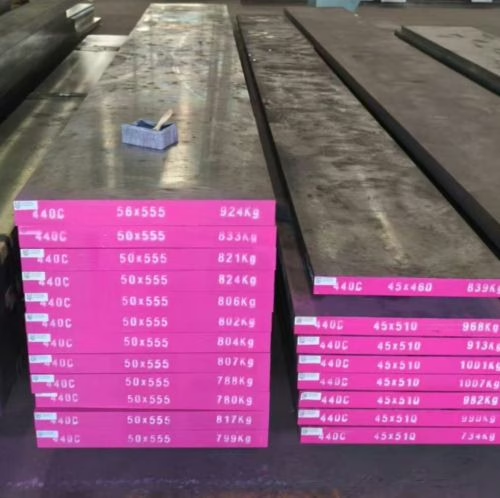
Interested in 440C stainless steel?
Please fill out the form below to contact us today!
4. Heat treatment
The heat treating of 440C stainless steel, like other martensitic stainless steels, typically involves austenitizing, quenching, and tempering. The process aims to transform the steel into a martensitic microstructure, which is then tempered to optimize its balance of hardness, strength, ductility, and corrosion resistance.
4.1 Austenitizing(hardening)
The austenitizing temperature is 925 to 1065 °C (1700 to 1950 °F). We recommend a temperature of 1038°C (1900°F), as we believe this temperature will provide the best hardness and corrosion resistance. Additionally, we suggest preheating the material to 650°C (1200°F) before this step to minimize distortion, warping, or cracking from high thermal gradients during rapid heating or quenching. Soaking time should be sufficient to ensure carbides dissolve into the austenite, which can be slower than in plain carbon steels due to the presence of chromium.
4.2 Quenching
Following austenitizing, 440C steel is typically quenched in air or oil. Oil quenching from temperatures like 1038°C (1900°F) or 1040°C (1900°F) is a common choice. After quenching, the steel transforms into martensite, a hard yet brittle structure.
4.3 Tempering
The step following quenching is tempering, which aims to reduce hardness, enhance toughness and ductility, and relieve internal stress.
The tempering temperature is 392°F to 662°F (200°C to 350°C). Different tempering temperatures result in varying hardness levels, as follows:
Temperature (°C) | Temperature (°F) | Hardness (HRC) |
150 | 300 | 60 |
315 | 600 | 57 |
425 | 800 | 58 |
480 | 900 | 57 |
540 | 1000 | 55 |
It should be noted that tempering 440C stainless steel and similar high-carbon martensitic stainless steels in the range of 427 °C to 566 °C (800 °F to 1050 °F) will result in temper brittleness and a decrease in impact strength and corrosion resistance.
If tempering outside the aforementioned temperature range is necessary to enhance toughness, we recommend a tempering temperature of 593°C (1100°F) or higher. Tempering at this temperature improves impact strength and corrosion resistance but sacrifices some hardness.
4.4 Special Considerations in 440C Steel Heat Treatment
- Preheating: Before the main hardening(austenitizing) process, we suggest preheating 440C stainless steel to approximately 650°C (1200°F). This helps to ensure a more uniform temperature distribution and minimize thermal shock during the subsequent austenitizing stage.
- Slow Cooling After Forging: For high-carbon steels such as 440C, we recommend slow cooling after forging, or intermittent cooling, which involves cooling to 150-250°C, reheating to approximately 650°C, and then final cooling. This helps prevent cracking and the formation of grain boundary carbides.
- Managing Retained Austenite: As-quenched 440C steel can sometimes contain a significant amount of retained austenite (potentially 20-30% by volume). If not addressed, this retained austenite can transform spontaneously over time, leading to dimensional changes and an increased risk of cracking. Performing a subzero cold treatment after quenching can effectively transform this retained austenite into untempered martensite. This cold treatment must be followed by at least one standard tempering cycle to temper the newly formed martensite and relieve internal stresses.
- Post-Weld Heat Treatment (PWHT): For welded 440C material components, PWHT is almost always a necessary step. This treatment serves to temper the martensite formed in the weld and heat-affected zone, as well as to relieve residual stresses. The PWHT temperature range for 440C is 480°C to 750°C (895°F to 1380°F).
5. Equivalent Grades
- DIN EN (Europe): 1.4125 (X105CrMo17)
- JIS (Japan): SUS440C
- ISO: X105CrMo17
- GB (China): 9Cr18Mo or 95Cr18
6. Compare 440C with other steels
6.1 440C vs. D2
D2 tool steel is characterized by excellent wear resistance, dimensional stability, and high hardness in cold-working tool applications, but it is difficult to machine and weld, and has limited toughness.
Characteristic | 440C Stainless Steel | D2 Tool Steel |
Classification | Martensitic stainless steel | High-carbon, high-chromium cold work tool steel |
Primary Feature | Corrosion Resistance | Wear Resistance & Dimensional Stability |
Hardness | 59-62 HRC | 58-62 HRC |
Wear Resistance | Good | Excellent |
Toughness | Poor; generally considered brittle due to large primary carbide particles. | Fair to Low; not recommended for applications requiring high shock resistance. |
Corrosion Resistance | Excellent; designed to resist air, fresh water, chemicals, and food acids without plating. | Limited; has appreciable resistance to staining when polished, but is not a true stainless steel as most chromium forms carbides. |
Machinability | Difficult to etch/reveal microstructure due to high chemical resistance. | Difficult to work and grind. It is often considered “nonweldable” by conventional means. |
Dimensional Stability | Good. | Excellent; known for minimum distortion during heat treatment. |
Typical Applications | Fine knives, surgical tools, ball bearings, races, injection molds for corrosive materials. | Long-run dies, piercing punches, trimming tools, mass-production blanking of metals. |
2. 440C vs. 1095
1095 is a high-carbon steel that can be hardened for strength and is commonly used for springs and applications where corrosion resistance is not a primary factor.
Feature | 440C Stainless Steel | 1095 Steel |
Classification | Martensitic Stainless Steel | High-Carbon Steel / Spring Steel |
Corrosion Resistance | Good | Poor |
Hardness | Very High. Can be heat-treated to achieve up to 60 HRC, offering excellent hardness and wear resistance. | High. Can also be hardened to ~60 HRC, but its hardenability is generally lower than alloy steels like 440C. |
Edge Retention | Excellent | Good. Known for taking a very fine edge, but may not retain it as long as 440C under heavy use. |
Toughness | Moderate. Can be somewhat brittle at very high hardness levels. | Good. Generally considered tougher than 440C, especially when tempered for spring applications. |
Primary Applications | Cutting tools, knife blades, surgical instruments, ball bearings, and races. | Springs, knives, and other tools where toughness is critical and corrosion is not a major concern. |
Key Advantage | Superior corrosion resistance and wear resistance. | Good toughness and ease of sharpening. |
3. 440C stainless steel vs. 316
316 stainless steel is a chromium-nickel grade classified as an austenitic stainless steel. Austenitic stainless steels are typically non-magnetic.
Feature | 440C Stainless Steel | 316 Stainless Steel |
Steel Type | Martensitic | Austenitic |
Key Characteristic | High Hardness & Wear Resistance | Superior Corrosion Resistance |
Hardness | Very high (can reach up to 60 HRC) | Softer and more ductile |
Corrosion Resistance | Good, but less resistant than 316, especially to chlorides | Excellent, particularly resistant to chlorides (“marine grade”) |
Magnetic Properties | Ferromagnetic (magnetic) | Generally non-magnetic |
Weldability | Not generally recommended for welding | Good, especially the 316L low-carbon version |
Key Alloying Elements | High Carbon (0.95-1.20%), High Chromium (16-18%) | Molybdenum (2-3%), Nickel (10-14%), Low Carbon (<0.08%) |
Common Applications | Ball bearings, races, high-quality knives, surgical instruments, cutting tools | Marine hardware, food processing equipment, chemical processing, nuclear reprocessing plants |
- Bringas, J. E. (Ed.). (2004). Handbook of Comparative World Steel Standards (3rd ed). ASTM International. ↩︎
- Beswick, J. M. (Ed.). (2002). Bearing Steel Technology. ASTM International. ↩︎
- Schweitzer, P. A. (2001). Metallic Materials: Physical, Mechanical, and Corrosion Properties. Marcel Dekker. ↩︎
FAQs
No, 440C is an American designation (AISI/ASTM).
Choose D2 for maximum abrasive wear resistance where corrosion is minor or the environment is mild (e.g., cold-work tooling, long-run dies). D2 offers superior wear resistance and dimensional stability for such applications.
Choose 440C for a balance of good wear resistance and significant corrosion resistance (e.g., molds, cutlery, and bearings in moist or mildly chemical environments).
Yes, it’s a combination of hardness, wear resistance, and corrosion resistance that makes 440C a very suitable and popular material for many knives.
Yes, 440C steel is well-regarded for its ability to hold an edge. It is explicitly stated to have the “best edge retention” among the 440 series and is commonly used for cutting tools, including fine custom knives and surgical instruments.
440C is a type of martensitic stainless steel that is designed to have corrosion resistance.
Yes, 440C stainless steel is magnetic.
Need High-Quality 440C Stainless Steel?
Get a fast, competitive quote from the experts at Aobo Steel. With over 20 years of experience, we deliver premium 440C stainless steel tailored to your exact specifications. Our knowledgeable team is ready to assist you.
Simply fill out the form below to discuss your requirements or request your no-obligation quote. We’ll respond promptly!
Explore Our Other Products
D2/1.2379/SKD11
D3/1.2080/SKD1
D6/1.2436/SKD2
A2/1.23663/SKD12
O1/1.2510/SKS3
O2/1.2842
S1/1.2550
S7/1.2355
DC53
H13/1.2344/SKD61
H11/1.2343/SKD6
H21/1.2581/SKD7
L6/1.2714/SKT4
M2/1.3343/SKH51
M35/1.3243/SKH55
M42/1.3247/SKH59
P20/1.2311
P20+Ni/1.2738
420/1.2083/2Cr13
422 stainless steel
52100 bearing steel
440C stainless steel
4140/42CrMo4/SCM440
4340/34CrNiMo6/1.6582
4130
5140/42Cr4/SCR440
SCM415