M2 tool steel hardness stands out in high-speed cutting and forming applications. M2 high-speed tool steel is a molybdenum-type general-purpose grade widely recognized for its balanced properties. Hardness, the material’s ability to resist penetration and withstand abrasion, is a primary factor dictating performance in demanding industrial environments.
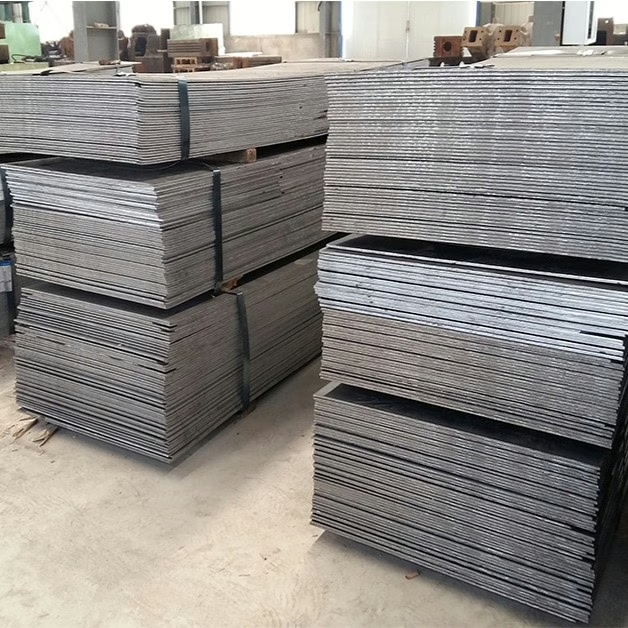
What Defines M2 Tool Steel Hardness?
The inherent hardness of M2 tool steel is a key characteristic. Typically, M2 high-speed tool steel can achieve a room temperature hardness of 64 HRC (Rockwell Hardness C scale). The specific M2 tool steel heat treatment process has a significant influence on the final hardness.
- Achievable Hardness Range: Depending on precise austenitizing and quenching methods, particularly with oil quenching, M2 can reach hardness values ranging from 60 to 66 HRC.
- As-Quenched Hardness: When properly air-quenched from the correct hardening temperature, the as-quenched hardness can be expected to be around 65-66 HRC.
The Crucial Role of Heat Treatment in M2 Hardness
Achieving and controlling the final M2 tool steel hardness relies heavily on expert heat treatment, involving austenitizing, quenching, and subsequent tempering.
Tempering is especially critical for M2. It’s performed after quenching to reduce internal stresses and enhance toughness. Crucially, tempering develops secondary hardness, a hallmark of high-speed steels. This phenomenon is driven by the precipitation of fine alloy carbides, primarily influenced by dissolved molybdenum, tungsten, and vanadium. These carbides are essential for M2 to maintain high hardness even at elevated temperatures.
A common first tempering temperature for M2 is 1050°F (565°C). The resulting tempered hardness typically falls within the 64-65 HRC range. Peak hardness is often achieved with tempering temperatures around 540-560°C.
The overall hardness you measure in M2 is a synergistic combination of its tempered martensite matrix and the various hard carbide phases embedded within its microstructure.
- Martensite Matrix: The base matrix in hardened high-speed steel contributes significantly, with a hardness of approximately 900 HV (Vickers Hardness) or 790 HK (Knoop Hardness), translating to about 60.5 HRC.
- Hard Carbides: M2 also contains extremely hard carbides that dramatically improve wear resistance:
- MC (Vanadium Carbides): These boast hardness values around 2300-3000 HV (or 2520 HK).
- M6C (Tungsten-Molybdenum Carbides): These typically exhibit hardness around 1400-1700 HV (or 1490 HK).
While the matrix provides the bulk hardness, these undissolved carbides are indispensable for the steel’s superior abrasion resistance. Steels with a higher proportion of these hard carbides can even approach hardness values closer to 70 HRC.
M2 Tool Steel’s Hot Hardness
For high-speed cutting operations, retaining hardness at elevated temperatures – known as hot hardness or red hardness – is essential. M2 tool steel excels in this regard, possessing good red hardness and high resistance to thermal softening. While hardness naturally decreases with increasing temperature, M2 maintains useful hardness up to approximately 600°C, ensuring consistent performance even under demanding conditions.
Balancing M2 Hardness and Toughness for Optimal Performance
It’s a fundamental principle in metallurgy that while high hardness generally improves strength and wear resistance, it often comes at the expense of toughness. This inverse relationship is a critical consideration in tool design. M2 tool steel offers a remarkably balanced combination of abrasion resistance and toughness.
- Relative Abrasion Resistance: M2 is rated at 95 (compared to D2 at 100), indicating excellent wear properties.
- Toughness: It possesses medium toughness, rated at 20 (similar to D2, though lower than grades such as A2 or S7).
For specific tooling applications, the desired M2 tool steel hardness level is often finely tuned to optimize this balance between wear resistance and toughness.
Our experience shows that a “one-size-fits-all” approach to hardness isn’t always best. Here’s how M2 tool steel hardness is typically adjusted for various uses:
APPLICATION TYPE | RECOMMENDED M2 HARDNESS RANGE (HRC) | PRIMARY BENEFIT OF RANGE |
Punches | 60-62 HRC | Improved ductility & toughness, reduced cracking under light service. |
Shearing Dies | 58-63 HRC | Balanced wear and toughness for cutting. |
General-Purpose Saw Blades | Slightly Lower Hardness | Enhanced toughness to prevent chipping. |
Maximum Wear Resistance | 64-65 HRC | Optimal for abrasive applications. |
Important Note: Attempting to harden M2 excessively, for example, by using austenitizing temperatures above 1210-1220°C (2230°F), might not significantly increase hardness but can lead to a notable loss in toughness. We always advise adhering to established heat treatment protocols to ensure optimal material properties.
Enhancing M2 Tool Steel Hardness with Surface Treatments
Beyond traditional heat treatment, surface treatments can further enhance the wear resistance of M2 tool steel, achieving extremely high surface hardness while maintaining the desired core hardness.
- Ion Nitriding: This process can achieve a very high surface hardness, typically ranging from 1050 to 1200 HV, while the core retains its specified hardness of 64-66 HRC.
- Boronizing: For applications requiring even greater surface hardness, boronizing can achieve values exceeding 1500 HV.
Your Partner in M2 Tool Steel
In summary, M2 high-speed tool steel is a remarkably versatile grade, offering a powerful combination of hardness (typically 64-65 HRC after tempering), exceptional wear resistance, and reliable hot hardness. Its performance is precisely controlled through careful heat treatment, leveraging the secondary hardening phenomenon driven by alloy carbides. While it possesses medium toughness, the specific working hardness is always tuned to meet the exact demands of your particular tooling application.
Unlock Superior Performance with Aobo Steel M2 Tool Steel
With over 20 years of expertise in forging tool steel and a commitment to quality, Aobo Steel is your trusted partner for premium M2 Tool Steel. Don’t compromise on durability and precision.
Ready to enhance your operations? Please fill out the form below to contact our tool steel experts today!