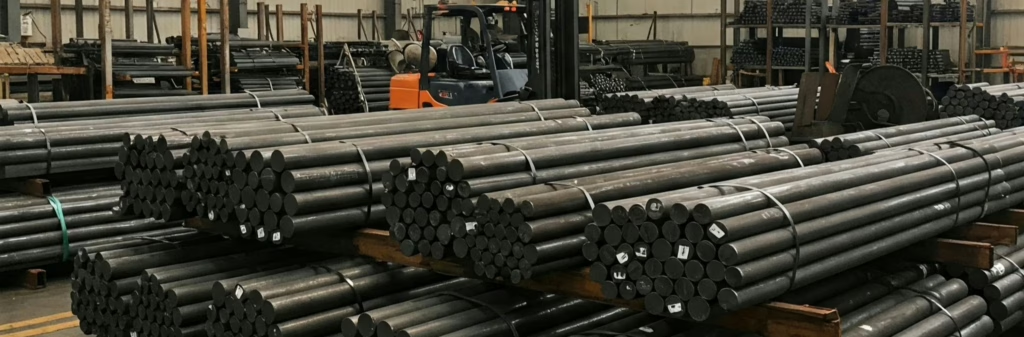
D6 Tool Steel | 1.2436 | SKD2
AOBO STEEL – Trusted Global Tool Steel Supplier
D6 Tool Steel is classified under the AISI system as a high-carbon, high-chromium cold-work tool steel. Steels in this category typically feature a nominal chromium content of around 12%, which is fundamental to their performance characteristics. The specific properties are fine-tuned through variations in alloying elements, such as carbon, molybdenum, vanadium, and manganese.
1. Applications
- Long production run blanking dies
- Cold-forming punches and dies
- Tooling components subjected to severe abrasion
- Applications where maintaining a sharp edge over extended use is critical
2. D6 Steel Composition
Carbon (C) | Chromium (Cr) | Tungsten (W) | Manganese (Mn) | Silicon (Si) |
2.00 – 2.20 | 11.50 – 12.50 | 0.60 – 0.90 | 0.20 – 0.40 | 0.10 – 0.40 |
The D6 tool steel equivalent grades’ composition
Carbon (C) | Silicon (Si) | Manganese (Mn) | Chromium (Cr) | Tungsten (W) | Phosphorus (P) | Sulfur (S) | |
Germany/W-Nr. 1.2436 (X210CrW12) | 2.00 – 2.30 | 0.10 – 0.40 | 0.30 – 0.60 | 11.0 – 13.0 | 0.60 – 0.80 | ≤ 0.030 | ≤ 0.030 |
Japan/JIS SKD2 | 2.00 – 2.30 | 0.10 – 0.60 | 0.30 – 0.60 | 11.0 – 13.0 | 0.60 – 0.80 | ≤ 0.030 | ≤ 0.030 |
China/GB Cr12W | 2.00 – 2.30 | ≤ 0.40 | ≤ 0.40 | 11.0 – 13.0 | 0.60 – 0.90 | ≤ 0.030 | ≤ 0.030 |
3. Properties of D6 Steel
3.1 Physical properties
Density | Thermal Expansion Coefficient | Thermal Conductivity | Specific Heat Capacity |
7.67 g/cm³ | 10.8 µm/m°C (21-400°C) | 20.5 W/mK (20°C) | 0.460 J/g-°C (20°C) |
3.2 Hardness and Wear Resistance
A primary advantage of D6 Tool Steel is its very high wear resistance. This stems directly from its high carbon and chromium content, which promotes the formation of hard chromium-rich carbides in the steel’s microstructure after heat treatment. Properly hardened and tempered, D6 typically achieves a hardness of between 54 and 61 HRC. Its wear resistance generally exceeds that of the more common D2 tool steel, making it suitable for applications that demand a long service life under abrasive conditions.
3.3 Toughness
D6 has high wear resistance, but lower toughness. Compared to shock-resistant steels (such as S-series) or other cold-work steels with lower carbon content (like A-series or D2), D6 Tool Steel is more brittle. The same hard carbides that resist wear can make the steel more prone to chipping or cracking under impact. Therefore, D6 Tool Steel is not recommended for applications involving significant shock or impact loading.
3.4 Hardenability and Heat Treatment
D6 is a deep-hardening steel; it can achieve relatively uniform hardness through its cross-section, even in larger sizes. It is typically an oil-hardening grade, although it can be air-hardened with some sacrifice in achievable hardness. Tempering after hardening is essential to relieve stresses and achieve the desired balance of hardness and toughness.
3.5 Dimensional Stability
As an oil-hardening steel, D6 may exhibit greater dimensional changes during heat treatment compared to air-hardening grades like D2 Tool Steel. Careful control of the heat treatment process is necessary if tight dimensional tolerances are critical.
3.6 Machinability and Grindability
Due to its high hardness and significant carbide content, D6 steel is considered more difficult to machine and grind compared to lower-alloy steels or even D2. This should be factored into manufacturing processes and costs.
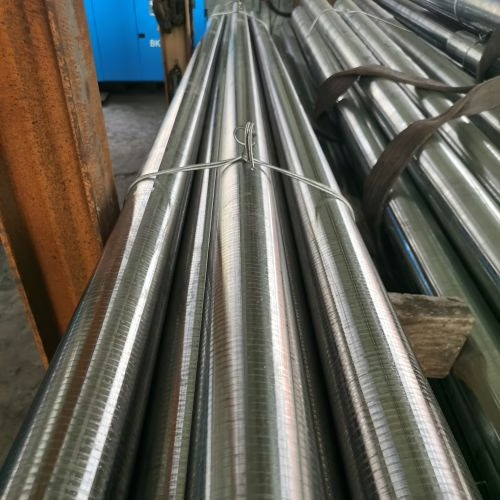
Interesting In D6 | 1.2436 Tool Steel? Please fill out the following form to contact us now!
4. D6 tool steel heat treatment
4.1 Preheating
Preheating reduces thermal shock, thereby lowering the risk of subsequent cracking or deformation. Preheating is typically performed at temperatures between 650°C and 760°C (1200°F and 1400°F). Ensure that the entire tool has reached the preheating temperature uniformly before calculating the soaking time. Based on our experience, the soaking time is 10–15 minutes.
4.2 Austenitizing (Hardening)
The purpose of this step is to transform the microstructure of the steel into austenite, preparing it for subsequent quenching. The temperature range is between 950°C and 1050°C (1740°F and 1920°F). The holding time is 1 hour per 25 mm (1 inch) of thickness. It is important to note that insufficient holding time may result in incomplete quenching, while excessive holding time may lead to grain growth and reduced toughness.
4.3 Quenching
This step involves transforming the austenite into hard martensite. D6 Tool Steel is an oil-hardening steel. Oil quenching provides a sufficiently fast cooling rate for hardening while being less harsh than water, which significantly reduces the risk of cracking and distortion.
The specific process involves quenching the workpiece in oil until it cools to room temperature or 65 °C (150°F).
Sometimes, air-quenching is also chosen, but the hardness after air quenching is relatively lower. If higher deformation requirements are specified, air quenching of D6 steel can be considered.
4.4 Tempering
The purpose of tempering is to reduce brittleness and increase toughness. A two-step tempering process is recommended to ensure maximum stress relief and dimensional stability.
The tempering temperature ranges from 150°C to 550°C (300°F to 1020°F). The soaking time is 2 hours per 25mm (1 inch) of thickness for each tempering cycle.
The tempering temperature determines the material’s final hardness. Higher tempering temperatures reduce the hardness of D6 steel but increase its toughness. The specific temperature should be determined based on actual application requirements.
4.5 Achieving Better Results and Avoiding Problems
Proper process control is crucial to achieving a successful heat treatment.
4.5.1 Dimensional Stability
To reduce the risk of deformation of D6 steel during quenching, the following precautions should be taken.
- Two preheating cycles can be performed.
- Ensure uniform heating during the austenitization process.
- Stir during oil quenching.
- Perform stress relief treatment after rough machining and before final heat treatment.
4.5.2 Stress Relief (Post-Hardening)
Stress relief treatment should be performed after heavy grinding, welding, or electrical discharge machining. The stress relief temperature should be 15°C to 30°C (25°F to 50°F) lower than the final tempering temperature. The holding time should be 1-2 hours per 25mm (1 inch) of thickness.
4.5.3 Common Heat Treatment Issues
- Cracking: Often caused by thermal shock (insufficient preheat or excessively harsh quench).
- Distortion: Caused by non-uniform heating/cooling or internal stresses.
- Inadequate Hardness: Results from incorrect austenitizing temperature/time or insufficient quenching.
4.6 Forging D6 tool steel
Slowly preheat to 900 °C (1650 °F). Forging should begin within the temperature range of 980 °C (1800 °F) to 1095 °C (2000 °F). Do NOT forge below 900 °C (1650 °F). For larger cross-sections, heavier pieces, or rapid thinning, use the higher end of the temperature range; for smaller cross-sections or lighter thinning, use the lower end of the temperature range.
5. Comparison with Other Tool Steels
5.1 D6 vs. D2
D2 tool steel and D6 tool steel are high-carbon, high-chromium cold-work tool steels known for wear resistance. D6 has slightly higher wear resistance at the cost of lower toughness and more complex/difficult heat treatment (oil quenching, higher distortion risk). D2 is more widely used due to its better balance of properties, especially its air-hardening capability and minimal distortion.
5.2 D6 vs. D3
- Both are high-carbon, high-chromium, oil-hardening steels renowned for their exceptionally high wear resistance.
- Minor compositional differences may exist (sometimes W or V in D6 Tool Steel).
- D3 heat treatment is complex than D6.
5.3 D6 vs. D7
- D7 contains added vanadium, potentially offering even higher abrasion resistance than D6 Tool Steel.
- D7 typically has lower toughness than D6 and requires higher hardening temperatures.
6. Considerations When Choosing D6 Tool Steel
D6 steel is an excellent choice for specific applications demanding maximum wear resistance in cold-work tooling. However, carefully consider:
- Lower Toughness: Not suitable for high-impact applications.
- Processing: More challenging to machine and grind.
- Heat Treatment: Oil quenching requires careful process control for dimensional stability.
- Availability: May be less readily available than D2 Tool Steel.
7. Equivalent Grades
- DIN EN (Europe): 1.2436 (X210CrW12)
- JIS (Japan): SKD2
- BS (UK): BD6
- ISO: X210CrW12
- GB(China): Cr12W
8. Supply forms and dimensions
The D6 tool steel that we supplied is in various forms, including round bars, sheet plates, slabs, flat bars, square bars, and blocks. The dimensions of the flat bar range from: width 20–600 mm × thickness 20–400 mm × length 1,000–5,500 mm. The dimensions of the round bar range from a diameter of 20–400 mm × a length of 1,000–5,500 mm. The block dimensions are obtained by cutting the flat bar.
For smaller sizes, such as round bars with a diameter less than 70 mm, we use the hot-rolled process. For sizes greater than 70 mm, we offer forged products.
UT testing: Sep 1921-84 D/d, E/e.
Surface Treatment: original black, peeled, machined/turned, polished, grounded, or milled surface finishes.
Inventory Status: We do not maintain a stock of D6 steel. We arrange production based on customer orders.
Delivery time: Electric Arc Furnace (EAF) materials are 30-45 days. ESR materials are approximately 60 days.
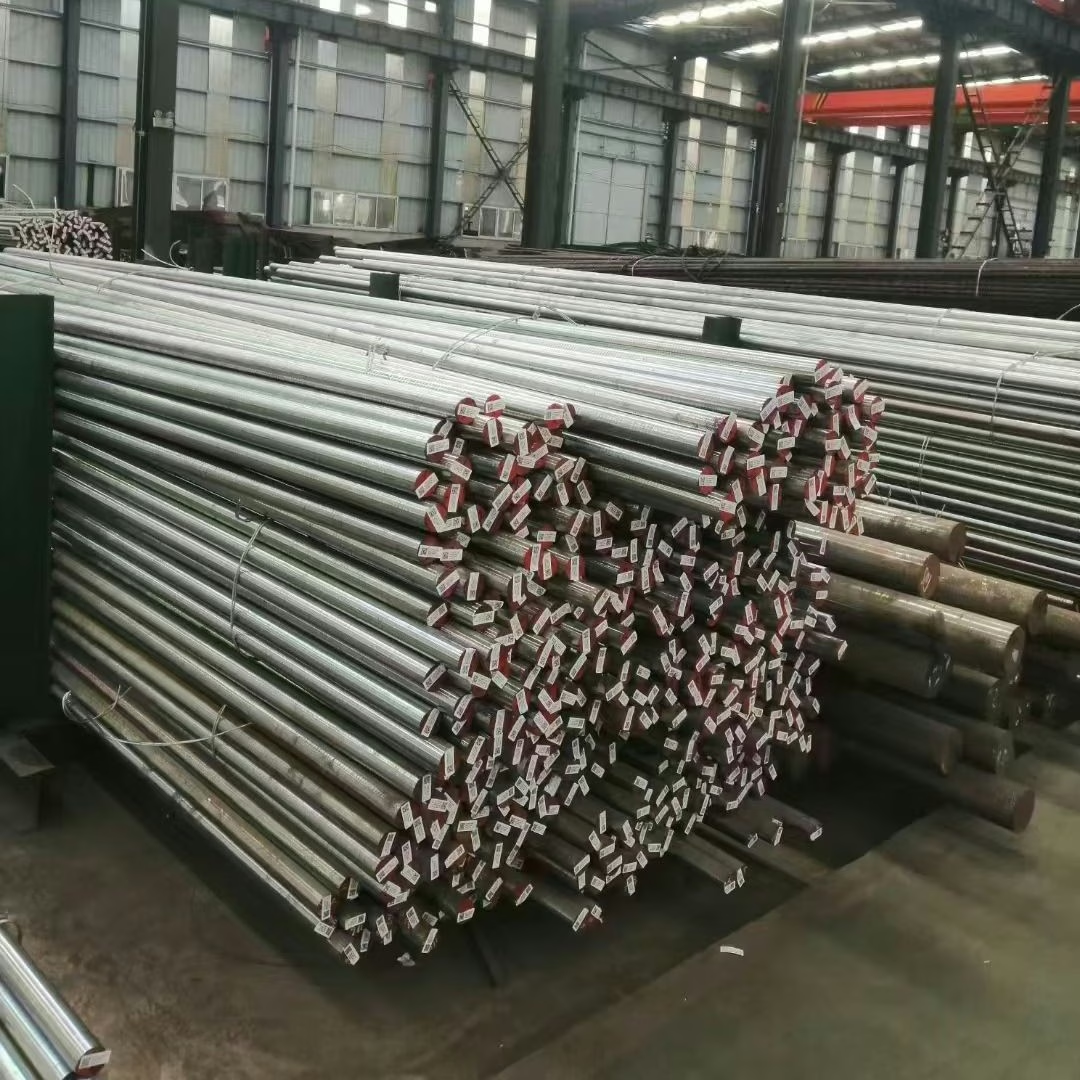
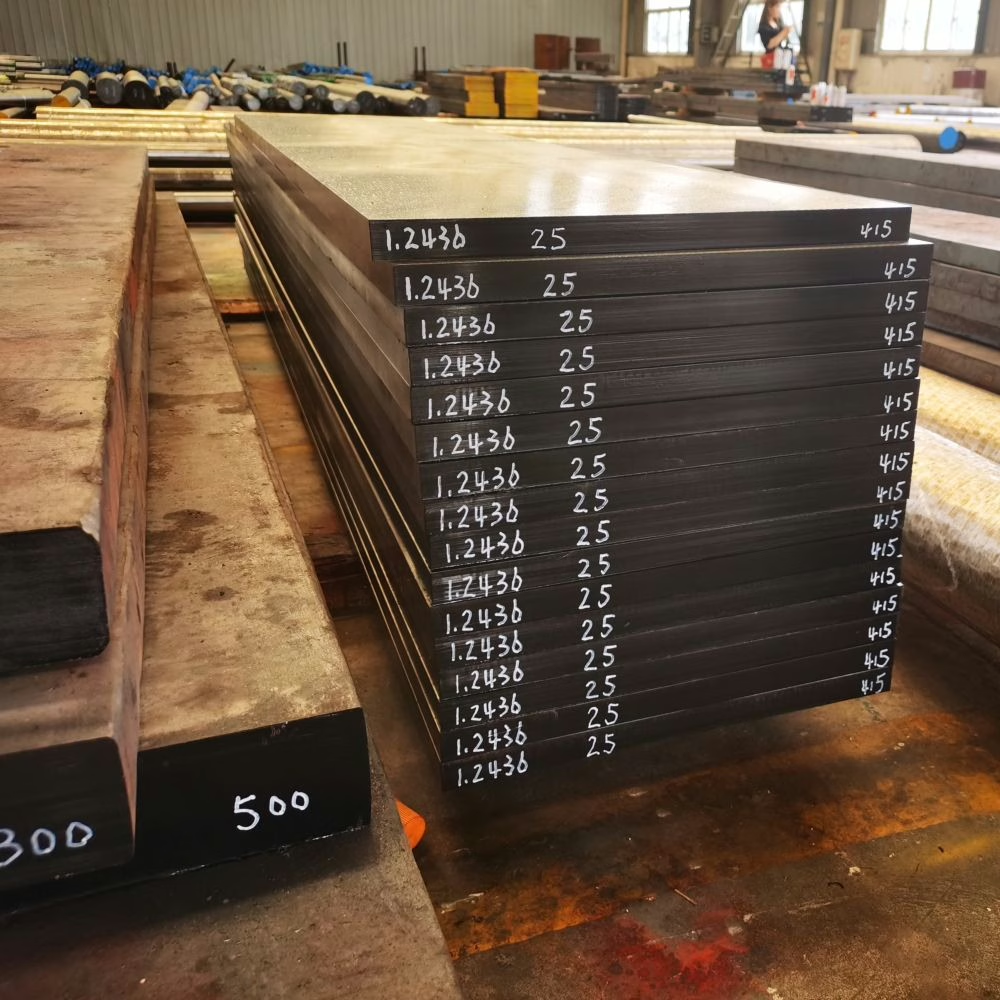
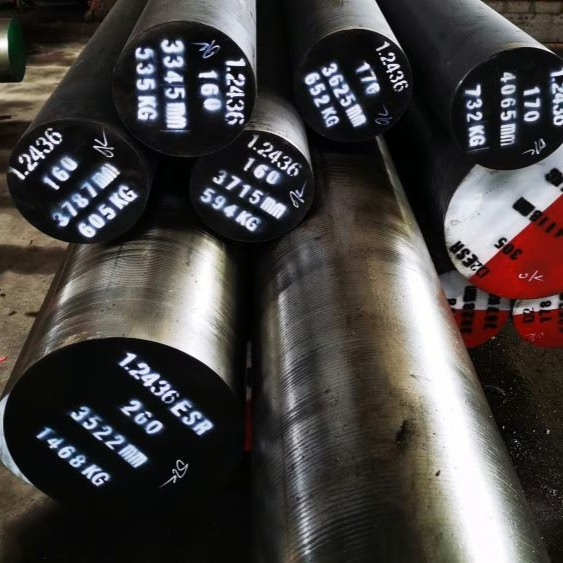
FAQ
D6 tool steel is a high-carbon, high-chromium tool steel alloyed with tungsten, primarily used for cold work applications. It is characterized by high compressive strength, high wear resistance, high surface hardness, and good hardening stability. It is also known as SKD2 steel and DIN 1.2436 steel.
D6 tool steel is characterized by excellent resistance to wear and abrasion, high compressive strength, high surface hardness, and good hardening and dimensional stability. Its robust carbide structure provides prolonged performance and reduced maintenance even under extreme stress.
AISI D6 tool steel is equivalent to JIS SKD2 in Japan and DIN 1.2436 (also X210CrW12) in Germany/UK/France. It is also referred to as UNS T30406.
D6 tool steel has a density of 7.67 g/cm³ (0.277 lb/in³). Its thermal expansion coefficient is 10.8 µm/m°C (6 µin/in°F) at 21-400°C, and its thermal conductivity is 20.5 W/mK (142 BTU.in/hrft².°F) at 20°C. It also has a specific heat capacity of 0.460 J/g-°C (0.110 BTU/lb-°F) at 20°C.
D6 tool steel exhibits a compressive strength of 1320 MPa (191000 psi) and a modulus of elasticity of 194 GPa (28100 ksi). Its Rockwell C hardness is 46 HRC in certain conditions, but can reach 55-62 HRC after heat treatment.
D6 tool steel is widely used for forming tools, molds for abrasive plastics and ceramics, and long-run press tools. It is also suitable for blanking dies, shearing tools for hard materials, stamping tools, scraping tools, woodworking tools, drawing tools, and machine knives. Specific uses include blanking dies for cutting sheets up to 2mm thick, paper and plastic blades, and extrusion dies for metals, plastics, and rubber.
Yes, D6 tool steel is used for outdoor fixed blades. A knifemaker noted that D6, being a super high-quality Tungsten alloyed tool steel, provides incredible edge retention due to its Tungsten carbides. While it can be heat-treated to 62 HRC, tempering it to 58 HRC makes it much tougher and a better daily tool for knives.
Yes, D6 tool steel is used for molds for abrasive plastics and also specifically for injection molds requiring high precision and wear resistance.
Yes, D6 tool steel is commonly used for blanking dies, shearing tools for hard materials, and blanking and shearing tools in general. It is suitable for cutting sheets up to 2mm thick and for cold shear blades for paper, plastic, cardboard, and metal.
D6 tool steel is heated slowly and uniformly to 700°C (1292°F), and then more rapidly to 900-1050°C (1652-1922°F) for forging. After forging, it should be cooled slowly to room temperature in a furnace.
D6 tool steel is annealed at 800-840°C (1472-1544°F) and then cooled slowly in a furnace. Alternatively, it can be heated at 50-100°C (122-212°F) per hour to 830-870°C (1526-1598°F), soaked for 1 hour per 25.4 mm (1 inch), and then cooled slowly in a furnace or controlled environment. The hardness after annealing will be approximately 225 Brinell.
Stresses from D6 tool steel can be eliminated before hardening by heating up to 650-700°C (1202-1292°F), especially if machining operations have been heavy. The steel is then allowed to cool slowly.
D6 steel is first pre-heated slowly to 750-800°C (1382-1472°F) and thoroughly soaked. Heating then continues until a final hardening temperature of 950-980°C (1742-1796°F), or 940-1000°C. It is then followed by air or oil quenching, or quenching in a warm bath or salt bath. Vacuum (high-speed gas) hardening is also considered a perfect method.
D6 tool steel is heated uniformly and thoroughly at the selected tempering temperature. Double tempering can also be carried out with intermediate cooling to room temperature. Tempering temperatures typically range from 500-600°C (932-1112°F), or specific temperatures like 100°C (resulting in 63 HRC) up to 600°C (resulting in 48 HRC). The final hardness of D6 tool steel after heat treatment can range from 55 to 62 HRC.
In hard turning of AISI D6 steel, machining parameters like speed, feed, and depth of cut affect output responses such as surface roughness, cutting force, crater wear length, crater wear width, and flank wear. Abrasion and adhesion are dominant wear mechanisms, with tool wear increasing with speed, and cutting force increasing rapidly at higher speeds (70-90 m/min). Higher feed and depth of cut values also result in more surface damage and higher cutting force. Machine learning models can be used to test, evaluate, and optimize these machining parameters to predict characteristics like surface roughness.
D6 tool steel has better through-hardening properties and dimensional stability compared to D3 steel.
Get a Competitive Quote for D6 Tool Steel
With over 20 years of forging expertise, Aobo Steel is your trusted partner for high-performance D6 tool steel. We provide not just materials, but solutions. Leverage our deep industry knowledge and reliable supply chain for your project’s success.
✉ Contact us by filling out the form below.
Explore Our Other Products
D2/1.2379/SKD11
D3/1.2080/SKD1
D6/1.2436/SKD2
A2/1.23663/SKD12
O1/1.2510/SKS3
O2/1.2842
S1/1.2550
S7/1.2355
DC53
H13/1.2344/SKD61
H11/1.2343/SKD6
H21/1.2581/SKD7
L6/1.2714/SKT4
M2/1.3343/SKH51
M35/1.3243/SKH55
M42/1.3247/SKH59
P20/1.2311
P20+Ni/1.2738
420/1.2083/2Cr13
422 stainless steel
52100 bearing steel
440C stainless steel
4140/42CrMo4/SCM440
4340/34CrNiMo6/1.6582
4130
5140/42Cr4/SCR440
SCM415