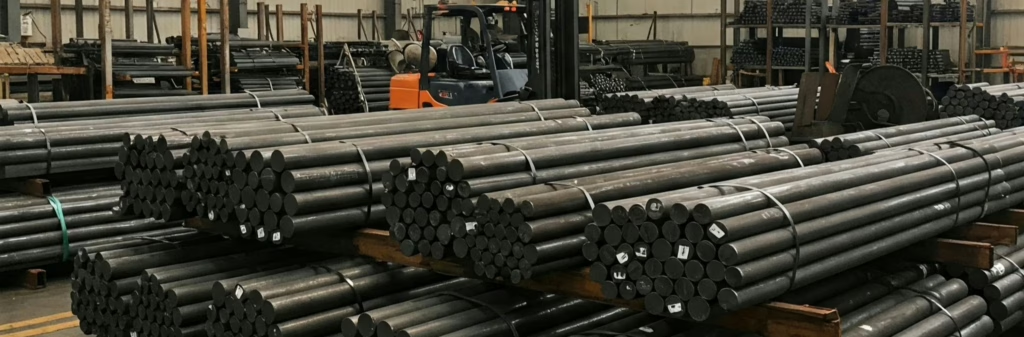
Cr12 tool Steel
AOBO STEEL – Trusted Global Tool Steel Supplier
Cr12 tool steel is a grade under the Chinese national standard. It is a very classic high-carbon, high-chromium cold work die steel that combines high strength, wear resistance, and hardenability. Equivalent grades to Cr12 include American AISI D3, German W – Nr. 1. 2080, and Japanese JIS SKD1.
1. Composition(GB / T 1299—2000)
C | Cr | Si | Mn | P | S |
2.00 – 2.30 | 11.50 – 13.00 | ≤ 0.40 | ≤ 0.40 | ≤ 0.030 | ≤ 0.030 |
2. Mechanical Properties
Cr12 steel is classified as a high-carbon, high-chromium ledeburitic steel. Due to its high mass fraction of carbon, it exhibits lower impact toughness and a tendency for brittle fracture, coupled with a susceptibility to forming non-uniform eutectic carbides.
The high concentration of chromium in the steel promotes the formation of (CrFe)₇C₃ complex carbides, which in turn reduces the amount of cementite (Fe₃C). During the quenching heat treatment, a significant volume of these carbides dissolves into the austenite phase. Subsequent quenching transforms the austenite into high-hardness martensite. Upon tempering, a fine and dispersed precipitation of carbides occurs within the martensitic matrix, resulting in excellent wear resistance.
Through an appropriate heat treatment process, a microstructure with a combination of high strength and toughness can be achieved.
3. Forging Process
Item | Heating Temperature/°C | Initial Forging Temperature/°C | Final Forging Temperature/°C | Cooling Method |
Steel Ingot | 1140 ~ 1160 | 1100 ~ 1120 | 900 ~ 920 | Slow Cooling |
Steel Billet | 1120 ~ 1140 | 1080 ~ 1100 | 880 ~ 920 | Slow Cooling |
The primary objective of forging Cr12 steel is to break down and refine the coarse carbides inherent in the steel, ensuring they are distributed uniformly throughout the matrix. This process significantly improves the material’s overall strength and toughness. Furthermore, proper forging establishes a rational alignment of flow lines within the die, which helps to promote consistent and predictable dimensional changes (distortion) in all directions during the subsequent quenching process.
Regarding the heating procedure for forging, it is crucial to first preheat the workpiece before gradually increasing it to the final forging temperature. Attention must be paid to the proper placement of the workpiece within the furnace, and the material should be turned or flipped periodically to ensure uniform heating.
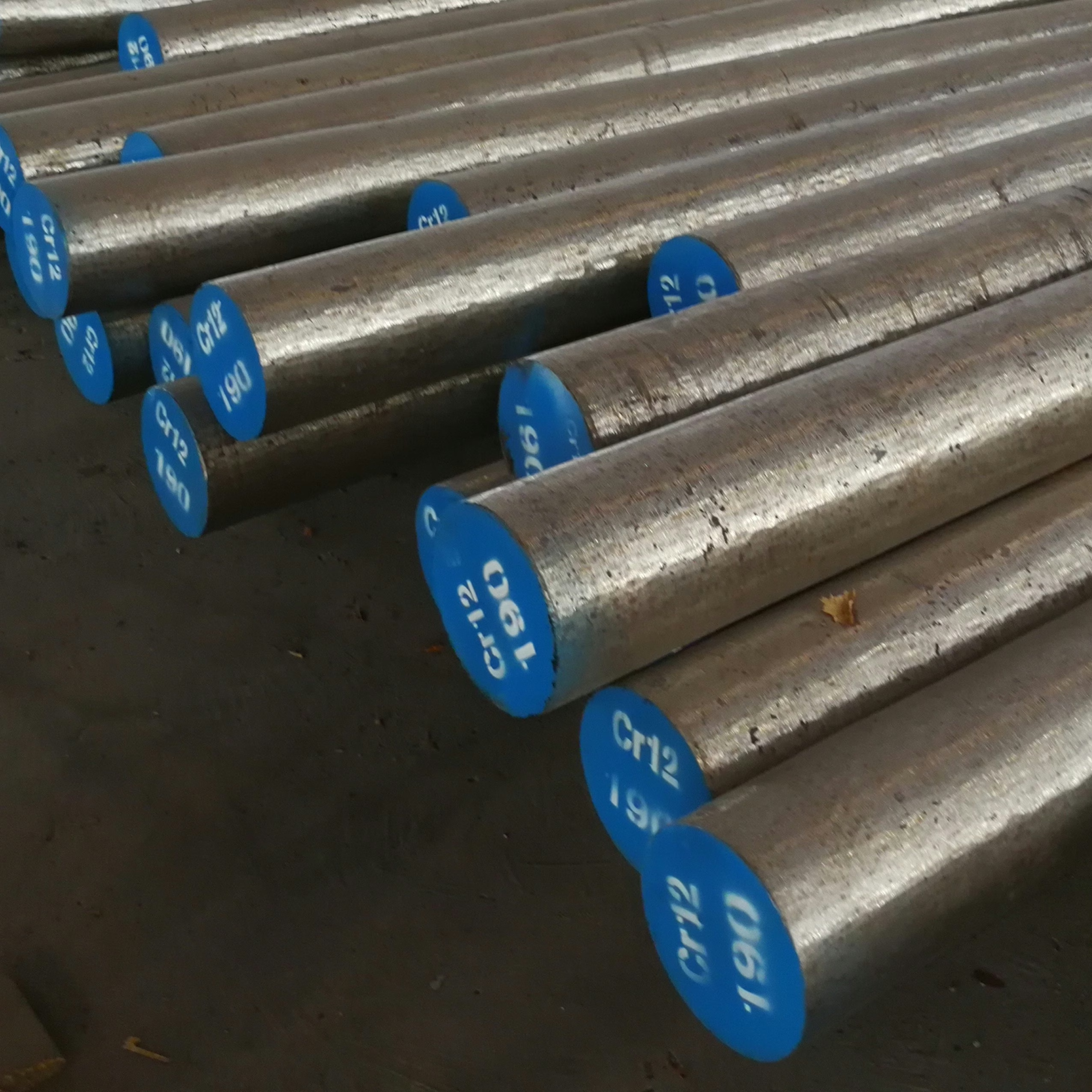
We have Cr12 round steel in stock and can ship it at any time. Please fill out the following form to contact us now!
4. Heat Treatment
4.1 Preheating
Process Parameters | |
General Annealing after Forging | Heating temperature: 850 ~ 870 °C. After uniform heating, hold for 4 ~ 5h. Furnace cool at a rate of <30°C/h to below 500°C, then air cool. Hardness after annealing: ≤229HBW. Microstructure after annealing: granular pearlite + carbide. |
Isothermal Annealing after Forging | Heating temperature: 830 ~ 850 °C. Hold for 2 ~ 3h. Furnace cool to 720 ~ 740°C and hold for 3 ~ 4h. Furnace cool to below 550°C, then air cool. Hardness after annealing: ≤269HBW. Microstructure: granular pearlite + carbide. |
4.2 Quenching
4.2.1 Quenching Specification
Process | Quenching Temperature/°C | Cooling Method | Hardness HRC |
Recommended Quenching Specification | 950 ~ 980 | Oil Cooling | ≥60 |
Isothermal Quenching Process | Heat to 980°C, hold for a certain period, then isothermally hold in a salt bath at 250 ~ 280°C for a period of time, and then air cool to obtain a mixed structure of lower bainite + martensite + retained austenite + carbide. Then, temper at an appropriate temperature to obtain a high-toughness structure. |
4.2.2 Performance Comparison of Different Heat Treatment Processes
Heat Treatment Process | Hardness HRC | Impact Toughness aᴋ / (J/cm²) | Retained Austenite (Volume Fraction, %) | Tapping Plate Life / x10⁴ pieces | Wear Loss/mg |
980°C heating, oil quenching | 66.5 | 14.1 | 13.2 | 4 | — |
980°C heating, 180°C graded quenching 50min | 65.8 | 15.8 | — | 5 | — |
980°C heating, 270°C isothermal 3h | 62.5 | 15.9 | — | 6 | 11.9 |
980°C heating, 270°C isothermal 4h | 60 | 17.7 | 15.02 | — | — |
980°C heating, 270°C isothermal 5h | 59 | 16.8 | — | — | — |
980°C heating, 180°C pre-quenching 35min, 270°C isothermal 1h | 64.6 | 14.6 | — | 12 ~ 15 | 8.2 |
980°C heating, 180°C pre-quenching 35min, 270°C isothermal 2h | 46.2 | 14.9 | 18.31 | 12 ~ 28 | — |
980°C heating, 180°C pre-quenching 35min, 270°C isothermal 3h | 63.8 | 15.2 | — | — | — |
Note: All samples were tempered twice at 180°C, 1.5h each time.
4.2.3 Relationship between Quenching Temperature and Hardness
Quenching Temperature/°C | 875 | 900 | 925 | 950 | 975 | 1000 | 1050 | 1100 |
Hardness HRC | 54.5 | 57 | 60 | 62.5 | 65 | 66 | 64 | 59.5 |
4.3 Tempering
Tempering Specification
Purpose of Tempering | Heating Temperature/°C | Tempering Time (h) | Number of Tempers | Hardness HRC |
Relieve stress, stabilize structure | 180 ~ 200 | 2 | 1 | 60 ~ 62 |
Relieve stress, reduce hardness | 320 ~ 350 | 2 | 1 | 57 ~ 58 |
Note: The tempering temperature is generally 180 ~ 200°C, with hardness ≥60HRC. To avoid cracks from EDM and grinding and to improve the toughness of the mold, it is often tempered below 400°C. The hardness after tempering is 54 ~ 58HRC. The temper brittleness range is 275 ~ 375°C, which should be avoided as much as possible during tempering.
Relationship between Tempering Temperature and Hardness
Tempering Temperature/°C | Not Tempered | 200 | 300 | 400 | 450 | 500 | 550 | 600 | 650 |
Hardness HRC | 65 | 63 | 62 | 60 | 60 | 60 | 59.5 | 57.1 | 44 |
Note: 955°C oil quenching.
5. Applications
It is predominantly selected for manufacturing components that require high wear resistance but are subjected to relatively low impact loads.
Specific applications include:
- Cold shearing blades and cutters
- Drill bushings
- Gauges
- Punches
- Thread rolling plates and dies
- Stamping and punching dies
- Wire drawing dies
- Cold extrusion dies
- Coining and embossing dies
- Deep drawing dies
Explore Our Other Products
D2/1.2379/SKD11
D3/1.2080/SKD1
D6/1.2436/SKD2
A2/1.23663/SKD12
O1/1.2510/SKS3
O2/1.2842
S1/1.2550
S7/1.2355
DC53
H13/1.2344/SKD61
H11/1.2343/SKD6
H21/1.2581/SKD7
L6/1.2714/SKT4
M2/1.3343/SKH51
M35/1.3243/SKH55
M42/1.3247/SKH59
P20/1.2311
P20+Ni/1.2738
420/1.2083/2Cr13
422 stainless steel
52100 bearing steel
440C stainless steel
4140/42CrMo4/SCM440
4340/34CrNiMo6/1.6582
4130
5140/42Cr4/SCR440
SCM415