3Cr2W8V is a grade under the Chinese GB/T standard, and its equivalent grade is ASTM/AISI H21 in the United States. 3Cr2W8V is a high thermal strength hot work tool steel, commonly used for dies that operate under high temperature and stress. It is a ledeburitic steel, meaning it has a microstructure with large primary carbides, which contributes to its high wear resistance at elevated temperatures.
1. Chemical Composition
C | Si | Mn | Cr | W | V | P | S |
0.30 – 0.40% | ≤0.40% | ≤0.40% | 2.20 – 2.70% | 7.50 – 9.00% | 0.20 – 0.50% | ≤0.030% | ≤0.030% |
2. Physical Properties of 3Cr2W8V Steel
2.1 Critical Points of 3Cr2W8V Steel
Critical Point | Ac₁ | Ac₃ | Ar₁ | Ar₃ | Ms | Mf |
Temperature/°C | 850 | 930 | 773 | 835 | 350 | 160 |
2.2 Linear Expansion Coefficient
Temperature/°C | 100 | 200 | 300 | 400 | 500 | 600 | 700 | 800 | 900 | 1000 |
Linear Expansion Coefficient α/ × 10⁻⁶ °C⁻¹ | 12.0 | 12.3 | 12.7 | 13.1 | 13.5 | 13.9 | 14.5 | 14.5 | 12.8 | 13.3 |
2.3 Specific Heat Capacity
Temperature/°C | 100 | 200 | 300 | 500 | 800 | 900 |
Specific Heat Capacity cₚ/ [J/(kg·K)] | 468.2 | 473 | 478 | 685.5 | 1262.4 | 660.4 |
2.4 Thermal Conductivity
Temperature/°C | 100 | 200 | 700 | 900 |
Thermal Conductivity λ/[W/(m·K)] | 20.1 | 22.2 | 24.3 | 23.0 |
2.5 Electrical Resistivity
Temperature/°C | 20 | 200 | 500 | 700 | 900 |
---|---|---|---|---|---|
Electrical Resistivity ρ/ × 10⁻⁶ Ω·m | 0.50 | 0.60 | 0.80 | 1.0 | 1.19 |
2.6 Other Physical Properties
Density/(g/cm³) | Modulus of Elasticity E/MPa | Shear Modulus G/MPa |
---|---|---|
7.74 | 214 000 | 73 000 |
3. Hot Forging Process Specification for 3Cr2W8V Steel
Item | Heating Temperature/°C | Initial Forging Temperature/°C | Final Forging Temperature/°C | Cooling Method ① |
Steel Ingot | 1150 ~ 1200 | 1100 ~ 1150 | 850 ~ 900 | Air cooling first, then pit or sand cooling |
Steel Billet | 1130 ~ 1160 | 1080 ~ 1120 | 850 ~ 900 | Air cooling first, then pit or sand cooling |
① After forging, it should be cooled relatively quickly in the air to below Ac₁ (about 700°C), followed by slow cooling (pit cooling, sand cooling, or furnace cooling), or high-temperature annealing can be carried out. If conditions permit, direct red-hot annealing can be performed.
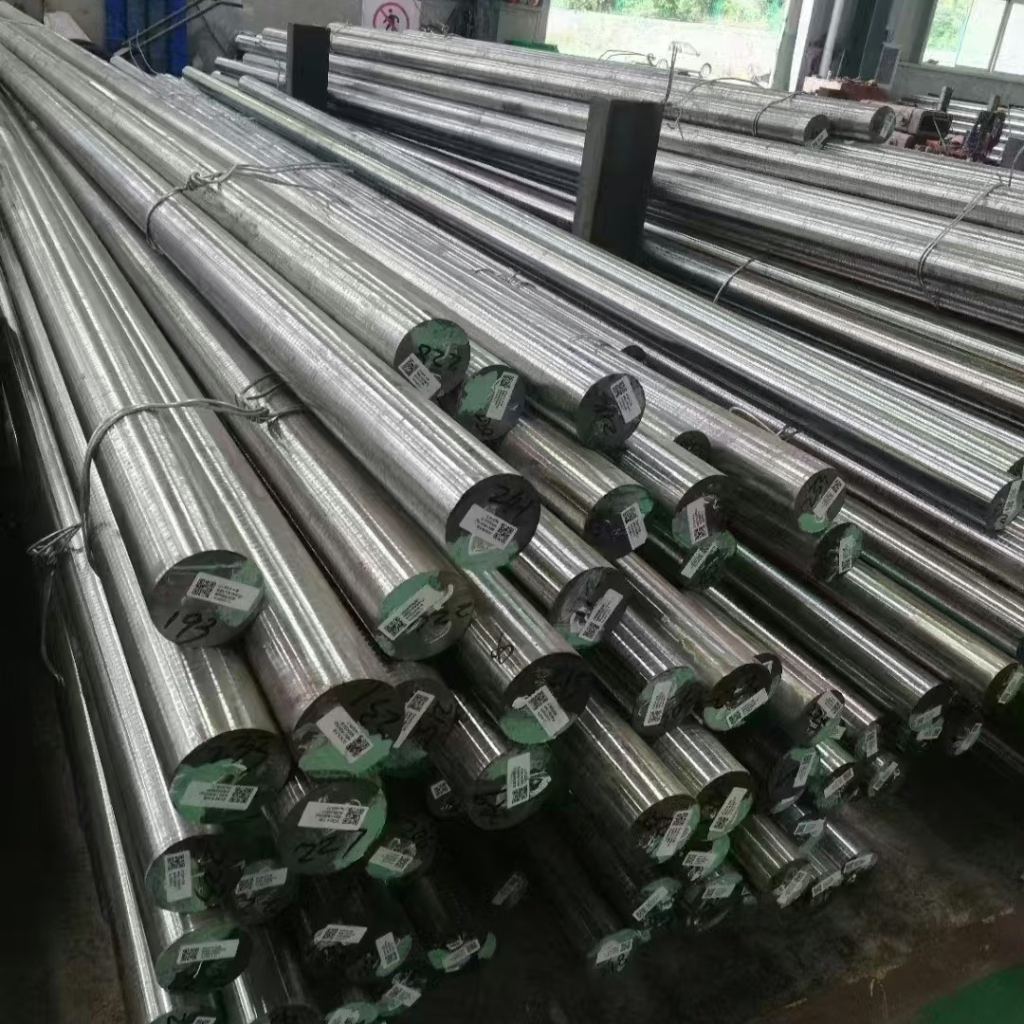
Please complete the following contact form to obtain a quotation for the best 3Cr2W8V(H10) steel.
4. Heat Treatment of 3Cr2W8V Steel
4.1 Preheating
① Preliminary Heat Treatment Process Specification
Preliminary Heat Treatment Plan | Process Parameters |
Annealing after forging | Heating temperature 800 ~ 820°C, holding for 2 ~ 4h, furnace cooling at < 30 ~ 40°C/h to below 600°C, then air cooling. Hardness after annealing is 207 ~ 255HBW, microstructure is pearlite + carbide. |
Isothermal annealing | Heating temperature 800 ~ 820°C, holding for 2 ~ 4h, furnace cooling at < 30 ~ 40°C/h to below 600°C, then air cooling. Hardness after annealing is 207~255HBW, microstructure is pearlite + carbide. |
② Hardness and Microstructure after Annealing
Hardness HBW | Microstructure | |
Unannealed | After Annealing | |
207 ~ 255 | Troostite + Martensite | Pearlite + Carbide |
4.2 Quenching
① Recommended Quenching Process
Quenching Temperature/°C | Quenching Cooling Medium | Quenching Cooling Medium Temperature/°C | Isothermal Holding Temperature/°C | Final Cooling to 20°C | Hardness HRC |
1050 ~ 1100 | Oil | 20 ~ 40 | 150 ~ 180 | Air Cooling | 49 ~ 52 |
Notes:
- For large dies, use the upper limit of the heating temperature. For small dies, use the lower limit.
- Large dies should be preheated to 600-650°C for 1-2 hours before continuing to heat.
- For flame furnace heating, hold for 40 ~ 50 minutes for every 25mm of die thickness. For electric furnace heating, increase the heating time by 40% over the time required for flame furnace heating.
② Common Quenching Processes for 3Cr2W8V Steel
Quenching Plan | Process Parameters |
Isothermal Quenching ¹ | Heating temperature is 1150°C, followed by oil cooling after holding at 350~450 °C. The microstructure is lower bainite + martensite, with hardness reaching over 47HRC. After isothermal quenching, low-temperature tempering is recommended at a temperature of 340~380 °C. |
High-Temperature Quenching ² | Heating temperature is 1150°C, followed by oil cooling after holding at 350~450 °C. The microstructure consists of lower bainite and martensite, with a hardness of over 47HRC. After isothermal quenching, low-temperature tempering is recommended at a temperature of 340~380 °C. |
¹ The bainitic structure obtained after isothermal quenching has high strength and toughness. Its tempering resistance is also much better than conventional heat treatment. It has high resistance to thermal shock and low die deformation, which can extend the service life of the die.
² Increasing the quenching heating temperature of 3Cr2W8V steel increases the alloying degree of martensite, resulting in excellent hot strength but slightly lower toughness. It is generally used for manufacturing dies that are not subjected to significant impact forces but require high hot strength, such as extrusion dies, die-casting dies, and press forming dies for copper and aluminum alloys.
③ Relationship between Quenching Temperature and Hardness of 3Cr2W8V Steel
Quenching Temperature /°C | 950 | 1050 | 1100 | 1150 | 1200 | 1250 |
Hardness HRC | 44 | 49 | 52 | 55 | 56 | 57 |
4.3 Solution Refining and Ultra-Fine Processing
Forged blanks are solution treated at 1200–1250°C to dissolve carbides into austenite, then quenched in hot oil or boiling water, followed immediately by high-temperature tempering or short-term isothermal spheroidizing treatment. High-temperature tempering is conducted at 720–850°C (the upper limit for blank processing and the lower limit for finished dies). Final heat treatment may employ conventional processes, such as oil quenching at 1100°C.
4.4 Termpering
① Recommended Tempering Process Specifications
Tempering Purpose | Heating Temperature/°C | Heating Equipment | Cooling | Hardness HRC |
Stress relief, stabilize structure and dimensions | 600 ~ 620 | Electric furnace | Air cooling | 40.2 ~ 47.4 |
Notes:
- Large molds should be tempered immediately after quenching. Generally, tempering is required twice (at 620°C and 600°C, for 2-3 hours each time). For large molds with complex shapes, three tempering cycles can be used.
- When tempering the mold, first place it in the furnace at 350 ~ 400°C for 1-3 hours, then raise the temperature to the final tempering temperature.
- The tempering holding time should be calculated as 40-45 minutes for every 25mm of thickness.
② Relationship between Tempering Temperature and Hardness
Quenching Condition | Hardness HRC at different Tempering Temperatures (°C) | Untempered | 500(°C) | 550(°C) | 600(°C) | 650(°C) | 670(°C) | 700(°C) |
1050°C Oil Quenching | Hardness HRC | 49 | 46 | 47 | 43 | 35 | 32 | 27 |
1075°C Oil Quenching | Hardness HRC | 50 | 47 | 48 | 44 | 36 | 33 | 30 |
1100°C Oil Quenching | Hardness HRC | 52 | 48 | 49 | 45 | 40 | 36 | 32 |
1150°C Oil Quenching | Hardness HRC | 55 | 49 | 53 | 50 | 45 | 40 | 34 |
4.5 Surface Treatment
Nitriding Process Specification
Process | Temperature/°C | Time/h | Medium | Nitrided layer | |
Depth/mm | Hardness HV | ||||
Gas Nitriding | 530 | 3 ~ 6 | NH₃ decomposition rate 30% ~ 60% | 0.07 ~ 0.12 | 1000 ~ 1160 |
5. Mechanical Properties
3Cr2W8V steel is a typical high-heat-strength hot-work tool steel. Its high content of W and Cr elements promotes carbide formation, resulting in superior high-temperature strength and thermal hardness, along with excellent high-temperature mechanical properties. However, its toughness and plasticity are relatively poor. This steel exhibits a high phase transformation temperature and demonstrates good resistance to thermal fatigue from alternating hot and cold cycles. It exhibits good hardenability, being fully hardenable in sections up to 80 mm in diameter, and possesses relatively high temper resistance.
5.1 Mechanical Properties of 3Cr2W8V Steel at Different Tempering Temperatures
Tempering Temperature/°C | Rm/MPa | Rp0.2/MPa | Z (%) | A (%) |
400 | 1800 | 1400 | 36 | 18 |
450 | 4800 | 1420 | 35.5 | 14 |
500 | 1800 | 1450 | 35 | 13 |
550 | 1760 | 1500 | 35.5 | 12 |
600 | 1620 | 1410 | 38 | 8 |
650 | 1270 | – | 36 | 12 |
Note: 1100°C oil quenching.
5.2 3Cr2W8V Steel High-Temperature Hardness
Temperatures (°C) | 300 | 450 | 600 | 650 | 700 | 750 |
Original Sample Hardness (HRC) | High-Temperature Hardness (HV) at various temperatures (°C) | |||||
48.8 ~ 49.1 | 479.5 | 448.5 | 414.5 | 398.5 | 354.5 | 208.5 |
42.0 ~ 43.0 | 390 | 386.5 | 332 | 304 | 268 | 203.5 |
5.3 Fatigue Performance Comparison Between 3Cr2W8V Steel and 4Cr5MoSiV1
Steel Grade | Number of Fatigue Cracks | Crack Length / mm | |
Total Length | Average Length | ||
3Cr2W8V (H21) | 125 | 2.81 | 0.023 |
4Cr5MoSiV1 (H13) | 11 | 0.46 | 0.041 |
6. Applications
3Cr2W8V steel is a high-heat-strength hot-work tool steel suitable for manufacturing hot-work dies and dies that endure high stresses at elevated temperatures with minimal impact loads. Examples include dies, core pins, and ejector pins for hot extrusion dies; punches, dies, and inserts for flat forging machines; copper alloy extrusion dies, die-casting molds, or counter-extrusion dies subjected to significant compressive, bending, and tensile stresses simultaneously. It is also used for high-temperature cutting tools in hot metal applications.
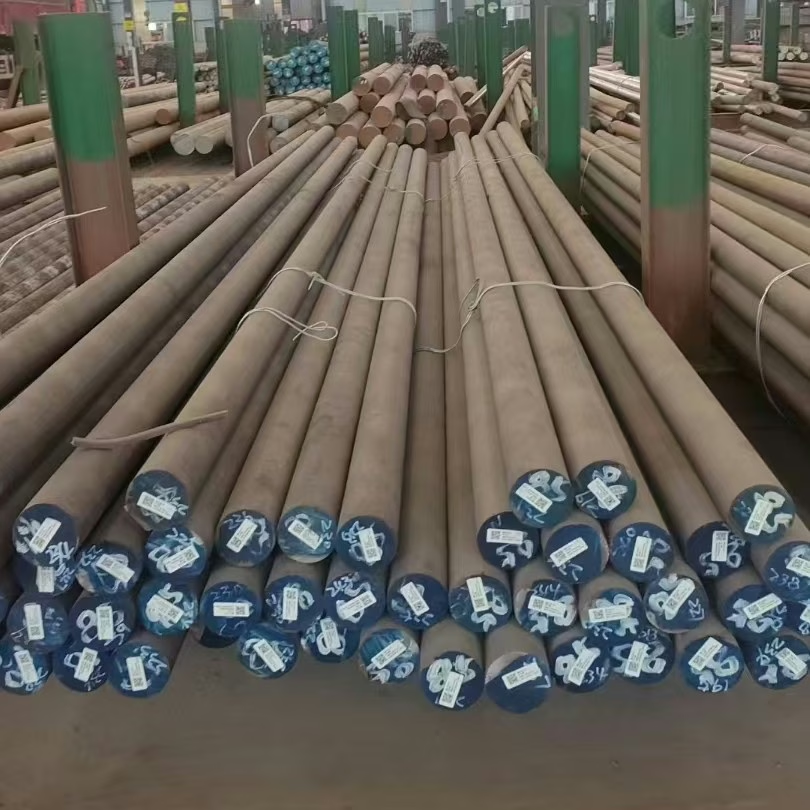
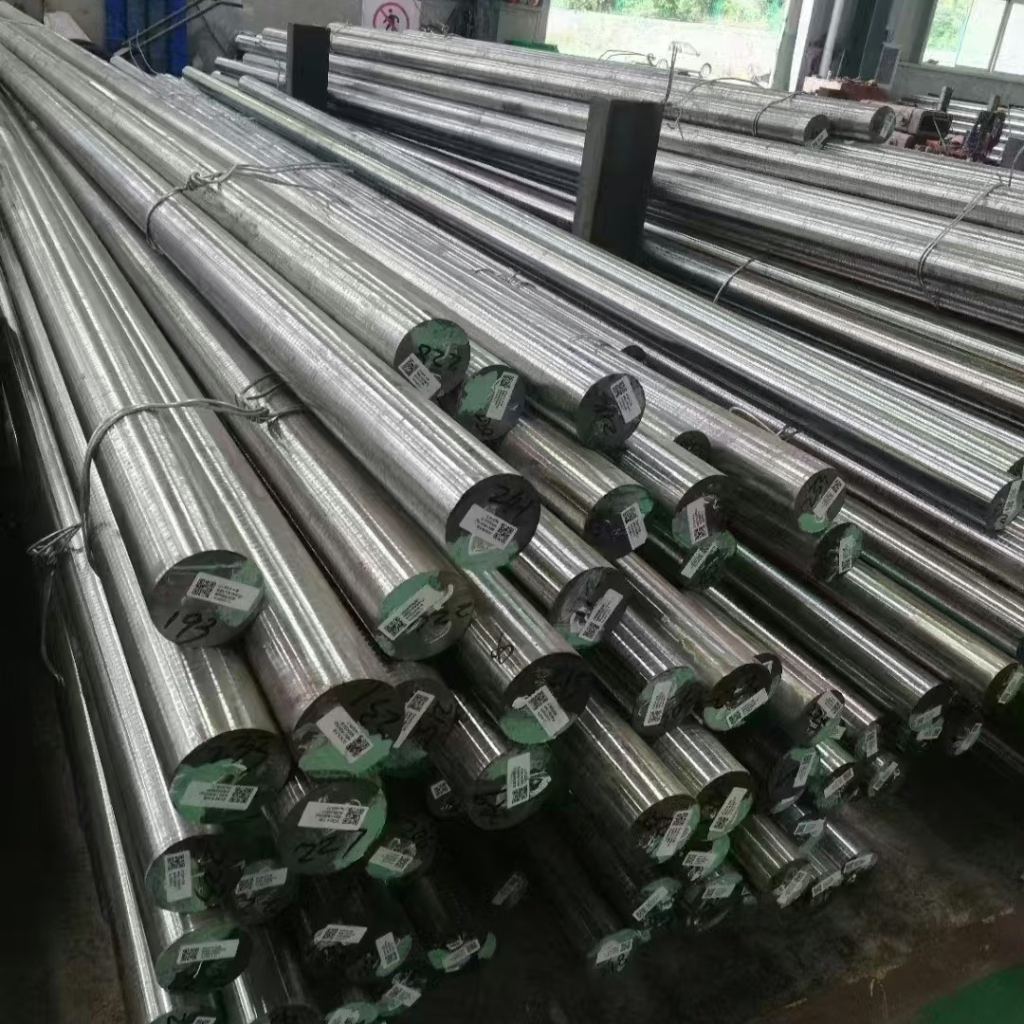
Get a Competitive Quote for 3Cr2W8V Tool Steel
With over 20 years of forging expertise, Aobo Steel is your trusted partner for high-performance 3Cr2W8V tool steel. We provide not just materials, but solutions. Leverage our deep industry knowledge and reliable supply chain for your project’s success.
✉ Contact us by filling out the form below.