The four most common heat treatments are: annealing, normalizing, hardening, and tempering. Hardening and tempering are closely related and are often used in conjunction with each other.
They are often used in conjunction and cannot be used without the other.
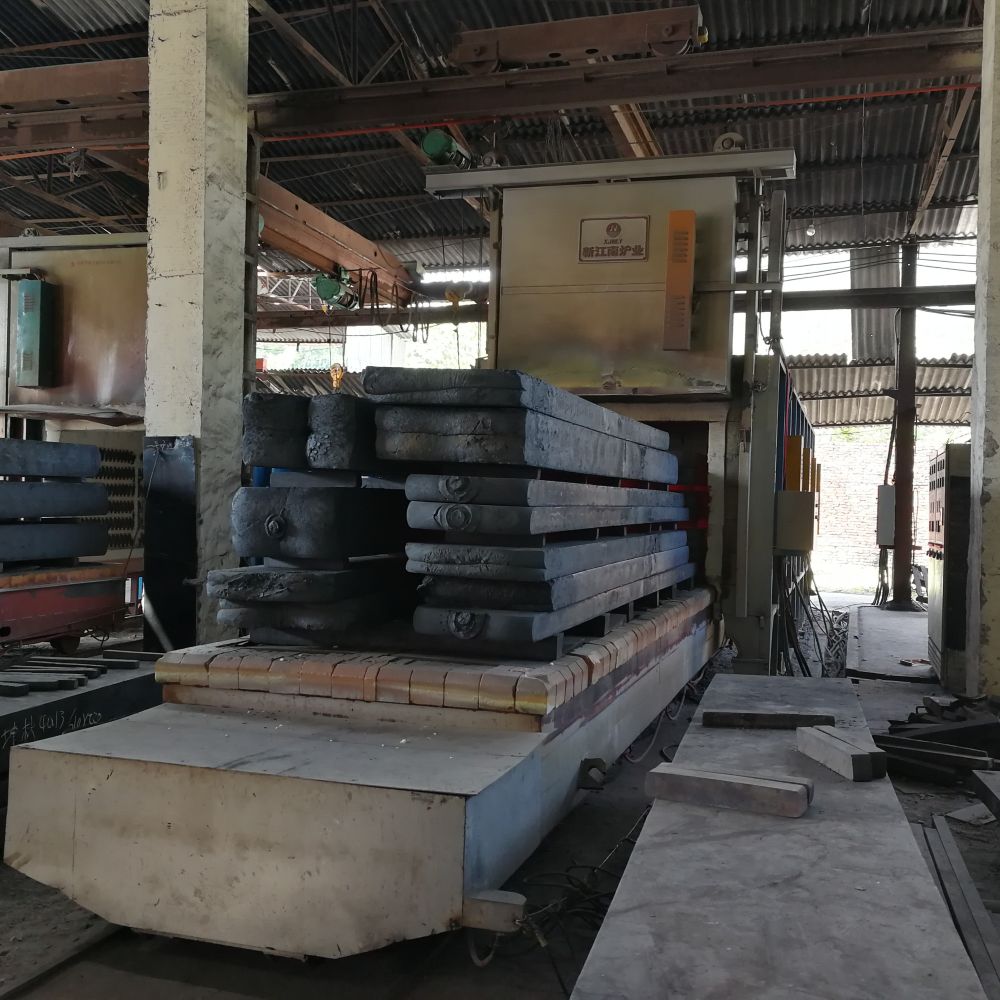
Annealing
Annealing is a heat treating process in which steel is heated to a specific temperature, held for a period of time, typically an hour per inch of thickness, and then slowly cooled in a furnace to room temperature. Its purpose is to improve the microstructure of steel, eliminate defects, reduce hardness, improve plasticity and toughness, and facilitate subsequent processing. Annealing is often used as a preparatory heat treatment for semi-finished products. For example, we Aobo Steel’s P20 steel, a plastic mold steel, is usually used in a pre-hardened state, but annealing can be used to relieve stresses in forging or rolling in preparation for further processing.
Normalizing
Normalizing is a method of heating steel above the austenitizing temperature, holding it, and then cooling it naturally in air (air cooling). It results in finer organization and slightly higher strength and hardness than annealing, while improving productivity. Normalizing is applicable to a wide range of steels, for example:
- D2 and D3 steels: As high-carbon, high-chromium tool steels, normalizing eliminates reticulated carburization and provides the basis for subsequent hardening and tempering.
- O1 and O2 steels: They are oil hardening steels hardened through oil quenching to enhance their durability for industrial applications, and normalized to refine grain and improve cutting and machining properties.
- A2 steel: It is an air hardening steel. Normalizing optimizes the organization and improves toughness.
Hardening
Quenching is the process of heating steel to an austenitizing temperature (high temperatures) and then rapidly cooling it to water, oil, or other media to form a high hardness martensite. The choice of quenching medium depends on the type of steel: water for water hardening steels, oil for oil quenching, or air for air hardening steels. Quenching significantly improves the hardness and wear resistance of steel, but needs to be used in conjunction with tempering. Some of our products are closely related to quenching:
- D2 and D3 steels: High-carbon, high-chromium tool steels, commonly used in stamping dies and cold work molds, require quenching to obtain high hardness.
- A2 steels: air hardening steels for stamping dies and plastic molds, quenched to obtain excellent wear resistance.
- O1 and O2 steels: oil quenched tool steels for cutting tools and stamping dies, oil quenching enhances hardness.
- M2 steel: high speed steels, used for cutting metals, quenching (water quenching in some cases) is its key process to ensure high and red hardness. Here, higher alloy tool steel like M2 benefits from precise quenching techniques.
Tempering
Tempering is a critical step in the heat treatment of tool steels, involving the reheating and cooling of hardened steel for stress relieving and to adjust hardness and toughness. Tempering is categorized into three types depending on the tempering temperature and is applied with Aobo Steel products as follows:
- Low temperature tempering (150 to 250°C)
Maintains high hardness and reduces brittleness, suitable for cutting tools and molds. Example:- O1 and O2 steels: low temperature tempering after oil quenching, used for cutting tools with hardness up to 60 HRC or more.
- M2 steel: low temperature tempering after quenching ensures high hardness and wear resistance for cutting tools. Multiple tempering may be applied to enhance stability.
- Medium temperature tempering (350 to 500°C)
Provide high toughness and elasticity for springs and hot work dies. D2 and D3 steels can be medium temperature tempered in specific applications to balance hardness and toughness. - High temperature tempering (500 to 650°C)
Combined with quenching to form a tempering treatment that balances strength and toughness. Example:- P20 steel: plastic mold steel, usually supplied pre-hardened, but performance can be further enhanced by quenching and high-temperature tempering for injection molds and die casting molds. P20 benefits from a wide range of acceptable tempering temperatures to fine-tune its properties.