S7 tool steel is a popular choice for applications demanding high impact strength and toughness. This guide provides essential information on the Rockwell hardness of S7 tool steel, helping you make informed decisions for your tooling needs.
1. Rockwell Hardness (HRC) and S7 Tool Steel
The Rockwell C scale (HRC) is the industry standard for measuring the hardness of hardened tool steels like S7. Hardness indicates the material’s resistance to indentation and wear. Achieving the correct S7 Rockwell hardness is vital for balancing toughness with wear resistance.
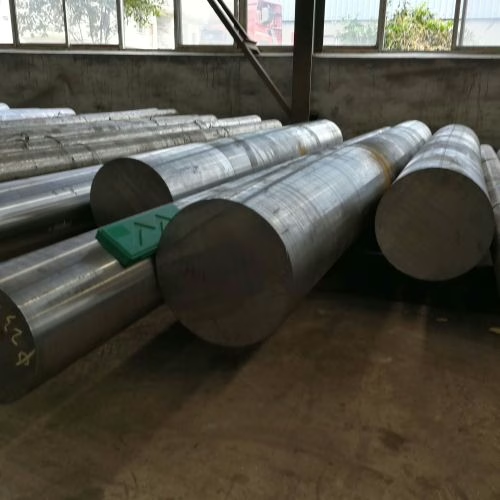
2. S7 Tool Steel Rockwell Hardness Chart and Key Values
While a comprehensive tempering curve showing hardness at every conceivable tempering temperature isn’t typically detailed for S7 in standard references, we can provide the critical Rockwell C hardness values achieved under various common S7 tool steel heat treatment conditions. This information is key for targeting the right properties for your specific application.
S7 Tool Steel: Typical Rockwell C Hardness Values
Treatment / Condition | Typical Tempering Temperature (°F) | Typical Tempering Temperature (°C) | Approximate Rockwell C Hardness (HRC) | Notes |
---|---|---|---|---|
As-Quenched (Air Cooled) | Not Applicable | Not Applicable | 59-60 HRC | Maximum obtainable hardness is typically 60 HRC. |
Tempered for Optimal Working Range | 450°F | 230°C | ~58 HRC | Balances toughness and wear resistance effectively. |
Normal Recommended Working Hardness | 400-450°F | 204-232°C | 56-58 HRC | Preferred range for superior toughness and extended service life. |
Case Hardened Surface (Post Heat Treat) | Not Applicable (Surface Treatment) | Not Applicable (Surface Treatment) | Up to ~64 HRC | Enhances surface wear resistance; may slightly reduce core toughness. |
Nitrided Surface | Not Applicable (Surface Treatment) | Not Applicable (Surface Treatment) | Very High (e.g., ~750 HV equivalent) | Provides excellent surface wear resistance. |
Note: HV (Vickers Hardness) can be converted to an approximate HRC value, but direct HRC measurement is standard for through-hardened S7.
3. Important Considerations for S7 Hardness
- Hardness vs. Toughness: For S7, maximizing hardness isn’t always the goal. Its primary advantage is toughness. Tempering S7 to 56-58 HRC significantly enhances its service life by maintaining superior toughness compared to hardening to 60-61 HRC, which can make the steel more prone to chipping or cracking under impact.
- Application Specifics: The ideal hardness will depend on your specific application. For tools subjected to severe shock, a hardness at the lower end of the working range (around 56-57 HRC) might be preferable. For applications requiring more wear resistance with moderate shock, the higher end (around 58 HRC) could be suitable.
- Surface Treatments: If your application demands exceptional surface wear resistance while maintaining core toughness, treatments like case hardening or nitriding can be considered. However, be aware that case hardening can affect the overall shock resistance.
4. Your Partner for S7 Tool Steel
Understanding the Rockwell hardness of S7 tool steel is key to leveraging its unique properties. At Aobo Steel, with our extensive experience in tool steels, we can help you specify the right S7 material and heat treatment to achieve the performance your factory demands.
Contact us today to discuss your S7 tool steel requirements or if you need further clarification on achieving the optimal hardness for your applications.
Unlock the Power of S7 Tool Steel for Your Applications
Discover the exceptional toughness, superior impact resistance, and excellent machinability of our premium S7 tool steel. Aobo Steel is dedicated to providing high-quality S7 solutions tailored to your precise engineering needs.
Ready to elevate your project? Fill out the form below to connect with our S7 steel specialists and receive your competitive, no-obligation quote today!