H13 steel heat treatment’s purpose is to transform the steel’s microstructure to achieve desired properties such as high hardness, toughness, and superior hot hardness. The heat treatment process for H13, like other tool steels, generally involves four key stages: preheating, austenitizing, quenching, and tempering.
What is H13 steel? H13 tool steel is a steel grade widely used in hot work dies, featuring excellent heat resistance, wear resistance, and resistance to thermal mechanical fatigue. It is commonly used in die casting molds, hot rolling, hot extrusion, and hot forging, among other applications.
The specific heat treatment details for H13 steel are as follows.
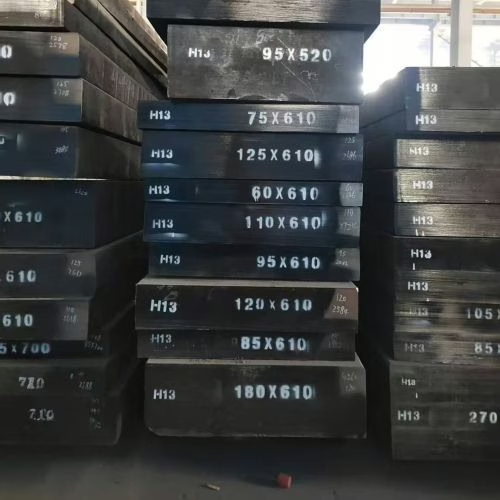
1. Preheating
Preheating is a necessary step for almost all tool steels, including H13. Its purpose is to adjust the internal structure of the material, reduce stress, thereby minimizing thermal shock and reducing the risk of cracking during subsequent high-temperature processing. The preheating temperature for H13 steel is 815°C (1500°F), and it is held for 10 to 15 minutes.
2. Austenitizing (Hardening)
Austenitizing involves heating the H13 steel to a specific high temperature where the desired amount of carbon and alloying elements (like chromium, molybdenum, and vanadium) dissolve into the austenite phase. The hardening temperature for H13 is approximately 1030°C (1885°F). The soak time depends on the cross-section of the part. For parts exceeding 25 mm (1 inch) thick, a general rule is 30 minutes per 25 mm (1 inch) of the smallest cross-section. For smaller parts, soak times range from 10-15 minutes for 3.175 mm (1/8 inch) to 30 minutes for 25 mm (1 inch). It’s crucial not to oversoak, as this can negatively affect the molecular structure.
Higher austenitizing temperatures lead to a greater dissolution of carbides, enriching the austenite with carbon and alloying elements. However, excessively high temperatures can cause grain coarsening, carbide coalescence, and an increase in retained austenite, potentially leading to embrittlement or even melting.
3. Quenching
Quenching rapidly cools the steel from its austenitizing temperature to form martensite.
H13 steel is an air-hardening steel with excellent hardenability. Air hardening minimizes deformation and residual stress. When the temperature of H13 material drops to 66-93°C (150-200°F), it must be immediately transferred to a preheated tempering furnace for tempering. If tempering is not performed promptly, it may cause the material to crack.
4. Tempering
The purpose of tempering is to provide stress relief and improve toughness. H13 is a twice-hardened steel. Through two hardening processes, fine alloy carbides are precipitated from the martensite, thereby improving D2 steel hardness and wear resistance.
The initial tempering temperature for H13 is 565°C (1050°F), and the second tempering temperature is 550°C (1025°F). Between the two tempering processes, it is essential to ensure that the material is cooled to room temperature. Avoid tempering H13 at around 500°C (930°F). Although H13 has high hardness at this temperature, its toughness is too low. High tempering temperatures promote increased precipitation of carbides, which can reduce corrosion resistance but improve hardness stability.
The above is our summary of H13 tool steel heat treatment based on experience and professional papers. We welcome you to contact us and discuss any questions related to H13 steel.
Get a Competitive Quote for H13 Tool Steel
With over 20 years of forging expertise, Aobo Steel is your trusted partner for high-performance H13 tool steel. We provide not just materials, but solutions. Leverage our deep industry knowledge and reliable supply chain for your project’s success.
✉ Contact us by filling out the form below.