9SiCr Tool Steel is a low-alloy tool steel, and its key characteristics come from silicon (Si) and chromium (Cr) being the main alloying elements. The typical chemical composition, by weight percentage (wt%), generally falls within these ranges, although you’ll see slight variations between different standards. The equivalents for 9SiCr steel are DIN 1.2109 / 90SiCr5 in the German standard and AISI L3 in the American standard.
1. Chemical Composition (GB / T 1299—2000) of 9SiCr Steel
C | Si | Mn | Cr | P | S |
0.85 – 0.95 | 1.20 – 1.60 | 0.30 – 0.60 | 0.95 – 1.25 | ≤0.030 | ≤0.030 |
2. Physical Properties of 9SiCr Steel
2.1 Critical Point Temperatures
Critical Point | Ac₁ | Acₑₘ | Ar₁ | Ms |
Temperature (approx. value) / °C | 770 | 870 | 730 | 160 |
2.2 Other Physical Properties
Density / (g/cm³) | Coercivity / (A/m) | Saturation Magnetic Induction / T |
7.80 | 795.8 | 1.78 – 1.82 |
3. Forging Process of 9SiCr Steel
Forging Process Specification
Item | Heating Temperature / °C | Initial Forging Temperature / °C | Final Forging Temperature / °C | Cooling |
Steel Ingot | 1150 – 1200 | 1100 – 1150 | 880 – 800 | Slow cooling (in sand or pit) |
Steel Billet | 1100 – 1150 | 1050 – 1100 | 850 – 800 | Slow cooling (in sand or pit) |
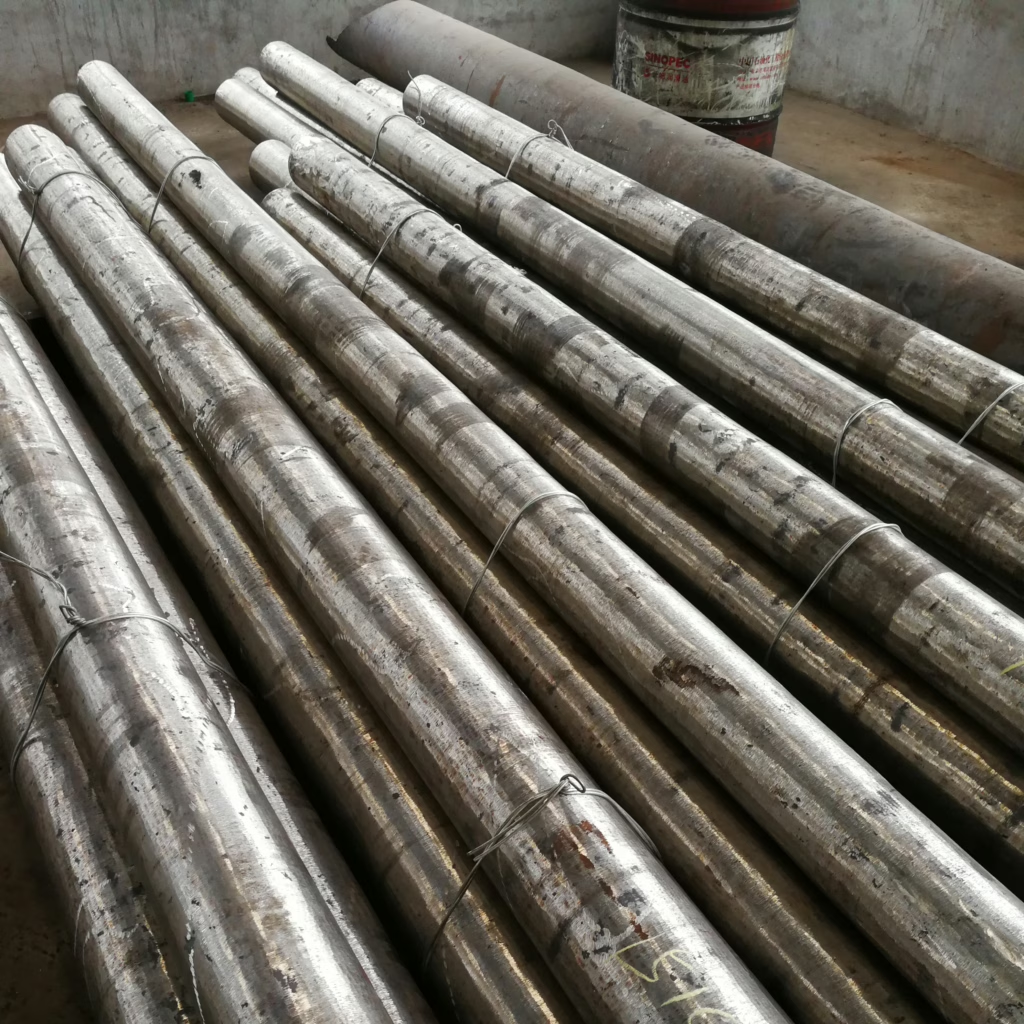
Please fill out the following form to contact us for 9SiCr steel
4. Heat Treatment of 9SiCr Steel
4.1 Preheating
Preliminary Heat Treatment Plan | Process Parameters |
Post-forging Annealing | Heating temperature 790 – 810°C, hold for 1-2h; furnace cool to below 550°C then air cool. Hardness after annealing: 197 – 241 HBW. |
Post-forging Isothermal Annealing | Heating temperature 790 – 810°C, hold for 1-2h; isothermal temperature 700 – 720°C, furnace cool to below 550°C then air cool. Hardness: 197 – 241 HBW. |
High-temperature Tempering | Heating temperature 600 – 700°C, hold for 2-4h; furnace cool or air cool. Hardness: 197 – 241 HBW. Used to eliminate work hardening from cold deformation. |
Normalizing | Heating temperature 900 – 920°C, air cool. Hardness: 321 – 415 HBW. Used to refine the grains of overheated steel and eliminate network carbides. |
Quenching and Tempering | Heating temperature 880 – 900°C, tempering temperature 680 – 700°C, hold for 2-4h; furnace cool or air cool. Hardness: 197 – 241 HBW. |
Hardness and Microstructure Before and After Annealing
Indentation Diameter/mm | Phase Composition (Mass Fraction, %) | Microstructure | ||||||
Before Annealing | After Annealing | Ferrite | Carbide | Carbide Form | Before Annealing | After Annealing | ||
Indentation Diameter/mm | HBW | Indentation Diameter / mm | HBW | |||||
3.0 – 3.4 | 415 – 321 | 3.9 – 4.3 | 241 – 197 | 87.3 – 85.8 | 12.7 – 14.2 | Fe₃C | Troostite + Sorbite | Spheroidite |
4.2 Quenching
Plan | Quenching Temp. / °C | Cooling | Hardness HRC | |||
Coolant | Coolant Temp. / °C | Duration | Cool to room temp | |||
I | 860 – 880 | Oil | 20 – 40 | To oil temperature | Air | 62 – 65 |
II | 860 – 880 | Oil | 80 – 140 | To 150 – 200°C | Air | 62 – 65 |
III | 860 – 880 | Molten nitrate salt or alkali | 150 – 200 | 3 – 5 min | Air | 61 – 63 |
IV | 860 – 880 | Molten nitrate salt or alkali | 150 – 200 | 30 – 60 min | Air | 59 – 62 |
Note: For workpieces with complex shapes and small deformation requirements, use plans III and IV.
4.3 Cold Treatment Specification
Quenching Plan | Cooling Temperature / °C | Purpose | Hardness Increase HRC |
I – III | -70 | High-precision tools, dimensional stabilization of molds | 0 – 1 |
Note: Cold treatment should be carried out within 1 hour after quenching.
5. Tempering
5.1 Tempering process specifications
Plan | Purpose of Tempering | Heating Temperature / °C | Heating Medium | Hardness HRC |
I | Stress relief, stabilize microstructure | 140 – 160 | Oil, saltpeter, alkali | 62 – 65 |
160 – 180 | 61 – 63 | |||
180 – 200 | 60 – 62 | |||
200 – 220 | 58 – 62 | |||
II | Stress relief, reduce hardness | Per hardness requirement | Saltpeter, alkali, air furnace | Per the hardness requirement |
Notes:
- For high-precision (1-2μm) workpieces, tempering (aging) should be performed after rough grinding.
- For tempering above 250°C, the dimensional stability of the workpiece can be guaranteed without cold treatment.
5.2 Relationship between tempering temperature and hardness
Tempering Temperature/°C | 100 | 150 | 200 | 250 | 300 | 350 | 400 | 450 | 500 | 600 |
Hardness HRC | 64 | 63 | 62 | 60 | 59 | 58 | 55 | 51 | 47 | 40 |
Note: 870°C oil quenching, tempering for 2h.
6. Mechanical Properties
9SiCr steel contains Si and Cr elements, giving it high hardenability, quenching hardness, and high resistance to tempering. This is beneficial for improving wear resistance and resistance to plastic deformation. When tempered at 300-400°C, the hardness can be maintained at around 60 HRC, exhibiting good wear resistance and toughness. However, this steel is prone to decarburization, and measures should be taken to prevent oxidative decarburization during quench heating.
Mechanical Properties of 9SiCr Steel at Different Temperatures
Temperature | Tension | Compression | Torsion | Impact Toughness | Hardness | |||||
(°C) | ReL | Rm | A (%) | Z (%) | Compressive Strength (MPa) | T (N·m) | φ (°) | l (%) | aKV / (J/ cm 2 ) | HBW |
20 | 456 | 805 | 26.2 | 54.2 | 3610 | 155 | 435 | 7.7 | 40 | 243 |
200 | 330 | 722 | 21.9 | 47.7 | 2660 | 141 | 396 | 6.9 | 90 | 218 |
400 | 335 | 635 | 32 | 63.4 | 1830 | 144 | 332 | 6.6 | 100 | 213 |
600 | 176 | 207 | 51.5 | 76.8 | 1900 | 64 | 1990 | 32.9 | 90 | 172 |
700 | 85 | 100 | 58 | 77.2 | 27 | 2270 | 39.5 | 150 | 53 | |
750 | 73 | 102 | 59.3 | 68.4 | 223 | 370 | 44.6 | |||
800 | 67 | 87 | 70.6 | 62.5 | 265 | 12 | 3300 | 57.4 | 360 | 29.3 |
850 | 46 | 67 | 51 | 48.3 | 230 | 320 | 33.6 | |||
900 | 42 | 52 | 39.7 | 30.2 | 265 | 11.5 | 2250 | 39.2 | 280 | 22.7 |
1000 | 24 | 30 | 22 | 26.7 | 7.5 | 935 | 16.3 | 222 | 19 | |
1100 | 15 | 20 | 41.5 | 53 | 4 | 1390 | 24.2 | 158 | 7.4 | |
1200 | 6 | 11 | 87 | 100 | 106 | 4.2 | ||||
1250 | 7 | 9.7 | 56.5 | 100 | 77 | |||||
1300 | 6 | 7 | 46.5 | 87 |
7. Applications
9SiCr steel is a low-alloy tool steel. It has high hardenability and tempering resistance, and is suitable for martempering or austempering. It is commonly used to manufacture high-speed cutting tools with high wear resistance requirements and cold work dies with complex shapes, small deformation requirements, and high wear resistance, such as:
- Coining dies
- Hand reamers
- Shear blades
- Thread rolling plates
- Cold rolling rolls
- Straightening rolls
- Thread rolling dies
- Drawing dies
- Stamping dies
- Cold heading dies
Get a Competitive Quote for 9SiCr tool steel
With over 20 years of forging expertise, Aobo Steel is your trusted partner for high-performance 9SiCr tool steel. We provide not just materials, but solutions. Leverage our deep industry knowledge and reliable supply chain for your project’s success.
✉ Contact us by filling out the form below.
Explore Our Other Products
D2/1.2379/SKD11
D3/1.2080/SKD1
D6/1.2436/SKD2
A2/1.23663/SKD12
O1/1.2510/SKS3
O2/1.2842
S1/1.2550
S7/1.2355
DC53
H13/1.2344/SKD61
H11/1.2343/SKD6
H21/1.2581/SKD7
L6/1.2714/SKT4
M2/1.3343/SKH51
M35/1.3243/SKH55
M42/1.3247/SKH59
P20/1.2311
P20+Ni/1.2738
420/1.2083/2Cr13
422 stainless steel
52100 bearing steel
440C stainless steel
4140/42CrMo4/SCM440
4340/34CrNiMo6/1.6582
4130
5140/42Cr4/SCR440
SCM415