420 stainless steel is a martensitic stainless steel, which is a type of iron-chromium alloy. It is part of the 400-series stainless steel classifications. Unlike some other stainless steel types, AISI 420 stainless steel is magnetic.
1. Applications
- Cutlery and Sharp-edged Tools
- Medical and Surgical Instruments
- Plastic Molds and Mold Tools
- Valve and Pump Parts
- Gears, Shafts, and Rollers
- Industrial and Wear-Resistant Applications
- Cups and Other Formed Parts
- Bearings
- Other Applications: Springs, Hand Tools, Magnets, Fasteners, Machinery Parts, Press Plates, Automotive exhaust components, Dies for fine piercing of micropatterns into metallic sheets, Domestic appliances and utensils.
2. 420 Stainless Steel Composition1
Element | Carbon (C) | Manganese (Mn) | Silicon (Si) | Phosphorus (P) | Sulfur (S) | Chromium (Cr) |
Compositional | 0.15- 0.40% | ≤ 1.00% | ≤ 0.50% | ≤ 0.040% | ≤ 0.030% | 12.00 – 14.00% |
3. 420 Stainless Steel Properties
- Hardness and Wear Resistance: After appropriate heat treatment, 420 stainless steel has a hardness of 46–52 HRC. This hardness gives it good wear and corrosion resistance.
- Corrosion Resistance: The chromium in AISI 420 stainless steel forms a passivation layer that protects its surface and provides excellent corrosion resistance in mild atmospheric, domestic, and industrial environments.
- Polishability: This grade exhibits excellent polishability, making it a preferred choice for applications requiring a high-quality surface finish, such as plastic injection molds and optical components.
- Toughness and Weldability: The carbon content is higher than that of low-carbon steel, making it harder than low-carbon steel but with lower toughness. Due to its high carbon content, it also has poor weldability. If welding is necessary, significant preheating and post-weld heat treatments (like annealing) are often required to prevent cracking. Using specialized filler metals (e.g., ERNiCr-3) might be considered, though this can affect the final strength and hardness of the weld area.
- Machinability: In its annealed condition, 420 steel offers fair machinability. For applications demanding more complex machining, a free-machining variant, 420F (with added sulfur), is available. Note that the sulfur addition can slightly decrease notch toughness.
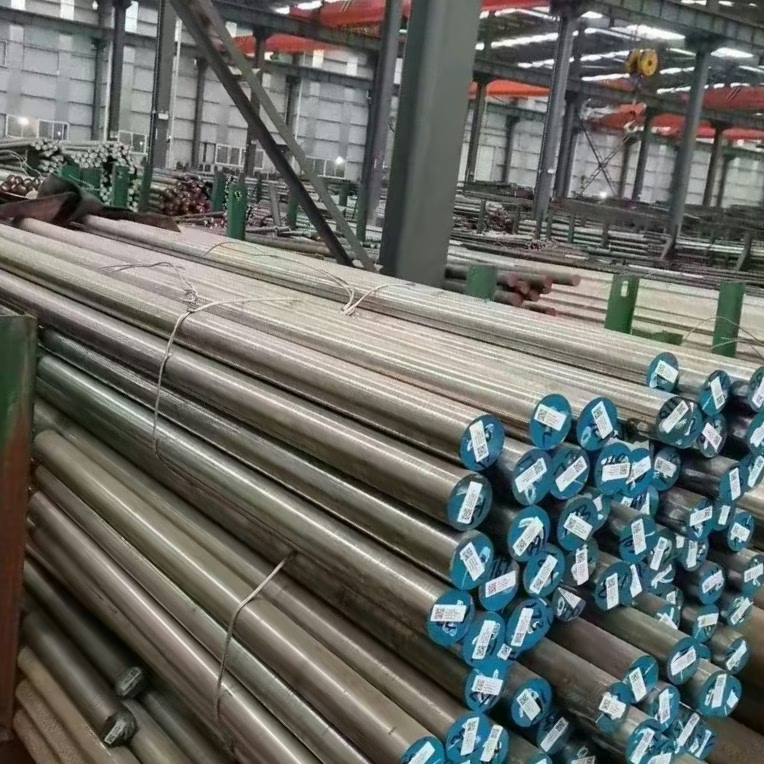
Interested in AISI 420 stainless steel? Please fill out the form below to contact us now!
4. Heat Treatment
Martensitic stainless steels, including 420 stainless steel, are hardened by heating them above their transformation temperature to achieve a fully austenitic structure, followed by rapid cooling in oil or air. It has a low thermal conductivity, which can lead to uneven heating during rapid heating or quenching, resulting in distortion, warping, or cracking. Therefore, we strongly recommend preheating.
The 420 stainless steel heat treatment involves austenitizing, quenching, and then tempering to optimize its mechanical properties, particularly ductility and toughness.
4.1 Hardening(Austenitizing)
The hardening temperature for 420 steel is 975 °C to 1075 °C (1787 °F to 1967 °F), though some sources list it as 954 °C to 1010 °C (1750 °F to 1850 °F). However, based on our experience, the former range is more appropriate.
Soak time is typically about 30 minutes per inch (1.2 minutes per millimeter) of thickness at the hardening temperature.
To prevent decarburization, 420 stainless steel should be hardened in a controlled neutral atmosphere, vacuum, or neutral-salt furnace environment.
4.2 Quenching
For complex or irregularly shaped workpieces, we suggest air quenching to minimize deformation and reduce the risk of cracking. If a higher hardness is required, we opt for oil quenching. The quenching process involves cooling the material to 66 °C (150 °F) when air-quenched, or to 66-93 °C (150-200 °F) when oil-quenched. Please note that the tempering treatment should be performed immediately after quenching.
4.3 Tempering
Tempering can improve the toughness and strength of 420 and adjust its hardness. 420 steel material must undergo at least two tempering cycles, or even three. For most applications, the minimum tempering temperature is 204°C (400°F). The soaking time is 2 hours per inch (4.7 minutes per millimeter) of thickness at the specified temperature. Between each tempering cycle, the parts should be allowed to cool naturally to room temperature.
Effect of Tempering Temperature on Properties:
- Hardness after different tempering temperatures: Hardness of 420 stainless steel is: 52 HRC minimum at 149 °C (300 °F), 50 HRC minimum at 204 °C (400 °F), and 48 HRC minimum at 316 °C (600 °F).
- Temper Embrittlement and Corrosion Resistance: 420 steel has the characteristic of temper embrittlement. Do NOT temper at temperatures ABOVE 427°C (800°F), as this temperature range may result in a significant decrease in impact strength and corrosion resistance. This reduction is attributed to the precipitation of coarser chromium carbides (Cr23C6), which can create chromium-depleted regions around the carbides. This negative effect disappears when the tempering temperature is 593 °C (1100 °F) or higher. At temperatures above 600 °C, chromium diffusion is thought to “heal” these depleted zones, restoring corrosion resistance. Within this temperature range, the toughness of 420 increases, but its hardness decreases.
4.4 Stress Relieving (Unhardened Material)2
For unhardened 420 stainless steel parts, stress relieving can be performed by heating slowly to 677 °C (1250 °F) and soaking for 2 hours per inch of thickness, followed by a slow cool in the furnace to room temperature.
5. Equivalent Grades
- JIS (Japan):SUS420J1, SUS420J2
- DIN (Germany):4021, 1.4028, 1.2083 (X42Cr13 – often used for molds)
- GB(China): 2Cr13 and 4Cr13.
6. Compare 420 stainless steel with other steels
6.1 420 stainless steel vs 304
420 steel is a hard, strong, wear-resistant, and magnetic martensitic alloy, best suited for applications requiring high performance after heat treatment. However, it requires careful handling during welding and tempering for optimal corrosion resistance. 304 steel, on the other hand, is a ductile, formable, generally non-magnetic austenitic alloy prized for its versatile corrosion resistance, excellent weldability, and suitability for a broad range of general and high-temperature applications. For more information on this topic, please refer to the comparison between 420 stainless steel and 304.
Feature | 420 | 304 |
Classification | Martensitic | Austenitic |
Magnetic? | Yes (Ferromagnetic) | Typically No (Non-magnetic in annealed condition) |
Hardenable? | Yes, by heat treatment (quench and temper) | No, hardens by cold work |
Carbon Content | Higher (0.15% min, often 0.2-0.4%) | Lower (max 0.08%) |
Nickel Content | Very low or absent | Significant (8-12%) |
Max Hardness | Much higher (e.g., C-54 to C-60 after heat treat) | Lower (max B-92 annealed) |
Corrosion | Moderate, dependent on heat treatment; lower than 304 | Good, “best all-rounder”; higher than 420 |
Weldability | Difficult to weld | Excellent weldability (especially 304L) |
Toughness | Lower impact strength, susceptible to temper brittleness | High ductility and toughness |
Typical Uses | Cutlery, surgical instruments, molds, shafts, valves | Food processing, appliances, automotive exhaust, general purpose |
6.2 420 stainless steel vs 316
420 steel is a hardenable martensitic stainless steel with high strength, hardness, and wear resistance, but it has moderate corrosion resistance and is sensitive to heat treatment. In contrast, 316 steel is a non-hardenable austenitic stainless steel with excellent corrosion resistance, particularly in chloride environments, where it exhibits outstanding resistance to pitting and crevice corrosion. For more information about this topic, please refer to 420 stainless steel vs 316
Feature | 420 | 316 |
Classification | Martensitic | Austenitic |
Hardenability | Can be hardened by heat treatment to over 50 HRC. | Cannot be hardened by heat treatment; can be hardened by cold working. |
Hardness | Annealed: B-92 Rockwell. Heat-treated: C-54 Rockwell. | Annealed: B-80 Rockwell (up to B-90). |
Tensile Strength | Annealed: 95 ksi. Heat-treated: up to 250 ksi. | Annealed: 75 ksi (316), 70 ksi (316L). |
Yield Strength | Annealed: 50 ksi. Heat-treated: up to 200 ksi. | Annealed: 30 ksi (316), 25 ksi (316L). |
Ductility | Good toughness, but ductility decreases as hardness increases. | Excellent ductility and high elongation, even at low temperatures. |
Corrosion Resistance | Good, but generally lower than austenitic grades. Tempering can reduce resistance. | Excellent, especially against pitting and crevice corrosion due to molybdenum. |
Weldability | Difficult to weld; not recommended for welded applications. | Good weldability, especially the ‘L’ grade (316L). |
Magnetic Properties | Ferromagnetic. | Generally non-magnetic (can be slightly magnetic after cold work). |
Common Applications | Cutlery, surgical instruments, molds, shafts, valve parts. | Chemical processing, marine applications, architectural cladding, medical implants. |
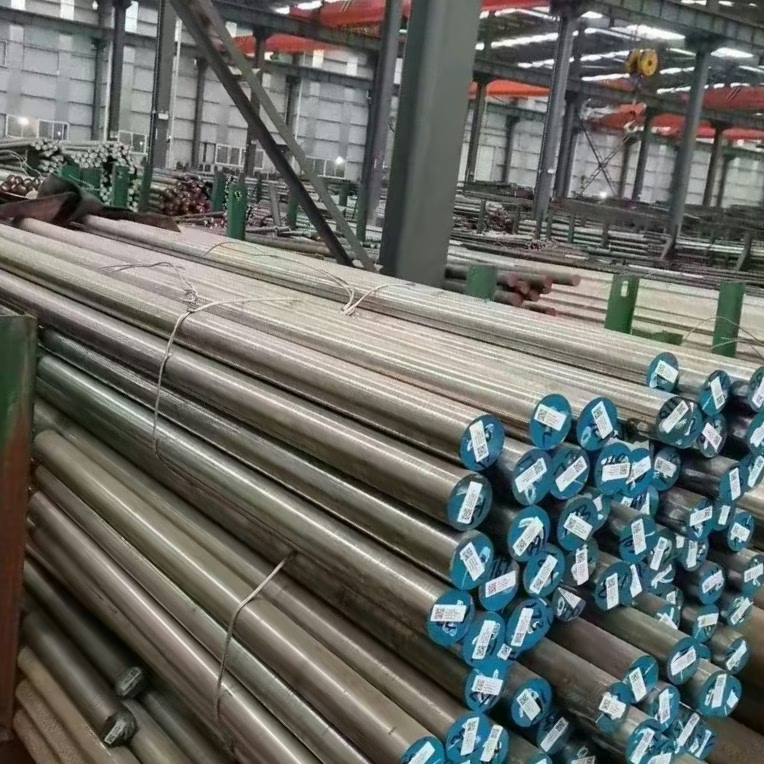
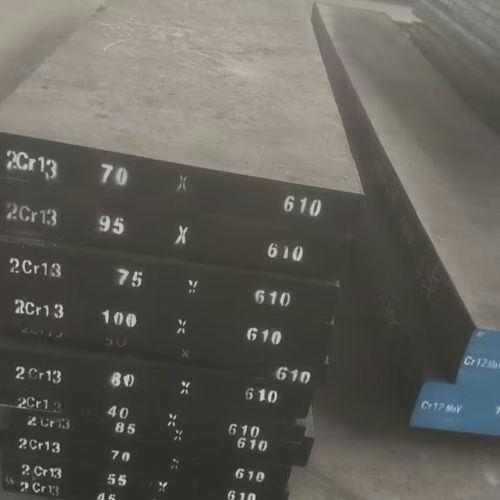
- Bringas, J. E. (Ed.). (2004). Handbook of Comparative World Steel Standards (3rd ed., p. 434). ASTM International. ↩︎
- Leed, R. M. (2007). Tool and die making troubleshooter. Society of Manufacturing Engineers. ↩︎
FAQs
420 stainless steel is a martensitic stainless steel and is also the most commonly used martensitic stainless steel. It has similar corrosion resistance to 410 stainless steel, but with higher strength and hardness. It is also widely known as “cutlery stainless steel.”
It has a hardness of 52-55 HRC (or Rockwell C55 when hardened and stress relieved), a density of 0.280 lbs/in³ (7.74 g/cm³), and a tensile strength of 275,000 psi (230 ksi or 1586 MPa when hardened and stress relieved). It is magnetic in both annealed and hardened conditions. Additionally, it possesses good machining properties, is hardenable, polishable, and conditionally acid-resistant.
Its chemical makeup typically includes Carbon (C) at 0.15 – 0.36% (or 0.15% minimum, extending up to 0.5% in some variations), Chromium (Cr) at 12 – 14%, and a maximum of 1.0% each for Silicon (Si) and Manganese (Mn). Phosphorus (P) is typically 0.04% Max, and Sulphur (S) is 0.03% Max.
420 stainless steel has excellent corrosion resistance. It can resist corrosion from the atmosphere, fresh water, steam, gasoline, alcohol, blood, sweat, grease, and food.
Yes, 420 stainless steel is attracted to a magnet and is magnetic in both its annealed and hardened states.
The hardness of 420 stainless steel ranges from 52 to 55 HRC.
420 stainless steel has several equivalent international standards, including AISI 420, BS970 420S37, 420S45, DIN 1.4021, 1.4025, 1.4034, AFNOR Z30C13, Z40C14, and JIS SUS 4200JI, 420J2. It is also covered by ASTM A 176 and AMS 5506 specifications, and its UNS number is S42000.
Typical uses include bearing manufacture, valve parts, hose connectors & fittings. It is also widely used for cutlery, surgical and dental instruments, scissors, tapes, and straight edges. It is considered ideal for applications that demand both good corrosion resistance and high hardness.
Yes, 420 stainless steel, particularly the 420HC (High Carbon) variant with proper heat treatment, is considered suitable and can be an excellent steel for knives. While some generic 420 might be considered outdated for general-use knives due to its softness and poorer edge retention, 420HC is known for being tough, stainless, easy to sharpen, and having respectable edge retention. Companies like Buck Knives have achieved solid performance with 420HC through specialized heat treatments. Learn more about this article, please refer to Is 420 stainless steel good for knives?
While often referred to as “budget steel because it is an older alloy, 420 stainless steel is not necessarily low-quality. Its performance heavily relies on the heat treatment it receives; with proper heat treatment (especially for 420HC), it can be a solid, usable, and even underrated performer for real-world use. It offers good corrosion resistance, toughness, and ease of sharpening, making it a viable option for everyday carry (EDC) knives.
No, 420 stainless steel is generally not recommended for functional swords and is often found in “wall hangers” (decorative swords). The carbon content of 420 can be fairly low, making the blade softer. Functional swords are typically made from carbon steel because it is cheaper, easier to forge, and easier to heat treat for the required performance. Stainless steel swords are broadly viewed as too brittle and prone to chipping or shattering for practical use.
There are conflicting views on the compatibility of stainless steel (including 420) with aluminum, particularly in exterior or wet environments, due to the risk of galvanic corrosion. Some sources indicate that stainless steel can be worse than galvanized steel when in contact with aluminum, leading to severe aluminum corrosion in marine or wet conditions. Conversely, other sources suggest stainless steel bolts might be used to avoid galvanic reactions, or that reactions are minimal in mild conditions due to aluminum’s protective oxide layer. To mitigate potential galvanic corrosion, it is widely recommended to use isolation washers made of plastic or rubber between the two metals to minimize direct contact.
Heat treatment is crucial for enhancing the performance characteristics of 420 stainless steel. Its maximum corrosion resistance is achieved only when the steel is fully hardened or hardened and stress-relieved; it is generally never used in the annealed condition for optimal corrosion resistance. Proper heat treatment can significantly improve properties such as hardness and edge retention, especially for variant 420HC. When 420 is soft (annealed), it is flexible; when hardened, it becomes quite hard.
Standard heat treatment processes for 420 stainless steel include:
Annealing (for maximum softness): Heat uniformly to 1500 – 1650°F (816 – 899°C) and cool slowly in the furnace.
Process Annealing: Heat to 1350 – 1450°F (732 – 788°C), then air cool.
Hardening: Preheat, then heat to 1800 – 1950°F (982 – 1066°C), soak at the temperature, and then air cool or quench in warm oil.
Stress Relieving: Heat at 300 – 800°F (149 – 427°C) for 1 to 3 hours, then cool in air or quench in oil or water.
Martensitic stainless steel series, including type 420, has limited weldability. If welding is required, it is recommended to preheat to 550°F (260°C). It is also recommended to perform heat treatment after welding.
Yes, if 420 stainless steel is annealed for maximum softness, it can be moderately drawn and formed.
420 stainless steel is not typically used at temperatures exceeding 800°F (427°C). This is because higher temperatures lead to rapid softening and a loss of its corrosion resistance.
The key difference lies in their carbon content, which significantly impacts their performance. Generic 420 (and 420J) typically has a lower carbon content, around 0.15%. In contrast, 420HC (High Carbon) has a notably higher carbon content, usually around 0.46%. This higher carbon content, especially when combined with specialized heat treatment, provides 420HC with improved hardness, better edge retention, and more robust performance for applications like knives. The variation in carbon content among different 420 grades explains why sources may report different carbon percentages for “420” steel.
Both 420 and 440 are generally considered decent and usable “budget” stainless steels. 420 (specifically 420HC) is described as very tough with respectable edge retention. 440 (particularly 440C) can achieve higher hardness (58 HRC or above) and typically offers better edge retention, though it may not be as tough as 420. 440C is also a corrosion-resistant martensitic chromium steel with high wear resistance. The specific grade and heat treatment are important for comparing their actual performance.
While 420 stainless steel offers good corrosion resistance compared to other cutlery steels, its corrosion resistance is inferior to 316 stainless steel. SAE 316 and 316L (often called “marine grade”) are chromium, nickel, molybdenum alloys known for their superior strength and corrosion resistance, and are considered biocompatible when produced to specific standards.
420 steel is indeed a good stainless steel, offering a satisfactory level of corrosion resistance for a wide range of applications, particularly when properly heat-treated. Its combination of corrosion resistance with achievable high hardness and wear resistance makes it a versatile material, notably for cutlery and certain tooling applications.
Get a Competitive Quote for 420 stainless steel
With over 20 years of forging expertise, Aobo Steel is your trusted partner for high-performance 420 stainless steel. We provide not just materials, but solutions. Leverage our deep industry knowledge and reliable supply chain for your project’s success.
✉ Contact us by filling out the form below.
Explore Our Other Products
D2/1.2379/SKD11
D3/1.2080/SKD1
D6/1.2436/SKD2
A2/1.23663/SKD12
O1/1.2510/SKS3
O2/1.2842
S1/1.2550
S7/1.2355
DC53
H13/1.2344/SKD61
H11/1.2343/SKD6
H21/1.2581/SKD7
L6/1.2714/SKT4
M2/1.3343/SKH51
M35/1.3243/SKH55
M42/1.3247/SKH59
P20/1.2311
P20+Ni/1.2738
420/1.2083/2Cr13
422 stainless steel
52100 bearing steel
440C stainless steel
4140/42CrMo4/SCM440
4340/34CrNiMo6/1.6582
4130
5140/42Cr4/SCR440
SCM415