At Aobo Steel, with our decades of experience in tool steel, we often discuss the practical aspects of using different grades. A common issue that arises is the difficulty some users encounter when sharpening D2 tool steel. Let’s look into the technical reasons for this.
D2 steel is a high-carbon, high-chromium cold-work tool steel. Its formulation provides exceptional abrasion resistance and dimensional stability after heat treatment. For these specific characteristics, D2 is often regarded as the industry standard.
However, the very properties that make D2 excellent for demanding cold-work tasks and long production runs are exactly what make it challenging to sharpen. Simply put, D2 is engineered to resist wear and tear. Sharpening, by its nature, is a process of controlled wear that removes material through the action of abrasion.
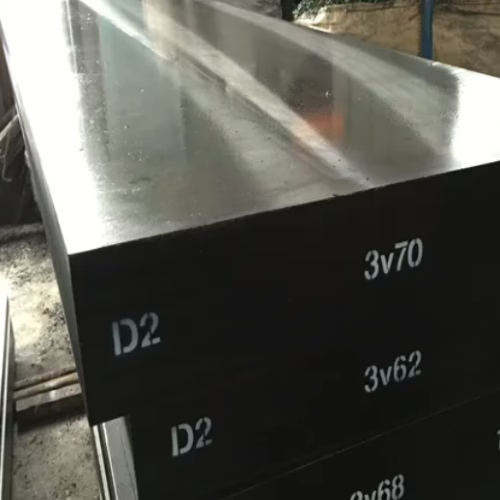
Understanding the Metallurgy
To understand why D2 resists sharpening, we need to look at its composition and structure:
- D2 Steel Composition: D2 has a high carbon content (typically 1.5% or more) and a high chromium content (around 12%). It often contains molybdenum and sometimes also vanadium. This specific mix of alloys, particularly the high carbon and chromium content, defines its performance.
- Microstructure: After undergoing the correct heat treatment, D2 develops a microstructure characterized by a matrix of tempered high-carbon martensite. Within this matrix, a large volume (approximately 13%) of dispersed, very hard alloy carbides is present, primarily chromium-rich M7C3 carbides.
- Hardness: D2 steel hardness is from 56 to 64 HRC. This hardness gives D2 its excellent wear resistance.
The Sharpening Challenge
The difficulty in sharpening D2 comes directly from this combination of high overall hardness and the presence of those extremely hard carbide particles.
- Filing: Attempting to use a standard file on hardened D2 is generally ineffective. The file often struggles to “bite” into the steel and may simply slide over the surface. Materials this hard require grinding, not filing.
- Grinding: Grinding is the necessary method for hardened tool steels such as D2 steel. However, D2 steel’s high abrasion resistance makes grinding itself a challenge. The grinding abrasive must constantly cut through the hard carbide particles, which resist being removed. D2 steel is known to be difficult to work with and grind precisely due to its high chromium and carbon content. Its machinability rating is significantly lower than simpler carbon steels, even in its softer, annealed state. Once hardened, conventional machining is usually not practical.
Important Considerations for Grinding D2 Steel
Grinding hard, high-carbon steels like D2 tool steel requires careful control. Applying too much pressure or speed can generate excessive localized heat on the surface. If the temperature becomes too high, the surface can re-harden incorrectly upon cooling, resulting in a thin, brittle layer of untempered martensite. This layer can contain micro-cracks, acting as stress points that could lead to tool failure later during use. This potential issue adds complexity to the sharpening process, demanding precision.
In Summary
D2 tool steel is challenging to sharpen because it is metallurgically designed for maximum wear resistance. Its high carbon and chromium content creates a hard structure filled with extremely hard carbide particles. This inherent abrasion resistance, combined with the need for careful grinding techniques to avoid surface damage, makes sharpening D2 a more demanding and time-consuming task compared to sharpening less wear-resistant steel grades. Understanding these properties helps in selecting the appropriate tools and techniques for effectively maintaining D2 components.