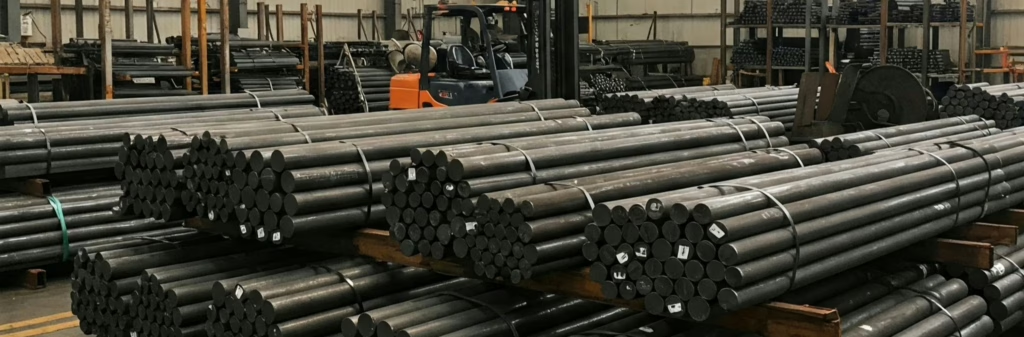
Tool Steel Product Catalog
Our Tool Steel Catalog
Click on any product to view details.
What is tool steel
It is a special steel alloy specifically used for manufacturing tools, dies, and molds. These tools, dies, and molds are used to cut, form, process, or stamp other materials, including ferrous metals, non-ferrous metals, plastics, wood, paper, rock, or concrete. Tool steel has good strength, toughness, hardness, wear resistance, and quenching stability. Depending on its application, tool steel can be divided into cutting-edge steel, mold steel, and measuring steel. Based on its chemical composition, it can be divided into carbon steel, alloy steel, and high-speed steel.
The main properties of tool steel include hardness, wear resistance, strength, toughness, machinability, quenching temperature range, hardenability, decarburization sensitivity, heat treatment deformation, grinding performance, etc. Among these, high hardness and wear resistance are the most important properties. Through quenching and heat treatment, the hardness and wear resistance can be significantly improved.

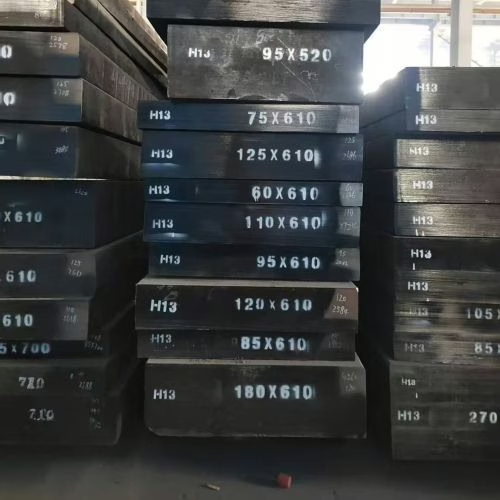
Composition
It is a complex iron-based alloy containing varying proportions of alloying elements, including carbon, chromium, vanadium, molybdenum, tungsten, nickel, manganese, and silicon.
The main functions of these alloying elements include:
- Carbon (C): The major alloying element, typically ranging from 0.6% to 2.40% in high-carbon steels and tool steels, is crucial for achieving high hardness through martensite formation and influencing carbide precipitation.
- Chromium (Cr): Improves hardenability, wear, corrosion, and oxidation resistance, polishability, and high-temperature properties. It is an excellent carbide former and raises hardening temperatures. Found in various types, including high-chromium cold-work steels and chromium hot-work steels.
- Vanadium (V): A strong carbide former, especially forms vanadium-rich MC type carbides, which significantly enhance wear resistance.
- Molybdenum (Mo): Adds heat resistance and hardenability. It is a carbide former and, along with tungsten, prevents softening during tempering.
- Tungsten (W): Similar to molybdenum, it is a carbide former that significantly contributes to hot hardness and wear resistance. Tungsten-rich M6C type carbides are common.
- Cobalt (Co): Imparts heat resistance (hot hardness) and is often added to high-speed steels to improve high-temperature hardness.
- Manganese (Mn): A deoxidizer that increases hardenability, even in small amounts, for carbon tool steels.
- Silicon (Si): Improves toughness in low-alloy tool steels, raises critical points in hot-work tool steels, reduces scaling, and increases hardenability and resistance to tempering. It can also promote graphite formation for improved machinability.
Key Properties
The choice of tool steel depends on the specific application, and no single tool steel can meet all requirements. The main properties of mold steel include:
- High Hardness and Wear Resistance. Hardness is the ability to resist penetration or withstand abrasion. It is generally a function of the tool’s hardness and its specific alloy content or type of carbide. Higher hardness typically improves strength and wear resistance, but can lower toughness. Wear resistance is primarily attributed to the hardness of the matrix (chiefly martensite) and the presence of hard, undissolved carbides.
- Toughness. It is a combination of ductility and elastic strength. It is the ability to resist breaking or chipping under impact loading or overloads. There is usually an inverse relationship between wear resistance and toughness; improving one often reduces the other. Reducing carbon and alloy content can improve toughness, but will reduce wear resistance.
- Hot Hardness/Red Hardness. This is the ability to maintain high hardness at high temperatures. Tool steel operating at high cutting speeds generates a large amount of heat, so the red heat resistance is very important. This is mainly because alloying elements such as tungsten, molybdenum, and cobalt in the composition form stable carbides that resist softening at high temperatures.
- Dimensional Stability. It can maintain minimal dimensional changes during heat treatment. Some air-hardened tool steels exhibit even less deformation during heat treatment.
- Machinability and Grindability. Machinability is the ease or difficulty with which a material can be machined to a desired size, shape, and surface finish. It is influenced by the steel’s microstructure, with spheroidized structures (where carbides are globular) generally preferred for tool steels due to their high carbon content. Grindability is also essential, especially after heat treatment when the tool steel is extremely hard. Tool steels with lower alloy content tend to be easier to machine and grind.
Classification
Different countries and manufacturers have different standards and grades. In this article, we will use the American AISI as a reference.
Tool steels are classified by the AISI (American Iron and Steel Institute) system, primarily based on their intended use, composition, special mechanical properties, or heat treatment method. The major groups are:
- W (Water-Hardening) Steels: High-carbon steels (0.60-1.40% C) with low alloy content. They are shallow hardening and must be water quenched for necessary hardness. Applications include chisels, files, wood-working tools, drills, reamers, and taps.
- S (Shock-Resisting) Steels: Medium-carbon (0.45-0.65% C), low-alloy steels designed for high toughness to withstand shock and impact loads. They contain elements like silicon, chromium, molybdenum, and tungsten. Used for chisels, punches, shear blades, and pneumatic tools. Our company offers S1 and S7 tool steel.
- O (Oil-Hardening Cold-Work) Steels: Possess improved hardenability over W-steels, allowing oil quenching, which minimizes distortion. They offer good wear resistance and non-deforming properties. Used for taps, reamers, blanking dies, and forming dies. O6 and A10 contain graphite for improved machinability and die life. Our company offers O1 and O2 tool steel.
- A (Air-Hardening Medium-Alloy Cold-Work) Steels: High alloy content allows air hardening, which minimizes distortion and promotes dimensional stability. They offer excellent abrasion resistance and good temper resistance, suitable for cold-work applications. Applications include shear knives, punches, blanking dies, forming dies, and gages. Our company offers A2 tool steel.
- D (High-Carbon High-Chromium Cold-Work) Steels: Offer superb wear resistance, nondeforming properties, and minimal dimensional change in hardening due to high carbon (up to 2.25%) and chromium (12-14%). Used for blanking and piercing dies, drawing dies, and shear blades. We offer D2, D3, and D6 tool steel.
- H (Hot-Work) Steels: Designed for operations at elevated temperatures (200°C to 800°C), such as hot forging, hot stamping, extrusion, and die casting. They combine red hardness with good wear and shock resistance. Examples include H10, H11, H12, H13, and H21.
- M (Molybdenum-based High-Speed) Steels: Contain molybdenum as their primary alloying element, often with tungsten and cobalt. Used for high-speed cutting tools like drills, reamers, and milling cutters due to excellent wear resistance and hot hardness. M2, M35, and M42 are common types.
- T (Tungsten-based High-Speed) Steels: Very high in tungsten concentration but contain no molybdenum. Similar applications to M-series, offering excellent strength, toughness, wear resistance, and hot hardness. T1, T4, T5, T8, T15 are examples.
- L (Low-Alloy Special-Purpose) Steels: Have compositions similar to AISI alloy steels but with increased carbon. They offer moderate hardenability and can be oil quenched, providing higher toughness than high-carbon oil-hardening steels. Used for arbors, dies, pins, punches, and machine tool parts. We offer L6 tool steel.
- P (Mold) Steels: Low-carbon steels, often carburized, used for plastic molding and die casting applications. They emphasize polishability, low distortion, and good machinability. Our company offers P20, P20+Ni, and P20+S.
- F (Carbon-Tungsten Special-Purpose) Steels: Extensively used for small-diameter drills.
Based on their intended use, they can also be classified as cold work tool steels, hot work tool steels, plastic mold steels, and high speed steels.
Heat Treatment
Heat treatment is a key process for achieving the best performance of tool steel. The process is usually divided into three stages:
- Austenitizing: The steel is heated to a specific temperature above its critical range for a defined period. This transforms the crystal structure to austenite and dissolves carbides.
- Quenching: Rapid cooling from the austenitizing temperature to transform austenite into martensite, which is the hard matrix structure in steels. The quenching medium (water, oil, air, salt) depends on the steel’s hardenability and desired dimensional stability. Tool steels generally have high hardenability, allowing for oil or air quenching to minimize distortion compared to water-quenched carbon steels.
- Tempering: Reheating the quenched and hardened steel to an intermediate temperature below the critical range to reduce internal stresses, increase toughness, and adjust hardness. This also helps in the transformation of retained austenite to martensite. Double or triple tempering cycles are common to ensure full transformation and stress relief.
For more information about this topic, please refer to “The heat treatment of tool steel“.
Applications
They are indispensable in a vast array of industrial applications. They are used for:
- Cutting Tools: Single-point lathe tools, drills, reamers, taps, milling cutters, end mills, hobs, saws, and broaches.
- Forming and Shaping Tools: Dies (blanking, forming, drawing, extrusion, forging, hot forging, coining, cold heading, stamping, trimming), punches, shear blades, rolls, and mandrels.
- Molds: For die casting, plastic molding (e.g., plastic injection molds), and ceramic molding.
- Specialized Components: Machine tool components, springs, ultrahigh-strength fasteners, special-purpose valves, and bearings, where high wear resistance, strength, toughness, and temperature stability are required.
FAQ
Tool steel is a special class of carbon or alloy steels, designed with high hardness, wear resistance, toughness, and often heat resistance, specifically for manufacturing tools, dies, and molds that cut, shape, or form other materials, primarily by undergoing precise heat treatments.
Tool steels are specialized steels primarily used for manufacturing tools like cutting tools, dies, and molds to shape other materials, including metals, plastics, and wood, under various temperature conditions. They are also used for high-performance machinery components and structural applications requiring high wear resistance, strength, and toughness.
Tool steels are complex iron-base alloys containing significant amounts of carbon, chromium, vanadium, molybdenum, or tungsten, and sometimes cobalt. They are specifically designed to have dispersed hard carbides within a hardened steel matrix to achieve properties like high hardness and wear resistance.
Many tool steels are high-carbon steels, with carbon content typically higher than most carbon structural steels, ranging from 0.4% to 2.5%. When high levels of carbon and alloying elements are combined in tool steel, high-hardness, high-wear-resistant carbides can be obtained after heat treatment. However, some mold steels are low-carbon (e.g., P-series) and are designed to be carburized to achieve a hard surface case while retaining a tough core.
Yes, most tool steels can rust because they are iron-based alloys. While some, particularly high-chromium types like D-series, offer appreciable resistance to staining due to their chromium content after hardening and polishing, this is generally not equivalent to the full corrosion resistance of stainless steels. Specialized martensitic stainless steels are sometimes used for molds where high corrosion resistance is required.
Tool steels are designed for high hardness, often ranging from 50 to 70 Rockwell C (HRC), depending on the specific type and heat treatment.
Strength is a material’s ability to withstand applied stress without deforming or breaking, measured by properties like yield strength and ultimate tensile strength.
Stiffness (Elastic Modulus) is its resistance to elastic (temporary) deformation under stress, meaning how much it bends or stretches before returning to its original shape.
Ductility is the ability to deform plastically (permanently) before fracturing, allowing it to be stretched or bent without breaking.
Flexibility, in terms of elastic deformation, is directly related to stiffness (elastic modulus), not strength. While tool steels are very strong, their stiffness (around 210 GPa or 30 x 10^6 psi) is relatively uniform across grades and decreases predictably with temperature. Strength, on the other hand, refers to the maximum load a material can withstand before permanent deformation or fracture.
High Hardness and Wear Resistance: To resist penetration and maintain a sharp edge against abrasive materials, often achieved through high carbon content and the presence of hard alloy carbides.
High Hot Hardness (Red Hardness): The ability to retain hardness at elevated temperatures generated during high-speed cutting.
Sufficient Toughness: To resist chipping and breaking under shock or impact loads, which is often a trade-off with extreme hardness.
Heat treatment for tool steel involves a series of controlled heating and cooling steps designed to transform its internal structure, significantly enhancing properties such as hardness, wear resistance, toughness, and hot hardness for demanding applications. The primary goal is to change the soft, annealed ferrite and carbide structure into a hard, strong martensitic structure with well-distributed carbides.
Tempering is a crucial post-hardening heat treatment that primarily increases the toughness and ductility of the steel while relieving internal stresses caused by quenching, which makes the as-quenched steel very brittle. It also helps to stabilize the microstructure, can lead to secondary hardness in some alloys by precipitating complex carbides, and transforms retained austenite into fresh martensite.
Tempering is performed immediately after the quenching step, as soon as the part cools to a safe temperature (typically between 50-75°C or 125-200°F), to minimize the risk of cracking due to high internal stresses in the as-quenched state.
Many high-alloy tool steels retain a significant amount of “retained austenite” after the initial quench because their martensite finish (Mf) temperature is below room temperature. The first tempering cycle “conditions” this retained austenite, causing it to transform into new, untempered, and brittle “fresh martensite” upon cooling from the temper. Subsequent tempering cycles (double or triple) are then necessary to temper this newly formed martensite, relieve its stresses, enhance overall toughness, refine the grain structure, and ensure dimensional stability.
Annealing involves heating the steel to an elevated temperature for a defined period (sometimes above, near, or below the upper critical temperature, typically 749–760°C for carbon steels), followed by very slow cooling, often within the furnace (e.g., 10-38°C per hour). The purpose is to soften the steel, usually to improve its machinability, homogenize its microstructure, and relieve internal stresses, resulting in a spheroidized microstructure with dispersed, spherical carbides in a ferrite matrix. Annealing is common for as-purchased steel and when reworking hardened tools.
Successful drilling of hardened tool steel primarily relies on specialized drill designs, such as solid carbide drills or heat-resistant alloy drills, combined with rigid machine setups and carefully controlled speeds and feeds.
Yes, carbide end mills are frequently used to cut tool steel, including hardened grades. They offer superior performance, wear resistance, and the ability to operate at higher cutting speeds compared to high-speed steel (HSS) cutters, often featuring advanced coatings for enhanced durability.
Yes, improper grinding can significantly damage the temper of hardened tool steel by generating excessive localized heat. This can lead to undesirable effects such as overtempering (softening the surface) or rehardening (forming a brittle, crack-prone “white layer”).
Tool steels can be welded, but it is a complex process requiring high skill and meticulous control. Proper preheating, post-weld stress relief, and precise tempering cycles are crucial to prevent cracking, minimize distortion, and manage the hardness variations within the heat-affected zone.
Yes, file steel is a type of tool steel, typically a high-carbon water-hardening grade like W1. W1 is known for achieving a very sharp edge and is used for fine kitchen knives. However, these steels have lower hot hardness and wear resistance compared to more alloyed tool steels.
No, 4140 steel is classified as a medium-carbon low-alloy steel, not a tool steel. It is widely used for machinery components and structural applications requiring good strength and toughness.
Yes, tool steels are generally much harder than most other common steels (like plain carbon or low-alloy steels) after heat treatment. They are designed for very high hardness, wear resistance, and durability.
Tool steels achieve their strength through high carbon content, which allows for the formation of very hard martensitic structures during quenching, and through alloying elements (like chromium, tungsten, molybdenum, and vanadium) that form very hard, wear-resistant carbide particles distributed throughout the steel matrix. This combination, optimized by specific heat treatments, results in high strength and wear resistance.
The primary advantages of tool steels are their high hardness, excellent wear resistance, good hot hardness (resistance to softening at elevated temperatures), durability, and strength, making them ideal for cutting, forming, and shaping other materials under severe conditions.
Yes, tool steels are a family of iron alloys. Like all steels, they are primarily composed of iron, with various alloying elements added to achieve specific properties.
All tool steels are a type of alloy steel (or high-carbon steel), but not all alloy steels are tool steels. Tool steels are a specialized category, specifically designed for tools that require extreme hardness, wear resistance, strength, and durability under severe service conditions. General alloy steels are a broader group used for structural, machinery, and other applications, where properties like hardenability, strength, and toughness are enhanced by alloying, but not necessarily to the extreme levels or specific balances required for tooling.
Steels are broadly categorized, and common classifications include: Carbon Steels, Alloy Steels, Stainless Steels, and Tool Steels. Some classifications may also include a separate category for High-Speed Steels, which are also a subset of tool steels.
“Strongest” can refer to different properties (tensile strength, yield strength, impact strength, and hardness). Ultrahigh-strength steels, which can be medium-carbon low-alloy steels (like modified 4340, such as 300M) or maraging steels, are designed for very high strength, often exceeding 1380 MPa (200 ksi) tensile strength. Highly alloyed tool steels, particularly certain high-speed steels (e.g., T15, M42) and powder metallurgy (P/M) tool steels, are also among the strongest in terms of hardness and wear resistance, capable of reaching very high Rockwell C hardness values (e.g., 66 HRC for some P/M tool steels, 69 HRC for M40 series). The “strongest” depends on the specific property of interest and the application.