Understanding O1 tool steel‘s hardness is critical for performance and tool life in factory applications. At Aobo Steel, this is a common question we address. To be direct, properly heat-treated O1 tool steel typically shows a Rockwell C hardness (HRC) from the low 50s to the mid-60s. In its as-quenched state—immediately after hardening and before tempering—O1 steel generally reaches a hardness of about 64–65 HRC. The final hardness you achieve will then be fine-tuned by the specific tempering process you employ.
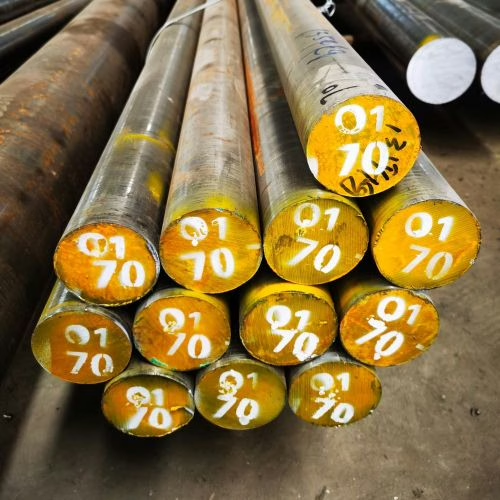
What is Rockwell Hardness and Why Does It Matter for O1?
Rockwell hardness, specifically the Rockwell C scale (HRC) for hardened steels like O1, measures the material’s resistance to permanent indentation. Essentially, it indicates how well the steel will resist wear and deformation. This characteristic is key to O1’s popularity in cold-work applications, as its ability to achieve and maintain good hardness is a significant advantage. The high carbon content in O1 significantly contributes to its excellent hardenability.
Achieving Hardness: The Heat Treatment Process
Getting the desired hardness in O1 isn’t just about the steel itself; it’s about a precise heat treatment process involving heating, quenching, and tempering.
As-Quenched Hardness: The Starting Point
To harden O1, heat it to a specific critical temperature and then quench it rapidly, typically in oil. This rapid cooling transforms the steel’s internal structure (to what we call martensite) and makes it very hard. As mentioned, O1 tool steel will usually measure around 64–65 HRC right after this oil quench. This is its maximum hardness, but also in its most brittle state.
Tempering O1 Steel: Tailoring Hardness and Toughness
Simply quenching steel leaves it too brittle for most practical uses. That’s where tempering comes in. After quenching, O1 is reheated to a lower temperature and held for a specific time. This process reduces brittleness and internal stresses, making the steel tougher. The critical thing to understand is that the tempering temperature directly controls the final hardness.
Here’s a general idea of how tempering temperatures affect O1’s hardness:
O1 Tool Steel Tempering Curve
This chart illustrates the general relationship between tempering temperature and Rockwell C hardness (HRC) for O1 tool steel. Actual hardness may vary based on specific composition and heat treatment processes.
Recommended Tempering and Working Hardness
For most tooling applications, the recommended tempering range for O1 steel is between 300°F (149°C) and 450°F (232°C). O1 maintains a high working hardness within this range, typically between 62 HRC and 63 HRC. This provides an excellent balance of wear resistance (from the high hardness) and the necessary toughness to prevent chipping or breaking in service. It’s worth noting that O1 generally offers better impact toughness at these high hardness levels compared to some other O-type steels. Remember, while higher tempering temperatures increase toughness, they will reduce the hardness and overall strength.
Essential Considerations for Your O1 Steel
Beyond the hardness numbers, a few other practical points about O1 are useful for factory applications.
Hardenability and Dimensional Stability
O1 is classified as a low-alloy cold-work tool steel. Its composition allows it to be hardened effectively right through its cross-section, up to about 2 inches (or 50 mm) thick, when quenched in oil. When O1 is hardened correctly, you can expect a small amount of dimensional change; it typically expands by about 0.0015 inches per inch (or 0.0015 mm per mm). This is an important factor to account for in precision tool making.
Best Practices for Heat Treatment
To get the best results from your O1 steel and avoid issues like decarburization (loss of carbon from the surface, which softens it), it’s best to carry out annealing and hardening processes in a controlled neutral atmosphere, a vacuum furnace, or a neutral salt bath.
Preheating the steel is also good practice. We usually recommend preheating to around 1200°F (650°C) before you take it up to the higher austenitizing (hardening) temperature, especially if your furnace is starting cold. For O1, which contains chromium and tungsten, maximum hardness is usually achieved when hardened from austenitizing temperatures slightly above 1550°F (845°C). You might see specific recommendations like 1450°F (790°C) for one hour, or up to 1520°F (830°C). While slightly higher hardening temperatures can increase how deeply the steel hardens, going too high can sometimes negatively affect ductility and toughness. Fortunately, O1 is generally less prone to excessive grain growth from slight overheating compared to some other tool steels.
Making O1 Work for You
O1 tool steel is a dependable choice offering significant Rockwell C hardness. After quenching, it typically reaches 62-65 HRC, which can be precisely adjusted through tempering to achieve an optimal balance of properties, often around 62-63 HRC for many applications. Its effective oil-hardening capability, good wear resistance, and toughness make O1 a go-to material for various cold-work tooling. Understanding how tempering affects final hardness is crucial for maximizing the performance of your O1 steel parts.
Ready to Get the Best O1 Steel?
Take the next step towards superior results. Fill out the short form below to get a custom quote or discuss your O1 tool steel requirements with our experts.
(Your information is secure and will only be used to contact you regarding your inquiry.)
Contact Us Via The Form Below: