The following steels from our company can be used for Cold Forming Hexagon Nuts

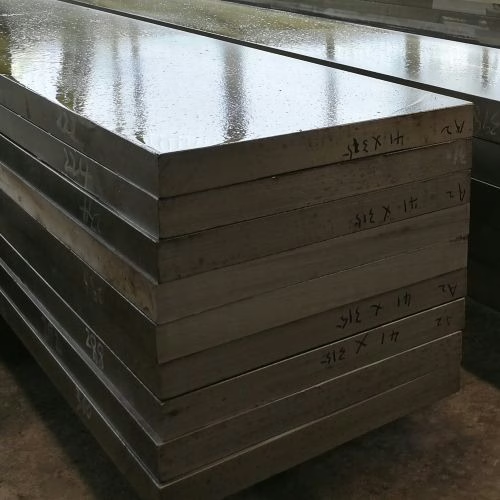
What is a punch, and why do punches need hardness and wear resistance?
A punch is an industrial tool that is commonly used to punch holes or stamp moldings in metal or other materials. Because it has to hit and rub against the material repeatedly, it must be very hard and not easily deformed or worn out. At the same time, the punch must not be too brittle, or it will break easily. Therefore, to manufacture a punch, you need to choose the right steel and adjust the hardness and toughness of the steel by heating and cooling methods (called heat treatment).
Heat Treatment Methods
Heat treatment makes T1, D2, and A2 ideal for harder and more durable punches. The following are specific heat treatment methods:
- T1 steel
T1 steel is a tool steel characterized by its suitability for the manufacture of punches that require high strength; it is heat-treated by heating to 2,300°F (about 1,260°C) and then oil quenched by rapid cooling in oil; after treatment, T1 steel can reach a hardness of HRC 59 to 61, which is suitable for the general needs of punches.
- D2 steel
D2 steel is characterized by being slightly harder than T1 steel and has better wear resistance; it is heat treated by heating to 1950°F (about 1065°C) and oil quenched, also using oil cooling; after treatment, D2 steel can reach a hardness of HRC 61; if the punch requires higher hardness and wear resistance, D2 steel can be chosen because it is slightly harder than T1 steel.
- A2 steel
A2 steel is harder than T1 and D2, and is especially suitable for the surface of the punch because the surface needs to bear the most friction. It is heat-treated by heating to 1700°F (about 925°C), then air quenched with air cooling, and later tempered to further increase the hardness; the hardness reaches HRC 61 after air cooling, and the surface hardness can reach HRC 65 after tempering.
Relationship between wear resistance and hardness
When the surface hardness reaches HRC 65, the punch can be used for a longer period of time and is less prone to wear. Keeping the center hardness at HRC 25 ensures that the punch as a whole will not be too brittle. This design makes the punch both durable and strong, which makes it ideal for stamping or punching work.
Summarize
Different steels (T1, D2, A2, etc.) and heat treatment methods (heating, cooling, tempering) are selected to make good hardness and wear resistance punches. Specific steps include:
- With T1 steel heated to 1260°C and oil quenched to a hardness of HRC 59-61.
- Heating to 1065°C with D2 steel, oil quenching, hardness to HRC 61.
- heated to 925°C with A2 steel, air quenched, and then tempered to a surface hardness of HRC 65.
- Steel with a carbon content of 0.9% can be used and heat-treated at low temperatures to give a hard surface and tough center, balancing hardness and toughness.
These methods aim to make hard, wear-resistant punches that do not break easily, making them suitable for stamping or punching.