What is cold forging? Cold heading is a metalworking method used to make fasteners such as bolts and screws. Because the molds are subjected to a lot of pressure during the cold heading process, they are prone to problems such as wear, adhesion, cracking, and even fatigue or the molds becoming misshapen.

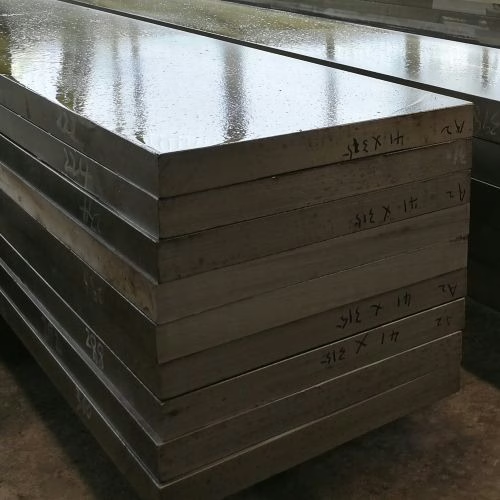
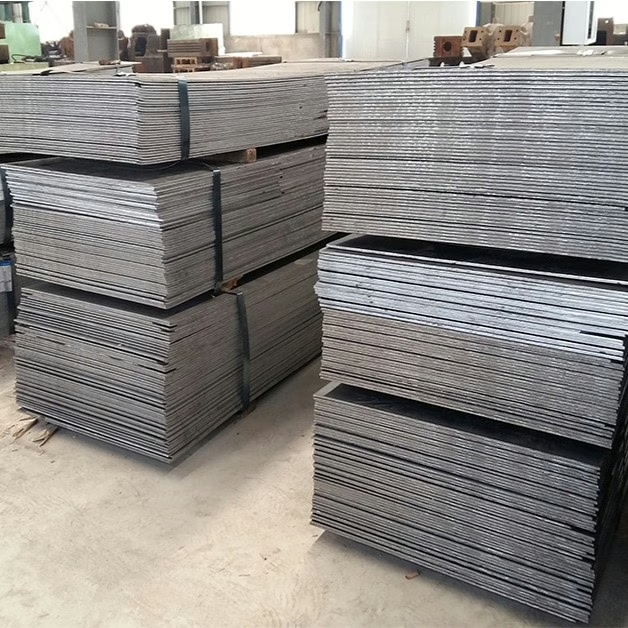
Why do cold heading molds fail?
Cold heading molds encounter several common failures in their work:
- Wear and tear: the surface of the mold is worn off, affecting the service life.
- Adhesion: The metal material adheres to the mold, resulting in poor processing.
- Cracking: the mold cracks because it cannot withstand the high pressure.
- Fatigue: Fatigue damage occurs inside the mold or on the working surface after a long time of use.
- Shape Enlargement: The shape of the mold is propped up, which compromises precision.
Because of the high pressure in the cold heading process, the mold’s working surface needs to be very hard, usually with a hardness of 62 HRC (a hardness unit). Therefore, it is very important to choose the right steel.
Commonly used steels: W1 and W2 water-hardened steels
As mentioned in the article, the most common materials used for cold heading dies and punches (punches are the tools used with the dies) are W1 and W2 water-hardened steels. These steels have the following characteristics:
- Shallow Hardening: These steels only harden on the surface when quenched (a heat treatment method that hardens the steel), the interior is still relatively soft.
- Hardenability control is important: Hardenability is the depth to which a steel can harden when quenched. Hardenability should be adjusted to the size of the mold.
However, W1 and W2 steels have drawbacks:
- Limited wear resistance: even with a 62-64 HRC hardness, they are not good enough. If the mold is to be used for a long time, this steel may not be durable enough.
The effect of vanadium: Sometimes, vanadium (a metallic element) is added to steel, but vanadium can lower hardenability. To solve this problem, other elements in the steel can be adjusted to ensure hardenability, make the steel grain finer, and improve toughness (toughness is the ability of a material not to break easily).
The more durable option: high-alloy steels (D2, M2, A2)
When it is necessary for a mold to last longer, choose a high-alloy steel such as D2, M2, or A2. The advantages and disadvantages of these steels are listed below:
- Advantages: much higher wear resistance than W1 and W2, suitable for mass production.
- Disadvantages: low toughness (easy to break), cannot be made directly into whole molds.
Solution:
- Make these high-alloy steels into inserts (small mold parts) and then mount them in a shell made of H11 steel.
- H11 steel is tough, with a hardness of 48-50 HRC, which protects the inserts and makes the entire mold both wear-resistant and less prone to breakage.
Selection of steel for cold-heading dies
Punch is a tool that works together with the mold in the cold heading process, and the choice of steel is also very important:
- Commonly used materials, like molds and punches, are also commonly made of W1 or W2 steel.
- When toughness is needed, if the punch breaks easily, or if wear resistance is not so important, S1 impact-resistant steel can be used. This steel is tough and can withstand impacts.
- When wear resistance is needed: If the punch needs to be more wear-resistant, use D2 or M2 steel.
In summary, the key to choosing steel
This article’s core idea is that different steels are suitable for different situations. The choice of steel is based on specific needs:
- If the mold or punch requires a hard, low-cost material, consider W1 or W2.
- If it needs to be used for a long time and has high wear resistance, choose D2, M2, or A2, but with a tough housing.
- If the punch is prone to breakage, choose S1.