Coin embossing dies are tools used to make coins. They are subjected to much pressure and wear and tear, so choosing the correct steel is crucial. The following steels are available from our company for use in coining dies.
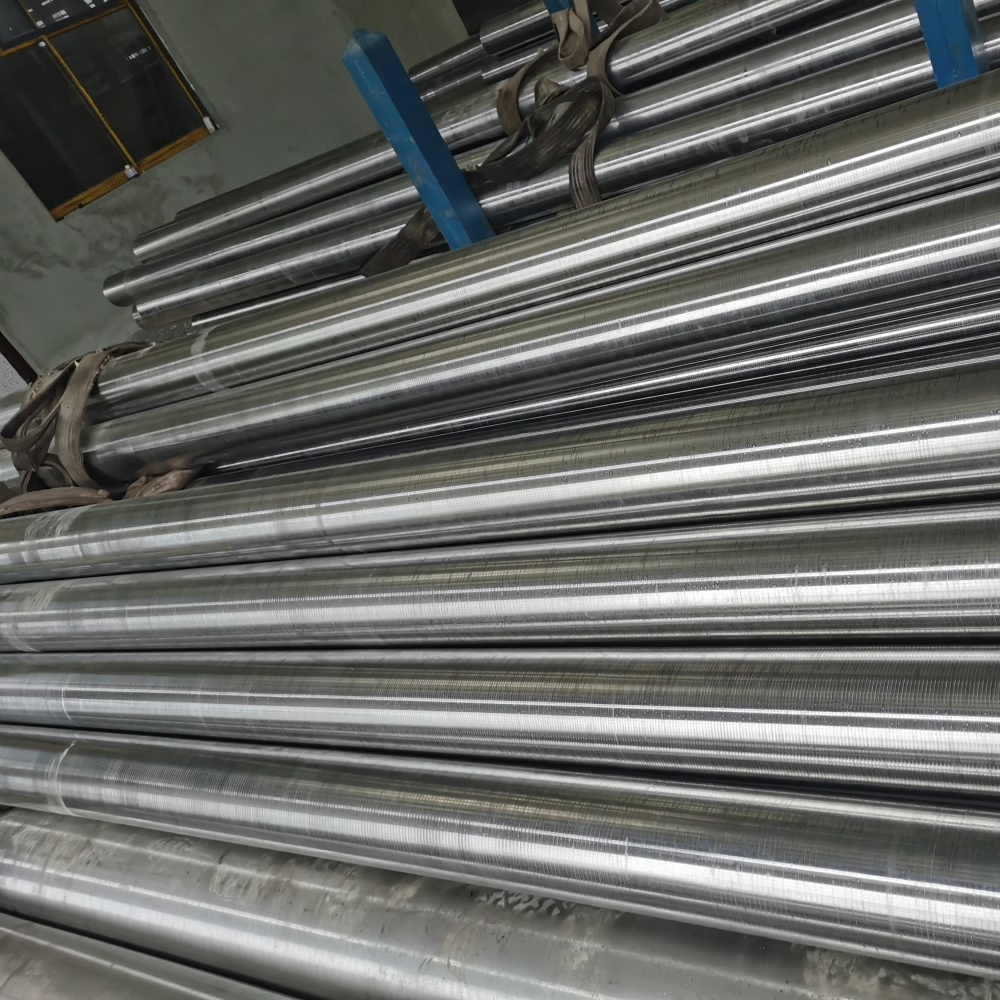
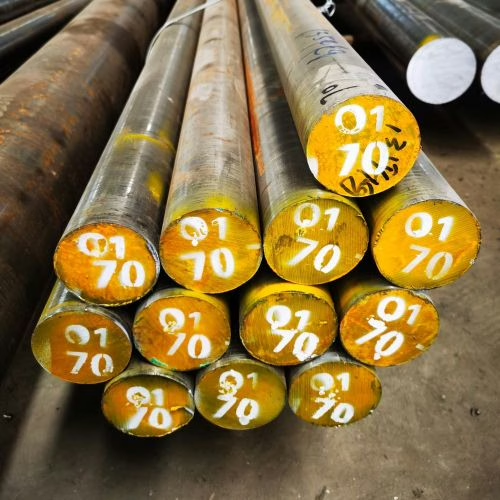
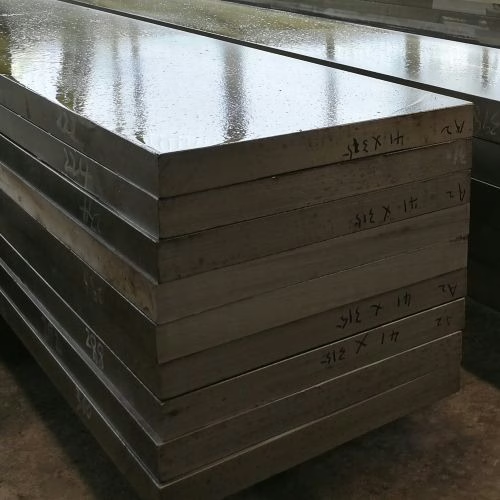

Causes of Coining Die Failure
Coin embossing dies can be damaged by the following problems:
- Wear: the surface of the die is worn away, especially when the pressure is low and the workpiece material is soft; the metal may stick to the die, leading to increased wear.
- Denting: the surface of the mold is pressed down.
- Cracking: the mold cracks, usually because it is under too much pressure or the design is too complex.
Commonly used steel in the silver industry – W1 water-hardened steel
In the silversmithing industry (e.g., the manufacture of silver, copper, or stainless steel coins), coin embossing is usually done with drop hammers. The most commonly used steel for this purpose is W1 water-hardened steel with the following characteristics:
- Surface hardness: 59 to 61 HRC (HRC is the hardness unit, and the higher the number, the harder it is).
- Shallow hardening properties: Only the surface layer hardens when quenched, and the interior remains softer. This characteristic gives the mold a hard surface (wear-resistant) and toughness (less prone to cracking).
- Controlled hardenability: The degree of hardening of the steel can be precisely controlled.
W1 steels are well suited to situations where the pressure is not too high and the workpiece is soft, such as embossing silver or copper alloys.
Challenges and solutions for deep embossed designs
If a coin has a deep design (e.g., a complex pattern), W1 water-hardened steel may fail due to cracking. To solve this problem, the following steels are available:
1. Deep-hardening carbon tool steel: hardens to a greater depth and can withstand more complex embossing.
2. Mild steel (e.g., S1 or L6):
- Hardness: 57 to 59 HRC.
- Toughness rating: 6 to 8 (tough and less prone to cracking).
3. High-toughness steels (e.g., H11 or H12):
- Hardness: 45 to 52 HRC (lower than W1, but better toughness).
- Because of its lower hardness, the surface scratches easily. It can be protected by adding a hard chrome plating (0.127 to 0.254 mm, or 0.005 to 0.010 inches thick).
Selection of small molds
For small molds that require higher wear resistance, the following steels can be used:
- Oil hardened steel O1: hardness 56 to 58 HRC.
- Air-hardened steels A2 and D2 have a 56 to 58 HRC hardness. These steels perform better on small molds because they are wear-resistant and suitable for high-precision imprinting.
How Dies are Made – Hubbing
Coin embossing dies are best made by hubbing rather than direct machining. Hubbing uses a master hob to press out the shape of the die and is much cheaper than machining. How different steels behave when hubbing:
- O1 and A2 steels can be cold hub pressed, but may require intermediate annealing (heating to soften the steel to avoid cracking too hard) between impressions.
- W1 steel is easier to hub press. At the same pressure, W1 steel has twice the indentation depth of A2 steel.
Summary: Key factors in choosing steel
In summary, the following factors need to be considered when choosing the steel for coin embossing dies:
- Wear resistance: the die should be able to be used for a long time without wear.
- Toughness: the die should not crack easily.
- Hardening properties: the balance of surface hardness and internal toughness.
- Machinability: whether it is easy to machine or hub press.
- Cost: try to reduce the cost while the performance meets the demand.
Different situations require different steels:
- W1 steel suits shallow embossing, low pressure, and the silverware industry.
- S1, L6 steel: suitable for deep embossing, when toughness is required.
- H11, H12 steel: when maximum toughness is required, with hard chrome plating for protection.
- O1, A2, D2 steels: small molds when high wear resistance is needed.