When you’re looking at S7 tool steel and 4140 alloy steel, the most important thing to know right off the bat is that they are designed for fundamentally different jobs. If your application involves high shock or impact, like in many tooling operations, S7 is generally your go-to. If you need a versatile, strong steel for structural components like shafts or gears, 4140 is often the more suitable choice. The best pick always comes down to the specific demands of what you’re making or the problem you’re solving in the factory.
Let’s break down these two popular steels in more detail.
Understanding S7 Tool Steel
S7 is a dedicated shock-resisting tool steel. That “S” in its name tells you its primary characteristic: toughness and the ability to withstand impact.
Key Characteristics of S7:
- Exceptional Impact Strength: This is what S7 is famous for. It’s built to take a hit. The chemical composition is engineered for this high toughness, typically including around 0.50-0.60% carbon, 0.70% manganese, 0.25% silicon (though silicon can range up to 1.90% in some variants), 3.25% chromium, and 1.40% molybdenum.
- Good Wear Resistance: While its main job is handling shock, S7 also offers decent resistance to wear, which is crucial for many tool and die applications.
- Air-Hardening: This is a big plus. S7 is an air-hardening steel, meaning its heat treatment process is generally safer, more straightforward, and results in less distortion compared to steels requiring liquid quenching. It can fully harden through sections up to about 2.5 inches (63.5 mm) with an air quench from a hardening temperature of 1,725°F (941°C). For more, please click S7 tool steel heat treatment.
- Typical Working Hardness: You’ll typically see S7 used at a hardness of around 56-58 HRC.
Common Factory Applications for S7:
Given its properties, S7 is a workhorse for:
- Tools and dies subjected to impact, such as medium cold-work tools and dies.
- Shear blades.
- Plastic molding dies (especially where toughness is a factor).
- Medium hot-work dies.
- Components like mandrels and cold swaging dies.
When it comes to machining, S7 in its annealed state has a machinability rating of about 70, using 1% carbon steel as a benchmark of 100.
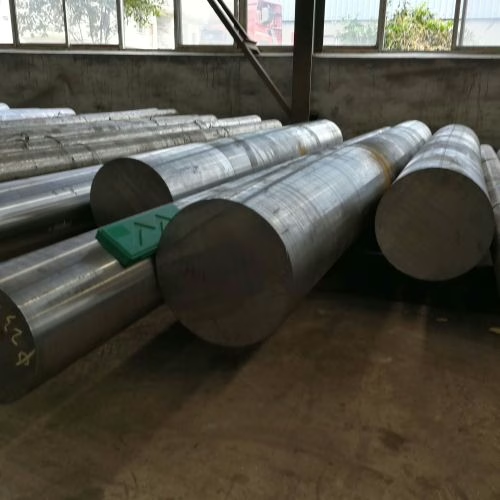
Getting to Know 4140 Alloy Steel
Now, let’s look at 4140. This isn’t typically classified as a “tool steel” in the same way S7 is. Instead, 4140 is a versatile medium-carbon, chromium-molybdenum (often called “chromoly”) alloy steel. The “41” in its SAE designation points to chromium and molybdenum as key alloying elements, and the “40” indicates an average carbon content of about 0.40%. A typical composition for 4140 includes 0.38-0.43% carbon, 0.75-1.0% manganese, 0.20-0.35% silicon, 0.80-1.1% chromium, and 0.15-0.25% molybdenum.
Key Characteristics of 4140:
- Good Strength and Toughness: 4140 offers a solid combination of strength and toughness, making it suitable for parts that must withstand significant stress.
- Resistance to Torsional and Reversing Stresses: This makes it excellent for applications like shafts.
- Versatile Heat Treatment: 4140 responds well to various heat treatments. It’s commonly quenched and tempered to achieve the desired mechanical properties. It’s also very suitable for surface hardening processes like nitriding (to achieve a very hard surface, around 690 HK or roughly 57 HRC) or induction hardening, which can provide a hard wear surface with a tough core.
- Weldability and Forgeability: It can be readily welded and forged, adding to its versatility.
Common Factory Applications for 4140:
You’ll find 4140 used extensively for:
- Drive shafts.
- Axles.
- Gears.
- Spindles.
- Other structural components and forgings where good strength, toughness, and fatigue resistance are required.
The machinability of 4140 heavily depends on its hardness and heat-treated condition. In an annealed state (around 150-200 HB), it’s reasonably machinable. However, after quenching and tempering to higher hardness levels, or especially after nitriding, machining becomes more challenging.

S7 vs. 4140: The Head-to-Head Comparison
The core difference lies in their intended purpose: S7 is a specialist tool steel for impact applications, while 4140 is a general-purpose engineering alloy steel for structural use.
Feature | S7 Steel | 4140 Steel |
---|---|---|
Primary Role | Tooling, especially shock-resisting tools and dies. | Structural components, machine parts. |
Impact Strength (Toughness) | Superior. Designed specifically for high-impact scenarios. | Good toughness, but not in the same league as S7 for shock resistance. |
Hardness & Wear Resistance | Achieves high through-hardness (typically 56-58 HRC) and good wear resistance from its standard air-hardening heat treatment. | Achieves its properties through quenching and tempering. Can be surface hardened (e.g., nitriding, induction hardening) to achieve very high surface wear resistance while the core remains tougher and less brittle. Its through-hardened capability is moderate. |
Heat Treatment | Air-hardening. This generally means simpler processing, more stable dimensions after treatment, and less risk of cracking or distortion. | Typically oil or water quenched and tempered. Offers flexibility to tailor properties through different tempering temperatures or surface hardening methods. |
Composition Highlights | Higher chromium (approx. 3.25%) and molybdenum (approx. 1.40%) content, along with specific carbon, manganese, and silicon levels, contributing to its shock resistance, hardenability, and wear characteristics. | Moderate chromium (approx. 0.80-1.1%) and molybdenum (approx. 0.15-0.25%) content, with controlled carbon, manganese, and silicon, providing a good balance of strength, toughness, and hardenability for its intended uses. |
Making the Right Call for Your Factory
So, how do you choose?
Opt for S7 when:
- Your primary concern is exceptional toughness and resistance to shock or impact.
- You’re making tools or dies that will experience repeated blows or high stresses.
- The stability and simplicity of air-hardening are advantageous for your heat treatment capabilities.
Opt for 4140 when:
- You need a good all-around engineering steel for structural parts.
- The component requires a good balance of strength, toughness, and fatigue resistance (e.g., shafts, gears).
- The ability to surface harden for enhanced wear resistance on specific areas, while maintaining core toughness, is beneficial.
Final Thoughts
Both S7 tool steel and 4140 alloy steel are excellent materials, but they excel in different arenas. S7 is your specialist for high-impact tooling, offering unmatched shock resistance. 4140 is your versatile workhorse for a wide range of structural and machinery components that need good strength and toughness.
Understanding the specific job your steel needs to do is the first and most critical step in selecting the right grade. If you’re ever unsure, discussing your application’s details can help pinpoint the best material to ensure performance and longevity for your parts.
Unlock the Power of S7 Tool Steel for Your Applications
Discover the exceptional toughness, superior impact resistance, and excellent machinability of our premium S7 tool steel. Aobo Steel is dedicated to providing high-quality S7 solutions tailored to your precise engineering needs.
Ready to elevate your project? Fill out the form below to connect with our S7 steel specialists and receive your competitive, no-obligation quote today!