This guide provides technical information for the S7 tool steel heat treatment process. S7 tool steel is a shock-resisting, air-hardening grade containing chromium and molybdenum, known for its excellent impact strength. It is used for applications such as medium cold-work, plastic molding dies, shear blades, and medium hot-work dies. Adhering to proper heat treatment procedures is crucial for achieving its intended properties.
We provide a free download of the S7 tool steel heat treatment PDF at the bottom of the page.
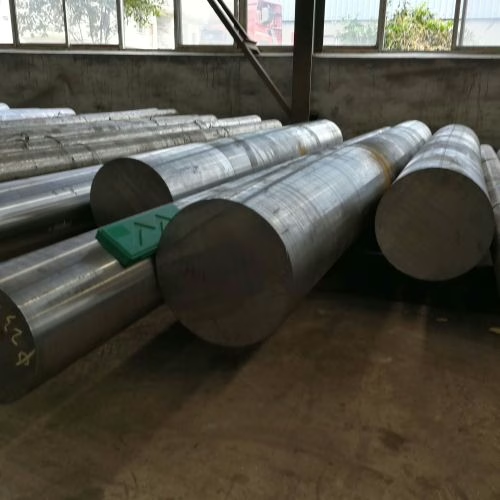
1. The S7 Tool Steel Heat Treatment Cycle
The S7 tool steel heat treatment process consists of several key stages designed to develop the material’s desired mechanical properties.
1.1. Annealing S7 Tool Steel (If Required)
Annealing is performed to soften S7 steel for improved machinability and to relieve stresses from prior processing. The goal is a microstructure of spheroidized carbides in a ferrite matrix.
- Purpose: Softening for machining, stress relief.
- Environment: Use a controlled atmosphere, vacuum, or neutral-salt furnace to prevent surface decarburization.
- Procedure:
- Heat to 1,550°F (843°C).
- Soak for 1.5 hours per inch (3.5 minutes per mm) of thickness.
- Cool slowly at 25°F (14°C) per hour down to 900°F (482°C).
- Air cool to room temperature.
- Expected Result: Approximate annealed hardness of 230 HB maximum.
1.2. Hardening S7 Tool Steel: Austenitizing and Quenching
The hardening process is essential for developing the strength and wear resistance of S7 tool steel. It involves transforming the microstructure to austenite and then quenching to form martensite.
1.2.1. Preheating
Preheating is an important step in the S7 tool steel heat treatment.
- Purpose: Minimizes thermal shock and equalizes temperature throughout the part before austenitizing. It can also help speed up the overall heat-treating cycle.
- Temperature: 1200°F (650°C).
- Time: Typically 10-15 minutes.
1.2.2. Austenitizing
- Purpose: Heating the steel to transform the microstructure into austenite.
- Temperature: The hardening temperature for S7 is 1725°F (940°C). Heat rapidly from the preheat temperature to the austenitizing temperature.
- Soak Time: Dependent on the smallest cross-section of the part:
- Over 1″ (25mm) thick: Soak for 1 hour per inch (25mm).
- 1″ (25mm) thick: Soak for 1 hour.
- 3/4″ (19.05mm): 50-55 minutes.
- 1/2″ (12.70mm): 45-50 minutes.
- 1/4″ (6.350mm): 40 minutes.
- 1/8″ (3.175mm): 30 minutes.
- Note: Ensure the part reaches furnace temperature before starting the soak time. Avoid prolonged soaking once the temperature is reached.
1.2.3. Quenching
- Purpose: Controlled cooling from the austenitizing temperature to transform austenite into a hard martensitic structure.
- Medium: S7 is primarily an air-hardening steel. Air cooling is the typical method.
- Size Limitation: For S7 sections exceeding 2 1/2 inches (63mm) in cross-section, full hardness may not be achieved with air cooling alone.
- Alternative for Larger Sections: For these larger sections requiring full hardness, oil quenching might be necessary.
- As-Quenched Hardness: Generally around 60 HRC. (Some data indicates 59-60 HRC, while other sources suggest 62-63 HRC).
1.3. Tempering S7 Tool Steel
Tempering is a critical step following quenching. It improves toughness, relieves stresses, conditions the martensite, and can precipitate fine carbides. This is a key part of the S7 tool steel heat treatment.
- Timing: Temper when parts cool to 125-150°F (52-65°C).
- Duration: Standard tempering time is 2 hours per inch (25mm) of cross-section.
- Cycles: Typically, two tempering cycles are performed.
- Temperatures and Resulting Hardness:
Tempering Temperature | Approximate Hardness (HRC) |
300°F (150°C) | 61 Rc |
400°F (205°C) | 60 Rc |
500°F (260°C) | 57 Rc |
600°F (315°C) | 55 Rc |
800°F (425°C) | 52 Rc |
1000°F (540°C) | 50 Rc |
1100°F (595°C) | 46 Rc |
- Recommended First Temper: 450°F (230°C).
- Recommended Second Temper: 425°F (220°C).
- Working Hardness: The normal working hardness for S7 is 56–58 HRC, typically achieved by tempering at 450°F (230°C).
- For Hot Working: If S7 is used for service up to 1,000°F (540°C), temper the tool 25 to 50°F (14 to 28°C) higher than the expected working temperature.
2. Post-Hardening Considerations for S7 Tool Steel
Additional steps may be necessary after the primary S7 tool steel heat treatment.
2.1. Stress Relieving (Post-Machining/Grinding)
- Purpose: To relieve residual stresses from machining, grinding, welding, or EDM, which helps minimize distortion.
- Procedure:
- If needed after significant post-hardening work: Select a tempering temperature 25 or 50°F (14 or 28°C) lower than the last tempering temperature used.
- For stress relieving after rough machining (before final machining): Temperatures of 1200 to 1350°F (650 to 730°C) can be used.
- Critical Note: The stress relief temperature for reground tools must be at or below the original tempering temperature.
3. Other Technical Factors in S7 Tool Steel Heat Treatment
Several other factors are important for a successful S7 tool steel heat treatment.
- 3.1. Dimensional Change: When air quenched from the proper hardening temperature, S7 is expected to expand approximately 0.001 inch per inch (0.001 mm per mm). Part geometry can influence distortion.
- Straightening: Can sometimes be performed after quenching while the part is between 1050°F (565°C) and 400°F (205°C).
- 3.2. Decarburization: While S7 is less prone to decarburization than grades like O1, using controlled atmosphere, vacuum, or neutral-salt furnace environments for annealing and hardening is recommended. Allow sufficient stock for finish grinding.
- 3.3. Equipment Calibration: Ensure heat treating equipment is properly calibrated.
It is crucial to refer to the steel manufacturer’s specific recommendations for the grade of S7 being used. Following these guidelines will help achieve the desired properties and performance from S7 tooling.
Interested in S7 Tool Steel?
With its exceptional impact toughness and resistance to shock, S7 Tool Steel is the ideal choice for a wide range of demanding applications. Whether you need it for chisels, punches, or plastic injection molds, Aobo Steel provides top-quality S7 tailored to your specifications. Let our 20+ years of expertise work for you.
Fill out the form below to get a personalized quote or to discuss your S7 tool steel requirements with our experts!