S1 tool steel is a shock-resisting material. Its primary characteristic is exceptional toughness, which makes it highly resistant to impact loading. Understanding its properties helps determine if it fits your manufacturing needs correctly.
1. Chemical Composition1
The typical chemical composition (weight %) for S1 steel falls within these ranges:
C | W | Cr | Si | V | Mn | Mo | P | S |
0.40 – 0.55% | 1.50 – 3.00% | 1.00 – 1.80% | 0.15 – 1.20% | 0.15 – 0.30% | 0.10 – 0.40% | up to 0.50% | ≤ 0.030% | ≤ 0.030% |
2. S1 Tool Steel Properties
Understanding these S1 steel properties will help you determine its suitability for your specific factory applications:
2.1 Hardness
S1 tool steel can achieve a hardness between 40 and 63 HRC after heat treatment. However, for most practical applications requiring its signature shock resistance, S1 is typically used in a working hardness range of 50-56 HRC, often around 55 HRC. It’s important to remember that while higher hardness improves wear resistance, it generally reduces toughness.
2.2 Heat Treatment Response
S1 is an oil-hardening steel, capable of reaching its required hardness through oil quenching. For simpler or larger cross-sections, water or brine quenching may also be viable options. It exhibits a medium depth of hardening.
Post-hardening and tempering are critical steps. While a low tempering temperature (around 300°C / 570°F) yields maximum hardness, S1 offers a broad usable tempering range from approximately 175°C to 540°C (350°F to 1000°F). Compared to steels with higher alloy content, S1 tool steel will show a more pronounced decrease in hardness as tempering temperatures rise. Be aware that tempering below 315°C (600°F) can make the steel more susceptible to notch sensitivity.
2.3 Toughness and Shock Resistance
This is where S1 tool steel truly excels. It has very high, often the highest, toughness among tool steels, particularly when compared to many cold-worked grades. This exceptional toughness, a core S1 steel property, makes it ideal for applications involving repeated impacts, mechanical shocks, or sudden loads. The medium carbon content, combined with silicon and tungsten additions, is key to this characteristic.
2.4 Wear Resistance
S1 tool steel offers medium to low wear resistance. This is generally lower than cold-work tool steels like D2 or A2. The tungsten content does contribute some inherent wear resistance. For applications requiring enhanced surface wear resistance, nitriding can be considered. However, this process requires careful management, as the temperatures involved might reduce the core hardness and strength, potentially leading to plastic deformation in high-stress areas if not properly controlled.
2.5 Hot Hardness and Heat Resistance
S1 tool steel possesses low to medium hot hardness. It doesn’t maintain its hardness at elevated temperatures as effectively as high-speed steels. Nevertheless, thanks in part to its tungsten content, it offers a degree of heat resistance, allowing its use in moderately elevated-temperature service or some hot-working applications, generally up to temperatures around 540°C (1000°F).
2.6 Machinability
When properly annealed, S1 tool steel is regarded as having good machinability. Its rating is often cited as 90-95, compared to a 1% carbon steel standard of 100. Even in the hardened condition, machinability is considered fairly good. The machinability of S1 steel can be further improved by increasing the sulfur content.
2.7 Dimensional Stability
Oil quenching, the typical method for S1, generally results in small and predictable dimensional changes. While air-hardening steels like S7 offer superior dimensional stability, the dimensional stability performance of S1 tool steel is considered good in oil- or water-hardening grades. Water quenching causes severe thermal shock to S1 tool steel, increasing the risk of cracking and deformation, so it should be used with caution.
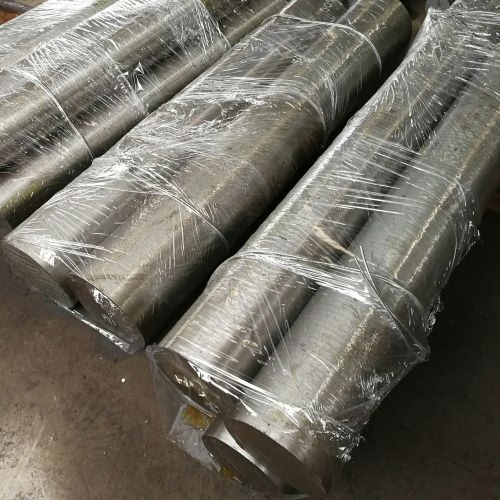
Interested in S1 Tool steel? Please fill out the following form to contact us for the most competitive S1 tool steel!
3. S1 Tool Steel Heat Treatment
S1 tool steel is a shock-resisting steel. Proper heat treatment is critical for its performance. This guide outlines the standard heat treatment steps for S1 tool steel.
3.1 Preheating
Preheating is necessary for S1 tool steel before austenitizing. It reduces thermal shock, helps relieve machining stresses, and can improve furnace productivity.
Procedure: Heat to 1200-1250°F (650-677°C). Hold for 10-15 minutes, or until uniformly heated. Rapid heating from preheat to austenitizing temperature is preferred.
3.2 Austenitizing (Hardening)
This step transforms the steel’s structure to austenite, dissolving alloying elements for hardening.
Procedure: Heat to 1725-1750°F (940-954°C). A range of 1550-1700°F (845-925°C) is also cited.
Soaking Time: Soak for 1 hour per inch of the smallest cross-section (e.g., 30 minutes for 1/8 inch). Adhere to soaking times rigidly, as excessive time can be detrimental.
3.3 Quenching
Rapid cooling transforms austenite into martensite. S1 is primarily an oil-hardening steel.
Procedure: Quench in oil to 125-150°F (52-65°C). Temper immediately. Air hardening may be possible for S1, but can be limited by section size.
3.4 Tempering
Tempering is performed immediately after quenching to relieve stresses, increase toughness, and adjust hardness. It also transforms retained austenite and precipitates fine carbides.
Procedure:
- Multiple Tempers: Multiple tempering cycles are highly recommended for S1 tool steel.
- Soaking Time: Soak for 2 hours per inch of cross-section thickness for each temper.
- Temperature Range: The general tempering range for S1 is 350-1000°F (175-540°C).
- Lower temperatures (e.g., 300-600°F / 149-316°C) yield higher hardness.
- Higher temperatures reduce hardness but can maximize toughness.
- Hardness typically ranges from about 58 HRC (as-quenched) down to around 41 HRC (tempered at 1000°F/540°C).
- Cooling: Cool slowly in still air.
4. Applications of S1 Tool Steel
The distinctive blend of toughness and shock resistance makes S1 tool steel a dependable material for a wide array of challenging industrial applications. If your manufacturing processes involve tools or components that are regularly subjected to heavy impacts or high-stress scenarios, S1 provides a robust and reliable material solution.
The following table outlines common S1 tool steel applications and highlights why it’s selected for these tasks:
Application Category | Specific Examples | Key Benefits of S1 Tool Steel in these Applications |
Impact & Cutting Tools | Hand chisels, pneumatic chipping chisels (S1 is sometimes referred to as “tungsten chisel steel” for this use), various punches (including piercing, trimming, and draw punches), shear blades for cold shearing of heavy stock and scrap materials. | The superior toughness of S1 tool steel prevents premature chipping, cracking, or catastrophic failure when subjected to repeated blows or intense cutting forces. |
Forming & Stamping | Cold forming dies, stamping dies, cold-heading tools (especially for intricate shapes), rivet sets, and material stamps. | S1 offers excellent shock resistance and good compressive strength, enabling it to withstand the severe, often repetitive, forces encountered in these forming and stamping operations. |
Specialized Cold Working | Mandrels, rolls, and various other tools utilized in demanding cold drawing and forming processes. | The inherent toughness of S1 is a critical attribute for tools that must endure substantial operational stress without fracturing, ensuring tool longevity. |
Moderate Hot Work Uses | Certain types of hot shearing blades, some hot working punches where temperatures are not extreme. | The tungsten content in S1 provides the capability to maintain structural integrity and hardness at moderately elevated temperatures, typically up to around 1000°F (540°C). |
Structural & Machine Parts | Various machine elements such as cams, shafts, spindles, gears, and sprockets that experience impact loading. | S1 tool steel provides a dependable option for components that require a combination of high strength and the ability to absorb shocks and impacts during operation. |
Plastic Molding | Small to medium-sized inserts for plastic injection molds. | In these applications, S1 offers enhanced toughness compared to alternative tool steels like D2, significantly reducing the risk of insert cracking and extending mold life. |
5. Important Considerations for S1 Tool Steel Selection
While S1 tool steel delivers excellent performance characteristics for its intended applications, prospective users should be mindful of the following points:
- Availability: In today’s market, the widespread use of S1 has seen some decline, with grades like S5 or S7 tool steel becoming more commonly stocked by suppliers. This might influence the immediate availability of S1. However, for those specific, critical applications where maximum toughness is paramount to prevent cracking under severe impact conditions, S1 tool steel remains an exceptionally valuable and effective material choice.
- Heat Treatment Precision: Achieving the optimal balance of hardness and toughness in any S1 tool steel component is critically dependent on executing the correct heat treatment protocol. The tempering cycle, in particular, is vital for fine-tuning these properties to ensure maximum service life and performance from the tool or part.
6. Equivalent grade
- DIN: 1.2550
- China GB: 6CrW2Si or 5CrW2Si
- Roberts, G., Krauss, G., & Kennedy, R. (1998). Tool steels (5th ed.). ASM International. ↩︎
FAQ
DIN: 1.2550, 60WCrV8
GB: 5CrW2Si or 6CrW2Si
JIS: SKS41
AFNOR: 55WC20
BS: BS1
UNS: T41901
S1 is a general-purpose, oil-hardening, shock-resisting tool steel. It is primarily designed for applications that encounter repetitive impact stresses, such as chisels, shear blades, and rock drills. S1 steel exhibits high toughness and fracture resistance under impact loading conditions, while also possessing excellent strength and wear resistance. Its composition includes tungsten, chromium, molybdenum, and silicon, which contribute to its hardness and hardenability.
S1 is an oil-hardening tool steel, while S7 is a free-hardening tool steel. S7 steel achieves a maximum hardness of 58 HRC, whereas S1 can reach a maximum hardness of 63-64 HRC.
S1 tool steel typically has a tempered working hardness ranging from 50 to 58 HRC, depending on its specific carbon content and the tempering conditions applied1130. When oil-quenched, S1 can achieve an as-quenched hardness as high as 63–64 HRC before subsequent tempering29.
Get a Competitive Quote for S1 Tool Steel
With over 20 years of forging expertise, Aobo Steel is your trusted partner for high-performance S1 tool steel. We provide not just materials, but solutions. Leverage our deep industry knowledge and reliable supply chain for your project’s success.
✉ Contact us by filling out the form below.
Explore Our Other Products
D2/1.2379/SKD11
D3/1.2080/SKD1
D6/1.2436/SKD2
A2/1.23663/SKD12
O1/1.2510/SKS3
O2/1.2842
S1/1.2550
S7/1.2355
DC53
H13/1.2344/SKD61
H11/1.2343/SKD6
H21/1.2581/SKD7
L6/1.2714/SKT4
M2/1.3343/SKH51
M35/1.3243/SKH55
M42/1.3247/SKH59
P20/1.2311
P20+Ni/1.2738
420/1.2083/2Cr13
422 stainless steel
52100 bearing steel
440C stainless steel
4140/42CrMo4/SCM440
4340/34CrNiMo6/1.6582
4130
5140/42Cr4/SCR440
SCM415