When selecting materials for your tooling, it is important to understand the differences between grades like O1 and O2 tool steel. Both are common in the O-series of oil-hardening tool steels, but their characteristics can affect your manufacturing.
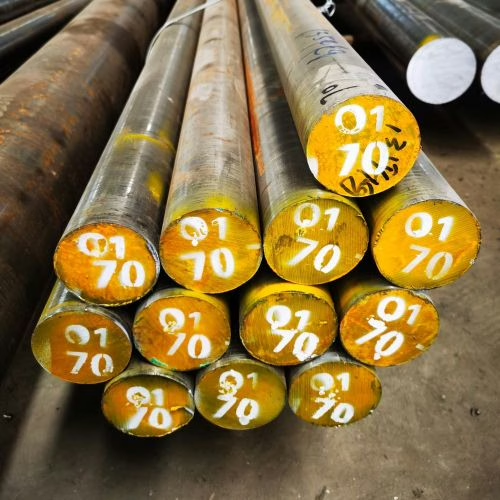

The Bottom Line Up Front
For factory managers and engineers comparing O1 and O2:
O1 tool steel is a well-documented, reliable, and versatile option, making it a standard for many general-purpose tool and die applications. It offers a good balance of wear resistance, toughness, and machinability.
O2 tool steel shares O1’s oil-hardening classification and cost-effectiveness. However, detailed public data on its specific performance, mechanical properties, and heat treatment are less available than for O1. Choosing O2 may mean relying more on supplier data or conducting more in-house validation, especially for critical applications.
O1 and O2: Shared Characteristics
O1 and O2 are manganese-based, oil-hardening, cold-work tool steels.
- Oil Hardening: Designed for oil quenching, leading to less distortion and cracking risk than water-hardening steels.
- Good Stability: Offers improved dimensional stability during heat treatment compared to water-hardening grades.
- Toughness: Can provide toughness comparable to water-hardening steels when properly hardened.
- Wear Resistance: Typically offers slightly better wear resistance than water-hardening steels with similar carbon content.
- Availability and Cost: Generally readily available and considered inexpensive tool steel grades.
O1 Tool Steel: A Closer Look
O1 is a widely used O-series tool steel due to its well-documented properties and extensive practical experience.
Chemical Makeup of O1
A typical composition for O1 tool steel includes:
- Carbon (C): ~0.90-0.95%
- Manganese (Mn): ~1.00-1.40%
- Silicon (Si): ~0.30%
- Chromium (Cr): ~0.40-0.60%
- Tungsten (W): ~0.40-0.60%
- Vanadium (V): ~0.20% (sometimes present)
The high carbon, along with manganese, chromium, and tungsten, contributes to its hardness, hardenability, and wear resistance.
Performance Profile: Hardness, Wear, and Strength
O1 achieves high hardness (typically 57-62 HRC, can be quenched to 64-65 HRC before tempering), providing good edge retention and wear resistance. Its composition gives it good wear performance and compressive strength suitable for forming and stamping.
Working with O1: Machinability and Heat Treatment
O1 offers excellent machinability in its annealed state, simplifying the creation of complex tools.
Key heat treatment points for O1:
- Hardening: Austenitize around 1450-1500°F (788-816°C), then oil quench.
- Tempering: Typically 300-500°F (149-260°C) to balance hardness and toughness.
- Decarburization: Susceptible to surface carbon loss; controlled atmosphere or protective wrap is recommended during heat treatment.
- Dimensional Change: Expect slight expansion upon hardening (approx. 0.0015 in./in.).
O2 Tool Steel: Understanding the Nuances
O2 is also a manganese oil-hardening grade, fundamentally similar to O1.
What We Know About O2
O2 is designed for good hardness and wear resistance in cold-work applications and is generally inexpensive. It may have a slightly lower resistance to softening during tempering compared to some other tool steels like A2. Manganese is its primary hardening element.
The Data Consideration
A key difference is that comprehensive public data on O2’s specific mechanical properties, fracture characteristics, and detailed heat treatment responses is less extensive than for O1. While suppliers provide specifications, O2 is not as universally characterized. This means factories might need to rely more on supplier-specific data or conduct more internal verification for critical uses.
Making Your Decision: O1 or O2?
How to choose for your workshop:
Why O1 is Often the Default
For many general-purpose tools, dies, and wear parts, O1 is often preferred due to its well-understood properties, predictable performance, excellent machinability, and balanced wear resistance and toughness. The extensive data and industry experience make O1 a reliable, lower-risk option.
When O2 Might Be Considered
O2 can be viable if:
- Your supplier provides robust data for their specific O2 grade.
- The application is less critical, or you have resources for validation.
- A specific O2 variant offers a particular characteristic beneficial for your application, and cost is a significant driver.
Ultimately, selecting the right tool steel involves understanding your application’s specific demands. Consulting with experienced steel suppliers is always recommended to ensure you get the best material for your factory’s needs.
Need High-Quality O1 or O2 Tool Steel?
Leverage Aobo Steel’s 20+ Years of Expertise for Your O1 & O2 Tool Steel Requirements.
Whether you need O1 for its excellent wear resistance and toughness, or O2 for its superior machinability and edge retention, our specialists are here to provide tailored advice and competitive pricing. We ensure you get the right steel for your application.
Ready to Discuss Your Project or Get a Quote?
Simply fill out the form below, and our expert team will get back to you promptly!