O1 tool steel is a general-purpose, oil-hardening tool and die steel, offering good abrasion resistance and sufficient toughness for a wide range of tooling applications. With proper O1 steel heat treatment, it provides good results in hardening with minimal dimensional changes and sufficient hardenability for adequate depth and surface hardness in most tools. Understanding the correct heat treatment procedures is crucial for achieving optimal performance. For more O1 steel, please click O1 steel technical overview.
We provide a free download of the O1 steel heat treatment PDF at the bottom of the page.
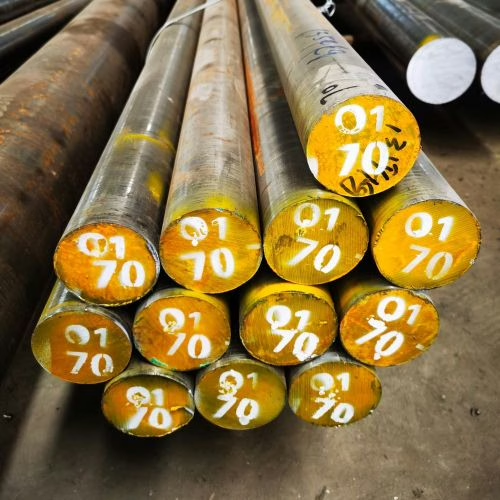
1. Typical Heat Treatment Process for O1 Tool Steel
The following outlines the typical O1 steel heat treatment process.
1.1 Loading the Furnace and Preheat Cycle
When starting with a cold furnace, place the O1 part in the center on the rack and close the door. Set the controller for a preheat temperature.
- Preheat Temperature: A standard preheat temperature for O1 is 1200°F (650°C).
- Heating Rate: Oil hardening steels like O1 can be heated quickly and can even be placed directly into a furnace preheated to this temperature.
- Minimizing Thermal Shock: To reduce the potential for cracking, it is good practice to first place the part on top of the furnace to remove any chill before loading it inside.
1.2 Austenitizing and Soak Time
After the preheat, elevate the temperature to the austenitizing point.
- Austenitizing Temperature: For O1, the austenitizing temperature is typically set to 1500°F (815°C). Some sources indicate a range between 802–816°C (1476-1501°F).
- Soaking: Hold the steel at this elevated temperature until it’s uniformly hot throughout. For O1, soak until the part reaches the austenitizing temperature, then add 5 minutes per inch of the smallest cross-section, or until you are certain the part is thoroughly soaked.
- Benefits: The high carbon content of O1 allows austenitizing at a relatively low intercritical temperature where austenite and carbides coexist. This helps maintain a fine grain size while still achieving high hardness and good hardenability after quenching.
1.3 Quenching
Following austenitizing, the steel needs to be rapidly cooled to form martensite, which is crucial for achieving high hardness.
- Quenching Medium: O1 is an oil-hardening steel, so it is typically quenched in oil.
- Procedure: After soaking, the O1 part is quenched in oil.
- Target Temperature: Quench the part to a temperature range of 150–200°F (66–93°C) and then temper it immediately. Quenching, especially oil quenching for O1, can result in some retained austenite along with the desired martensite structure.
1.4 Tempering Cycle
Tempering is a critical step immediately following quenching. It is vital that tempering begins as soon as the parts cool down to 125 to 150°F (52 to 65°C). Tempering involves reheating the steel to an intermediate temperature, always below the critical transformation temperature. This process increases the toughness of the steel and reduces the high internal stresses that make quenched steel susceptible to cracking. Tempering also decreases hardness and strength while increasing ductility as the temperature is increased.
- Typical Tempering Temperatures: The most commonly used tempering temperature for O1 is 350°F (175°C), though the normal tempering range is considered to be 300–450°F (149–232°C).
- Soak Time: The soak time for tempering is typically 2 hours per inch (25mm) of cross-section. It is important not to undertemper parts.
Table: O1 Steel Tempering Temperatures and Expected Hardness (HRC). For more information, please click O1 tool steel rockwell hardness.
Tempering Temperature | Expected Hardness (Rockwell C) |
As Quenched | 64–65 HRC |
300°F (150°C) | Approx. 63 HRC |
350°F (177°C) | 62–63 HRC |
400°F (205°C) | Approx. 62 HRC |
900°F (482°C) | Approx. 47 HRC |
- Double Tempering: While single tempering is often sufficient for oil-hardening steels like O1, double tempering may sometimes be preferred. Double tempering involves two complete tempering cycles at substantially the same temperature to ensure the tempering reaction is complete and to promote microstructural stability. If you double temper O1, soak for 2 hours per inch (4.7 minutes/mm) of thickness for each temper, cooling to room temperature in air between cycles.
2. Other Considerations for O1 Steel Heat Treatment
Several other factors should be considered during the O1 steel heat treatment process.
2.1 Dimensional Stability
- When oil quenched from the proper hardening temperature, O1 is expected to expand approximately 0.0015 in./in. (0.0015 mm/mm).
- Distortion like bending, bowing, or twisting can also occur due to part geometry and can add to the dimensional changes.
2.2 Decarburization
- O1 is susceptible to decarburization during heat treatment.
- To avoid this, annealing and/or hardening should be done in a controlled neutral atmosphere, vacuum, or a neutral-salt furnace.
2.3 Cracking and Stress
- Quenched steel is in a highly stressed state and prone to cracking. O1 is subject to cracking from the thermal shock of oil quenching.
- Using a preheat cycle helps reduce this risk.
- If significant grinding, welding, or EDM is performed after hardening, a stress-relief temper is strongly recommended, typically at a temperature 25–50°F (14–28°C) lower than the last tempering temperature used.
2.4 Straightening
- Most steels can only be straightened while their temperature remains above 400°F (205°C).
It’s crucial to grasp these correct heat treatment procedures first. Always refer to your specific steel manufacturer’s recommendations for precise time and temperature graduations for the best results with your particular material batch.
Premium O1 Tool Steel: Get Your Expert Quote from Aobo Steel
Tap into Aobo Steel’s 20+ years of specialized forging experience. We deliver top-quality O1 tool steel, precision-engineered for your demanding applications.
Our dedicated experts are ready to help you find the perfect material solution and optimize your project’s success.
Ready for superior performance and reliability?
Complete the form below to discuss your requirements and receive your personalized, no-obligation quote!