This page details the O1 steel hardness characteristics, a general-purpose oil-hardening tool steel. It is frequently supplied for cold-work applications such as dies, punches, gauges, and machinery components. For more O1 steel information, please click O1 steel technical overview.
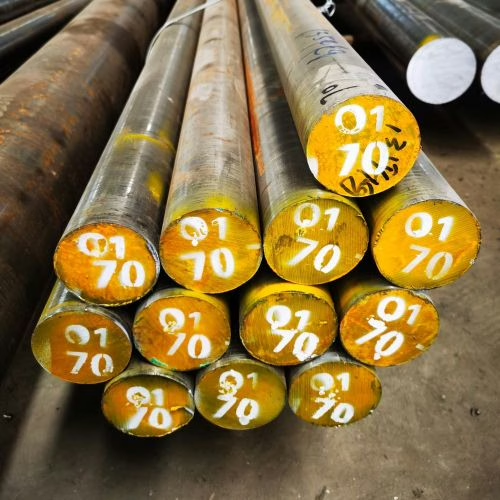
Understanding O1 Steel Composition and Initial Hardness
The O1 steel hardness is primarily derived from its high carbon content (around 0.90%) and manganese (around 1.20%), with some chromium, tungsten, and vanadium. This composition allows for the formation of martensite with high hardness upon quenching. O1 steel can harden to 62-63 Rockwell C (HRC) after heating to its critical temperature and quenching in oil.
Heat Treatment for Achieving Desired O1 Steel Hardness
Proper heat treatment, including austenitizing, quenching, and tempering, is crucial for achieving the target O1 steel hardness. Each step plays a vital role in determining the final mechanical properties of the steel.
Austenitizing O1 Steel
O1 steel is typically hardened from a relatively low austenitizing temperature, generally around 802–816 °C (1475–1500°F).
Increasing the austenitizing temperature can potentially increase hardenability. This may contribute to higher surface hardness by dissolving more alloying elements and excess carbides into the austenite.
Caution: Significantly raising the hardening temperature beyond the recommended range can negatively impact the steel’s toughness and increase the likelihood of cracking during quenching.
Quenching O1 Steel
O1 is classified as an oil-hardening steel. This is due to its alloy content, which provides sufficient hardenability for hardening sections of reasonable size using an oil quench.
It has a significantly deeper hardening capacity when compared to other O-series steels like O7 steel. The choice of quenching medium and technique is critical to achieve the desired hardness without introducing excessive internal stresses or distortion.
Tempering O1 Steel
After quenching, tempering is a critical step to adjust the final O1 steel hardness and other mechanical properties, such as toughness and ductility.
O-type steels, including O1, exhibit a continuous softening characteristic as the tempering temperature increases. To retain high hardness, which is essential for applications requiring good wear resistance and edge-holding capabilities, O1 is typically tempered at low temperatures. The common tempering range is between 150 and 260 °C (300 and 500 °F).
While higher tempering temperatures will increase the toughness of the steel, they will concurrently decrease its hardness and strength. The selection of the tempering temperature must be carefully balanced based on the specific application requirements for the O1 tool steel.
Learn more about O1 steel heat treatment.
Typical O1 Steel Hardness Ranges
After tempering, the typical hardened O1 steel hardness range is 57 to 64 HRC. For most die applications using O1, O2, or O6 steels, surface hardnesses ranging from 56 to 62 HRC provide suitable mechanical properties. This is typically obtained after oil quenching, followed by tempering from 175 to 315 °C (350 to 600 °F). The normal working O1 steel hardness range is generally cited as 58-60 HRC, though it can range from 57 to 62 HRC.
Heat Treatment Aspect | Typical Hardness (HRC) | Notes |
After Oil Quenching | 62-63 HRC | From critical temperature. |
Tempered (General Range) | 57-64 HRC | Final hardness depends on tempering temperature. |
Tempered (Die Applications) | 56-62 HRC | Tempering typically 175-315°C (350-600°F). |
Common Working Hardness | 58-60 HRC | Can range from 57 to 62 HRC. |
In the usual working hardness range of 57 to 64 HRC, O1 exhibits good impact toughness compared to other O-type steels like O2 and O7.
Hardenability of O1 Steel
O1 steel can be through-hardened in sections up to approximately 50 mm (2 inches) in diameter. For example, bars up to 63.5 mm (2.5 inches) in diameter can be through-hardened when oil quenched from 800 °C (1475°F). For larger tools, the hardenability of O1 may not be sufficient to achieve uniform O1 steel hardness.
Summary
O1 steel achieves high O1 steel hardness levels, typically 56-62 HRC after quenching and low-temperature tempering, making it suitable for demanding cold-work tooling. Its heat treatment response and hardenability make it a versatile choice for tooling needs, particularly in sections up to around 50 mm (2 inches) in diameter.
Premium O1 Tool Steel: Get Your Expert Quote from Aobo Steel
Tap into Aobo Steel’s 20+ years of specialized forging experience. We deliver top-quality O1 tool steel, precision-engineered for your demanding applications.
Our dedicated experts are ready to help you find the perfect material solution and optimize your project’s success.
Ready for superior performance and reliability?
Complete the form below to discuss your requirements and receive your personalized, no-obligation quote!