As with all tool steels, L6 tool steel heat treatment is critical to achieving the best performance. The process typically involves a sequence of preheating, austenitizing (hardening), quenching, and tempering.
What is L6 tool steel? L6 is a low-alloy special-purpose tool steel.
L6 steel composition1 includes:
- Carbon (C): 0.65-0.75%
- Manganese (Mn): 0.25-0.80%
- Silicon (Si): 0.25%
- Chromium (Cr): 0.60-1.20%
- Nickel (Ni): 1.25-2.00%
- Molybdenum (Mo): Up to 0.50% (in some variants)
Nickel acts as an austenite-stabilizing element, contributing to solid-solution strengthening without forming carbides, while chromium is a ferrite-stabilizing and carbide-forming element. L6 steel has high toughness, good impact resistance, and low-temperature wear resistance. It has moderate hardenability and low resistance to softening and thermal hardness, making it unsuitable for use in high-temperature environments. L6 also boasts good machinability, grindability, and safety in hardening, with good resistance to cracking.
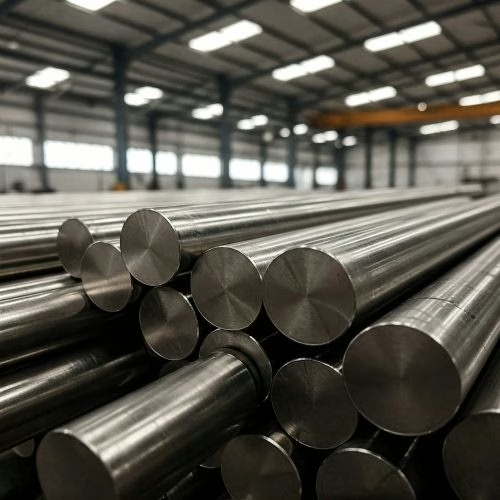

Preheating
Preheating is a necessary operation for virtually all tool steels, including L6. It preconditions the material’s molecules for transformation and helps relieve stresses from previous manufacturing steps, such as machining. The preheat temperature is 650°C (1200°F). The steel should be held at this temperature for 10 to 15 minutes, or until uniformly heated. For large or intricate sections, it’s advisable to heat slowly through the critical temperature range of 650 to 760°C (1200 to 1400°F). Prolonged soaking at the preheat temperature should be avoided as it can disrupt the molecular structure.
Austenitizing(hardening)
This is the second step in the heat treatment process. The recommended austenitizing temperature for L6 is in the range of 790-845°C (1454-1553°F). We recommend a specific temperature of 830°C (1525°F). The entire material should reach this temperature completely; do not keep it warm for an extended period. During austenitizing, the L6 steel is heated to a temperature where its ferrite-pearlite structure transforms into austenite, and various complex alloy carbides begin to dissolve.
Quenching
Following austenitizing, the steel is rapidly cooled to transform the austenite into the hard martensitic structure. L6 steel is an oil-hardening tool steel, and oil quenching is the preferred medium. Oil quenching is generally considered a safer method than water quenching, as it minimizes thermal shock and internal stresses. To minimize dimensional changes, parts can be removed from the oil just below its flash point (around 204°C / 400°F) and then cooled in air to below 65.5°C (150°F). As-quenched hardness for L6 is approximately 64 HRC.
Tempering
Tempering is a critical post-hardening treatment that reduces internal stresses, improves toughness, and adjusts the final hardness of the steel. The tempering temperature range for L6 typically falls between 175 °C and 540°C (350°F and 1000°F). The specific tempering temperature depends on the final hardness required for L6. For example, for general tool and die work, a tempering range of 177-260°C (350-500°F) is common to achieve a hardness of 58-62 HRC. For applications requiring a higher degree of toughness, such as chisels, higher tempering temperatures (e.g., 550-600°F / 288-316°C) may be used. Hardness of L6 continuously decreases with increasing tempering temperature.
Some manufacturers recommend a single tempering process for L6, but we recommend two or even three tempering processes. Multiple tempering helps to reduce retained austenite, precipitate carbides, and further relieve internal stresses, thereby enhancing wear resistance and overall stress relief. Each tempering cycle should typically be held for a minimum of two hours, or one hour per inch of cross-section for parts thicker than two inches.
The above is the heat treatment process for L6 steel. Some of these are our customers’ treatment solutions, while others are from professional technical documentation. Additionally, the equivalents of L6 tool steel are:
- Europe (EN/DIN): 1.2714/55NiCrMoV7 (or 56NiCrMoV7 or 55NiCrMoV6)
- Japan (JIS): SKT4
- China (GB): 5CrNiMo
If you are interested in L6/1.2714 tool steel or have any questions about it, please do not hesitate to contact us at your convenience.
- Davis, J. R. (Ed.). (1998). Metals Handbook Desk Edition (2nd ed). ASM Internationa ↩︎
Get a Competitive Quote for L6/1.2714 Tool Steel
With over 20 years of forging expertise, Aobo Steel is your trusted partner for high-performance L6/1.2714 tool steel. We provide not just materials, but solutions. Leverage our deep industry knowledge and reliable supply chain for your project’s success.
✉ Contact us by filling out the form below.