So, the big question: is P20 steel weldable? Yes, it absolutely is. P20 steel is commonly welded, particularly for repairing and modifying molds and dies. However, it’s not as straightforward as welding basic carbon steel. P20 is a specialized alloy tool steel, and to weld it successfully without issues, you need to follow specific procedures and take certain precautions. Getting this right is key to maintaining the integrity and performance of your valuable tooling.
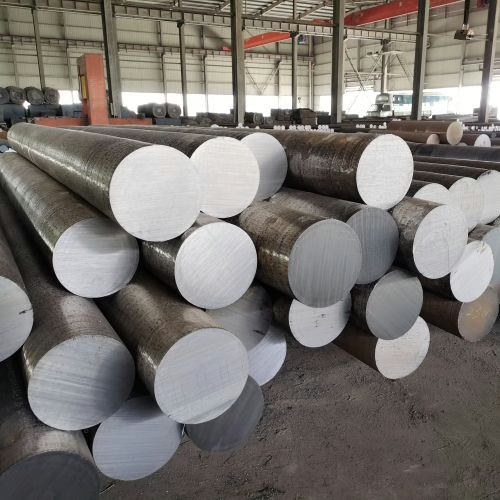
Understanding P20 Steel and Its Welding Characteristics
P20 is a well-known pre-hardened mold steel, valued for its balance of toughness, machinability, and polishability. Its typical composition includes elements like carbon (usually in the 0.3-0.4% range, though some variants differ), chromium, molybdenum, and manganese. These alloying elements give P20 desirable properties, but also mean it behaves differently under the intense heat of welding than mild steel.
The main challenge with welding P20 lies in its hardenability and alloy content. If not handled correctly, these factors make it more susceptible to issues like cracking in the weld area or the heat-affected zone (HAZ). The thermal stresses from welding can be significant, and managing them is crucial.
Key Factors for Welding P20 Steel Successfully
Several factors need careful attention to ensure a strong, reliable weld on P20 steel. Consider these non-negotiable steps for your workshop.
The Right Welding Method
For P20 steel, Gas Tungsten Arc Welding (GTAW), also commonly known as TIG welding, is a highly recommended process. TIG welding offers excellent control over the heat input and the weld pool, which is vital when dealing with alloy steels like P20. This precision helps in minimizing the risk of defects.
Choosing Your Filler Material Wisely
Selecting the correct filler wire is critical. You’re not just filling a gap; you’re aiming to create a weld that meets specific performance requirements.
- Matching Filler Metals: Ideally, use a filler material specifically designed for P20 or one with a very similar chemical composition. This helps ensure that the welded area has comparable hardness, strength, and wear resistance to the parent P20 material.
- Lower Carbon P20-Type Fillers: For some repairs, especially larger ones where cost is a factor, filler wires with a composition similar to P20 but with a lower carbon content are available. These can be a good option and are often suitable for subsequent surface treatments like nitriding.
- Specialized Alloy Fillers (e.g., 312 Stainless Steel): Sometimes, a filler like 312 stainless steel is used due to its excellent crack resistance and ability to join dissimilar or difficult-to-weld steels. While it’s very tough, its composition is quite different from P20. This means it might not be suitable if the repaired area needs to be highly polished, textured, or if a perfect cosmetic match is essential.
If you’re unsure about the best filler for your specific P20 application, always consult with your welding supplier or a metallurgist.
Heat Treatment: The Make-or-Break Step
This is arguably the most critical phase of welding P20 steel. Proper heat treatment before, during, and after welding is essential to prevent cracking and ensure the tool’s longevity.
- Preheating: Always preheat the P20 steel workpiece before you strike an arc. The exact preheat temperature can vary depending on the specific P20 grade and part thickness, but it’s typically in the range of 200-300°C (392-572°F). Preheating reduces the temperature difference between the weld area and the rest of the workpiece, minimizing thermal shock and the risk of cracking.
- During Welding: Interpass Temperature Control: Maintain the preheat temperature as your interpass temperature. This means ensuring the area doesn’t cool down too much between weld passes. Consistent temperature control is key.
- Cooling Down Slowly: Once welding is complete, the workpiece must be cooled slowly and uniformly. This can be achieved by wrapping it in an insulating blanket or burying it in a dry, insulating material like vermiculite. Rapid cooling is a primary cause of cracking in alloy steels.
- Post-Weld Heat Treatment (PWHT): After the part has cooled, a post-weld heat treatment is usually necessary. This typically involves:
- Stress Relieving: This process helps to remove internal stresses created during welding. For P20, stress relieving is often done at temperatures around 480-590°C (900-1100°F), holding for a specific time based on the thickness of the section, followed by slow cooling. This step is vital for dimensional stability and preventing premature failure.
- Tempering: If the welding process has significantly affected the hardness of the HAZ, or if the tool requires a specific hardness, tempering might be needed. For instance, if the P20 steel hardness is achieved through initial quenching and tempering, you may need to re-temper the affected area or the entire tool to restore the desired properties. A common practice for P20, if it has been hardened, is tempering around 200°C (392°F) to achieve good toughness and prevent cracking, often resulting in a 48 HRC or higher hardness.
Always refer to the steel supplier’s datasheet for specific heat treatment recommendations for the particular grade of P20 you are working with. We have another article on P20 heat treatment. Please click on the Is P20 steel a hardened steel?
Final Thoughts: Welding P20 with Confidence
To recap, P20 steel is weldable, and it’s a standard repair method in many industries. However, it demands a higher level of skill and attention to detail than welding simpler steels.
For factories relying on P20 tooling, understanding these welding principles is crucial. Success hinges on:
- Useing the proper welding process (TIG is preferred).
- Selecting the correct filler material for the job.
- Meticulously following the recommended pre-heating, interpass temperature control, slow cooling, and post-weld heat treatment procedures.
Adhering to these guidelines will help you effectively repair and maintain your P20 steel tools, extending their service life and ensuring they continue to produce quality parts. If you’re dealing with complex repairs or are new to welding P20, consulting with experienced tool steel welders or metallurgical experts is always a wise investment.
Ready to Source High-Quality P20 Tool Steel?
With over 20 years of forging expertise and a network of 40+ stable suppliers, Aobo Steel is your trusted partner for premium P20 tool steel. Get the best material for your molds and dies, backed by our extensive industry knowledge.
Fill out the form below to get a personalized quote or expert consultation!