At Aobo Steel, with our extensive experience in tool steel, we frequently receive questions about the best material for specific applications. A common one involves D2 tool steel and its suitability for demanding applications, often described as “chopping” – think shearing, blanking, or heavy trimming in manufacturing.
D2 steel is a popular choice for these cold-work tasks, and for good reason. Its main advantage is excellent wear resistance. Thanks to its high carbon (around 1.55%) and chromium (around 11.5%) content, D2 forms very hard carbides. These carbides withstand exceptionally well against the abrasive wear common in cutting and forming tools, resulting in longer tool life, particularly in high-volume production. For wear resistance, D2 is often the benchmark.
However, wear resistance isn’t the whole story. When it comes to operations involving significant impact – the “chopping” force – we need to consider toughness. D2 steel, while very wear-resistant, is not as tough as some other tool steels, particularly the shock-resisting grades, such as S7 tool steel. Its high hardness and carbide content make it more brittle in comparison. In applications with heavy impacts, such as punching thick materials or interrupted cuts, this lower toughness means D2 can be prone to chipping or even breaking.
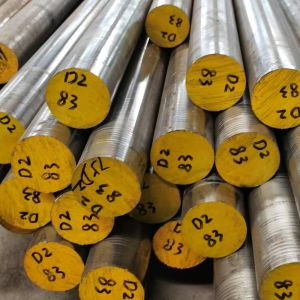
Does this mean D2 is unsuitable for chopping? Not necessarily. It has been successfully used in many blanking and trimming dies. Success hinges on a few key factors:
- Tool Design: Avoid sharp corners or thin sections in your tool design. These features create stress points where cracks can start, especially in less resilient materials like D2. Smart design minimizes these risks.
- Heat Treatment: Proper heat treatment is critical for D2. As an air-hardening steel, careful control over austenitizing and tempering temperatures is needed to balance hardness, wear resistance, and toughness. Incorrect heat treatment can significantly increase the risk of failure. Generally, lower tempering temperatures maximize hardness, while higher tempering temperatures can increase toughness slightly, but require careful process control.
- Application Severity: Assess the level of impact. If the primary failure mode is wear, and impacts are moderate, D2 is likely an excellent choice. If chipping or breaking is the primary issue, despite good design and heat treatment, D2 may not be tough enough.
Making the Right Choice
So, is D2 good for chopping? It excels where wear resistance is the top priority for long runs. But if your operation involves heavy impact and toughness is critical to prevent tool breakage, D2 might reach its limit.
If you consistently experience chipping or fractures with D2, even after optimizing design and heat treatment, it’s worth considering a tougher alternative. Steels from the S-series (such as S1 or S7) offer significantly better impact resistance, although you may trade off some wear resistance.
Choosing the right tool steel involves understanding the specific demands of your application – the forces involved, the material being cut, and the tool geometry. At Aobo Steel, we have the experience to help you evaluate these factors. D2 could be the perfect fit, or perhaps another grade would serve you better. Let’s focus on finding the solution that optimizes performance and lifespan for your tools.