When deciding between tool steels, specifically AISI A2 and AISI D2, it’s not just about which one is “better.” Both are excellent cold-work tool steels, but they shine in different situations. The key is understanding your specific needs and matching them to the right steel. Let’s break down their characteristics.
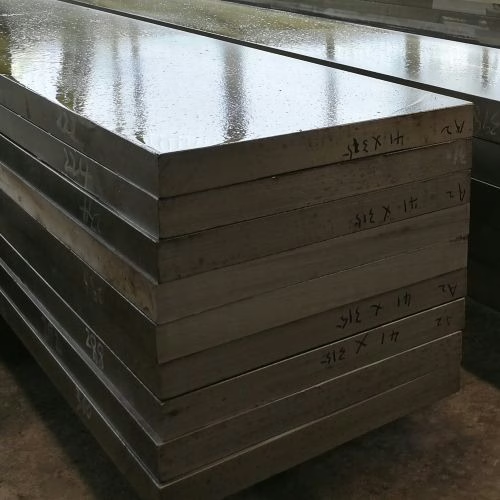

AISI D2 Tool Steel: The Abrasion Resistance Champion
D2 is a high-carbon, high-chromium steel. What does that mean in practical terms?
- Exceptional Wear Resistance: Thanks to its high carbon content (around 1.52-1.55%) and chromium content (around 11.50-12.05%), D2 is designed to resist abrasion. It contains a high volume of hard chromium carbides ( M7C3 type) in its structure. For applications where wear and tear over long production runs is the primary concern, D2 is often the benchmark. It offers significantly better wear resistance compared to A2.
- Toughness Considerations: While it excels in wear resistance, D2’s toughness is generally considered moderate to fair. If your application involves heavy impact or shock loading, D2 might be more prone to chipping or fracturing compared to A2.
- Heat Treatment & Stability: D2 is an air-hardening steel, which is ideal for minimizing distortion during heat treatment, typically hardened to a range of 58-62 HRC. It’s known for good dimensional stability. However, achieving peak hardness often involves lower tempering temperatures, which can leave some retained austenite. This might be a factor in very high-precision applications over time. Double tempering is usually a good practice for D2.
- Workability: Let’s be direct: D2 is more challenging to machine and grind due to its hardness and high carbide content. Welding also requires extra care.
- Common Uses: Think long-run stamping dies (blanking, forming, drawing), slitter knives, shear blades, and forming rolls – especially when you’re working with abrasive materials or need maximum tool life.
AISI A2 Tool Steel: The Balanced Performer
A2 is also an air-hardening tool steel, but it’s a medium-alloy type with lower carbon (approximately 1.00%) and chromium (approximately 5.00%) content compared to D2.
- Good Wear Resistance and Better Toughness: A2 offers a great middle ground. It provides good abrasion resistance – better than shock-resisting steels like the S-series – but significantly more toughness than D2. This makes it more resistant to chipping and breaking under stress or impact.
- Heat Treatment & Stability: Like D2, A2 is air-hardening, offering low distortion and reliability during heat treatment, typically achieving a hardness of 58-60 HRC. Its dimensional stability is excellent, although it might expand slightly more than D2 during quenching.
- Easier Machinability: A significant plus for A2 is that it’s much easier to machine and grind compared to D2. This can save time and cost during tool manufacturing.
- Common Uses: A2 is a versatile, general-purpose workhorse. It’s ideal for medium-run cold-work tools and dies, including forming, blanking, and trimming dies. It’s often the choice when you need a reliable balance between toughness and decent wear resistance, or when improved toughness is more critical than achieving the absolute maximum wear life.
So, Which Steel Should You Choose?
It boils down to your priorities:
- Choose D2 if:
- Your top priority is maximizing wear resistance for extended runs or when working with abrasive materials.
- You can manage its moderate toughness and the associated challenges of machining and welding.
- Choose A2 if:
- You need a solid balance of good wear resistance and improved toughness to prevent chipping and breakage.
- Easier machinability and potentially lower manufacturing costs are important factors.
- It suits general-purpose or medium-to-long run tooling needs.
Essentially, D2 pushes wear resistance to the limit, sometimes sacrificing toughness. A2 offers a more balanced profile, trading some top-end wear resistance for greater toughness and easier handling in the workshop.
The “better” steel is always the one that best fits the demands and manufacturing realities of your specific application. If you need assistance, please don’t hesitate to contact us at Aobo Steel. With our experience, we can help guide you to the right material.