Conclusion: While AISI A2 tool steel is a versatile and popular air-hardening, cold-work steel known for its good toughness and dimensional stability, it’s generally not the top recommendation for most knife applications. Its wear resistance is good, but is surpassed by other grades, such as D2 tool steel. Notably, it lacks the corrosion resistance typically desired in modern knife steels, particularly when compared to martensitic stainless grades designed explicitly for cutlery. However, its notable toughness might suit specific heavy-duty utility knives where chipping resistance is paramount and corrosion can be managed.
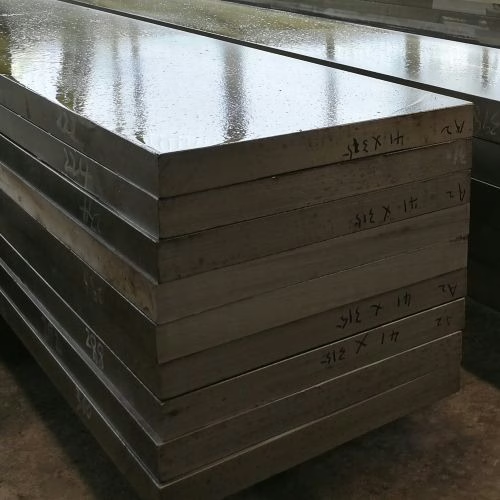
Understanding AISI A2 Tool Steel
AISI A2 tool steel is a well-regarded air-hardening, cold-work tool steel, widely used for various tooling applications. Let’s look at its composition and properties relevant to cutting tools.
Chemical Composition
Typically, A2 contains:
- Carbon (C): ~1.00%
- Chromium (Cr): ~5.25%
- Molybdenum (Mo): ~1.10%
- Vanadium (V): ~0.25%
- Manganese (Mn): Small amount
The 5% chromium content is crucial to its wear-resistant characteristics.
Key Properties for Knife Applications
When evaluating steel for knives, we primarily consider hardness, wear resistance, toughness, ease of maintenance (including machinability and grindability), and corrosion resistance.
Hardness
A2 steel can achieve a solid working hardness, typically between 58 and 60 HRC, and sometimes up to 64 HRC. This is essential for edge retention. This hardness level is comparable to D2 tool steel (often 58-62 HRC) but slightly lower than high-speed steels like M2 (60-65 HRC).
Wear Resistance
A2 steel offers good to excellent wear resistance, thanks to the chromium and vanadium carbides in its structure. It outperforms oil-hardening steels (like O1 tool steel) and shock-resistant steels (S-series) in this regard. However, it doesn’t match the higher wear resistance of grades like D2 tool steel (which has significantly more chromium and carbon) or specialized high-speed steels like M4 or T15. So, while good, it’s not the best available for pure abrasion resistance.
Toughness
This is where A2 steel often shines. It provides a better balance of toughness and wear resistance compared to the more brittle D-series steels, while being less tough but more wear-resistant than the S-series. Good toughness is vital for preventing chipping, especially in knives that might encounter impact. A2 steel is often chosen for punching tools where toughness is critical.
Dimensional Stability (Heat Treatment)
Being an air-hardening steel, A2 tool steel exhibits minimal distortion during heat treatment, with an expected expansion of approximately 0.001 inches per inch. This is a significant advantage for precision tools, such as dies, ensuring reliable and predictable results after hardening. While less critical for a knife’s performance profile than wear or toughness, it simplifies the heat treatment process.
Machinability and Grindability
A2 steel is relatively easy to machine and grind compared to many other types of tool steel. Its machinability rating (around 60-65, compared to 100 for 1% carbon steel) is better than D2 (around 45-60) and significantly better than highly alloyed grades like T15. This suggests A2 blades might be easier to sharpen and maintain compared to those made from higher-wear-resistant steels.
Corrosion Resistance
This is a significant factor for knife applications. A2, with its 5.25% chromium, is not a stainless steel. It does not have sufficient chromium to prevent rust effectively under typical conditions, especially compared to martensitic stainless steels (such as 410, 420 series, Sandvik 12C27, and Uddeholm AEB-L), which are designed explicitly for cutlery and offer good corrosion resistance alongside wear resistance. Non-stainless high-carbon steels generally require more care to prevent rust.
A2 Steel for Knives: The Verdict
A2 is a solid performer in the tool steel world, offering a great blend of toughness, reasonable wear resistance, and ease of heat treatment. It’s excellent for a wide range of dies and punches.
However, when it comes to most knife applications:
- Its wear resistance, while good, is lower than that of other available options, such as D2 or specialized powder metallurgy steels.
- Its lack of corrosion resistance is a significant drawback compared to stainless steels commonly used for knives, requiring diligent maintenance to prevent rust.
While A2 steel can be used for knives, its toughness is an asset for heavy-duty blades where chipping is a concern. However, it’s generally not the optimal choice for everyday carry, kitchen use, or applications that demand high edge retention combined with low maintenance. You’ll often find stainless steels or tool steels with higher wear resistance, such as D2, despite its trade-offs in toughness and grindability, being preferred.
Choosing the right steel always depends on the specific demands of the application. For general knife making, exploring dedicated cutlery steels, such as stainless or high-wear-resistant tool steels, may be more beneficial. However, if exceptional toughness is the primary need for a specific cutting tool, A2 remains a viable candidate.
✅ Get Instant Access to Premium A2 Tool Steel – Direct from Manufacturer!
- 📦 In-Stock and Ready to Ship: Sizes customized to your needs.
- 🏭 Factory-Direct Price: No middlemen. Save up to 15% instantly.
- 🛡 Quality Guaranteed: Full MTC (Material Test Certificate) provided.
- ⚡ Fast Response: Quote within 6 hours.
- 🎁 Limited Offer: Free cutting service for first-time customers.
👇Get Your Best Quote Now! Fast, free, no obligation.👇