H21 Tool Steel is a tungsten-based hot-work tool steel, classified under the AISI H-group. These types of steels were among the earliest high-alloy options developed for demanding high-temperature tooling applications. At Aobo Steel, with our extensive experience in tool steel forging, we understand the nuances of materials.
1. H21 Tool Steel Chemical Composition
The performance of H21 steel is largely determined by its alloying elements. A typical composition includes:
- Carbon (C): 0.26% – 0.36% (Provides hardenability and wear resistance)
- Manganese (Mn): 0.15% – 0.40% (Improves hardenability, acts as deoxidizer/desulfurizer)
- Silicon (Si): 0.15% – 0.50% (Increases strength and hardness, acts as a deoxidizer)
- Chromium (Cr): 3.00% – 3.75% (Enhances resistance to high-temperature oxidation and corrosion)
- Vanadium (V): 0.30% – 0.60% (Forms hard carbides, increasing wear resistance and hot strength)
- Tungsten (W): 8.50% – 10.00% (Key element for hot hardness, high-temperature strength, and wear resistance)
2. H21 Tool Steel Properties
2.1 Hardness and Heat Resistance
H21 steel is recognized for its good heat resistance and ability to maintain hardness at elevated temperatures, a critical factor in hot-work applications.
- Tempered Hardness: After austenitizing and tempering (e.g., 2 hours at 595°C / 1100°F), a hardness of approximately 529 HB can be achieved. Increasing the tempering temperature (e.g., to 650°C / 1200°F) reduces hardness to approximately 437 HB.
- Hot Hardness: At operating temperatures, hardness decreases. For instance, hot hardness might be around 280 HB at 595°C (1100°F) and 211 HB at 650°C (1200°F). (Based on typical data with initial room temp hardness of 444 HB).
2.2 Toughness and Ductility
While offering good hot strength, H21’s toughness and shock resistance are generally lower compared to chromium-based hot-work steels, such as H11 or H13. Its shock characteristics are also considered inferior to H19.
- The chosen tempering temperature and the cooling rate after hardening, such as oil quenching versus slower cooling, significantly influence impact toughness (Izod or Charpy V-notch).
- Torsional properties can vary significantly depending on the specific heat treatment parameters used to achieve the target hardness, typically within the 42-55 HRC range.
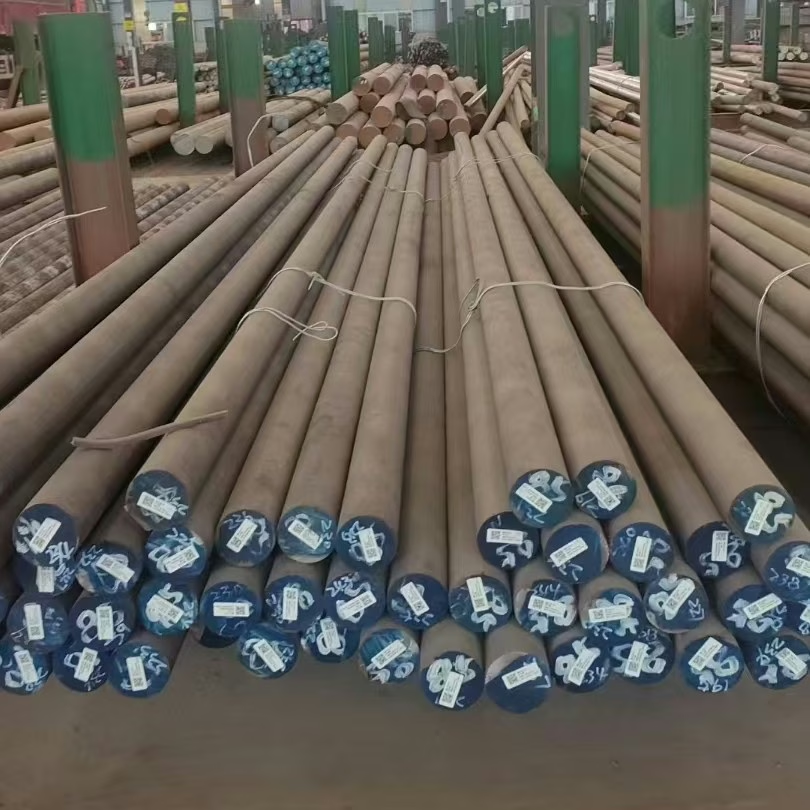
Are you looking for H21 tool steel? Please fill out the following form to contact us today!
3. Heat Treatment
Achieving the optimal performance from H21 tool steel relies heavily on a precise heat treatment process. This procedure develops the necessary hardness, wear resistance, and toughness essential for demanding hot work applications.
3.1 Preheating
Before the main hardening process, H21 tool steel must be carefully preheated.
- Temperature: Heat uniformly to 760–815 °C (1400–1500 °F).
- Purpose: This crucial step minimizes thermal shock and prevents cracking, especially in components with complex shapes or varying thicknesses. Slow and even heating ensures that the temperature is evenly distributed throughout the steel, preparing it for the high temperatures of austenitizing.
3.2 Austenitizing (Hardening)
Following preheating, the steel is brought to the austenitizing temperature.
- Temperature: Heat to 1095–1205 °C.
- Purpose: At this stage, the steel’s microstructure transforms into austenite. This allows carbon and critical alloying elements, such as tungsten (W) and chromium (Cr), to dissolve into the structure, which is fundamental for achieving hardness upon cooling.
Soaking at Austenitizing Temperature
Holding the steel at the austenitizing temperature (soaking) is vital.
- Duration: Typically 2 to 5 hours, depending on the cross-section thickness (allow sufficient time, e.g., 1 hour per inch of thickness).
- Purpose: H21’s high content of tungsten and chromium forms stable carbides. Sufficient soaking time ensures these carbides fully dissolve and distribute evenly within the austenite, leading to a uniform structure ready for quenching.
3.3 Quenching (Cooling)
Rapid cooling transforms the austenite into hard, martensitic steel.
- Methods: H21 steel can be quenched in either air or oil.
- Considerations: Due to its high hardenability, H21 readily hardens even with slower air cooling. Air quenching is often preferred as it significantly reduces the risk of distortion and quench cracking compared to more severe oil quenching, especially for larger or intricate parts. Oil quenching can be used if maximum hardness is the primary goal. The cooling rate must be sufficiently fast to prevent the formation of softer structures, such as pearlite or bainite.
3.4 Tempering
Quenched H21 steel is extremely hard but also brittle. Tempering is necessary to refine its properties.
- Temperature: Reheat the steel to 595–675 °C.
- Purpose: Tempering reduces brittleness and significantly improves toughness and ductility while retaining substantial hardness. The specific temperature and time used will determine the final balance between hardness and toughness.
- Multiple Tempers: For high-alloy tool steels like H21, performing two or more tempering cycles is common practice. This ensures structural stability, transforms any retained austenite, and can contribute to secondary hardening, further enhancing performance at elevated temperatures.
3.5 Important Process Controls
3.5.1 Preventing Decarburization
H21 steel is prone to decarburization, or the loss of carbon from the surface, at high heat treatment temperatures, resulting in a soft and weak surface layer.
- Solution: Protective measures are essential during austenitizing. This includes using controlled atmosphere furnaces, salt baths, or wrapping the parts in protective material like stainless steel foil.
3.5.2 Cooling After Forging
Due to H21’s high hardenability, forgings should be cooled slowly (e.g., furnace cooling or burying in insulation) immediately after the forging operation.
- Reason: Avoid normalizing (air cooling from high temperature), as this can cause the steel to partially or fully harden, leading to brittleness and potential cracking before the intended hardening and tempering process. Slow cooling ensures a more suitable structure for subsequent heat treatment.
This structured approach to heat treating H21 tool steel ensures the material delivers the high performance required for its intended hot work tooling applications. Precise control over each parameter is key to success.
4. H21 Tool Steel Applications
Thanks to its hot hardness and wear resistance, H21 steel is used in various hot-work processes:
- Forging Dies and Inserts
- Hot Work Punches, Piercers, and Mandrels
- Hot Extrusion Tooling
- Hot Shear Blades (especially for severe applications, sometimes alongside H25)
- Die Casting Dies (particularly for brass)
- Coining Dies (especially where some wear resistance can be traded for better breakage resistance in thin sections)
H21 is often considered a suitable choice for tooling intended for medium production runs.
5. H21 Tool Steel Equivalent grades
- European (EN): X30WCrV9-3 (1.2581)
- Germany (DIN): 1.2581
- Japan (JIS): SKD5
- France (AFNOR): 32CDV12-28
- China (GB): 3Cr2W8V
Need High-Performance H21 Tool Steel?
Leverage Aobo Steel’s 20+ years of forging expertise for your critical high-temperature applications. Our H21 Tool Steel offers exceptional toughness and heat resistance, ensuring reliability and longevity for your tools and dies.
Let our specialists provide you with tailored advice, superior quality H21 steel, and competitive quotes.
Ready to enhance your operations? Contact us today!
Simply fill out the form below to get started, and our experts will be in touch shortly.
Explore Our Other Products
D2/1.2379/SKD11
D3/1.2080/SKD1
D6/1.2436/SKD2
A2/1.23663/SKD12
O1/1.2510/SKS3
O2/1.2842
S1/1.2550
S7/1.2355
DC53
H13/1.2344/SKD61
H11/1.2343/SKD6
H21/1.2581/SKD7
L6/1.2714/SKT4
M2/1.3343/SKH51
M35/1.3243/SKH55
M42/1.3247/SKH59
P20/1.2311
P20+Ni/1.2738
420/1.2083/2Cr13
422 stainless steel
52100 bearing steel
440C stainless steel
4140/42CrMo4/SCM440
4340/34CrNiMo6/1.6582
4130
5140/42Cr4/SCR440
SCM415