At Aobo Steel, we know that achieving the correct H13 steel hardness is vital for your tools and dies. This guide provides essential technical information on H13 tool steel‘s hardness characteristics to help you optimize your die casting, forging, and plastic molding operations.
We offer a free download of the technical data of the H13 steel hardness PDF at the bottom of the page.
1. H13 Steel: An Overview
H13 is a chromium-molybdenum-vanadium (Cr-Mo-V) hot-work tool steel, known for its excellent red hardness, toughness, and thermal fatigue resistance. It’s a medium-alloy air-hardening steel used for:
- Die-casting dies
- Plastic-injection-mold tooling
- Forging tools
- Extrusion dies
The final hardness is determined by its composition and heat treatment.
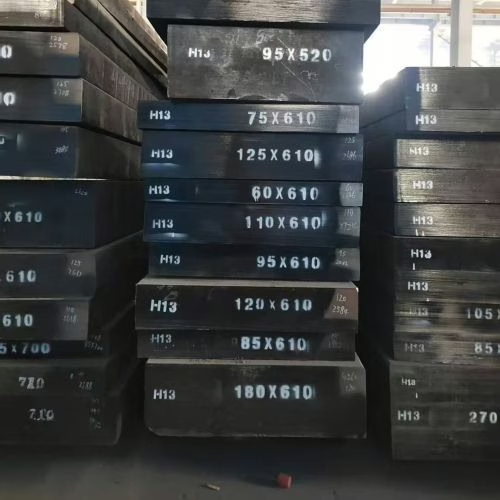
2. What is H13 Steel Hardness?
Hardness measures a material’s resistance to permanent deformation, like indentation. For H13 steel, it’s typically reported in Brinell (HB) or Rockwell C (HRC). Optimal hardness balances wear resistance, toughness, and heat resistance, crucial for tool longevity and factory productivity.
3. Typical H13 Steel Hardness Values
H13 steel hardness varies with its metallurgical state, mainly due to heat treatment.
3.1. Annealed Hardness
In its fully annealed condition, H13 steel has a maximum hardness of approximately 220 HB. This softer state is ideal for machining before hardening.
3.2. As-Quenched Hardness
After austenitizing and air cooling, H13 develops its as-quenched hardness:
- A 1-inch (25mm) cube typically reaches about 53 HRC.
- Larger sections (e.g., a 330 mm/13 in. diameter bar cooled from 1010 °C/1850 °F) might be around 45 HRC.
Higher austenitizing temperatures can increase the as-quenched hardness in smaller sections. Slower cooling in heavy sections can result in lower hardness. H13 is deep hardening, capable of hardening through sections up to about 2-1/2 inches (63.5 mm) in diameter with air quenching.
3.3. Tempered Hardness
The final working hardness comes from tempering after quenching. As a secondary hardening steel, H13 develops optimal properties when tempered above approximately 510 °C (950 °F), which also provides stress relief. A secondary hardening peak occurs around 540 °C (1000 °F) due to vanadium-rich MC carbide precipitation. Double tempering is recommended.
The achievable tempered H13 steel hardness ranges from 38 to 57 HRC.
It’s critical to select tempering parameters to balance hardness with toughness; for instance, tempering around 500°C (930°F) is often avoided as it can lead to high hardness but low toughness, risking premature cracking.
4. Optimizing Hardness for Applications
Correct H13 steel hardness is key to tool performance. For more information, please click H13 tool steel applications.
4.1. Controlled Tempering for Desired H13 Steel Hardness
Tempering fine-tunes H13 steel hardness to balance wear resistance, toughness, and stability at operating temperatures.
4.2. Recommended Hardness Ranges
Application | Recommended Hardness (HRC) | Notes |
General Die Casting Dies | 42–52 HRC | 47 HRC often preferred for aluminum. |
Die Casting Inserts, Cores, Slides | 46–52 HRC | Higher wear resistance. |
Die Casting Plungers | 46–50 HRC | Good wear and thermal shock resistance. |
Die Casting Shot Sleeves | 44–48 HRC | Resistance to wear and erosion. |
Die Casting Nozzles | 32–42 HRC | Improved toughness. |
Die Casting Tooling (Optimal) | 44–48 HRC | General working range. |
Tooling Requiring Shock Resistance | 40–44 HRC | Enhanced toughness. |
Forging Dies (Hammers/Presses) | 47–56 HRC | Maximize wear resistance; 53-56 HRC (min. severity), 47-49 HRC (max. severity). |
Extrusion Punches and Dies | 48–52 HRC | High wear resistance at elevated temperatures. |
Plastic Mold Applications | 40 HRC+ | Often 48-54 HRC or 54-56 HRC; may be nitrided. |
4.3. Surface Treatments for Enhanced H13 Steel Hardness
- Nitriding: Can achieve surface hardness near 1100 HV (>70 HRC) with a typical layer of 0.1-0.3 mm. The core (often ~45 HRC) remains tough. Ideal for hot wear applications.
- Boriding: Can produce surface microhardness around 1800 HV, significantly harder than standard hardened or nitrided H13.
5. The Basis of H13 Steel Hardness and Wear Resistance
Heat-treated H13’s wear resistance comes from:
- The hardness of its martensitic matrix.
- The presence of hard, undissolved alloy carbides (Vanadium-rich MC, Molybdenum-rich M6C, Chromium-rich M23C6). MC carbides can be around 84 HRC.
These carbides resist wear, especially at high temperatures.
6. Consistent H13 Steel Hardness with Aobo Steel
Achieving the target H13 steel hardness requires precise heat treatment control (austenitizing, quenching, tempering). While Aobo Steel supplies high-quality H13, we emphasize collaboration with experienced heat treaters to optimize your components for maximum life and efficiency.
For questions or to source H13 steel, contact Aobo Steel.
Expert H13 Tool Steel Solutions
Leverage Aobo Steel’s 20+ years of forging expertise for your H13 tool steel needs. We provide top-quality, certified materials tailored to your precise specifications.
Ready to enhance your project with superior H13 tool steel?
Fill out the brief form below to connect with our specialists and get your custom quote.