The objective of D6 tool steel heat treatment is to transform its annealed structure, consisting mainly of ferrite and alloy carbides, into a hardened and tempered martensitic structure. If heat treatment is not performed correctly, D6 steel may also exhibit poor performance.
What is D6 tool steel? D6 tool steel is a high-carbon, high-chromium cold-work tool steel. D6 tool steel’s high carbon content and high chromium content are key to its properties. Its microstructure contains a large amount of chromium-rich M7C3-type hard block-shaped alloy carbides. These carbides, combined with high base hardness (typically around 60 HRC after heat treatment), are the main factors contributing to the high wear resistance of D6 steel.
The equivalent grades of D6 tool steel include:
- DIN EN (Europe): 1.2436 (X210CrW12)
- JIS (Japan): SKD2
- BS (UK): BD6
- ISO: X210CrW12
D6 steel composition is C2.00 – 2.20%, Cr11.50 – 12.50%, W0.60 – 0.90%, Mn0.20 – 0.40%, Si0.10 – 0.40%. The heat treatment process involves several critical stages: preheating, austenitizing, quenching, and tempering.
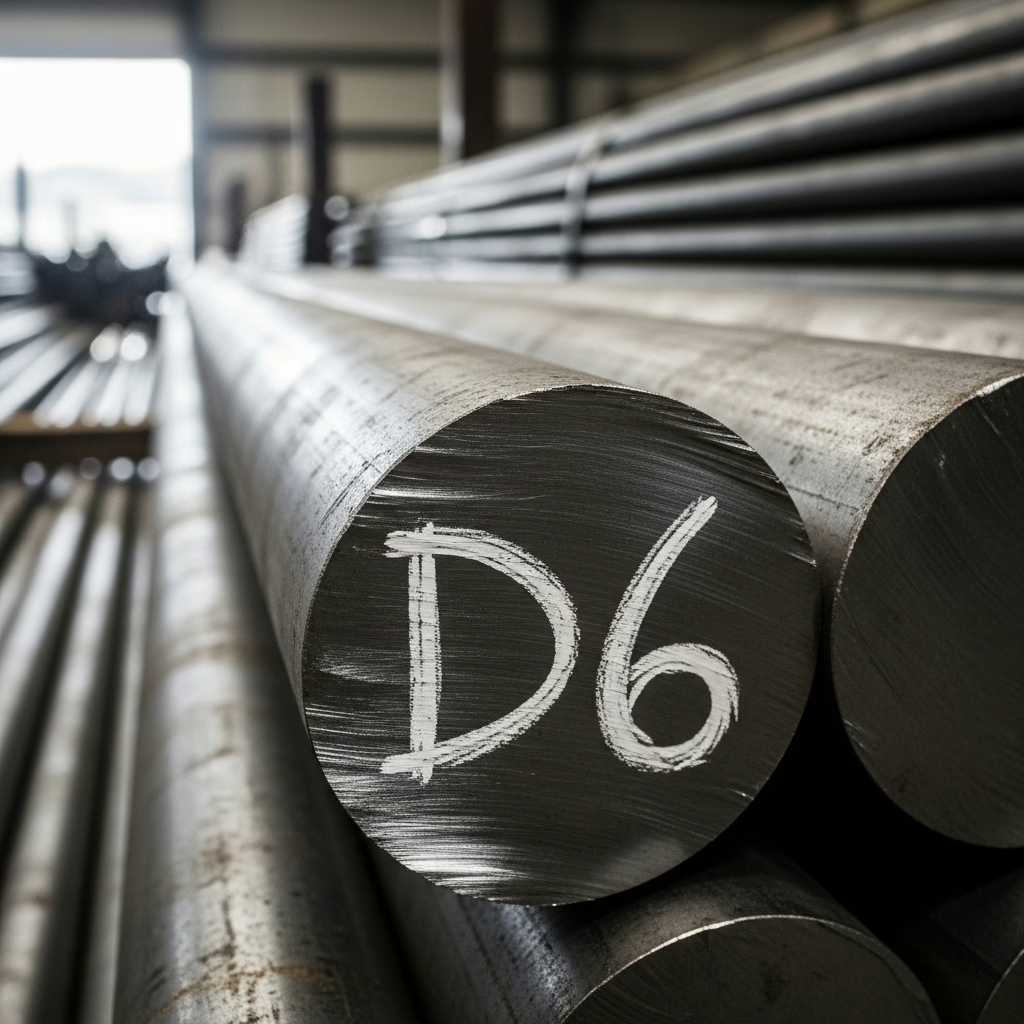
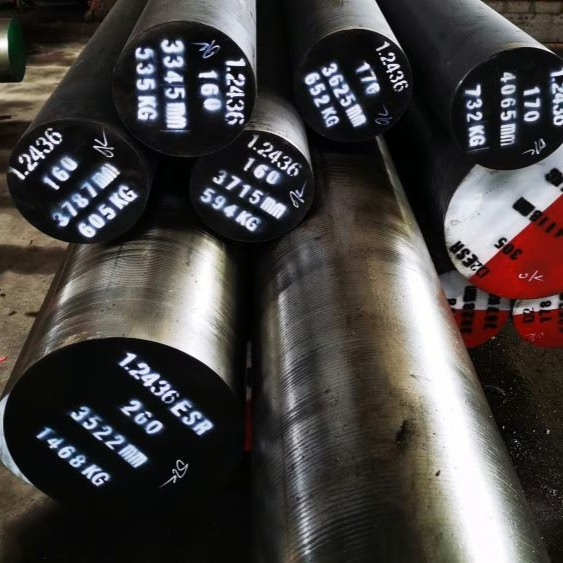
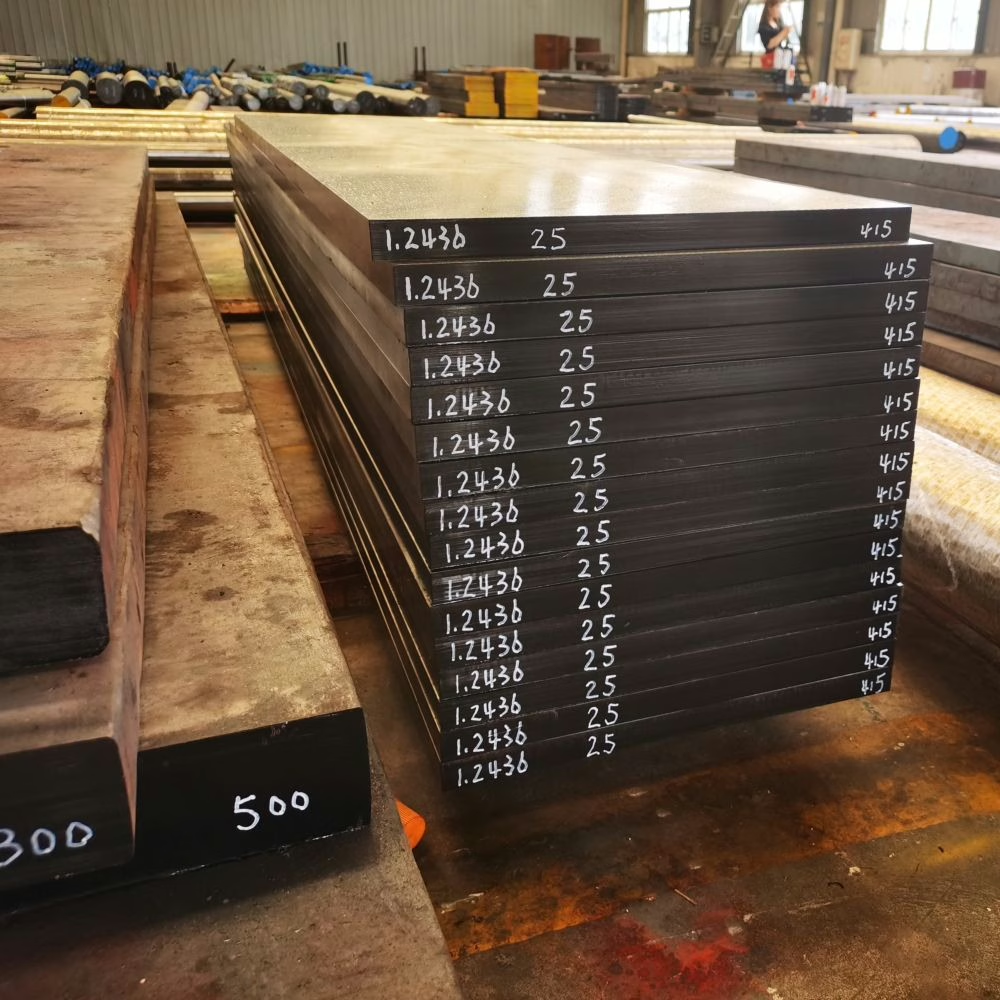
Preheating
D6 steel has low thermal conductivity, so we recommend slow and even heating. Preheating at temperatures between 650 to 705 °C (1200 to 1300 °F) helps prevent cracking and minimize distortion during the subsequent high-temperature stages. It also equalizes the temperature and minimizes the time required at the higher-temperature austenitizing stage.
Austenitizing(hardening)
This step involves transforming the structure of D6 steel into austenite and dissolving most of the carbides at high temperatures. The hardening temperature is typically around 960°C (1760°F). The material should be heated in neutral atmospheres, salt baths, or vacuum furnaces to prevent surface decarburization (loss of carbon from the surface) or oxidation.
Quenching
D6 is typically oil quenched. Oil quenching has a slower cooling rate than water quenching, which reduces thermal shock and internal stress, making heat treatment safer. This process causes hard martensite to form inside it.
Tempering
After quenching, the steel is reheated to an intermediate temperature to slightly soften it and relieve internal stresses that would otherwise make the steel unduly brittle. D6 steel typically achieves a hardness of approximately 60 HRC through tempering at a lower temperature, approximately 200°C (390°F). We strongly recommend double tempering or triple tempering. Each tempering process must be cooled to room temperature before the next tempering process can be performed.
This is done to transform retained austenite (a softer phase that can remain after quenching) into more desirable martensite and to temper any “fresh” martensite that forms during cooling from the first temper, thus enhancing overall hardness, toughness, and dimensional stability.
Summary
When properly heat-treated, D6 tool steel exhibits very high abrasive wear resistance, because of its high volume of hard carbides. Its hardness typically falls in the range of 58-60 HRC after standard tempering conditions, with maximum achievable hardness of 64 HRC in the as-quenched state. The wear resistance increases with carbide hardness and homogeneous distribution. Despite its high wear resistance, D6 has relatively lower toughness compared to some other tool steels. In summary, the D6 tool steel heat treatment determines its performance.
Get a Competitive Quote for D6/1.2436 TOOL STEEL
With over 20 years of forging expertise, Aobo Steel is your trusted partner for high-performance D6/1.2436 tool steel. We provide not just materials, but solutions. Leverage our deep industry knowledge and reliable supply chain for your project’s success.
✉ Contact us by filling out the form below.