This is the steel we(Aobo Steel) supply the most, and we have extensive experience in D2 tool steel heat treatment. This guide outlines the key steps for processing D2. Following these procedures carefully will achieve the desired hardness, wear resistance, and toughness. At the bottom of the article, you can download the D2 steel heat treatment guide PDF.
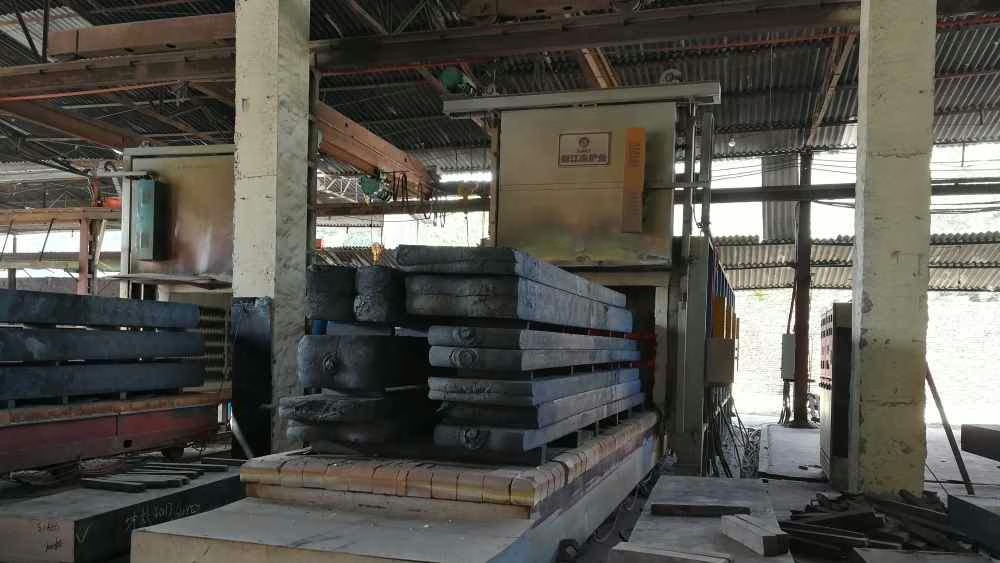
1. Preparation and Preheating
Before starting the heat treatment, proper preparation is important.
1.1 Minimizing Decarburization
To prevent carbon loss from the steel surface during heating (decarburization), we recommend wrapping the material in stainless steel foil. For general heat treating up to 1093 °C (2000°F), Type 321 foil (0.05 mm / 0.002 in. thick) is suitable. If using higher austenitizing temperatures, consider Type 309 foil.
1.2 Preheating
Preheating is a critical step that doesn’t transfer heat quickly. This helps prevent thermal shock and potential cracking.
- Recommended Preheat: Heat the steel to approximately 649 °C (1,200°F).
- Hold Time: Maintain this temperature for 10-15 minutes.
Uniform heating is crucial for preventing stress buildup.
2. Austenitizing
Austenitizing transforms the steel’s structure and dissolves carbides, which is vital for achieving the final properties.
- Temperature: Heat the preheated steel to the austenitizing range, typically 1010 °C (1850°F).
- Soak Time: Maintain the steel at this temperature to ensure the core reaches the target temperature and undergoes the necessary transformation. A common guideline is 1 hour per 25 mm (1 inch) of the thickest section.
- Atmosphere: It’s essential to heat D2 in a controlled atmosphere, such as a vacuum furnace or neutral salt bath, or use the stainless steel wrap method to prevent surface decarburization.
Precise temperature control during this stage is crucial.
3. Quenching
D2 is an air-hardening steel. We don’t need a liquid quench, which simplifies the process and helps minimize distortion.
- Method: Cool the steel in still air after removing it from the furnace.
- Goal: The cooling rate must be fast enough to form the hard martensitic structure but controlled enough to prevent quench cracks.
- Result: The structure after quenching will be predominantly martensite, but it will also contain some retained austenite, which can be as high as 20%. Retained austenite can be an issue for dimensional stability later on.
4. Tempering
After quenching, the material is very hard but also brittle, with internal stress. Tempering relieves this stress and increases toughness.
- Process: Reheat the hardened steel to a specific temperature below its critical point, hold it at this temperature, and then cool it, typically in air.
- Double Tempering: We strongly recommend double tempering. This provides better stress relief, improves toughness, and helps transform some of the retained austenite for better stability.
- Typical Cycle:
- First Temper: Heat to approximately 515 °C (960°F). Hold for 2 hours per 25 mm (1 inch) of thickness. Cool to about 65° C (150° F).
- Second Temper: Reheat to a slightly lower temperature, approximately 480 °C (900°F). Hold for the same duration (2 hours per 25 mm / 1 inch).
- Typical Cycle:
- Hardness vs. Toughness: The tempering temperature determines the final balance.
- Lower temperatures (e.g., 200 °C / 390°F) result in higher hardness (approximately 60 HRC).
- Higher tempering temperatures increase toughness but slightly reduce hardness. Choose the temperature based on your application’s specific needs.
5. Stress Relief (Post-Hardening)
If this material undergoes significant grinding, EDM, or welding after hardening and tempering, we strongly recommend an additional stress relief operation.
- Temperature: Heat the part slowly and uniformly to a temperature approximately 14°C to 28°C (25°F to 50°F) below the final tempering temperature.
- Hold Time: Soak for an adequate amount of time (e.g., 1-2 hours per inch of thickness).
- Cooling: Cool slowly, preferably in the furnace.
6. Managing Potential Issues
Even with careful processing, some issues can arise.
6.1 Distortion
D2 steel has relatively good dimensional stability during heat treatment compared to other tool steels, with an expected change of around 0.0005 in./in. However, factors such as complex part geometry or uneven heating and cooling can still cause warping or twisting. Ensure uniform heating and air cooling to minimize this. Limited straightening may be possible during cooling between approximately 565 °C (1,050°F) and 205 °C (400°F).
6.2 Quench Cracks
Cracking during quenching can happen if cooling is too fast or uneven, or if the steel has internal flaws. Proper preheating and controlled air cooling are the best ways to prevent this.
7. Conclusion
Successfully heat treating D2 tool steel requires careful attention to preparation, temperature, time, and cooling rates throughout each stage: preheating, austenitizing, air quenching, and double tempering. Following established procedures and considering the specific demands of the application will ensure us get the optimal balance of properties. If you have questions about heat treating D2, please don’t hesitate to contact us.
Click on the button below to download the D2 steel heat treatment PDF.
Interested in D2 Tool Steel?
With over 20 years of expertise in forging high-quality tool steel, Aobo Steel is your trusted partner.
Our D2 Tool Steel offers exceptional wear resistance and toughness for your demanding applications.
Get a personalized quote or expert advice today!
Fill out the form below, and our specialists will get back to you promptly.