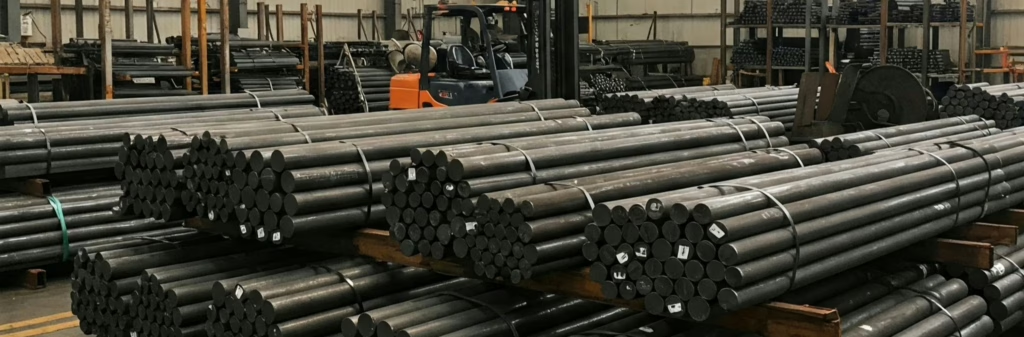
Cr12MoV Tool Steel
AOBO STEEL – Trusted Global Tool Steel Supplier
Cr12MoV tool steel is a high-carbon, high-chromium ledeburite cold work tool steel with high hardness, wear resistance, and minimal quenching deformation. This steel grade is an improved version of Cr12 tool steel, with the addition of molybdenum (Mo) and vanadium (V) elements to enhance its performance characteristics.
1. Composition of Cr12MoV Steel(GB/ T 1299—2000)
C | Si | Mn | Cr | V | Mo | S | P |
---|---|---|---|---|---|---|---|
1.45 ~ 1.70 | ≤0.40 | ≤0.40 | 11.00 ~ 12.50 | 0.15 ~ 0.30 | 0.40 ~ 0.60 | ≤0.030 | ≤0.030 |
2. Properties of Cr12MoV Steel
Critical Point Temperature
Critical Point | Ac₁ | Ac₃ | Ar₁ | Ms |
---|---|---|---|---|
Temperature (approx.) / °C | 810 | 1200 | 760 | 185 |
Linear Expansion Coefficient
Temperature / °C | Linear Expansion Coefficient α / (10⁻⁶ °C⁻¹) |
---|---|
20 ~ 100 | 10.9 |
20 ~ 400 | 11.4 |
20 ~ 600 | 12.2 |
Cr12MoV is a high-carbon, high-chromium, high-hardenability ledeburitic steel. It is characterized by high hardness, good impact toughness, high hardenability, and low distortion upon quenching.
For cross-sectional dimensions up to 400mm, it can be fully through-hardened. Furthermore, it maintains good hardness and wear resistance at elevated temperatures in the range of 300 ~ 400°C.
With minimal volumetric change during quenching and excellent overall mechanical properties, Cr12MoV is considered one of the representative steel grades for high-end cold work tooling materials.
3. Forging Process Specification of Cr12MoV Steel
Item | Heating Temp. / °C | Initial Forging Temp. / °C | Final Forging Temp. / °C | Cooling Method |
---|---|---|---|---|
Ingot | 1100 ~ 1150 | 1050 ~ 1100 | 850 ~ 900 | Slow cooling (pit or sand cooling) |
Billet | 1050 ~ 1100 | 1000 ~ 1050 | 850 ~ 900 | Slow cooling (pit or sand cooling) |
Note: Cr12MoV steel has a low melting point, so the heating temperature should not be too high; it has poor thermal conductivity, so attention should be paid to slow heating. After forging, it must be cooled slowly to avoid cracks. It can be placed in a preheated pit and cooled to 400-500°C. Annealing can be performed after cooling.
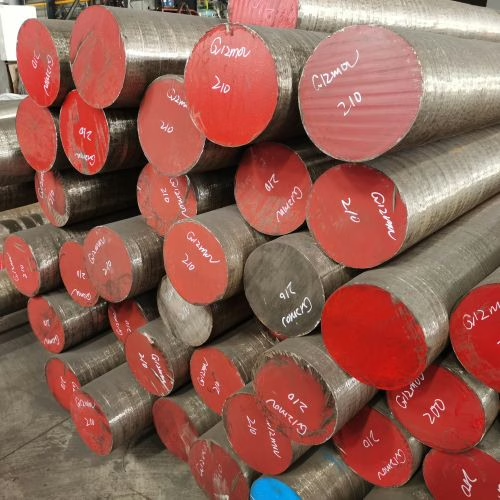
Please fill out the following form to contact us now!
4. Heat Treatment
4.1 Preheating
Process Parameters | |
---|---|
Post-Forging Annealing | Heating temperature 850 ~ 870°C, hold for 1 ~ 2h, furnace cool to below 500°C then air cool. Hardness after annealing is 207 ~ 255HBW, microstructure is fine pearlite + carbide. |
Post-Forging Isothermal Annealing | Heating temperature 850 ~ 870°C, hold for 1 ~ 2h, furnace cool to 720 ~ 750°C, hold for 3 ~ 4h, furnace cool to below 550°C then air cool. Hardness after annealing is 207 ~ 255HBW. Microstructure is fine pearlite + carbide. |
High-Temperature Tempering | Heating temperature 760 ~ 790°C, hold for 2 ~ 3h, furnace cool or air cool. Hardness is 207 ~ 255HBW. |
4.2 Quenching
Quenching Process Specifications for Cr12MoV Steel
Scheme | 1st Preheating Temp./°C | 2nd Preheating Temp./°C | Quenching Temp./°C | Quenching Medium | Quenching Medium Temp./°C | Cooling in Medium | Subsequently | Hardness HRC |
I | 550 ~ 600 | 840 ~ 860 | 950 ~ 1000 | Oil | 20 ~ 60 | To oil temp | Air cooling | 58 ~ 62 |
II | 1020 ~ 1040 | Oil | 20 ~ 60 | To oil temp | Air cooling | 62 ~ 63 | ||
III | 1020 ~ 1040 | Molten nitrate salt | 400 ~ 550 | 5 ~ 10min | Air cooling | 62 ~ 63 | ||
IV | 1115 ~ 1130 | Oil | 20 ~ 60 | To oil temp | Air cooling | 42 ~ 50 | ||
V | 1115 ~ 1130 | Molten nitrate salt | 400 ~ 450 | 5 ~ 10min | Air cooling | 42 ~ 50 |
Note: Schemes IV and V are used for molds that require hot hardness and high wear resistance, such as hot stamping dies working below 450°C, but their mechanical properties are poor, and dimensional deformation is large. After quenching according to schemes I and II, the volume fraction of the microstructure is 12% carbides, 68% to 73% martensite, and 20% to 25% retained austenite.
Hardness and Quenching Temperature Under Different Heating and Cooling Conditions
Heating Conditions | Cooling Method | Quenching Temp./°C | Hardness HRC |
Heating in carburizing agent | Oil cooling | 930 | 64 |
980 | 65 | ||
1010 | 65 | ||
1030 | 63.5 | ||
Heating in air furnace | Oil cooling | 930 | 60.2 |
980 | 63 | ||
1010 | 63.9 | ||
1030 | 63.5 | ||
Heating in air furnace | Air cooling | 930 | 59 |
980 | 62.5 | ||
1010 | 63.2 | ||
1030 | 62 |
4.3 Tempering
Tempering Process Specifications
Scheme | Quenching Temp./°C | Tempering Purpose | Tempering Temp./°C | Medium | Hardness HRC |
I | 1020 ~ 1040 | Stress relief | 150 ~ 170 | Oil or nitrate salt | 61 ~ 63 |
II | Stress relief, reduce hardness | 200 ~ 275 | — | 57 ~ 59 | |
III | 400 ~ 425 | — | 55 ~ 57 | ||
IV | 1115 ~ 1130 | Stress relief and secondary hardening | 510 ~ 520℃ Multiple tempering | — | 60 ~ 61 |
V | -78℃ Cryogenic treatment + 510 ~ 520℃ single tempering | — | 60 ~ 61 | ||
VI | -78℃ Cryogenic treatment plus one 510 ~ 520℃ tempering, then another -78℃ cryogenic treatment | — | 61 ~ 62 |
Note:
- Workpieces tempered according to Scheme I need to maintain high hardness and high wear resistance, and their dimensional changes are almost independent of the quenching state.
- Scheme II is used to obtain workpieces with good toughness.
Tempering Temperature and Hardness
Tempering Temp./°C | Untempered | 100 | 200 | 300 | 400 | 500 | 550 | 600 | 650 |
---|---|---|---|---|---|---|---|---|---|
Hardness HRC | 63 | 62 | 61 | 59 | 57 | 59 | 53 | 47 | 40 |
Note: Oil quenched at 1030°C, tempered for two hours.
5. Applications
Cr12MoV steel is suitable for manufacturing a wide variety of tools and dies that are characterized by large cross-sections, complex shapes, and are subjected to significant impact loads. Examples of such applications include:
- Punching dies with complex geometries
- General stamping dies
- Blanking dies for silicon steel sheets
- Trimming dies
- Edge rolling/curling dies
- Wire drawing dies
- Cold extrusion dies
- Deep drawing dies for steel plate
- Thread rolling plates
- Cold shearing blades
- Circular saws
- Standard tools and gauges
Explore Our Other Products
D2/1.2379/SKD11
D3/1.2080/SKD1
D6/1.2436/SKD2
A2/1.23663/SKD12
O1/1.2510/SKS3
O2/1.2842
S1/1.2550
S7/1.2355
DC53
H13/1.2344/SKD61
H11/1.2343/SKD6
H21/1.2581/SKD7
L6/1.2714/SKT4
M2/1.3343/SKH51
M35/1.3243/SKH55
M42/1.3247/SKH59
P20/1.2311
P20+Ni/1.2738
420/1.2083/2Cr13
422 stainless steel
52100 bearing steel
440C stainless steel
4140/42CrMo4/SCM440
4340/34CrNiMo6/1.6582
4130
5140/42Cr4/SCR440
SCM415