فولاذ أداة O2 heat treatment is crucial to achieving optimal performance. O2 tool steel is an oil-quenched cold work tool steel with high hardness, high wear resistance, and minimal deformation during heat treatment. Compared to water-quenched steel, O2 steel exhibits better dimensional stability and higher toughness after complete quenching1. The equivalent grades of O2 tool steel include:
- أوروبا (EN/DIN): 1.2842 أو 90MnCrV8.
- اليابان (JIS): SKS31
- الصين (GB): 9Mn2V
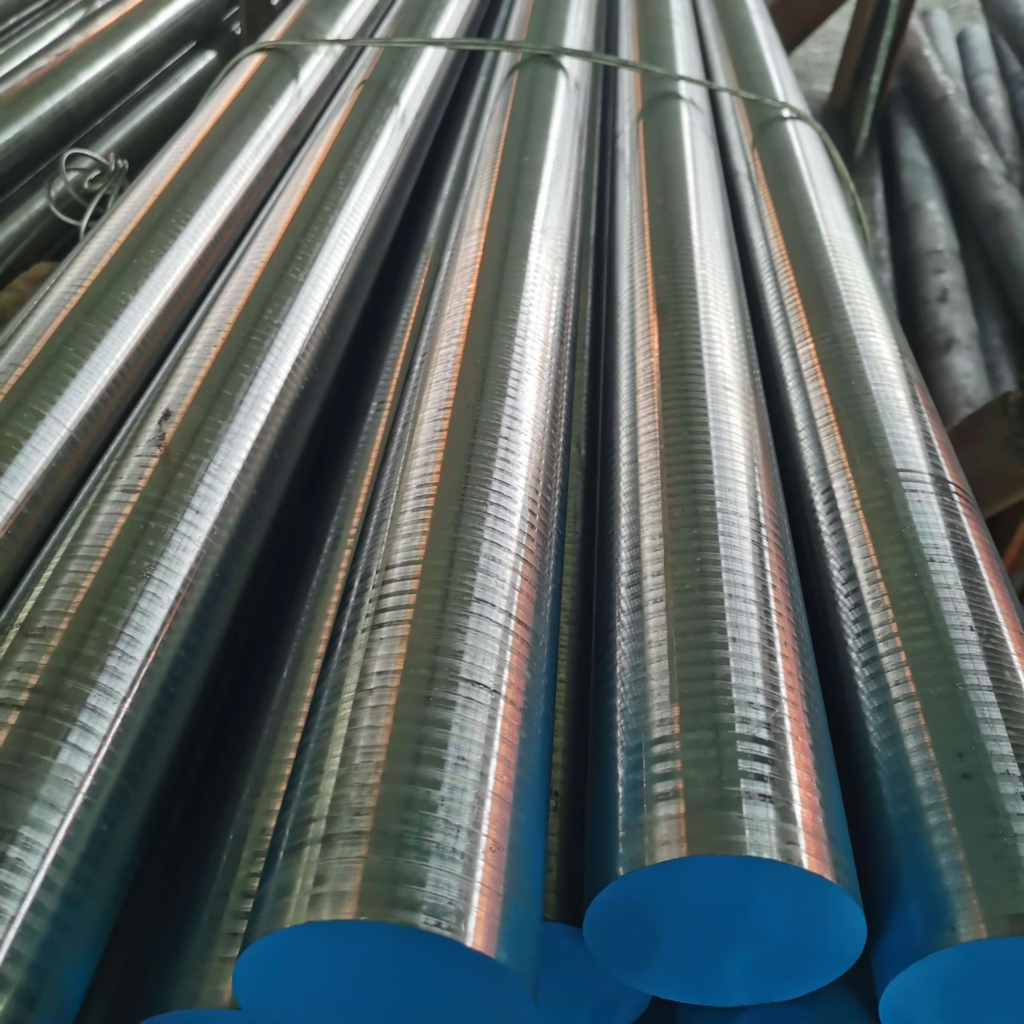
O2 tool steel heat treatment typically involves preheating, austenitizing, إخماد، و التلطيف.
التسخين المسبق
Almost all tool steels, including O2, must undergo preheating treatment. It helps reduce thermal shock and lowers the risk of deformation or cracking when cold tools are placed in a hot furnace. It can also relieve stress generated during the processing of O2 materials and improve the production efficiency of furnaces. Preheat to 649-677°C (1200-1250°F) until the O2 material is evenly heated.
التصلب (الأوستنيتي)
The austenitizing temperature range for O2 steel is typically 760 to 800°C (1400 to 1472°F). At this temperature, various complex alloy carbides are dissolved, and the microstructure is transformed into الأوستينيت. The soaking time at this temperature should be carefully controlled to avoid adverse effects on the molecular structure.
إخماد
After austenitizing, the steel is rapidly cooled, typically in oil for O2 tool steel, to transform the austenite into martensite, which is the desired hard structure. Oil quenching has a slower cooling rate than water quenching, but it has a lower risk of deformation and cracking. The O2 material should be cooled to a temperature between 66 and 93 °C (150 and 200 °F) before proceeding to the tempering step. Unlike air-hardening steel, oil-quenched tool steel is not typically wrapped in stainless steel foil during the quenching process, as the foil would impede the oil quenching process.
التقسية
O2 tool steel is typically tempered at low temperatures, usually between 150 °C and 260°C (300°F to 500°F), to maintain its high hardness. O2 tool steel commonly requires a single tempering cycle, but double tempering can sometimes be preferred. Each tempering cycle typically requires a soak time of at least 2 hours per inch (4.7 minutes per millimeter) of cross-section, with air cooling to room temperature between multiple tempers. The timing of tempering is critical and must begin immediately when the temperature from the previous quenching step has dropped to 52-65°C (125-150°F) to prevent adverse effects on tool life and to avoid stabilization of retained austenite. The higher the tempering temperature, the lower the hardness.
The above is a summary of our 20 years of industry experience in O2 heat treatment, with some information sourced from relevant literature. We hope it is helpful to you. If you are interested in O2 steel, please do not hesitate to contact us.
- Nee, J. G. (Chief Technical Reviewer & Managing Editor). (2010). Fundamentals of Tool Design (6th ed.). Society of Manufacturing Engineers. ↩︎
Get a Competitive Quote for O2 Tool Steel
With over 20 years of forging expertise, Aobo Steel is your trusted partner for high-performance O2 tool steel. We provide not just materials, but solutions. Leverage our deep industry knowledge and reliable supply chain for your project’s success.
✉ تواصل معنا عن طريق ملء النموذج أدناه.