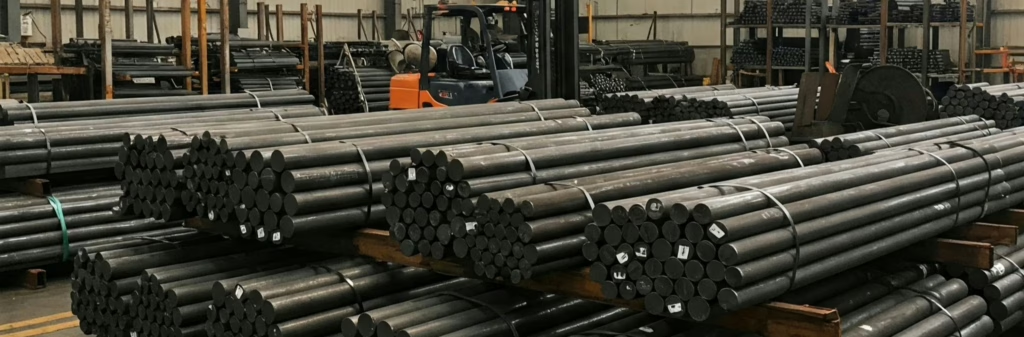
فولاذ الأدوات D6 | 1.2436 | SKD2
AOBO STEEL – مورد عالمي موثوق لأدوات الفولاذ
يتم تصنيف الفولاذ D6 ضمن نظام AISI كنسبة عالية من الكربون والكروم فولاذ الأدوات للعمل الباردتتميز الفولاذات في هذه الفئة عادةً بمحتوى اسمي من الكروم يبلغ حوالي 12%، وهو أمر أساسي لخصائص أدائها. تُضبط هذه الخصائص المحددة بدقة من خلال تباين عناصر السبائك، مثل الكربون والموليبدينوم والفاناديوم والمنغنيز.
1. التطبيقات
- قوالب تقطيع الإنتاج الطويلة
- لكمات التشكيل البارد ويموت
- مكونات الأدوات المعرضة للتآكل الشديد
- التطبيقات التي يكون فيها الحفاظ على الحافة الحادة أثناء الاستخدام المطول أمرًا بالغ الأهمية
2. تركيبة الفولاذ D6
الكربون (C) | الكروم (Cr) | التنجستن (W) | المنجنيز (Mn) | السيليكون (Si) |
2.00 – 2.20 | 11.50 – 12.50 | 0.60 – 0.90 | 0.20 – 0.40 | 0.10 – 0.40 |
تكوين درجات مكافئة لفولاذ الأداة D6
الكربون (C) | السيليكون (Si) | المنجنيز (Mn) | الكروم (Cr) | التنجستن (W) | الفوسفور (P) | الكبريت (S) | |
ألمانيا/W-Nr. 1.2436 (X210CrW12) | 2.00 – 2.30 | 0.10 – 0.40 | 0.30 – 0.60 | 11.0 – 13.0 | 0.60 – 0.80 | ≤ 0.030 | ≤ 0.030 |
اليابان/JIS SKD2 | 2.00 – 2.30 | 0.10 – 0.60 | 0.30 – 0.60 | 11.0 – 13.0 | 0.60 – 0.80 | ≤ 0.030 | ≤ 0.030 |
الصين/جي بي Cr12W | 2.00 – 2.30 | ≤ 0.40 | ≤ 0.40 | 11.0 – 13.0 | 0.60 – 0.90 | ≤ 0.030 | ≤ 0.030 |
3. خصائص الفولاذ D6
3.1 الخصائص الفيزيائية
الكثافة | معامل التمدد الحراري | التوصيل الحراري | السعة الحرارية النوعية |
7.67 جم/سم³ | 10.8 ميكرومتر/متر درجة مئوية (21-400 درجة مئوية) | 20.5 واط/متر كلفن (20 درجة مئوية) | 0.460 جول/جم-°م (20°م) |
3.2 الصلابة ومقاومة التآكل
الميزة الأساسية لـ D6 Tool Steel هي مقاومة عالية جدًا للتآكلينبع هذا مباشرةً من محتواه العالي من الكربون والكروم، مما يُعزز تكوين كربيدات صلبة غنية بالكروم في البنية الدقيقة للفولاذ بعد المعالجة الحرارية. عند تقسيته وتلطيفه بشكل صحيح، يحقق D6 عادةً صلابة تتراوح بين 54 و 61 حقوق الإنسان. مقاومتها للتآكل تتجاوز بشكل عام مقاومة الأنواع الأكثر شيوعًا أداة فولاذية D2ل، مما يجعلها مناسبة للتطبيقات التي تتطلب عمر خدمة طويل في ظل الظروف الكاشطة.
3.3 المتانة
تتمتع D6 بمقاومة عالية للتآكل، ولكن صلابة أقلبالمقارنة مع أنواع الفولاذ المقاوم للصدمات (مثل سلسلة S) أو أنواع الفولاذ الأخرى المُستخدمة في العمل البارد ذات المحتوى الكربوني المنخفض (مثل سلسلة A أو D2)، يُعد فولاذ الأدوات D6 أكثر هشاشة. الكربيدات الصلبة نفسها المقاومة للتآكل قد تجعل الفولاذ أكثر عرضة للتشقق أو التشقق تحت تأثير الصدمات. لذلك، لا يُنصح باستخدام فولاذ الأدوات D6 في التطبيقات التي تنطوي على صدمات أو أحمال صدمات كبيرة.
3.4 قابلية التصلب والمعالجة الحرارية
D6 هو الفولاذ شديد التصلب؛ يمكنه تحقيق صلابة موحدة نسبيًا من خلال مقطعه العرضي، حتى في الأحجام الأكبر. وهو عادةً تصلب الزيت درجة، مع إمكانية تقسيته بالهواء مع تضحية ببعض الصلابة الممكنة. يُعدّ التطبيع بعد التصلب ضروريًا لتخفيف الضغوط وتحقيق التوازن المطلوب بين الصلابة والمتانة.
3.5 استقرار الأبعاد
نظرًا لكونه فولاذًا مُصلدًا بالزيت، قد يُظهر D6 تغيراتٍ أبعاديةً أكبر أثناء المعالجة الحرارية مقارنةً بدرجات التصلب الهوائي مثل فولاذ الأدوات D2. يُعدّ التحكم الدقيق في عملية المعالجة الحرارية أمرًا ضروريًا إذا كانت حدود الأبعاد الدقيقة ضرورية.
3.6 قابلية التشغيل والطحن
نظرًا لصلابته العالية ومحتوى الكربيد الكبير، يعتبر الفولاذ D6 أصعب في التصنيع والطحن مقارنةً بالفولاذ منخفض السبائك أو حتى الفولاذ D2. ينبغي أخذ ذلك في الاعتبار عند إجراء عمليات التصنيع وتكاليفها.
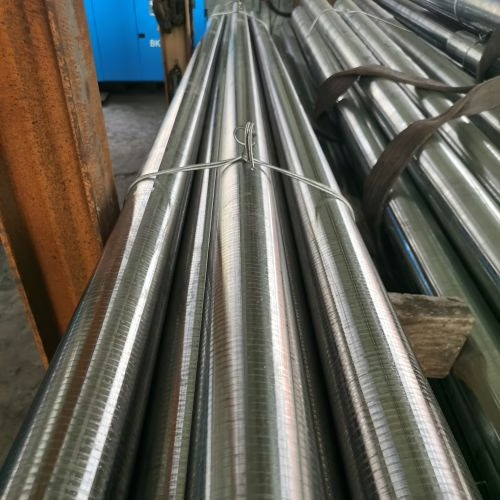
هل أنت مهتم بـ D6 | 1.2436 أداة الفولاذ؟ يرجى ملء النموذج التالي للتواصل معنا الآن!
4. المعالجة الحرارية لفولاذ الأدوات D6
4.1 التسخين المسبق
يُقلل التسخين المسبق من الصدمة الحرارية، مما يُقلل من خطر التشقق أو التشوه اللاحق. يُجرى التسخين المسبق عادةً عند درجات حرارة تتراوح بين 650 درجة مئوية و760 درجة مئوية (1200 درجة فهرنهايت و1400 درجة فهرنهايت)تأكد من وصول الأداة بأكملها إلى درجة حرارة التسخين المسبق بالتساوي قبل حساب وقت النقع. بناءً على خبرتنا، يتراوح وقت النقع بين 10 و15 دقيقة.
4.2 الأوستنيت (التصلب)
الغرض من هذه الخطوة هو تحويل البنية الدقيقة للصلب إلى الأوستينيت، تحضيره للتبريد اللاحق. يتراوح نطاق درجة الحرارة بين 950 درجة مئوية و1050 درجة مئوية (1740 درجة فهرنهايت و1920 درجة فهرنهايت)مدة التثبيت ساعة واحدة لكل ٢٥ مم (بوصة واحدة) من السُمك. من المهم ملاحظة أن مدة التثبيت غير الكافية قد تؤدي إلى إخماد غير كامل، بينما قد تؤدي مدة التثبيت الزائدة إلى نمو الحبيبات وانخفاض صلابتها.
4.3 التبريد
تتضمن هذه الخطوة تحويل الأوستينيت إلى مارتنسيت صلب. فولاذ الأدوات D6 هو فولاذ مُصلد بالزيت. يوفر التبريد بالزيت معدل تبريد سريعًا بما يكفي للتصلب، مع كونه أقل قسوة من الماء، مما يقلل بشكل كبير من خطر التشقق والتشوه.
تتضمن العملية المحددة تبريد قطعة العمل في الزيت حتى تبرد درجة حرارة الغرفة أو 65 درجة مئوية (150 درجة فهرنهايت).
أحيانا، إخماد الهواء يُختار أيضًا، لكن صلابته بعد التبريد الهوائي أقل نسبيًا. إذا حُددت متطلبات تشوه أعلى، يُمكن النظر في تبريد فولاذ D6 بالهواء.
4.4 التلطيف
الغرض من عملية التلدين هو تقليل الهشاشة وزيادة المتانة. يُنصح بإجراء عملية تلدين على مرحلتين لضمان أقصى قدر من تخفيف الضغط وثبات الأبعاد.
تتراوح درجة حرارة التلطيف من 150 درجة مئوية إلى 550 درجة مئوية (300 درجة فهرنهايت إلى 1020 درجة فهرنهايت)تبلغ مدة النقع ساعتين لكل 25 مم (1 بوصة) من السمك لكل دورة نقع.
تُحدد درجة حرارة التلطيف الصلابة النهائية للمادة. تُقلل درجات الحرارة المرتفعة من صلابة فولاذ D6، لكنها تزيد من صلابته. يجب تحديد درجة الحرارة النوعية بناءً على متطلبات التطبيق الفعلية.
4.5 تحقيق نتائج أفضل وتجنب المشاكل
يعد التحكم السليم في العملية أمرًا بالغ الأهمية لتحقيق المعالجة الحرارية الناجحة.
4.5.1 الاستقرار البعدي
لتقليل خطر تشوه الفولاذ D6 أثناء الإطفاء، يجب اتخاذ الاحتياطات التالية.
- يمكن إجراء دورتين للتسخين المسبق.
- ضمان التسخين الموحد أثناء عملية الأوستنيت.
- قم بالتحريك أثناء تبريد الزيت.
- قم بإجراء معالجة تخفيف الضغط بعد التشغيل الخشن وقبل المعالجة الحرارية النهائية.
4.5.2 تخفيف التوتر (بعد التصلب)
يجب إجراء معالجة تخفيف الإجهاد بعد عمليات الطحن أو اللحام أو التشغيل بالتفريغ الكهربائي الثقيلة. يجب أن تكون درجة حرارة تخفيف الإجهاد من 15 درجة مئوية إلى 30 درجة مئوية (من 25 درجة فهرنهايت إلى 50 درجة فهرنهايت) أقل من درجة حرارة التصلب النهائية. مدة التماسك تتراوح بين ساعة وساعتين لكل ٢٥ مم (بوصة واحدة) من السُمك.
4.5.3 مشاكل المعالجة الحرارية الشائعة
- التشقق: غالبًا ما يكون السبب هو الصدمة الحرارية (التسخين المسبق غير الكافي أو التبريد القاسي المفرط).
- تشويه: يحدث بسبب التسخين/التبريد غير المنتظم أو الضغوط الداخلية.
- صلابة غير كافية: النتائج الناجمة عن درجة حرارة/وقت الأوستنيت غير الصحيحة أو الإطفاء غير الكافي.
4.6 تشكيل فولاذ الأدوات D6
قم بالتسخين ببطء إلى 900 درجة مئوية (1650 درجة فهرنهايت)يجب أن يبدأ التشكيل ضمن نطاق درجة الحرارة 980 درجة مئوية (1800 درجة فهرنهايت) إلى 1095 درجة مئوية (2000 درجة فهرنهايت). يفعل لا حدادة أقل من 900 درجة مئوية (1650 درجة فهرنهايت)بالنسبة للمقاطع العرضية الأكبر، أو القطع الأثقل، أو التخفيف السريع، استخدم الحد الأعلى لنطاق درجة الحرارة؛ أما بالنسبة للمقاطع العرضية الأصغر أو التخفيف الأخف، فاستخدم الحد الأدنى لنطاق درجة الحرارة.
5. مقارنة مع أنواع الفولاذ الأخرى
5.1 D6 مقابل D2
فولاذ الأدوات D2 فولاذ الأدوات D6 وD6 هما فولاذ أدوات عالي الكربون والكروم، يُستخدم على البارد، ويُعرف بمقاومته للتآكل. يتميز D6 بمقاومة تآكل أعلى قليلاً، على حساب انخفاض صلابته وتعقيد/صعوبة معالجته حرارياً (إخماد الزيت، وزيادة خطر التشوه). يُستخدم D2 على نطاق أوسع بفضل توازن خصائصه الأفضل، وخاصةً قدرته على التصلب بالهواء وانخفاض تشوهه.
5.2 D6 مقابل. د3
- كلاهما عبارة عن فولاذ عالي الكربون والكروم ومقاوم للزيت ويشتهر بمقاومته العالية للتآكل بشكل استثنائي.
- قد توجد اختلافات تركيبية بسيطة (أحيانًا W أو V في فولاذ الأداة D6).
- تعتبر المعالجة الحرارية لـ D3 أكثر تعقيدًا من D6.
5.3 D6 مقابل D7
- يحتوي D7 على مادة الفاناديوم المضافة، مما يوفر مقاومة أعلى للتآكل من الفولاذ D6 Tool Steel.
- عادةً ما يكون لدى D7 صلابة أقل من D6 ويتطلب درجات حرارة تصلب أعلى.
6. اعتبارات عند اختيار فولاذ الأدوات D6
يُعد فولاذ D6 خيارًا ممتازًا لتطبيقات محددة تتطلب أقصى مقاومة للتآكل في أدوات العمل الباردة. مع ذلك، يُرجى مراعاة ما يلي بعناية:
- صلابة أقل: غير مناسب للتطبيقات ذات التأثير العالي.
- يعالج: أكثر تحديًا للتصنيع والطحن.
- المعالجة الحرارية: تتطلب عملية إخماد الزيت التحكم الدقيق في العملية لتحقيق الاستقرار الأبعادي.
- التوفر: قد يكون أقل توفرًا من الفولاذ D2 Tool.
7. الدرجات المكافئة
- دين إن (أوروبا): 1.2436 (X210CrW12)
- JIS (اليابان): SKD2
- بكالوريوس العلوم (المملكة المتحدة): BD6
- ايزو: X210CrW12
- GB(الصين): Cr12W
8. أشكال وأبعاد التوريد
يتوفر فولاذ الأدوات D6 الذي نوفره بأشكال متنوعة، بما في ذلك القضبان المستديرة، والصفائح، والألواح، والقضبان المسطحة، والقضبان المربعة، والكتل. تتراوح أبعاد القضيب المسطح بين: العرض 20-600 مم × السُمك 20-400 مم × الطول 1000-5500 مم. تتراوح أبعاد القضيب المستدير بين القطر 20-400 مم × الطول 1000-5500 مم. يتم الحصول على أبعاد الكتلة بقطع القضيب المسطح.
للأحجام الصغيرة، مثل القضبان المستديرة التي يقل قطرها عن 70 مم، نستخدم عملية الدرفلة الساخنة. أما الأحجام التي تزيد عن 70 مم، فنقدم منتجات مزورة.
اختبار UT: سبتمبر 1921-84 D/d، E/e.
معالجة السطح: سطح أسود أصلي، مقشر، ميكانيكي/مخروطي، مصقول، مؤرض، أو مطحون.
حالة المخزون: لا نحتفظ بمخزون من فولاذ D6. نرتب الإنتاج بناءً على طلبات العملاء.
مدة التسليم: مواد فرن القوس الكهربائي (EAF) تتراوح بين 30 و45 يومًا. ومواد فرن القوس الكهربائي (ESR) حوالي 60 يومًا.
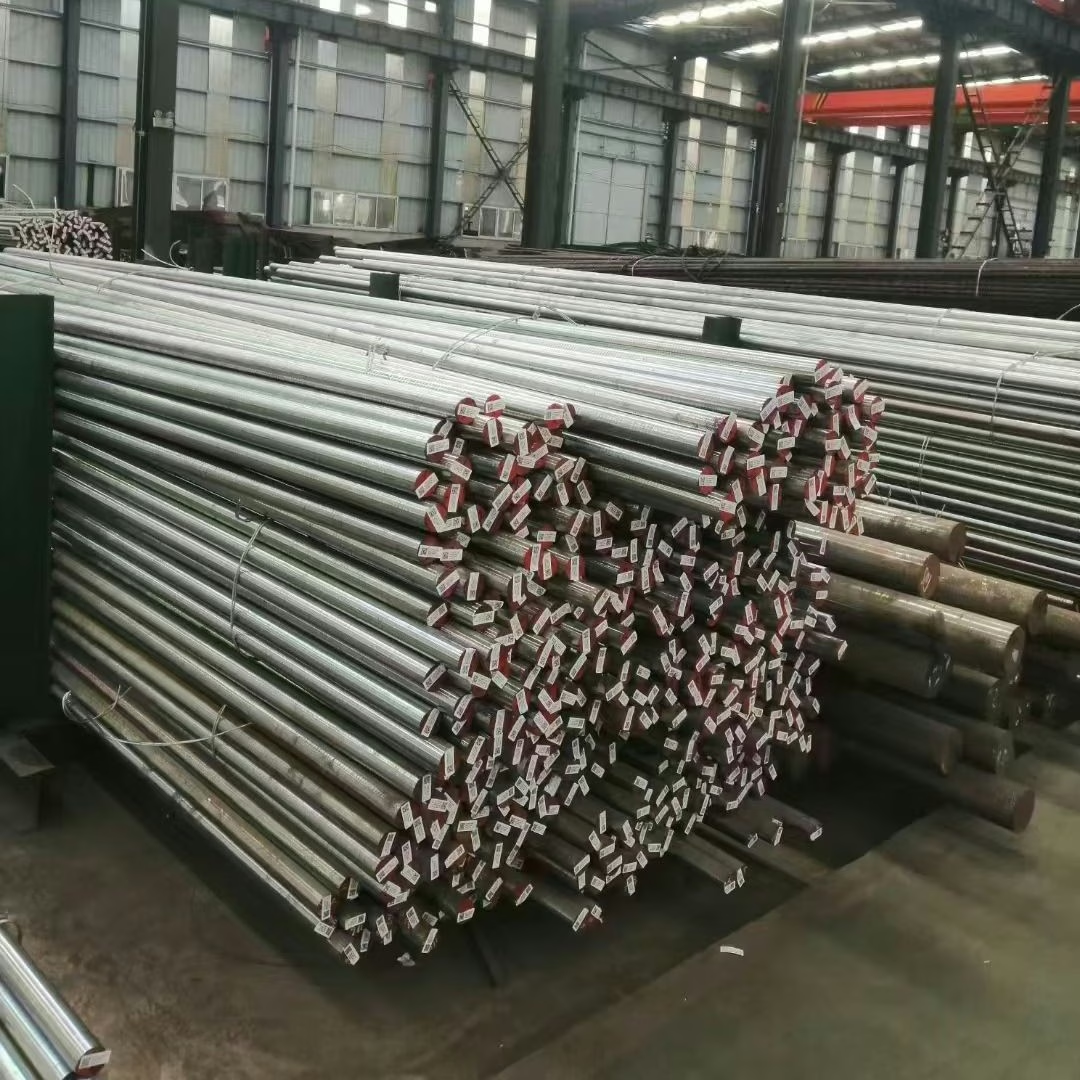
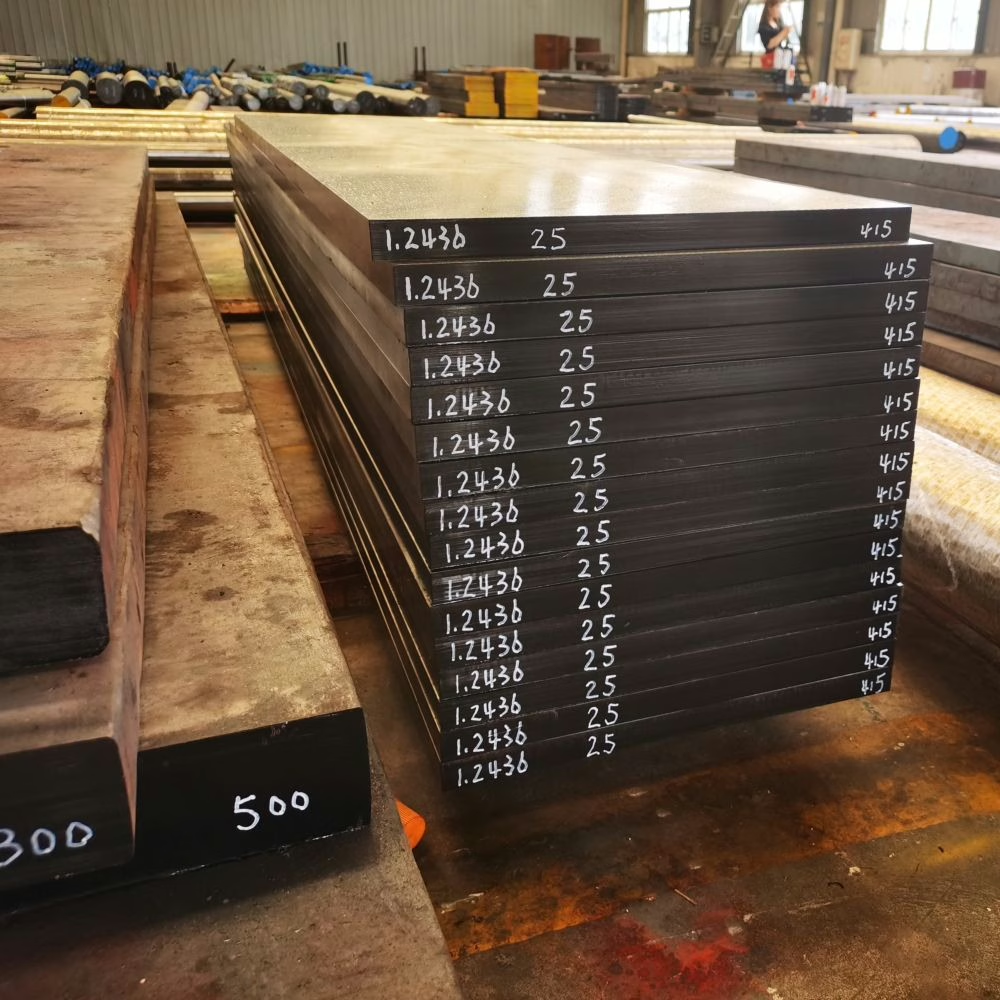
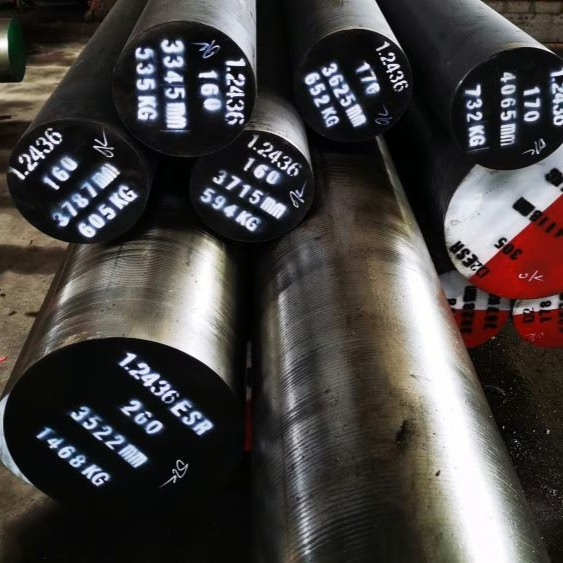
التعليمات
فولاذ الأدوات D6 هو فولاذ أدوات عالي الكربون والكروم، ممزوج بالتنغستن، ويُستخدم بشكل رئيسي في تطبيقات العمل البارد. يتميز بقوة ضغط عالية، ومقاومة عالية للتآكل، وصلابة سطحية عالية، وثبات جيد في التصلب. يُعرف أيضًا باسم فولاذ SKD2 وفولاذ DIN 1.2436.
يتميز فولاذ الأدوات D6 بمقاومة ممتازة للتآكل والتآكل، وقوة ضغط عالية، وصلابة سطحية عالية، وثبات جيد للأبعاد والتصلب. يضمن هيكله الكربيدي المتين أداءً ممتدًا وصيانة أقل حتى في ظل الضغوط الشديدة.
فولاذ الأدوات AISI D6 يُعادل JIS SKD2 في اليابان وDIN 1.2436 (المعروف أيضًا باسم X210CrW12) في ألمانيا/المملكة المتحدة/فرنسا. ويُعرف أيضًا باسم UNS T30406.
تبلغ كثافة فولاذ الأدوات D6 7.67 غ/سم³ (0.277 رطل/بوصة³). معامل التمدد الحراري له 10.8 ميكرومتر/م³ (6 ميكرومتر/بوصة² فهرنهايت) عند درجة حرارة تتراوح بين 21 و400 درجة مئوية، وموصليته الحرارية 20.5 واط/متر كلفن (142 وحدة حرارية بريطانية/بوصة² فهرنهايت) عند درجة حرارة 20 درجة مئوية. كما تبلغ سعته الحرارية النوعية 0.460 جول/غ-درجة مئوية (0.110 وحدة حرارية بريطانية/بوصة² فهرنهايت) عند درجة حرارة 20 درجة مئوية.
يتميز فولاذ الأدوات D6 بقوة ضغط تبلغ 1320 ميجا باسكال (191000 رطل/بوصة مربعة) ومعامل مرونة يبلغ 194 جيجا باسكال (28100 كيلو باسكال). تبلغ صلادته وفقًا لمقياس روكويل سي 46 HRC في ظروف معينة، ويمكن أن تصل إلى 55-62 HRC بعد المعالجة الحرارية.
يُستخدم فولاذ الأدوات D6 على نطاق واسع في تشكيل الأدوات، وقوالب البلاستيك والسيراميك الكاشطة، وأدوات الكبس طويلة المدى. كما أنه مناسب لقوالب التقطيع، وأدوات قص المواد الصلبة، وأدوات الختم، وأدوات الكشط، وأدوات النجارة، وأدوات الرسم، وسكاكين الآلات. وتشمل استخداماته المحددة قوالب التقطيع لقطع صفائح يصل سمكها إلى 2 مم، وشفرات الورق والبلاستيك، وقوالب البثق للمعادن والبلاستيك والمطاط.
نعم، يُستخدم فولاذ الأدوات D6 في الشفرات الثابتة الخارجية. وقد أشار أحد صانعي السكاكين إلى أن D6، كونه فولاذ أدوات عالي الجودة مُخلوط بالتنغستن، يُحافظ على ثبات الحواف بشكل ممتاز بفضل كربيدات التنغستن. وبينما يُمكن معالجته حراريًا حتى 62 HRC، فإن تلطيفه حتى 58 HRC يجعله أكثر صلابةً وأداةً يوميةً أفضل للسكاكين.
نعم، يتم استخدام فولاذ الأدوات D6 في قوالب البلاستيك الكاشطة وكذلك على وجه التحديد في قوالب الحقن التي تتطلب دقة عالية ومقاومة للتآكل.
نعم، يُستخدم فولاذ الأدوات D6 بشكل شائع في قوالب القطع، وأدوات قص المواد الصلبة، وأدوات القطع والقص بشكل عام. وهو مناسب لقطع صفائح يصل سمكها إلى 2 مم، ولشفرات القص البارد للورق والبلاستيك والكرتون والمعادن.
يُسخّن فولاذ الأدوات D6 ببطء وبشكل متساوٍ إلى 700 درجة مئوية (1292 درجة فهرنهايت)، ثم بسرعة أكبر إلى 900-1050 درجة مئوية (1652-1922 درجة فهرنهايت) للتشكيل. بعد التشكيل، يُبرّد ببطء إلى درجة حرارة الغرفة في فرن.
يُلَدَّن فولاذ الأدوات D6 عند درجة حرارة تتراوح بين 800 و840 درجة مئوية (1472-1544 درجة فهرنهايت)، ثم يُبرَّد ببطء في الفرن. أو يُمكن تسخينه عند درجة حرارة تتراوح بين 50 و100 درجة مئوية (122-212 درجة فهرنهايت) في الساعة حتى يصل إلى 830-870 درجة مئوية (1526-1598 درجة فهرنهايت)، ثم يُنقع لمدة ساعة لكل 25.4 مم (بوصة واحدة)، ثم يُبرَّد ببطء في فرن أو في بيئة مُتحكم بها. تبلغ صلابته بعد التلدين حوالي 225 برينل.
يمكن التخلص من إجهادات فولاذ الأدوات D6 قبل التصلب بتسخينه إلى 650-700 درجة مئوية (1202-1292 درجة فهرنهايت)، خاصةً إذا كانت عمليات التشغيل شاقة. ثم يُترك الفولاذ ليبرد ببطء.
يُسخّن فولاذ D6 مسبقًا ببطء إلى 750-800 درجة مئوية (1382-1472 درجة فهرنهايت) ويُنقع جيدًا. يستمر التسخين حتى تصل درجة حرارة التصلب النهائية إلى 950-980 درجة مئوية (1742-1796 درجة فهرنهايت)، أو 940-1000 درجة مئوية. ثم يُتبع ذلك التبريد بالهواء أو الزيت، أو التبريد في حمام دافئ أو حمام ملح. كما يُعدّ التصلب بالتفريغ (غاز عالي السرعة) طريقة مثالية.
يُسخّن فولاذ الأدوات D6 بالتساوي وبشكل كامل عند درجة حرارة التطبيع المُختارة. كما يُمكن إجراء التطبيع المزدوج بالتبريد المتوسط إلى درجة حرارة الغرفة. تتراوح درجات حرارة التطبيع عادةً بين 500 و600 درجة مئوية (932-1112 درجة فهرنهايت)، أو درجات حرارة مُحددة مثل 100 درجة مئوية (مما يُنتج 63 HRC) وحتى 600 درجة مئوية (مما يُنتج 48 HRC). تتراوح الصلابة النهائية لفولاذ الأدوات D6 بعد المعالجة الحرارية بين 55 و62 HRC.
في الخراطة الصلبة لفولاذ AISI D6، تؤثر معلمات التشغيل، مثل السرعة والتغذية وعمق القطع، على استجابات المخرجات، مثل خشونة السطح وقوة القطع وطول وعرض تآكل الفوهة وتآكل الجانب. يُعدّ التآكل والالتصاق آليات التآكل السائدة، حيث يزداد تآكل الأداة مع السرعة، وتزداد قوة القطع بسرعة عند السرعات العالية (70-90 مترًا/دقيقة). كما تؤدي قيم التغذية وعمق القطع الأعلى إلى مزيد من تلف السطح وزيادة قوة القطع. يمكن استخدام نماذج التعلم الآلي لاختبار معلمات التشغيل هذه وتقييمها وتحسينها للتنبؤ بخصائص مثل خشونة السطح.
يتمتع فولاذ الأداة D6 بخصائص تصلب أفضل واستقرار أبعادي مقارنة بالفولاذ D3.
احصل على عرض أسعار تنافسي لفولاذ الأدوات D6
بخبرة تزيد عن 20 عامًا في مجال التشكيل، تُعدّ Aobo Steel شريكك الموثوق في فولاذ الأدوات D6 عالي الأداء. لا نوفر المواد فحسب، بل نوفر أيضًا الحلول. استفد من معرفتنا العميقة بالصناعة وسلسلة التوريد الموثوقة لنجاح مشروعك.
✉ تواصل معنا عن طريق ملء النموذج أدناه.
استكشف منتجاتنا الأخرى
D2/1.2379/1.2379/SKD11
D3/1.2080/1.2080/SKD1
D6/1.2436/SKD2
A2/1.23663/1/SKD12
O1/1.2510/1.2510/SKS3
O2/1.2842
S1/1.2550
S7/1.2355
DC53
H13/1.2344/1.2344/SKD61
H11/1.2343/1.2343/SKD6
H21/1.2581/SKD7
L6/1.2714/SKT4
م2/1.3343/1.3343/سخ 51
M35/1.3243/1.3243/SK55
M42/1.3247/1.3247/SK59
P20/1.2311
P20+Ni/1.2738
420/1.2083/2Cr13
422 الفولاذ المقاوم للصدأ
محمل فولاذي 52100
الفولاذ المقاوم للصدأ 440C
4140/42CrMo4/SCM440
4340/34CrNiMo6/1.6582
4130
5140/42Cr4/SCR440
SCM415