AISI A2 tool steel is an air-hardening, medium-alloy cold-work steel widely recognized for its balanced wear resistance and toughness. This guide provides a technical breakdown of its typical elemental makeup.
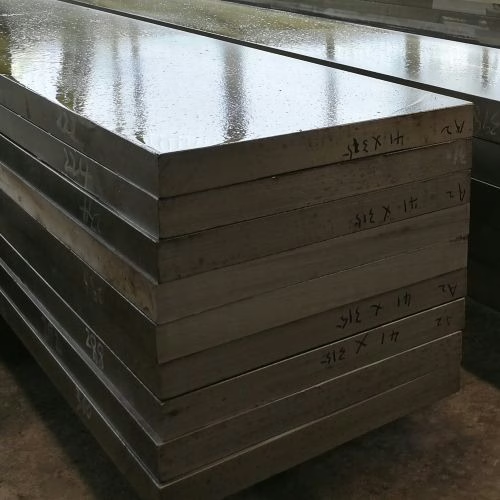
What is A2 Tool Steel
A2 tool steel is specifically classified for cold-work applications. Its defining characteristic is the combination of good wear resistance and toughness, achieved through its specific alloying and air-hardening capability.
Key Alloying Elements in A2 Steel Composition1
The typical chemical A2 steel composition, by weight percentage, based on industry specifications, is as follows:
Element | Symbol | Typical Range (%) | Primary Contributions |
Carbon | C | 0.95 – 1.05 | Critical for hardness and carbide formation for wear resistance |
Manganese | Mn | Up to 1.00 | Contributes to hardenability |
Silicon | Si | Up to 0.50 | Primarily a deoxidizer |
Chromium | Cr | 4.75 – 5.50 | Essential for air-hardening and wear resistance |
Molybdenum | Mo | 0.90 – 2.20 | Enhances hardenability and wear resistance |
Vanadium | V | Up to 0.50 | Contributes to wear resistance by forming hard carbides |
Nominal values often observed include: Carbon ~1.00%, Manganese ~0.60-0.62%, Silicon ~0.17-0.25%, Chromium ~5.00-5.31%, Molybdenum ~1.00-1.20%, and Vanadium ~0.20-0.32%.
Elements such as Phosphorus (P) and Sulfur (S), while always present in steel, are maintained at low maximum levels in the A2 steel composition. This is crucial as they can have detrimental effects on toughness and hot working characteristics. Standard specifications for similar steels often limit Phosphorus to below 0.04% and Sulfur to below 0.05%.
The specific elemental balance in the A2 steel composition dictates its characteristic performance attributes.
Wear Resistance and Toughness
A2 tool steel offers a good combination of wear resistance and toughness.
- Compared to S-series (shock-resistant) steels, A2 provides greater abrasion resistance.
- Compared to D-series (high-carbon, high-chromium) steels like D2, A2 exhibits better toughness and ductility, although D2 has very high wear resistance. D2 has poorer machinability and toughness relative to A2.
Dimensional Stability in Heat Treatment
A2 tool steel has good dimensional stability during air quenching in heat treatment. It expands approximately 0.001 in./in. (0.001 mm/mm). This minimal distortion is a key reason A2 is preferred for applications where maintaining tight tolerances after heat treatment is critical. For more information, please click A2 steel heat treatment guide.
Summary
The typical A2 steel composition is engineered to deliver a reliable balance of wear resistance, toughness, and dimensional stability through air hardening, making it a staple for many cold-work tooling applications.
- Bringas, J. E. (Ed.). (2004). Handbook of Comparative World Steel Standards (3rd ed., p. 433). ASTM International. ↩︎
Expert Guidance on A2 Tool Steel – Get Your Custom Quote
With over 20 years of forging expertise, Aobo Steel is your trusted partner for high-quality A2 tool steel. Our specialists are ready to discuss your specific requirements and provide a tailored solution. Discover the Aobo Steel difference and let our experience work for you.
Ready to proceed? Fill out the form below, and one of our A2 steel experts will contact you shortly.