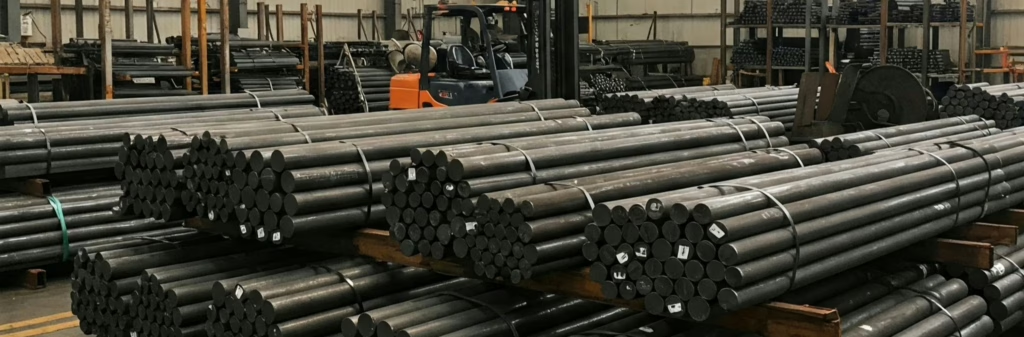
9Cr18Mo Stainless Steel |102Cr17Mo
AOBO STEEL – Trusted Global Tool Steel Supplier
9Cr18Mo and 102Cr17Mo are the same type of steel. 9Cr18Mo is the old designation used in the Chinese national standard GB/T 1220-1992. 102Cr17Mo is the new designation adopted in the revised Chinese national standards GB/T 1220-2007 and GB/T 20878-2007.
9Cr18Mo(102Cr17Mo) is a high-carbon, high-chromium martensitic stainless steel, developed from the 95Cr18 (9Cr18) grade through the addition of molybdenum (Mo). Consequently, it exhibits superior hardness, wear resistance, high-temperature strength, tempering resistance, and corrosion resistance compared to 95Cr18 (9Cr18) steel. This steel also possesses good high-temperature dimensional stability, making it suitable for manufacturing plastic molds, bearings, surgical instruments, and measuring tools that operate under high loads, high wear, and corrosive conditions. As a ledeburitic steel, it is prone to the formation of non-uniform carbide segregation, which can adversely affect the service life of components. Therefore, it is imperative to control the processing parameters and select an appropriate processing ratio during hot working.
1. Compostion(GB/T 20878-2007)
C | Cr | Mo | Ni | Si (≤) | Mn (≤) | P (≤) | S (≤) |
0.95 – 1.10 | 16.00 – 18.00 | 0.40 – 0.70 | -0.6 | 0.8 | 0.8 | 0.04 | 0.03 |
Equivalent Grades and Compositions
Standard | Steel Grade | C | Cr | Mo | Ni | Si (≤) | Mn (≤) | P (≤) | S (≤) |
Japan JIS | SUS440 | 0.95 – 1.20 | 16.00 – 18.00 | ≤(0.75) | -0.6 | 1 | 1 | 0.04 | 0.03 |
USA ASTM | 440C / S4400C | 0.95 – 1.20 | 16.0 – 18.0 | ≤0.75 | — | 1 | 1 | 0.04 | 0.03 |
International ISO | X105CrMo17 | 0.95 – 1.20 | 16.0 – 18.0 | 0.40 – 0.80 | — | 1 | 1 | 0.04 | 0.015 |
Europe EN | X105CrMo17 / 1.4125 | 0.95 – 1.20 | 16.0 – 18.0 | 0.40 – 0.80 | — | 1 | 1 | 0.04 | 0.015 |
2. Critical Points of 9Cr18Mo(102Cr17Mo)
- Ac1≈815∼865℃: This is the lower critical temperature upon heating. It represents the temperature range at which austenite begins to form from the ferrite-carbide matrix.
- Ar1≈665∼765℃: This is the lower critical temperature upon cooling. It represents the temperature range where the transformation of austenite to ferrite or pearlite is completed.
- Ms≈145℃: This is the Martensite start temperature. It is the temperature at which the transformation of austenite to martensite begins during rapid cooling (quenching).
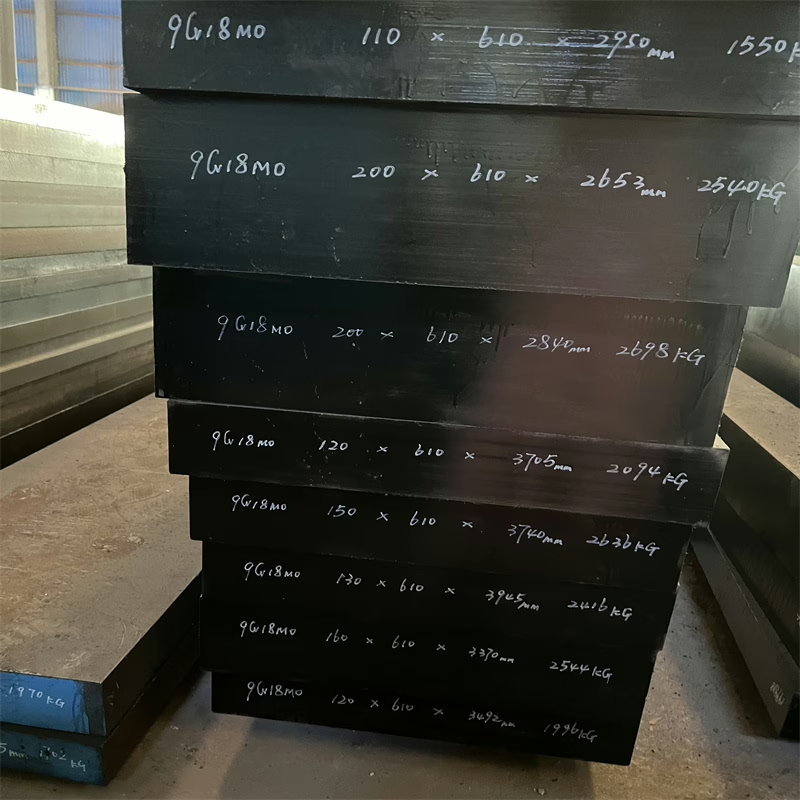
Please fill out the following contact form to get the latest 9Cr18Mo(102Cr17Mo) quotation!
3. Hot Froging Process of 9Cr18Mo(102Cr17Mo)
Item | Heating Temperature/°C | Initial Forging Temp./°C | Final Forging Temp./°C | Cooling Method |
Steel Ingot | 1130 ~ 1150 | 1080 ~ 1100 | 850 ~ 900 | Sand Cooling |
Steel Billet | 1100 ~ 1120 | 1050 ~ 1080 | 850 ~ 900 | Sand Cooling |
Special attention should be paid to the hot working process of 9Cr18Mo (102Cr17Mo)steel. It is recommended to use a cold-charged furnace for heating, and the heating rate should not be too fast, especially below 700°C. At the same time, the final forging temperature should be controlled at a higher level, and strict attention should be paid to the cooling conditions.
4. Heat Treatment of 9Cr18Mo(102Cr17Mo)
The processes for preliminary heat treatment are as follows:
- Recrystallization Annealing: Heat to a temperature of 730∼750°C, followed by air cooling.
- Annealing: Heat to a temperature of 850∼870°C and soak for 4 to 6 hours. Subsequently, furnace cool to below 600°C, followed by air cooling. The hardness after annealing should be ≤255HBW.
- Quenching: Heat to a temperature of 1050∼1100∘C, followed by an oil quench. The as-quenched hardness should be ≥58HRC.
- Tempering: Heat to a temperature of 160∼180∘C and soak for 3 to 5 hours. The final hardness after tempering should be ≥58HRC.
The effect of quenching temperature and cold treatment on hardness
Quenching Temperature (°C) | 1020 | 1040 | 1060 | 1080 | 1100 |
Hardness after Conventional Quenching (HRC) | 58.5 | 58 | 61.5 | 61 | 61 |
Hardness after Cold Treatment (HRC) | 60 | 60.5 | 62 | 63 | 64 |
Relationship between hardness and tempering temperature
Tempering Temperature (°C) | Untempered | 100 | 200 | 300 | 400 | 500 | 600 | 700 | |
950°C Air Cooling | Hardness (HRC) / Quenching | 50 | 47 | 48 | 48 | 47 | 47 | 38 | 25 |
1000°C Air Cooling | 56 | 51.5 | 52 | 50 | 49 | 49 | 40.5 | 27 | |
1050°C Air Cooling | 58 | 56 | 56 | 53 | 52 | 52 | 43 | 29 | |
1100°C Air Cooling | 60.5 | 57 | 58 | 56 | 54 | 55 | 47 | 32 |
5. Mechanical Properties
Influence of Quenching Temperature and Cryogenic Treatment on Mechanical Properties
Quenching Temperature /°C | Not Cryogenically Treated | After -75°C Cryogenic Treatment (held for 1h) | ||
σbb/MPa | aK / J・cm⁻² | σbb/MPa | aK / J・cm⁻² | |
1020 | 3250 | 30 | 30 | 30 |
1040 | 3000 | 37 | 37 | 11 |
1060 | 3500 | 40 | 40 | 6 |
1080 | 2750 | 25 | 25 | 3 |
1100 | 2500 | 3 | 3 | 2.5 |
6. Corrosion Resistance
Corrosion Resistance of 102Cr17Mo (9Cr18Mo) Steel
Heat Treatment Process | Hardness HRC | Medium Conditions | Corrosion Rate /g·(m²·h)⁻¹ | ||
Medium | Mass Fraction (%) | Temperature/°C | |||
1050°C Oil Quenching | 61 | Sulfuric Acid | 2 | Boiling | 575.6 |
Sulfuric Acid | 5 | 1003.9 | |||
Nitric Acid | 40 | 1.15 | |||
1050°C Oil Quenching, 150°C Tempering for 1h | 60 | Sulfuric Acid | 2 | 502 | |
Sulfuric Acid | 5 | 968.3 | |||
Nitric Acid | 40 | 1.04 |
Get a Competitive Quote for 9Cr18Mo(102Cr17Mo) Stainless Steel
With over 20 years of forging expertise, Aobo Steel is your trusted partner for high-performance 9Cr18Mo(102Cr17Mo) stainless steel. We provide not just materials, but solutions. Leverage our deep industry knowledge and reliable supply chain for your project’s success.
✉ Contact us by filling out the form below.