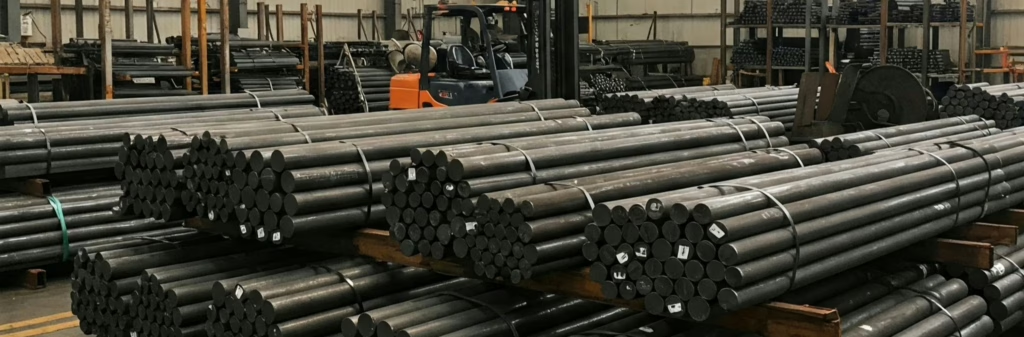
95Cr18 | 9Cr18 Stainless Steel
AOBO STEEL – Trusted Global Tool Steel Supplier
In China’s GB standards, 9Cr18 and 95Cr18 actually refer to the same type of steel. 95Cr18 is the new designation for 9Cr18 steel.
The old designation 9Cr18 originates from the GB/T 1220-1992 standard. It is primarily based on carbon and chromium content, with “9” representing a carbon content of approximately 0.9% and “18” representing a chromium content of approximately 18%.
The new grade 95Cr18 is named according to the latest GB/T 1220-2007 standard. The new naming convention is more standardized, with “95” representing a carbon content of approximately 0.95%, which more accurately indicates the carbon content compared to the old grade.
95Cr18 steel is a high-carbon, high-chromium martensitic stainless steel. It has high hardness, wear resistance, and corrosion resistance. This steel also exhibits good hot plasticity and low heat treatment deformation tendencies.
1. Chemical Composition(GB/T 1220—2007)
C | Si | Mn | Cr | S | P |
0.90% to 1.00% | ≤0.80% | ≤0.80% | 17.00% ~ 19.00% | ≤0.030% | ≤0.040% |
For the improved version, “9Cr18Mo” (also known as AISI 440C), the composition includes Molybdenum (Mo) typically in the range of 0.40% to 0.70%.
2. Physical Properties of 95Cr18(9Cr18)
Critical Point Temperature
Critical Point | Temperature (approximate) / °C |
---|---|
Ac₁ | 830 |
Ar₁ | 810 |
Linear Expansion Coefficient
Temperature / °C | Linear Expansion Coefficient α / (10⁻⁶ °C⁻¹) |
20 ~ 100 | 10.5 |
20 ~ 200 | 11 |
20 ~ 300 | 11 |
20 ~ 400 | 11.5 |
20 ~ 500 | 12 |
Other Physical Properties
Property | Value |
Density / (g/cm³) | 7.7 |
Modulus of Elasticity E(20°C) / MPa | 203,890 |
Specific Heat Capacity cₚ(20°C) / [J/(kg·K)] | 459.8 |
Thermal Conductivity λ(20°C) / [W/(m·K)] | 29.3 |
Electrical Resistivity ρ(20°C) / (10⁻⁶ Ω·m) | 0.6 |
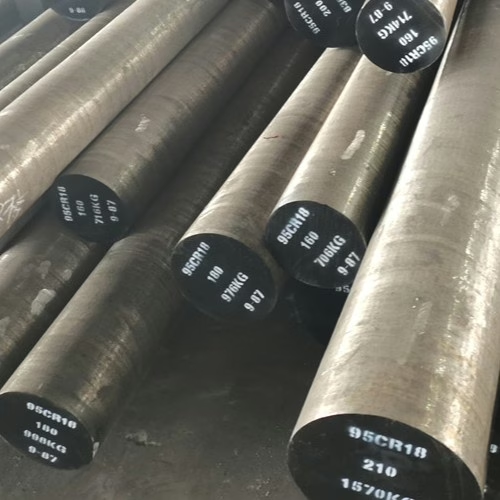
Are you looking for a 9Cr18 Stainless Steel supplier? Please fill out the form below to contact us today!
3. Forging Process of 95Cr18(9Cr18)
Furnace Charging Temperature | Initial Forging Temperature / °C | Final Forging Temperature / °C | Cooling |
---|---|---|---|
Cold charging temp. ≤600°C, Hot charging temp. unlimited | 1050 ~ 1100 | ≥850 | Furnace cooling |
Note: The heating speed of the hot working process should not be too fast. The stop forging (rolling) temperature should be controlled at a higher level, and slow cooling conditions must be strictly followed.
4. Heat Treatment of 95Cr18(9Cr18)
4.1 Preliminary Heat Treatment Specification of 95Cr18 Steel
Preliminary Heat Treatment Plan | Heating Temperature / °C | Cooling Method | Hardness HBW |
---|---|---|---|
Softening Annealing | 800 ~ 840 | Furnace cool to 500°C, then air cool | ≤255¹ |
Full Annealing | 840 ~ 860 | Furnace cooling | ≤255¹ |
Note: ① The annealed structure is pearlite.
4.2 Quenching and Tempering
4.2.1 Quenching and Tempering Process Specification of 95Cr18 Steel
Quenching Temp. / °C | Cooling Method | Hardness HRC (Quenching) | Tempering Temp. / °C | Hardness HRC (Tempering) |
---|---|---|---|---|
1030 ~ 1070 | Oil cooling | ≥55 | 200 ~ 300 | 56 |
4.2.2 Hardness, Retained Austenite Content, and Impact Toughness
Quenching Temp. / °C | Hardness HRC | Retained Austenite (vol. fraction, %) | aₖ / (J/cm²) |
---|---|---|---|
800 | 35 | — | 31 |
900 | 48 | — | 17 |
950 | 52 | 1.7 | 14 |
1000 | 57 | 5.2 | 11 |
1050 | 60 | 29.2 | 10 |
1100 | 53 | 93.9 | 15 |
1150 | 42 | 97 | 22 |
1200 | 35 | 99 | 26 |
4.2.3 Effect of Different Tempering Temperatures on Hardness and Impact Toughness
Tempering Temp. / °C | After Quenching | 100 | 200 | 300 | 400 | 450 | 500 | 550 | 600 | 650 |
---|---|---|---|---|---|---|---|---|---|---|
Hardness HRC | 60 | 60 | 58 | 55 | 56 | 57 | 54 | 47 | 40 | 32 |
aₖ / (J/cm²) | 11.5 | 20 | 28 | 29 | 24 | 22 | 21 | 25 | 30 | — |
4.3 Cold Treatment
4.3.1 Cold Treatment Process Specification
Cold Treatment Process | Hardness HBW |
---|---|
1000°C × 10min + -73°C × 6-8h + 100-200°C × 30-40min Air Cooling | 55 ~ 60 |
4.3.2 Effect of Cold Treatment on the Hardness
Quenching Temperature/°C | Hardness HRC | Hardness HRC after cooling to -75°C and holding for 1h | Hardness HRC after Tempering (Tempering Temperature) | ||
100°C | 150°C | 200°C | |||
1000 | 58 | — | 58 | 57 | 55 |
1000 | 59 | 59.5 | 59.5 | 59 | 57 |
1050 | 60 | 61.5 | 61 | 61 | 59 |
1100 | 60.5 | 62 | 62 | 62 | 60.5 |
5. Corrosion Resistance of 95Cr18 (9Cr18) Steel
Medium | Mass Fraction (%) | Temperature/℃ | Corrosion Rate /mm⋅a-1 |
Nitric acid | 5 – 20 | 20 | < 0.1 |
5 | 60 ~ Boiling | < 1.0 | |
20 | 60 | < 0.1 | |
20 | 80 | < 1.0 | |
20 | Boiling | 2.0 ~ 3.0 | |
40 | 60 ~ 80 | < 1.0 | |
40 | Boiling | 3.0 ~ 10.0 | |
50 | 20 | < 0.1 | |
50 | 80 | < 1.0 | |
60 | 20 | < 0.1 | |
60 | 60 ~ 80 | < 1.0 | |
60 | Boiling | 1.0 ~ 3.0 | |
90 | 20 | < 1.0 | |
90 | Boiling | 3.0 ~ 10.0 | |
Acetic acid | 5 | 20 | < 1.0 |
5 | 50 ~ 75 | 3.0 ~ 10.0 | |
5 | Boiling | > 10.0 | |
25 | 50 ~ 75 | 3.0 ~ 10.0 | |
25 | Boiling | > 10.0 | |
50 | 20 | < 0.1 | |
50 | 50 | 3.0 ~ 10.0 | |
50 | 75 | > 10.0 | |
Phosphoric acid | 1 | 20 | < 0.1 |
10 | 20 | < 3.0 | |
15 | 20 | 3.0 ~ 10.0 | |
Sulfuric acid | 5 | 20 | > 10.0 |
5 | 50 | > 10.0 | |
5 | 80 | > 10.0 | |
Hydrochloric acid | 0.5 | 20 | < 1.0 |
0.5 | 50 | < 3.0 | |
0.5 | Boiling | > 10.0 | |
1 | 20 | < 3.0 | |
1 | 50 | 3.0 ~ 10.0 |
Explore Our Other Products
D2/1.2379/SKD11
D3/1.2080/SKD1
D6/1.2436/SKD2
A2/1.23663/SKD12
O1/1.2510/SKS3
O2/1.2842
S1/1.2550
S7/1.2355
DC53
H13/1.2344/SKD61
H11/1.2343/SKD6
H21/1.2581/SKD7
L6/1.2714/SKT4
M2/1.3343/SKH51
M35/1.3243/SKH55
M42/1.3247/SKH59
P20/1.2311
P20+Ni/1.2738
420/1.2083/2Cr13
422 stainless steel
52100 bearing steel
440C stainless steel
4140/42CrMo4/SCM440
4340/34CrNiMo6/1.6582
4130
5140/42Cr4/SCR440
SCM415